Why Adhesive PET Material High Temperature Tape is Ideal for Small-Scale Electronics Assembly?
IntroductionIn the realm of electronics assembly, choosing the right materials is crucial for both performance and cost efficiency. Adhesive PET (Polyethylene Terephthalate) material high temperature tape offers a unique balance between functionality and affordability, making it an ideal choice for hobbyists, small-scale manufacturers, and prototyping projects. This article delves into the advantages of PET tape, focusing on its cost-effectiveness, performance capabilities, and suitability for non-critical applications in small-scale environments.
Section 1: Cost vs. PerformanceOne of the primary reasons PET tape shines in small-scale assembly is its cost advantage. Typically priced 50% lower than high-end tapes like Kapton/PI (Polyimide), PET tape provides a budget-friendly solution without sacrificing essential features. While Kapton excels in extreme environments (up to 260°C), PET tape offers a maximum temperature resistance of 200°C, which suffices for most DIY soldering, reflow processes, and general electronics fabrication. Additionally, its adequate adhesion properties ensure secure temporary masking during assembly, making it suitable for applications where permanent bonding is not required.
Section 2: Small-Scale Benefits1. Easy Handling and FlexibilityPET tape’s hand-tearable nature eliminates the need for precision cutting tools, streamlining workflows in small-scale operations. This ease of use is particularly beneficial for prototypes and quick repairs, where flexibility and speed are prioritized.
2. Limited Waste and LongevitySmall-scale projects often involve intermittent use, and PET tape’s manageable roll sizes (typically lasting months in hobbyist applications) reduce material waste. This longevity, coupled with its RoHS compliance (ensuring environmental friendliness and safety), makes it a sustainable choice for resource-conscious users.
3. Versatile Performance in Common ScenariosPET tape’s resistance to solvents, acids, and bases protects components during processes like cleaning and chemical treatments. Its non-residue properties post-heat exposure prevent contamination of delicate circuits, ensuring clean results even after removal.
Section 3: Practical Applications in Small-Scale Electronicsa. PCB Masking and Solder ProtectionPET tape efficiently covers sensitive areas during wave soldering or hot air rework, preventing damage to non-targeted components. Its transparency (in some variants) allows visual alignment, enhancing precision.
b. Component Fixation and Cable ManagementThe tape’s adhesive layer securely holds small parts during handling or transport, while its low friction surface facilitates easy removal without residue.
c. Heat Tool CompatibilityCompatible with tools like hot air guns and soldering irons, PET tape withstands typical DIY heating durations, safeguarding underlying materials from thermal degradation.
Section 4: Limitations and Appropriate Use CasesWhile PET tape excels in small-scale scenarios, it’s important to acknowledge its constraints. Its 200°C limit and shorter-term exposure to high temperatures make it unsuitable for continuous industrial processes or extreme chemical exposures. Thus, PET tape is best reserved for:
● Prototyping and testing
● Non-critical applications (where failure risks are manageable)
ConclusionAdhesive PET material high temperature tape’s combination of cost-efficiency, ease-of-use, and reliable performance positions it as a cornerstone for small-scale electronics assembly. For hobbyists, startups, and those prioritizing budget without compromising on essential heat resistance and protection, PET tape offers a practical solution. By understanding its capabilities and limitations, users can leverage this versatile material to drive innovation and productivity in resource-limited environments.
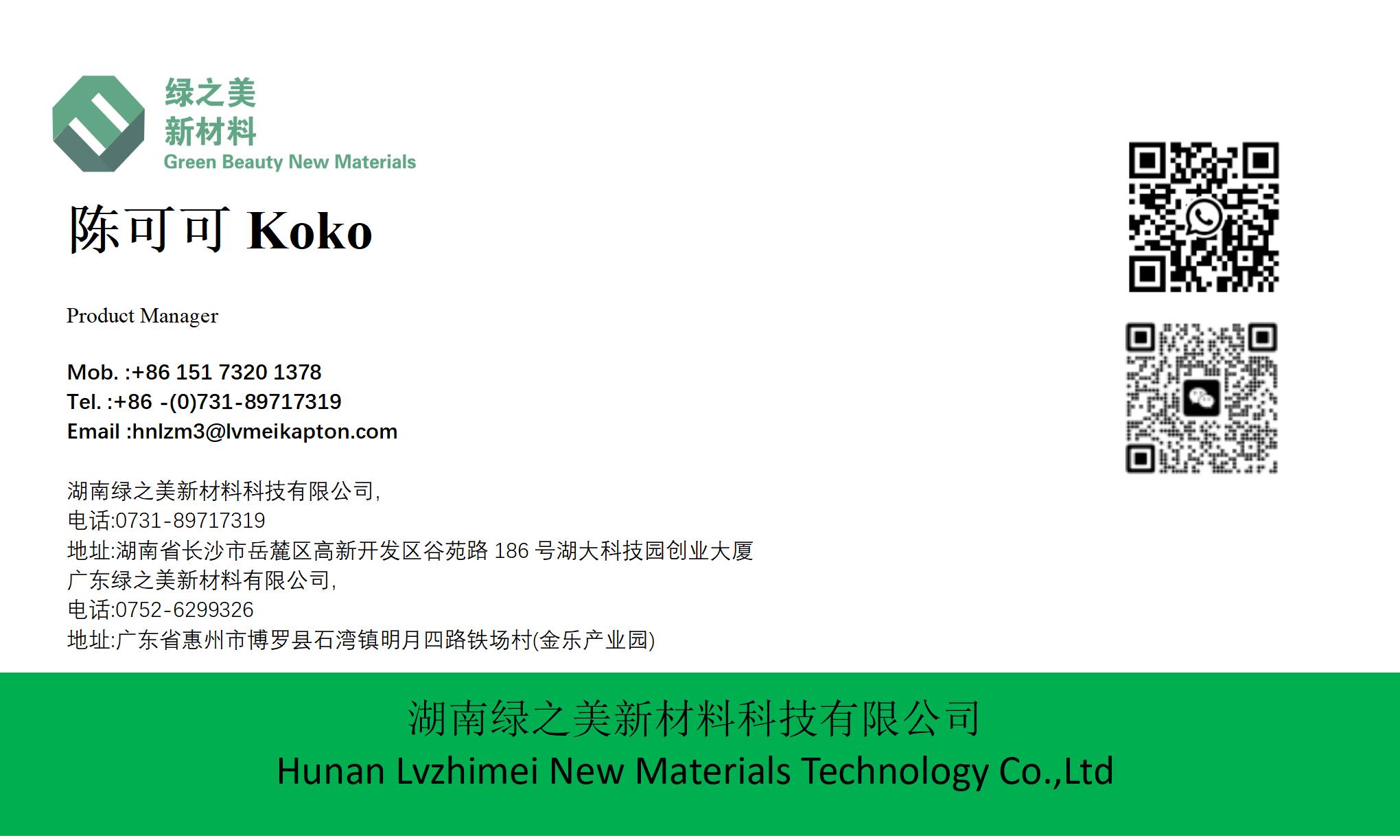