1. Temperature Resistance: Beyond the Specified Range
One of the most significant limitations of self-adhesive back blocking tape is its temperature threshold. While products like tesa 51136 and 3M Scotch 233+ boast temperature resistance up to 100°C and 120°C, respectively, industrial processes often demand higher tolerances. For example, automotive underbody coatings may require exposure to temperatures exceeding 150°C during curing, while aerospace or metal fabrication processes can reach 200°C or more. Exceeding the tape’s rated temperature can lead to:
Adhesive degradation: The acrylic or rubber-based adhesive may soften, causing tape slippage or detachment.
Backing deformation: Materials like PE (polyethylene) or creped paper can warp, compromising the seal integrity.
Residue formation: High temperatures may cause adhesive migration, leaving stubborn残留胶 even on smooth surfaces.
Table: Temperature Limits vs. Industrial Processes
Product | Rated Temp. | Industrial Use Limitations |
---|
tesa 51136 | 100°C | Unsuitable for powder coating curing (150-200°C) or metal welding |
3M Scotch 233+ | 120°C (short) | Risk of adhesive residue in high-temp automotive baking |
tesa 53128 (yellow) | 80°C (long) | Inadequate for electronics soldering (260°C) |
2. Surface Compatibility: Challenges with Complex Geometries and Materials
The tape’s performance heavily depends on the substrate’s texture, porosity, and surface energy. Common issues include:
2.1. Poor Adhesion on Low-Surface-Energy Materials
Self-adhesive tapes struggle to bond effectively to plastics (e.g., PP, PE) or polished metal surfaces without pretreatment. For example, tesa 51134’s acrylic adhesive may exhibit weak adhesion on HDPE components, requiring mechanical anchoring or surface activation to achieve reliable blocking.
2.2. Limited Flexibility for Irregular Surfaces
Tapes with rigid backings (e.g., thick PET films) may not conform to sharp edges, deep recesses, or compound curves, leading to gaps and paint bleed. While products like tesa 53128 offer some flexibility with its micro-creped paper backing, excessive elongation can cause tape fracture or uneven coverage.
2.3. Incompatibility with Coatings and Solvents
Industrial paints containing aggressive solvents (e.g., xylene, toluene) can degrade tape adhesive, causing premature detachment or adhesive dissolution. For instance, 3M 233+’s acrylic adhesive may swell when exposed to prolonged solvent exposure, compromising its blocking efficacy.
3. Residue and Surface Contamination: Post-Removal Challenges
Despite claims of "no-residue" performance, self-adhesive tapes can leave behind sticky remnants or alter the surface finish, particularly under the following conditions:
Overstaying: Prolonged exposure (e.g., weeks instead of days) can cause adhesive curing and bonding enhancement, requiring aggressive removal methods.
High Humidity: Moisture absorption by paper backings or adhesive layers can weaken the bond, leading to residue or tape tearing.
High-Surface-Energy Materials: Surfaces like polished aluminum or glass can trap adhesive residues, necessitating costly post-processing cleaning.
Case Study: Automotive Paint Shops
Tesa 51136’s PE backing is prone to residual adhesive transfer on plastic bumper parts, often requiring additional wipe-down with isopropyl alcohol, delaying production timelines.
4. Environmental and Regulatory Compliance: VOCs and Waste Management
Industrial applications must adhere to stringent environmental regulations, posing challenges for traditional tape formulations:
VOC Emissions: Many acrylic and solvent-based adhesives release volatile organic compounds (VOCs) during curing or application, violating air quality standards.
Waste Disposal: Tape remnants, especially those containing plastic backings, contribute to non-biodegradable waste. Recycling options are limited, and incineration may release toxins.
Flammability: Some tape materials are combustible, posing fire hazards in industrial settings with open flames or sparks.
5. Durability and Reusability: Limited Long-Term Performance
Self-adhesive tapes are designed for single-use applications. Repeated application and removal cycles can:
Damage the backing material, reducing its tear resistance.
Weaken the adhesive’s cohesion, causing slippage or incomplete seals.
Accumulate dust or contaminants, impairing subsequent adhesion.
Table: Reusability Comparison
Product | Backing Material | Reusability |
---|
tesa 51136 (PE) | PE Film | Poor (≤1 reuse) |
3M 233+ | Creped Paper | Fair (≤2 reuses with surface prep) |
tesa 53128 | Micro-Creped Paper | Fair (≤3 reuses) |
6. Cost and Efficiency: Balancing Performance with Budget
High-performance tapes with advanced adhesive systems and backings (e.g., silicone-based formulations) command premium prices, making them cost-prohibitive for large-scale applications. Additionally, manual application and post-removal cleanup can increase labor costs, offsetting the tape’s convenience advantages.
