Innovations Driving the Evolution of lvmeikapton Insulating Electrical Tape— From Material Advancements to BreakthrougWhen Should You Replace Your PI Material High Temperature Resistant 300 Tape?— Identifying Degradation Signs and Establishing Scientific Replacement Criteria
PI Material High Temperature Resistant 300 Tape (polyimide tape) is widely used in electronic manufacturing, coil winding, high-temperature protection, and other fields due to its excellent heat resistance, insulation, and mechanical stability. However, tape performance gradually degrades over time, which may lead to insulation failure, adhesion failure, or even equipment malfunctions. Therefore, it is crucial to determine the replacement timing scientifically. This article will help you establish reasonable replacement criteria from three dimensions: visual inspection, performance testing, and time-based guidelines, avoiding operational risks caused by tape aging.
IntroductionDegradation of PI tape compromises protection, necessitating timely replacement. Understanding the signs of degradation and establishing a replacement schedule are essential to ensure equipment reliability and operational safety.
Section 1: Visual IndicatorsVisual inspection is the first step to preliminarily assess tape condition. Key indicators include:
1. Cracking or Brittleness: Visible cracks or brittleness indicate thermal aging and mechanical fatigue. Cracks accelerate heat stress transmission, particularly in high-temperature environments, compromising protection.
2. Discoloration: Normal wear may cause slight yellowing. However, severe yellowing, charring, or delamination suggests excessive heat radiation or chemical corrosion, significantly reducing insulation performance.
3. Adhesive Bleeding: Softening, oozing adhesive, or significantly weakened adhesion (e.g., visible adhesive flow under light pressure) indicate adhesive system failure, unable to ensure long-term stable adhesion.
Tip: Periodically photograph tape conditions to compare historical images and capture subtle changes.
Section 2: Performance TestsWhen visual inspections raise concerns, laboratory or field tests are required for quantitative evaluation:
● Peel Strength Test: Use a specialized tester to measure peel strength. Replace if the value drops below 3 N/25mm (industry critical threshold).
● Dielectric Breakdown Test: Evaluate insulation performance at the maximum operating voltage. Replacement is necessary if the breakdown voltage is less than 80% of the equipment's maximum voltage to prevent arc risks.
● Residue Testing: After tape removal, check the substrate for adhesive or fiber residue. Excessive residue indicates material structure degradation, compromising cleanliness and subsequent process reliability.
Caution: Tests should be conducted by professionals to avoid misjudgment due to incorrect operation.
Section 3: Time-Based GuidelinesPreventive replacement based on time intervals is equally important even without visible degradation:
1. Continuous High-Temperature Use: Replace every 12-18 months at temperatures ≥250°C. High heat accelerates molecular chain breakage, shortening service life.
2. Intermittent Use or Lower Temperature: Extend to 24-36 months, but combine post-use condition assessments.
3. Special Environment Adjustments:
○ In corrosive gas (e.g., acid/alkali vapors): Shorten to 6-12 months.
○ In frequent mechanical bending areas: Add monthly peel strength checks.
Maintenance Recommendation: Establish a "tape service archive" to record installation dates, operating temperatures, and maintenance logs for data-driven replacement decisions.
Section 4: Comprehensive Evaluation and Replacement Prioritization
1. Immediate Replacement Signals: Replace promptly if severe cracking, excessive adhesive bleeding, or failed dielectric breakdown tests occur to prevent safety incidents.
2. Preventive Replacement Window: Schedule replacement during the next maintenance cycle if moderate discoloration, peel strength nearing critical values, or time-based thresholds are reached.
3. Cost-Risk Balance: For critical equipment (e.g., high-voltage coils, aerospace components), prioritize proactive replacement rather than waiting for complete performance failure to minimize downtime losses.
Section 5: Practical Tips to Extend Tape Life
● Storage Protocol: Store unused tape in sealed containers at阴凉干燥 environments (≤30°C), avoiding UV exposure.
● Installation Control: Avoid over-stretching during winding (recommended tension ≤10%) to reduce mechanical stress damage.
● Temperature Monitoring: Use thermocouples to monitor real-time temperatures in application areas to prevent overheating.
