Why Choose Kapton Tape for PCB Manufacturing?I. Characteristics and Advantages of Kapton Tape1.1 High Temperature ResistanceKapton Tape stands out for its exceptional high-temperature resistance, maintaining stability under extreme conditions. While most materials fail at 400°C, Kapton Tape retains its physical and chemical properties. This is due to its polyimide film substrate, which has a high thermal decomposition temperature. In PCB manufacturing, soldering is essential, involving instantaneous high temperatures. Common tapes may melt, deform, or burn, releasing harmful substances and compromising PCB quality. Kapton Tape, however, remains stable during soldering, retaining adhesion and structure. It plays a crucial role in high-temperature processes like laminating, preventing PCB deformation and ensuring process continuity.
1.2 Chemical ResistanceKapton Tape exhibits remarkable stability in corrosive environments. During PCB production, storage, and use, exposure to acids, alkalis, and solvents can cause circuit shorts and component damage. The polyimide substrate of Kapton Tape resists most corrosive agents, protecting PCBs in harsh conditions. For example, in chemical equipment control boards, Kapton Tape acts as a barrier, preventing corrosives from reaching sensitive areas, ensuring long-term reliability.
1.3 Excellent Insulation PerformanceKapton Tape’s high insulation properties are vital for electronics safety. Its polyimide film has a low dielectric constant (≈3.5) and dissipation factor (≈0.04), ideal for dense circuits with minimal spacing. In high-frequency applications, it maintains stable insulation, preventing current leakage and signal interference. This is critical for modern PCBs operating at GHz frequencies, ensuring reliable signal transmission.
1.4 Mechanical PropertiesKapton Tape’s flexibility and tensile strength make it suitable for complex PCB structures. It bends and folds without breaking, tightly conforming to surfaces and corners for comprehensive protection. During production, transportation, and use, PCBs face mechanical stresses like vibration and compression; Kapton Tape absorbs these impacts, preventing deformation and damage, thereby improving yield rates.
II. Material Requirements for PCB Manufacturing2.1 High Temperature EnvironmentPCB fabrication involves numerous high-temperature processes (soldering, laminating). For example, wave soldering or reflow soldering reaches >250°C. Materials with poor heat resistance can deform or melt, causing structural defects like delamination or voids. While FR-4’s glass transition temperature (Tg) is around 150°C, polyimide substrates (like Kapton) have Tg >260°C, enabling stability in demanding processes. As 5G and high-density PCBs evolve, materials must withstand increasingly severe thermal conditions.
2.2 Chemical Corrosion ImpactPCB manufacturing uses aggressive chemicals (etching solutions, cleaners), posing corrosion risks. Corrosion can lead to conductor degradation, increased resistance, and electrochemical migration (ion deposition causing shorts). Phenolic resin boards are susceptible to corrosion, suitable only for low-end applications. Epoxy boards offer better resistance but are inferior to polyimide, which withstands most acids, alkalis, and solvents. Selecting corrosion-resistant materials is crucial to prevent failures and extend PCB lifespan.
2.3 Insulation RequirementsAs PCBs become more densely packed, maintaining insulation is paramount. Poor insulation can cause shorts, arcing, or signal attenuation. Materials with high dielectric constants slow signal speed and increase losses. Polyimide’s low dielectric properties support high-speed signals, making Kapton Tape ideal for applications like RF circuits and data communication systems.
2.4 Mechanical StabilityPCB manufacturing (drilling, cutting) and end-use environments (vibration, shock) demand mechanical robustness. Materials must resist fracture, delamination, and dimensional changes. Polyimide’s flexibility and high tensile strength ensure durability during fabrication and operation, particularly in aerospace or automotive electronics subjected to extreme mechanical stress.
III. How Kapton Tape Meets PCB Manufacturing Requirements3.1 High Temperature ApplicationsDuring component assembly, Kapton Tape secures parts during soldering. For example, in precision electronics manufacturing, it fixes components while enduring reflow temperatures, preventing displacement and oxidation. In laminating processes, it ensures multilayer bond integrity under high pressure/temperature, avoiding delamination and voids.
3.2 Chemical Corrosion ProtectionIn etching processes (e.g., using strong alkalis), Kapton Tape covers non-etch areas, shielding them from corrosives. After etching, removing the tape reveals pristine circuit patterns. Similarly, during cleaning with aggressive solvents, Kapton Tape protects sensitive pads and traces, maintaining surface integrity.
3.3 Insulation EnhancementKapton Tape acts as an additional insulation layer in dense circuits, preventing shorts between adjacent traces or components. In high-frequency designs, it reduces signal losses and crosstalk, critical for 5G, microwave, and radar systems. It also serves as a remedial measure for insulation weaknesses during manufacturing.
3.4 Mechanical SupportDuring drilling, Kapton Tape cushions PCBs from drill-induced vibrations, preventing fractures. In cutting operations, it reinforces edges against chipping. Its tensile strength supports PCB stability during pick-and-place assembly, ensuring precise component positioning.
IV. Role of Kapton Tape in Specific PCB Processes4.1 Assembly and SolderingDuring assembly, Kapton Tape secures components while withstanding soldering heat. For example, in surface mount technology (SMT), it holds small parts during reflow, preventing displacement. In wave soldering, it protects heat-sensitive regions (e.g., connectors) from molten solder, ensuring clean joints and preventing thermal damage.