Example Calculation:
For a medium-sized automotive body shop喷漆 100 vehicles/month using tesa 51136 (1450mm x 66m roll, 500/roll),tapecostsalonewouldexceed 5,000/month, not including labor for tape application and residue removal.
7. Specialized Application Limitations
Beyond general喷漆遮蔽, specific industrial uses pose additional challenges:
Electronics Manufacturing: Thin tapes may not withstand wave soldering temperatures (260°C), while thicker options can interfere with component placement.
Food Processing: Adhesives must meet FDA/EFSA food contact regulations, limiting available tape options.
Outdoor Use: UV exposure can degrade tapes, causing brittleness and adhesive failure within months.
Conclusion: Mitigating Limitations through Smart Selection and Process Optimization
Self-adhesive back blocking tape remains a valuable tool in industrial喷漆 protection, but its effectiveness hinges on understanding its constraints. Key recommendations include:
Temperature Matching: Select tapes with temperature ratings 20-30°C above process requirements.
Surface Preparation: Use primers or corona treatment for low-energy surfaces.
Residue Management: Implement controlled peel-off techniques (e.g., low-angle, warm removal).
Eco-friendly Alternatives: Explore water-based adhesive tapes or reusable silicone masking systems.
Process Integration: Evaluate robotic tape application for complex geometries.
By addressing these limitations through material advancements and process optimization, manufacturers can maximize the benefits of self-adhesive tape while minimizing its drawbacks in industrial喷漆 applications.
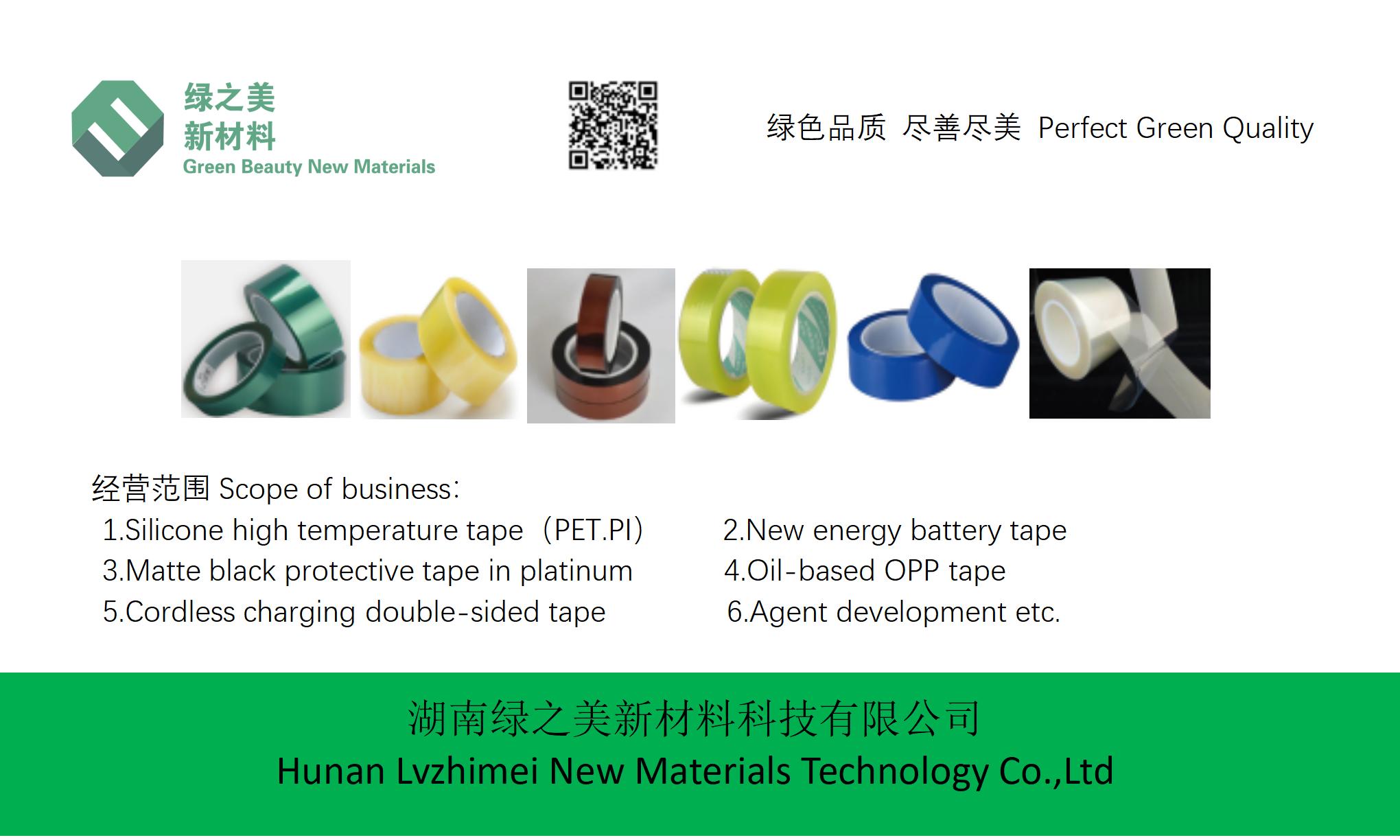
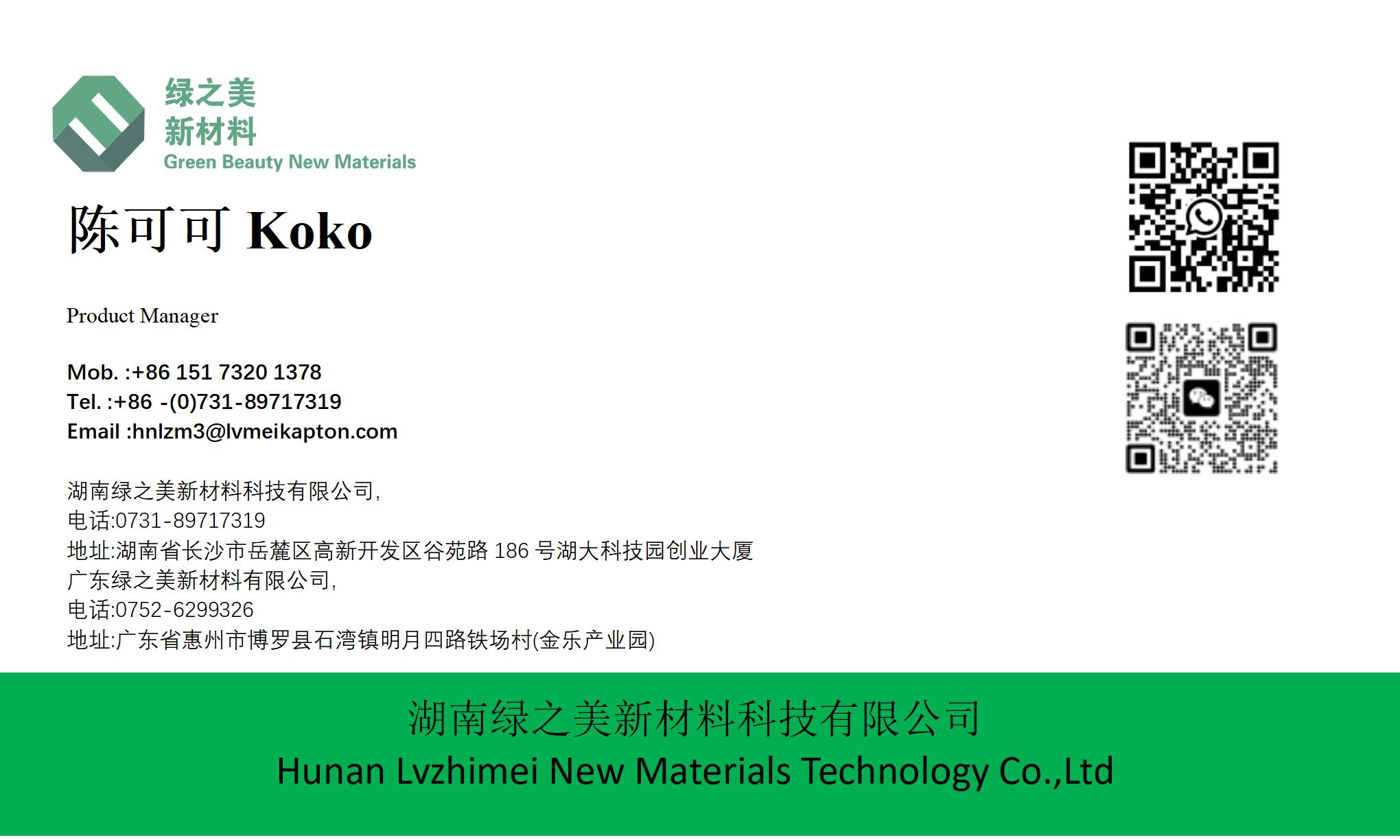