ConclusionTimely replacement of PI high-temperature tape is a critical link in ensuring equipment safety and production efficiency. A three-in-one evaluation system ("visual inspection + performance testing + time-based guidelines") combined with dynamic environmental adjustments can effectively prevent failures caused by material aging. It is recommended that enterprises establish standardized inspection processes and integrate tape maintenance into preventive maintenance systems to achieve the optimal balance between cost and reliability.
References(Add industry standards or research literature as needed)
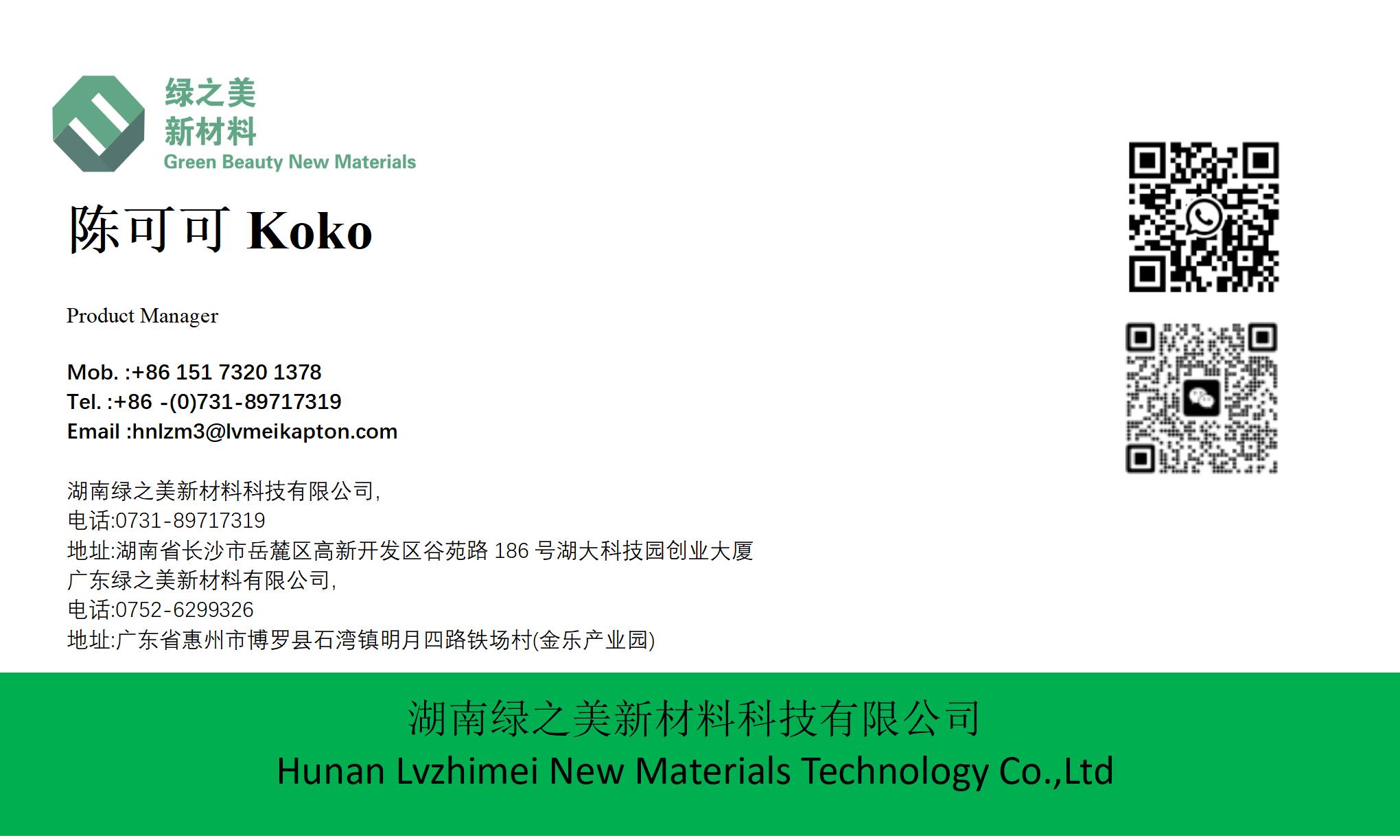