Technical Features of Gold Finger Electronics Polyimide Tape Kapton
Polyimide tape, also known as Kapton tape, is fabricated from polyimide film with a pressure-sensitive adhesive (PSA) layer. Gold Finger Electronics’ Kapton tape exhibits the following critical attributes:
1. Temperature Resistance
Aerospace components experience thermal cycling during takeoff, flight, and landing. Kapton tape withstands continuous exposure to temperatures up to 260°C (short-term up to 400°C), ensuring stability even in engine compartments or near electronic control units. This feature aligns with MIL-STD-883 environmental testing requirements, which mandate materials to perform under thermal shock and prolonged high temperatures.
2. Mechanical Strength and Shock Resistance
The tape’s polyimide core provides superior tensile strength (≥200N/cm) and flexibility, preventing fractures during installation or operation. Notably, its 50,000g shock resistance surpasses typical aerospace standards (e.g., MIL-STD-202G), safeguarding wiring harnesses against impacts during launch, turbulence, or emergency landings.
3. Electrical Insulation and Signal Integrity
Kapton tape features low dielectric constant (ε ≈ 3.4) and dissipation factor (tan δ ≈ 0.002), minimizing signal loss and interference in high-frequency applications. Its superior electrical breakdown strength (≥3kV/mil) prevents arcing—a common cause of failures in traditional PET or brown circuit board tapes.
4. Chemical and Corrosion Resistance
Aerospace environments expose materials to fuels, lubricants, and saltwater. Kapton’s resistance to solvents, oils, and moisture (≤0.6% water absorption) ensures long-term reliability. Additionally, its flame retardancy (UL94 V-0 rating) mitigates fire hazards.
Applications in Aerospace Wiring Harnesses
Gold Finger Electronics Polyimide Tape Kapton is employed across diverse aerospace systems:
1. Engine and Avionics Wiring
In engine compartments, where temperatures exceed 200°C, Kapton tape insulates wires from heat and mechanical stress. It is also used in avionics systems (e.g., flight control computers) to protect against electromagnetic interference (EMI) and radio frequency interference (RFI).
2. Connectors and Splices
The tape’s gold-plated “fingers” (edges) enhance electrical conductivity and corrosion resistance at wire terminations. This feature is particularly vital in military aircraft, where connectors must withstand saltwater corrosion and frequent disconnections.
3. Cable Management
Kapton tape’s self-fusing properties (when heated) allow it to form secure, seamless wraps around bundles, preventing wire chafing and abrasion. Its low outgassing characteristic (≤1% TML) ensures compatibility with sensitive spacecraft environments.
4.典型案例:波音787的电气系统
波音787“梦想客机”采用Kapton胶带替代传统材料,显著提升系统可靠性。其应用包括:
● 发动机线束绝缘:抵御高温和振动,降低维护成本。
● 驾驶舱显示系统:保障高频信号传输的稳定性,减少电磁干扰。
● 燃油系统电缆防护:耐受航空燃油腐蚀,增强安全性。
Advantages Over Traditional Materials
Table: Comparison of Aerospace Electrical Tapes
Table: Comparison of Aerospace Electrical Tapes
Property | Kapton Tape | PET Tape | Brown Circuit Board Tape |
Temperature Range | -55°C to 260°C | -40°C to 150°C | -40°C to 130°C |
Shock Resistance | 50,000g | 10,000g | 5,000g |
Dielectric Constant | 3.4 | 4.0-4.5 | 5.0-6.0 |
Corrosion Resistance | Excellent | Moderate | Poor |
Flame Retardancy | UL94 V-0 | VTM-0 | None |
Key Advantages:
● Enhanced Durability: Kapton tape’s extended temperature range and shock resistance reduce failures, extending wiring harness lifespan.
● Signal Preservation: Lower dielectric properties maintain data integrity in avionics and communication systems.
● Safety Compliance: MIL-STD-883 and UL certifications ensure adherence to aerospace safety regulations.
● Cost Efficiency: Despite higher upfront costs, Kapton tape’s longevity and reliability minimize maintenance and replacement expenses.
LVMEIKAPTON Insulating Electrical Tape: A Specialized Variant
LVMEIKAPTON’s insulating tape combines Kapton’s properties with advanced adhesive formulations, offering:
1. Improved Adhesion: Customized PSA layers provide strong bonding to various substrates (e.g., copper, aluminum) without residue.