4.2 Etching and CleaningKapton Tape masks areas during acid/alkali etching, ensuring only designated copper patterns are removed. Its chemical resistance allows safe exposure to etchants without degradation. Post-etching, it is easily peeled off, leaving defined circuits. Similarly, during solvent cleaning, it shields delicate areas from solvent attack.
4.3 Layer Protection in Multilayer PCBsIn multilayer fabrication, Kapton Tape aids in aligning and bonding layers during laminating. Its thermal stability prevents layer separation under high pressure/temperature, ensuring electrical continuity and structural integrity. It also protects inner layers from contamination during drilling or routing.
4.4 Surface Protection and FinishingKapton Tape temporarily covers gold fingers or plated surfaces during handling, preventing scratches or oxidation. It is removed before final assembly, preserving surface finish critical for connector reliability.
ConclusionKapton Tape’s unique combination of thermal stability, chemical resistance, insulation, and mechanical durability makes it indispensable in PCB manufacturing. From protecting components during soldering to ensuring layer integrity in multilayer boards, its versatility addresses critical challenges across the fabrication chain. As electronics evolve toward miniaturization and high performance, Kapton Tape remains a reliable solution for maintaining PCB quality and reliability in diverse applications.
Key Notes:
● Technical terms are maintained for industry accuracy.
● Structures and headings are preserved for clarity.
● Example applications are included to illustrate real-world use cases.
● Emphasis on material properties aligning with PCB process requirements.
● Data (temperatures, properties) remain consistent with the original content.
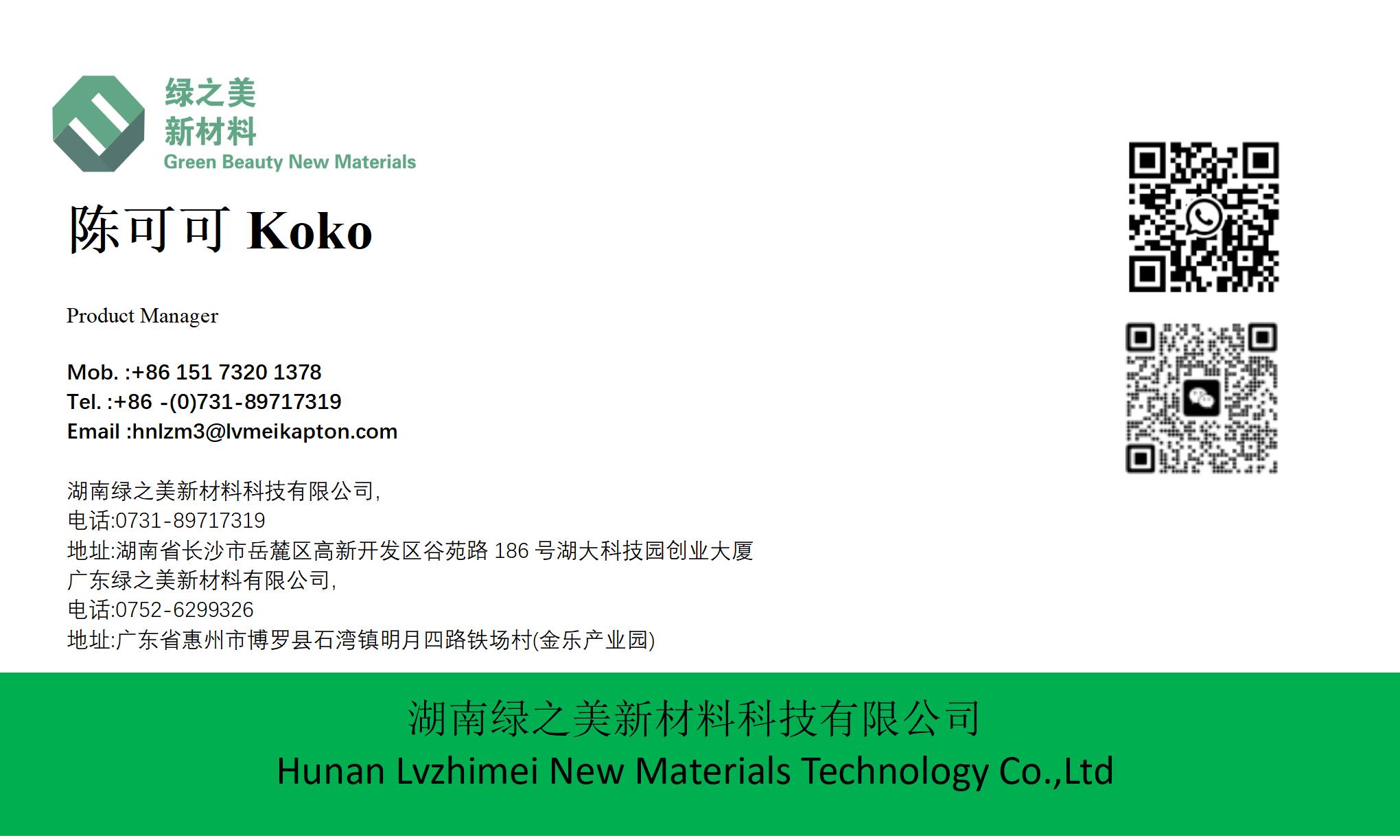