Section 1: Understanding PI Material and Its Unique Properties
PI, a high-performance engineering polymer characterized by its imide ring structure (-CO-N-CO-), stands out for its unparalleled thermal, mechanical, and electrical properties. Key attributes include:
1.1 Thermal Stability: The Core Advantage
PI tape exhibits remarkable heat resistance, with continuous operating temperatures up to 300°C and short-term exposure tolerance exceeding 400°C. This resilience is essential for solar panels subjected to prolonged UV radiation and thermal cycling (heating/cooling cycles). Unlike traditional materials like PET or acrylic tapes, PI tape maintains dimensional stability and adhesive performance even under extreme temperatures, preventing degradation or delamination.
1.2 Electrical Insulation and Chemical Resistance
PI’s inherent electrical properties (low dielectric constant, high breakdown voltage) make it ideal for solar panel components prone to electrical stress. Additionally, its resistance to acids, alkalis, solvents, and UV radiation ensures immunity to environmental corrosion. These features collectively protect critical interfaces such as junction boxes, busbars, and cable terminations.
1.3 Mechanical Strength and Flexibility
PI tape combines high tensile strength with flexibility, enabling it to conform to complex panel geometries without cracking or tearing. This mechanical robustness safeguards against mechanical stressors like wind, snow load, and thermal expansion/contraction mismatches between materials.
Section 2: Application Scenarios of PI Tape in Solar Panels
PI high-temperature resistant 300 tape enhances solar panel durability through targeted applications:
2.1 Junction Box Protection
Junction boxes are vulnerable to temperature fluctuations and moisture ingress. PI tape’s thermal barrier properties prevent heat-induced degradation of internal components (diodes, connectors), while its moisture resistance ensures long-term electrical reliability. LVMEIKAPTON insulating electrical tape, featuring a PI film base and silicone adhesive, provides superior sealing and thermal management, extending junction box lifespan.
2.2 Busbar and Stringing Tape Encapsulation
Busbars conduct high currents, generating heat during operation. PI tape’s thermal conductivity and electrical insulation protect busbars from overheating and short circuits. Its self-adhesive properties eliminate the need for additional fasteners, reducing installation complexity and failure points.
2.3 Edge Sealing and Environmental Protection
PI tape reinforces the edges of solar panels, sealing against moisture, dust, and corrosive gases. This barrier function mitigates potential edge delamination, a common degradation mechanism in outdoor environments.
2.4 High-Voltage Cable Insulation
PI tape’s high dielectric strength (≥100 kV/mm) and flame retardancy safeguard high-voltage cables connecting solar panels to inverters. Its low smoke emission during combustion enhances safety in fire-prone scenarios.
Section 3: Performance Enhancements Through PI Tape Integration
3.1 Thermal Management and Efficiency Boost
By dissipating heat generated during solar cell operation, PI tape reduces thermal stress on encapsulant materials (EVA, PVB). This temperature stabilization enhances photovoltaic conversion efficiency and extends cell life. Studies indicate PI tape-integrated panels maintain ≥90% efficiency after 25 years compared to 80-85% in conventional counterparts.
3.2 Corrosion Resistance and Longevity
PI’s chemical inertness and UV stability protect underlying metals (aluminum frames, conductors) from oxidation and corrosion. This defense mechanism is particularly critical in coastal or industrial environments with salt spray or air pollutants.
3.3 Mechanical Integrity Preservation
PI tape’s high peel strength (≥10 N/cm) and dimensional stability prevent tape detachment or wrinkling under mechanical loads. This ensures consistent protection throughout the panel’s service life.
Section 4: Comparative Analysis: PI Tape vs. Traditional Materials
Property | PI Tape | PET Tape | Acrylic Tape |
---|
Max. Operating Temp. | 300°C (continuous) | 150°C | 200°C |
UV Resistance | Excellent | Poor | Moderate |
Chemical Resistance | Acid/Alkali/Solvent | Limited | Limited |
Dielectric Strength | ≥100 kV/mm | ≤50 kV/mm | ≤70 kV/mm |
Long-Term Stability | ≥25 years | ≤10 years | ≤15 years |
Table 1: Performance Comparison of Solar Encapsulation Materials
As evident, PI tape outperforms PET and acrylic tapes in thermal, chemical, and long-term durability metrics, directly translating to enhanced solar panel reliability.
