1. Understanding PI Material: Key Properties for Aerospace Applications
PI material is a high-performance thermoplastic polymer with a unique combination of properties that make it indispensable in aerospace electronics:
1.1 Extreme Temperature Resistance
PI tapes can withstand continuous exposure to temperatures up to 300°C (short-term resistance up to 400°C) without compromising mechanical integrity. This thermal resilience is vital in aerospace environments, where components may encounter rapid temperature fluctuations during takeoff, flight, and re-entry. For example, PI tapes used in engine wiring harnesses can protect cables from melting or degradation under prolonged exposure to high heat.
1.2 Electrical Insulation and Dielectric Strength
PI exhibits excellent electrical properties, including a high dielectric constant (3.4) and low dielectric loss. This makes it ideal for applications requiring reliable insulation in high-voltage systems. In aerospace electronics, PI tapes ensure safety and prevent short circuits in critical components like transformers, motors, and circuit boards.
1.3 Chemical and Radiation Resistance
PI’s resistance to solvents, fuels, and corrosive agents ensures durability in aerospace environments contaminated by aviation fuels or hydraulic fluids. Additionally, its low gas emission under vacuum conditions and radiation resistance (maintaining 90% strength after 5×109 rad exposure) make it suitable for space applications.
1.4 Mechanical Strength and Flexibility
Despite its rigidity, PI maintains flexibility, allowing it to conform to complex shapes without cracking. This property is crucial for wrapping irregularly shaped components or tight spaces in aerospace equipment.
2. Aerospace Electronics: Challenges and PI Tape Solutions
Aerospace electronics face unique challenges that PI high-temperature tapes address effectively:
2.1 Thermal Management
Modern aircraft and spacecraft generate intense heat during operation, especially in engine compartments and avionics systems. PI tapes with self-adhesive backing (e.g., Flashtape 300) provide reliable thermal barriers, preventing heat transfer to sensitive components. Their high thermal conductivity helps dissipate heat, maintaining optimal operating temperatures.
Table: Comparison of PI Tape vs. Traditional High-Temperature Materials
Property | PI Tape | PTFE Tape | PEEK Tape |
Operating Temp. | -269°C to +300°C | -200°C to +260°C | -40°C to +250°C |
Dielectric Strength | 22 kV/mm | 18 kV/mm | 15 kV/mm |
Chemical Resistance | Solvent-resistant | Limited resistance | Moderate resistance |
Flexibility | High | Low | Moderate |
2.2 Protection During Manufacturing and Maintenance
Self-adhesive back blocking spray paint tapes (e.g., PI-based variants) are essential during aerospace component painting. These tapes protect circuit boards, connectors, and wiring from paint overspray, ensuring electrical integrity. Their easy removal without residue (even after curing) minimizes post-processing labor.
2.3 Cable Management and Insulation
PI tapes offer superior cable insulation in aerospace applications. For example, brown circuit board high-temperature tapes (e.g., with silicone adhesive) provide:
● Abrasion resistance: Protecting cables from chafing during mechanical movement.
● EMI/RFI shielding: PI’s inherent stability reduces electromagnetic interference in avionics systems.
● Long-term reliability: Preventing cable degradation over decades of service.
3. Critical Applications of PI High-Temperature Tapes in Aerospace Electronics
3.1 Motor and Transformer Insulation
PI tapes are widely used in aerospace motors and transformers to:
● Provide multi-layer insulation for high-voltage windings.
● Enhance thermal stability, reducing the risk of coil failure.
● Mitigate corona discharge and electrical arcing.
3.2 Wiring Harness Protection
In aircraft cabins and engine bays, PI tapes protect wiring harnesses from:
● Thermal exposure (up to 300°C).
● Mechanical abrasion from vibrations and impacts.
● Chemical corrosion from engine oils and fuels.
3.3 Thermal Barrier Coatings
PI tapes with aluminum or ceramic coatings create thermal barriers on aerospace components. For instance, they protect sensors and electronics in rocket engines from extreme heat during launch, maintaining their functionality.
3.4 Aerospace Testing and Repair
PI tapes are employed during:
● Thermal cycling tests to assess component durability.
● Temporary repairs in emergency situations (e.g., sealing leaks in fuel lines).
● Bonding dissimilar materials (metal, ceramic, composites) without thermal expansion mismatches.