2. Thermal Conductivity: Special grades dissipate heat, ideal for thermal management in aerospace electronics.
3. Thickness Options: Ranging from 0.025mm to 0.2mm, enabling precise insulation for micro-wire applications.
These features make LVMEIKAPTON tape suitable for:
● Satellite Wiring: Protecting delicate sensors and communication modules from cosmic radiation.
● Unmanned Aerial Vehicles (UAVs): Lightweight construction without compromising insulation performance.
Challenges and Future Trends
While Kapton tape dominates aerospace applications, challenges remain:
1. Weight Reduction: Future tapes may adopt nano-enhanced materials to further reduce mass.
2. Automated Application: Integration with robotic winding systems could enhance manufacturing efficiency.
3. Smart Materials: Self-monitoring tapes with embedded sensors could detect insulation degradation in real-time.
Conclusion
Gold Finger Electronics Polyimide Tape Kapton’s synergy of thermal stability, mechanical robustness, and electrical performance is indispensable in aerospace wiring harnesses. From commercial airliners to military aircraft and space systems, its role in ensuring safety, reliability, and efficiency cannot be overstated. As aerospace technology evolves, Kapton tape will continue to evolve, meeting the demands of next-generation systems while upholding the stringent standards of the industry.
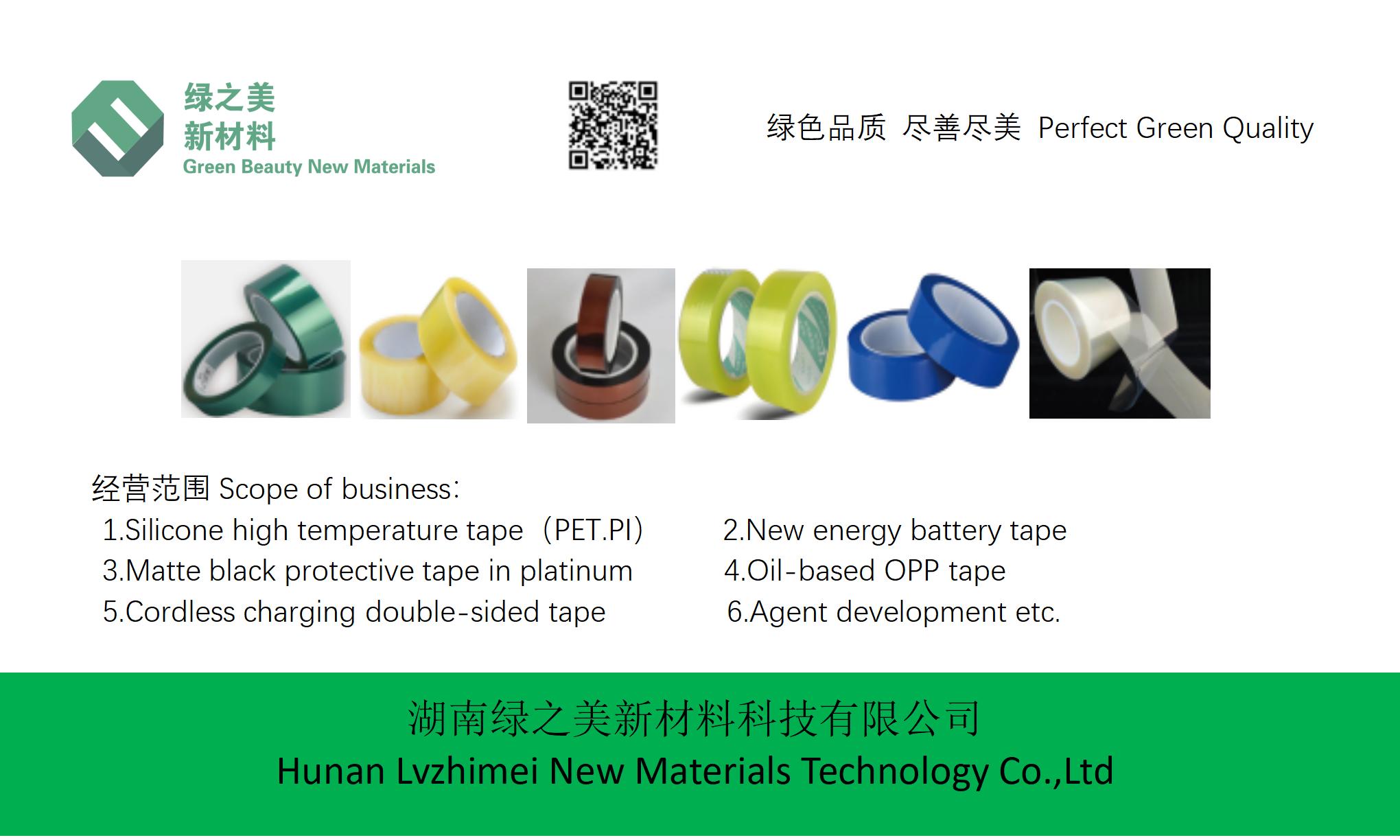
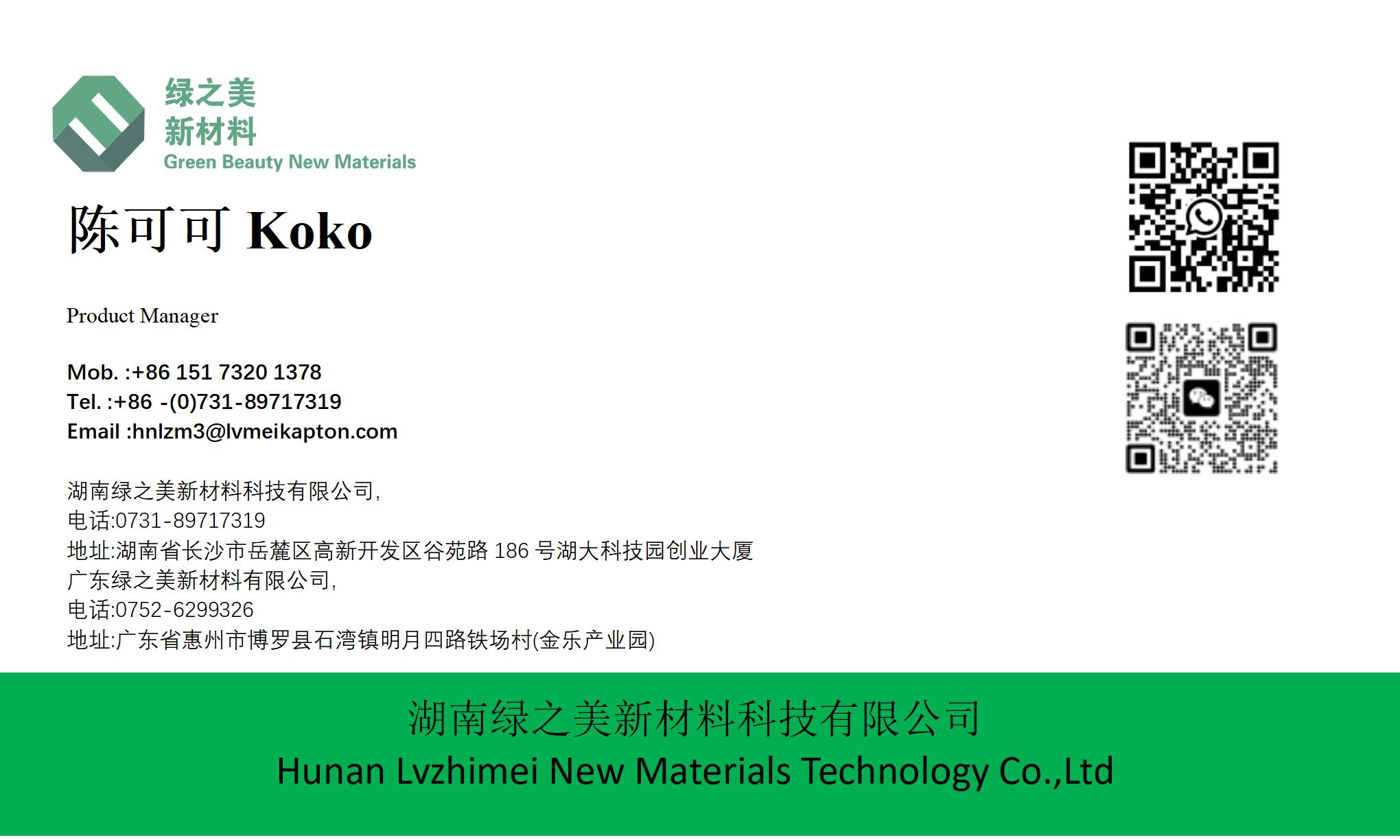