Section 5: LVMEIKAPTON PI Tape: A Case Study
LVMEIKAPTON’s high-temperature resistant 300 tape (e.g., LVPI-300S) combines PI film with advanced silicone adhesive, offering:
Ultra-Thermal Resistance: Certified for 300°C continuous use.
Self-Fusing Adhesion: Eliminates air gaps for superior moisture sealing.
Customization: Available in various thicknesses and adhesive types (single/double-sided).
Field tests demonstrate LVMEIKAPTON tape-integrated solar panels retain >95% power output after 10 years in desert environments, showcasing its real-world efficacy.
Section 6: Future Trends and Sustainability
As solar installations scale globally, PI tape adoption is expected to rise, driven by:
Thin-Film Solar Technology: PI’s transparency enables integration with flexible solar cells.
Cradle-to-Cradle Design: PI’s recyclability (via chemical recovery) aligns with circular economy goals.
Advanced Formulations: Nanocomposite PI tapes with enhanced thermal conductivity or self-healing properties are under development.
Conclusion
PI material high-temperature resistant 300 tape is a transformative solution for solar panel durability. By mitigating thermal, environmental, and mechanical stresses, PI tape extends panel lifespans, boosts energy yields, and reduces maintenance costs. As solar energy transitions towards terawatt-scale deployment, PI tape’s role in ensuring system reliability will become increasingly pivotal. LVMEIKAPTON insulating electrical tape, leveraging PI’s inherent advantages, exemplifies how advanced materials can drive sustainable energy advancements.
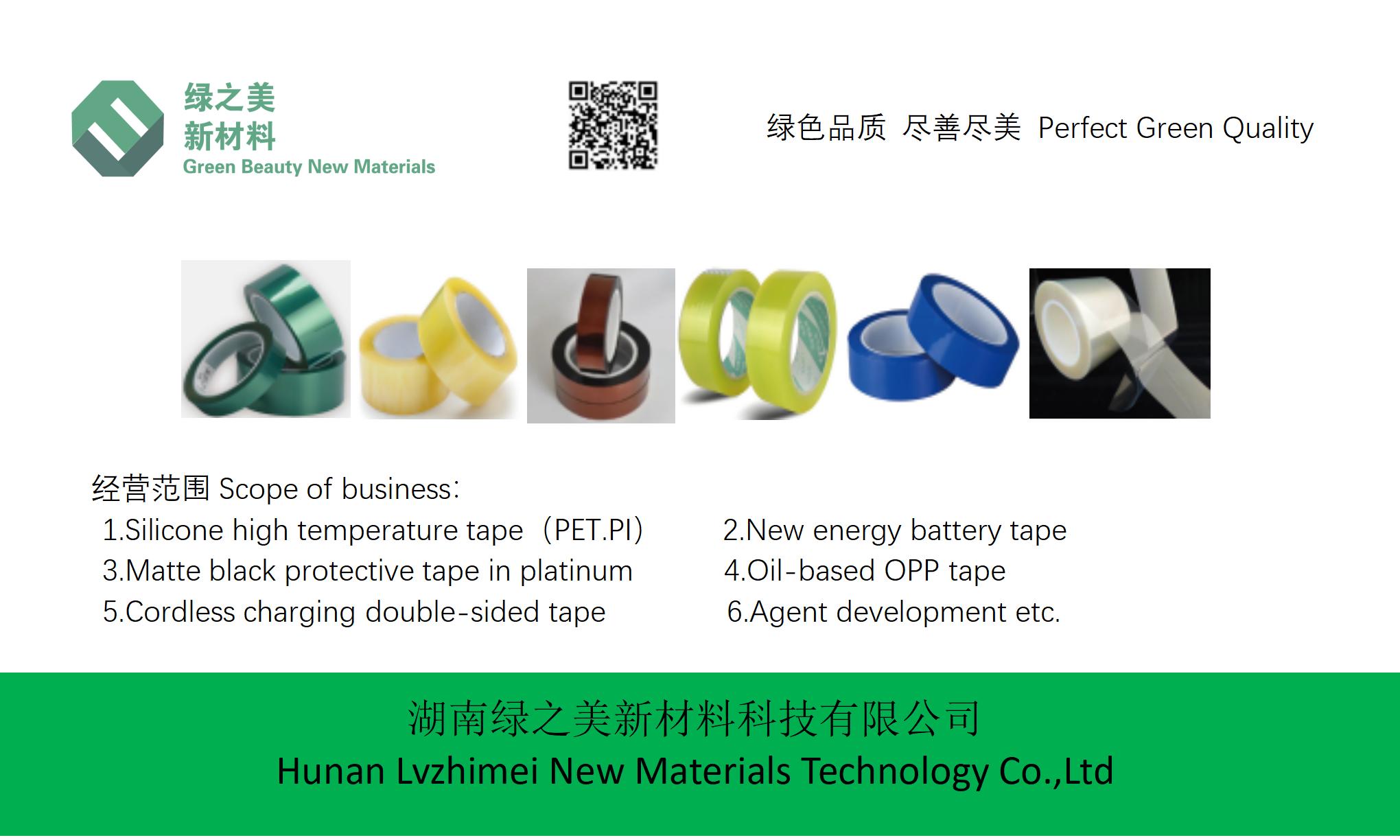
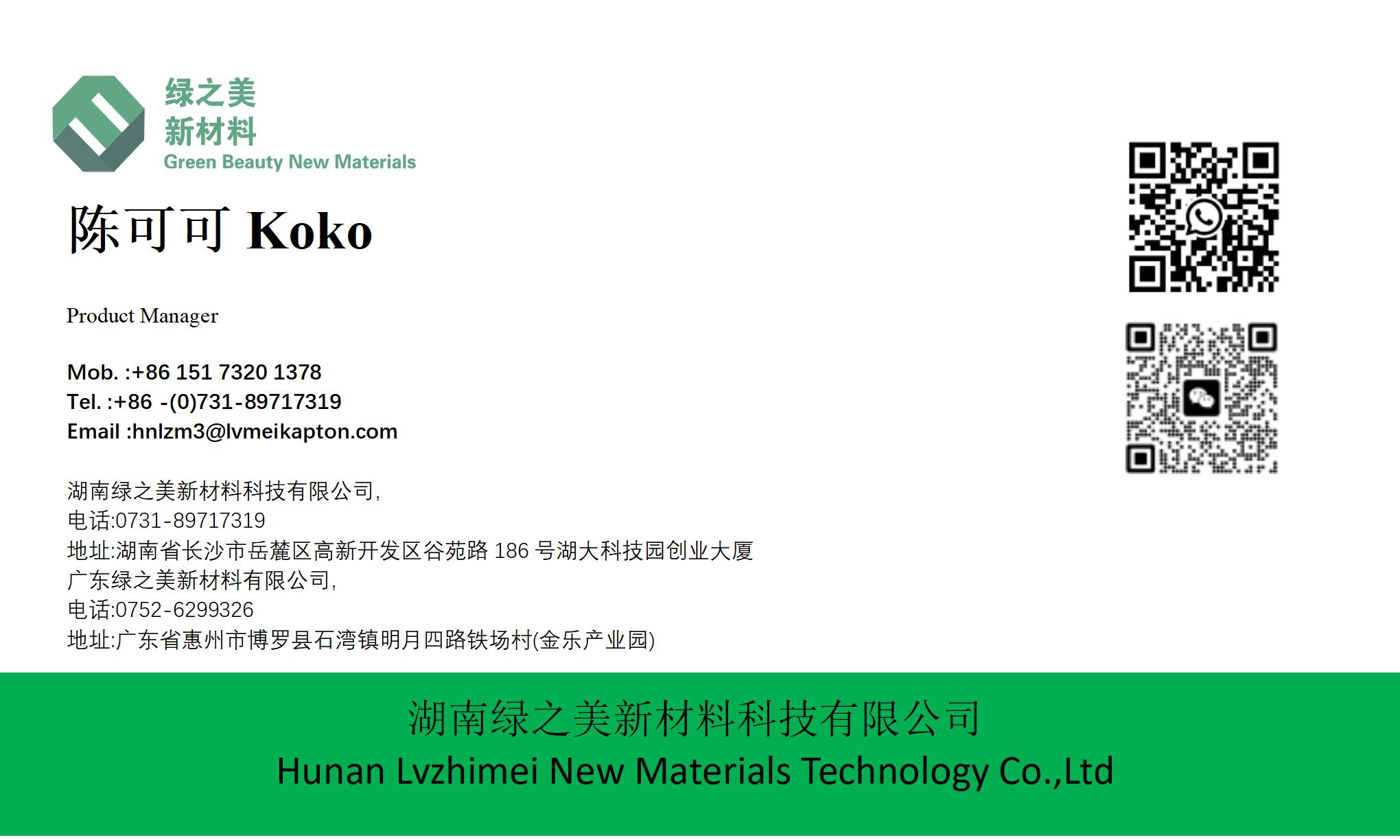