4. Advantages Over Traditional Materials
PI tapes offer distinct advantages over alternatives like PTFE (Teflon) and Kapton:
● Higher operating temperatures: PI’s continuous service temperature of 300°C surpasses PTFE’s 260°C limit.
● Better mechanical strength: PI’s tensile strength at 200°C (24 MPa) is superior to most polymers.
● Environmentally friendly: PI emits minimal smoke and toxic gases, meeting stringent aerospace safety standards.
● Cost-effectiveness: Though PI tapes are premium, their long service life reduces replacement costs in aerospace applications.
5. Future Trends and Innovations
Advancements in PI tape technology are driving further aerospace adoption:
● Nano-reinforced PI tapes: Incorporating carbon nanotubes or graphene for enhanced mechanical and thermal properties.
● 3D-printable PI filaments: Enabling rapid prototyping of aerospace components with integrated thermal management features.
● Smart PI tapes: Embedded sensors for real-time monitoring of temperature and strain in aerospace systems.
Conclusion
PI high-temperature resistant 300 tapes are critical to aerospace electronics due to their unparalleled thermal stability, electrical insulation, and mechanical durability. From protecting wiring harnesses to enabling advanced thermal management, PI tapes ensure the reliability and safety of aerospace systems in the most demanding environments. As aerospace technology evolves, PI materials will continue to play a pivotal role in pushing the boundaries of performance and innovation.
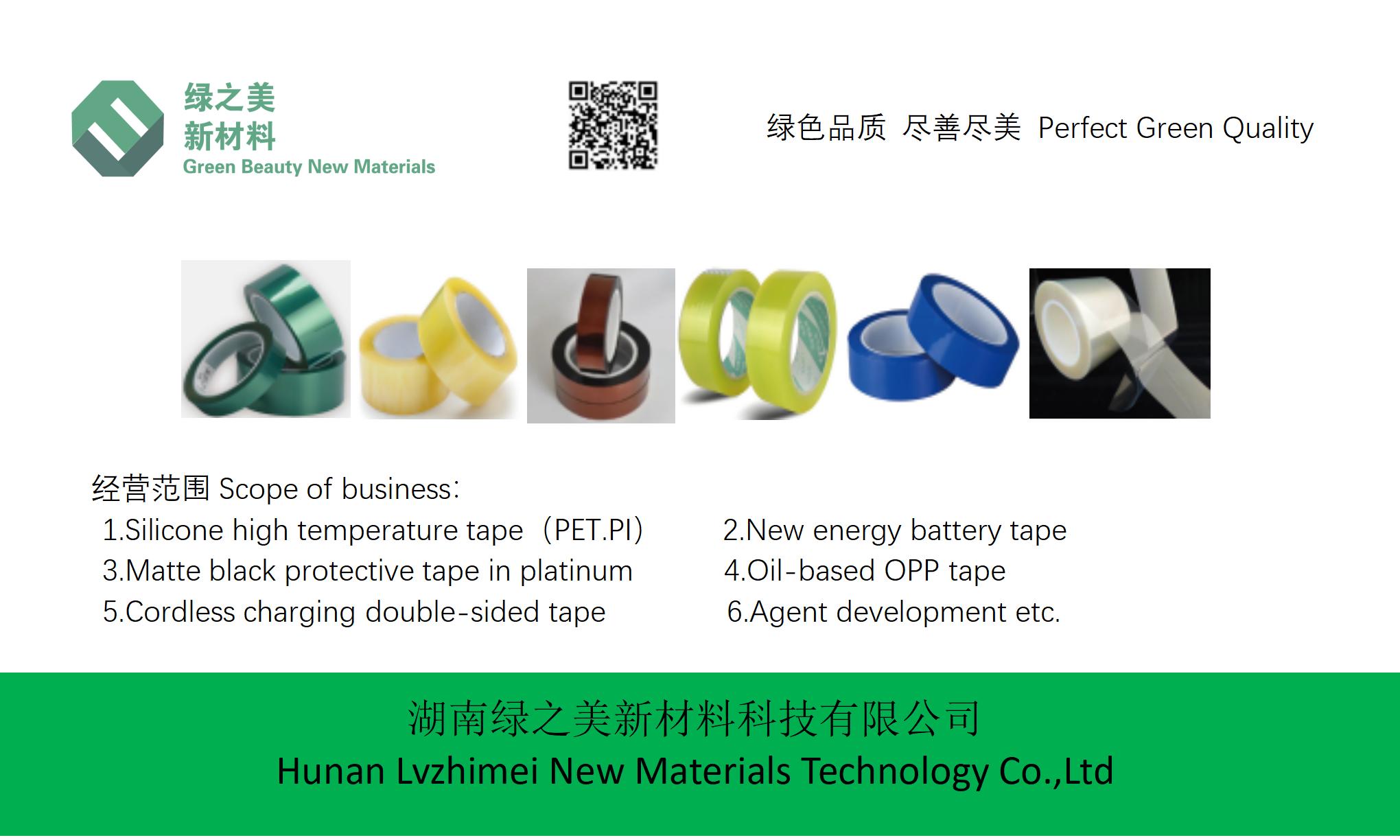
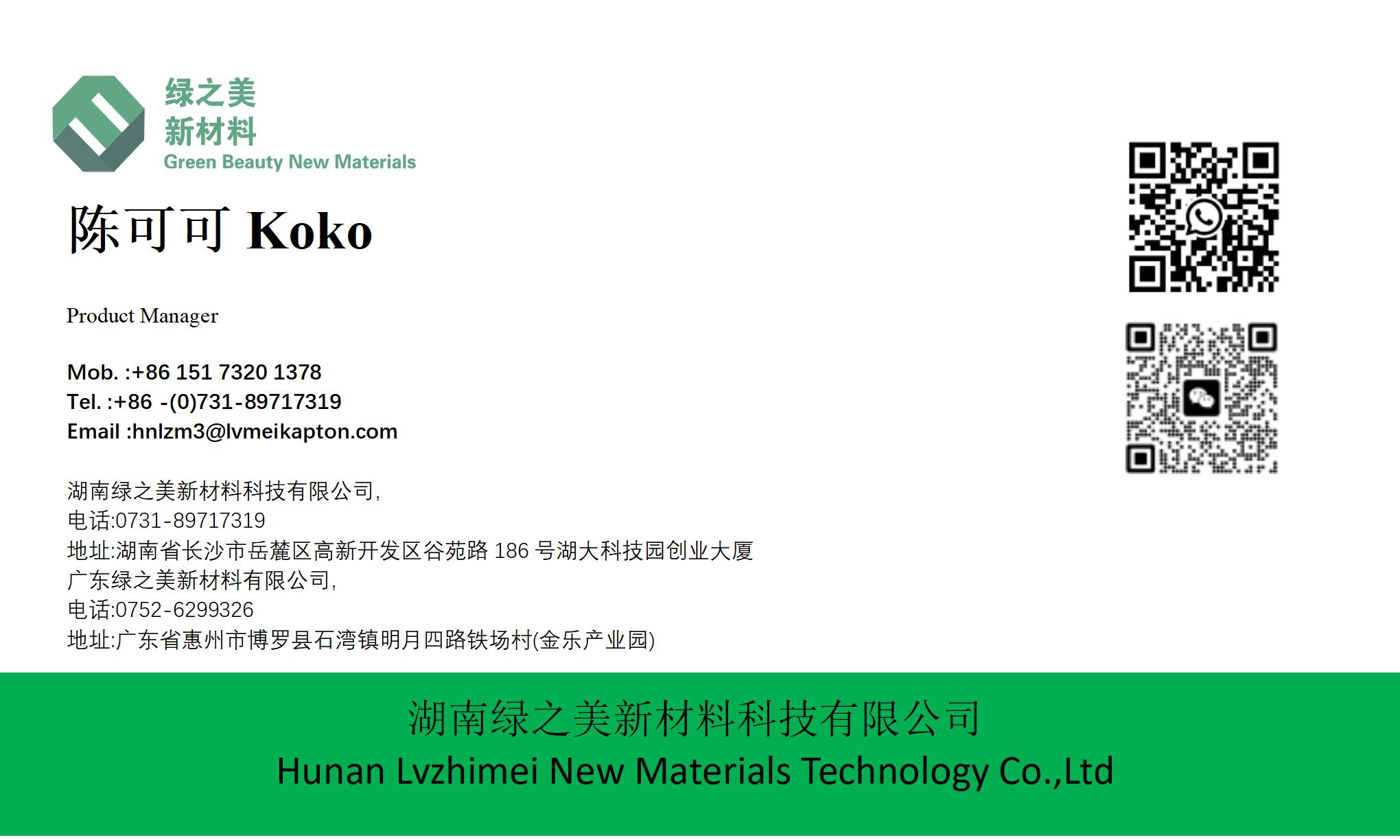