1. Hidden Risks of Using SABT in Automotive Wiring
1.1 Adhesion Degradation Over Time
One of the primary concerns with SABT is its long-term adhesion performance. While the tape boasts "strong adhesion and blocking high-temperature tape" properties, real-world conditions can significantly impact its bonding strength. Key factors include:
● Thermal Cycling: Engine compartments experience extreme temperature fluctuations (-40°C to +150°C), causing the adhesive to expand and contract repeatedly. Over time, this cycling may lead to adhesive fatigue, detachment, or delamination from the wire harness.
● Chemical Exposure: Automotive fluids (e.g., oil, coolant, brake fluid) and environmental contaminants (e.g., road salt) can penetrate the tape barrier and degrade the adhesive. This chemical interaction weakens the bond, increasing the risk of wire insulation exposure.
● Vibration: Constant vibrations from engine operation or road颠簸 can cause mechanical stress on the tape-adhesive interface. If the tape lacks sufficient shear resistance, it may gradually peel off, compromising the wire protection.
Table 1: Adhesion Degradation Factors and Consequences
Risk Factor | Impact |
Thermal cycling | Adhesive softening/hardening → bond failure |
Chemical exposure | Corrosion of adhesive → tape detachment |
Vibration stress | Progressive delamination → wire abrasion |
Humidity absorption | Adhesive swelling → reduced adhesion |
1.2 Poor Electrical Insulation and Risk of Short Circuits
SABT is often used to isolate wires from high-voltage or sensitive components. However, inferior-quality tapes may exhibit the following issues:
● Insufficient Dielectric Strength: If the tape’s electrical insulation properties are subpar, it may fail under high voltages, leading to arcing or short circuits. This risk is exacerbated in hybrid/electric vehicles (HEVs/EVs) with higher operating voltages (e.g., 400V+).
● Micro-Cracks and Porosity: Manufacturing defects or improper application (e.g., bubbles during wrapping) can create microscopic pathways for moisture or contaminants. Over time, these cracks may allow current leakage, causing electrical failures or fires.
1.3 Health and Environmental Hazards
Self-adhesive tapes typically contain volatile organic compounds (VOCs) and plasticizers during production. While these chemicals enhance flexibility and adhesion, they pose risks during application and disposal:
● VOC Emissions: When SABT is applied in confined spaces (e.g., underhood repairs), VOCs may accumulate, posing health hazards to technicians through inhalation or skin contact.
● Environmental Impact: Most tapes are made from non-biodegradable materials (e.g., PVC or PET). Improper disposal may contribute to environmental pollution, particularly if the tape contains residual adhesives or contaminants.
1.4 Manufacturing and Application Deficiencies
Unregulated SABT products may lack critical performance certifications (e.g., UL, SAE, or ISO standards), exposing users to the following risks:
● Inferior Material Quality: Counterfeit or low-quality tapes often use cheaper adhesives and backing films, resulting in poor heat resistance, chemical susceptibility, or adhesion failure.
● Application Errors: Users may inadvertently dilute the adhesive by adding water or use incorrect wrapping techniques (e.g., insufficient overlap or stretching), compromising tape effectiveness.
2. Case Studies: Real-World Consequences of SABT Risks
2.1 Engine Wiring Failure Due to Thermal Degradation
A recent study by the National Highway Traffic Safety Administration (NHTSA) found that a certain model of vehicles experienced frequent engine control module (ECM) failures. Investigation revealed that SABT used to protect the ECM wiring had delaminated due to prolonged exposure to engine heat (125°C+). The tape detachment exposed wires to abrasion, eventually causing short circuits and ECM malfunctions.
2.2 Electric Vehicle Fire Hazard
In a HEV recall case, the OEM discovered that the SABT protecting high-voltage battery cables had developed micro-cracks after 2 years of use. Moisture intrusion through these cracks corroded the cable insulation, leading to arcing and fires. The root cause was traced to the tape’s inadequate dielectric strength (rated only for 300V vs. system voltage of 600V).
3. Mitigation Strategies for SABT-Related Risks
To ensure safe and reliable SABT usage, the following measures are recommended:
3.1 Material Selection and Testing
● Certification Compliance: Choose tapes certified to automotive standards (e.g., SAE J1127, ISO 6722) and validated for specific environmental conditions (temperature, humidity, chemical resistance).
● Performance Testing: Conduct laboratory tests (e.g., thermal aging, salt spray, peel adhesion) to confirm tape durability before field deployment.
3.2 Application Best Practices
● Surface Preparation: Clean wire surfaces thoroughly to remove oils, dirt, or oxidation using isopropyl alcohol.
● Wrapping Techniques: Apply tape with 50% overlap, avoiding stretching or bubbles. Use heat guns (if tape allows) to activate thermosetting adhesives.
● Environmental Monitoring: Install tapes in areas with controlled temperatures (e.g., avoid direct engine heat) and protect from fluids using additional barriers.
3.3 Maintenance and Inspection
● Regular Audits: Periodically inspect taped areas for signs of delamination, discoloration, or cracking, especially in high-stress regions.
● Replacement Timelines: Replace tapes based on manufacturer recommendations (e.g., every 5 years for engine compartments) or after exposure to extreme conditions.
4. Future Directions: Advancements in Tape Technology
To address current risks, research is focusing on:
● Nano-Modified Adhesives: Developing self-healing polymers that autonomously repair micro-cracks and maintain adhesion under thermal cycling.
● Smart Tape Sensors: Embedding conductive inks or sensors within the tape to detect early signs of detachment or insulation failure.
● Biodegradable Materials: Transitioning to eco-friendly tapes made from plant-based polymers while maintaining performance.
Conclusion
While self-adhesive back blocking spray paint tape offers essential protection for automotive wiring, its hidden risks demand careful consideration. Adhesion degradation, electrical insulation failures, environmental hazards, and quality inconsistencies can pose severe safety and reliability threats. By adopting stringent material selection, application protocols, and maintenance practices, stakeholders can mitigate these risks and ensure long-term performance. As tape technologies evolve, future innovations will further enhance reliability while addressing sustainability concerns.
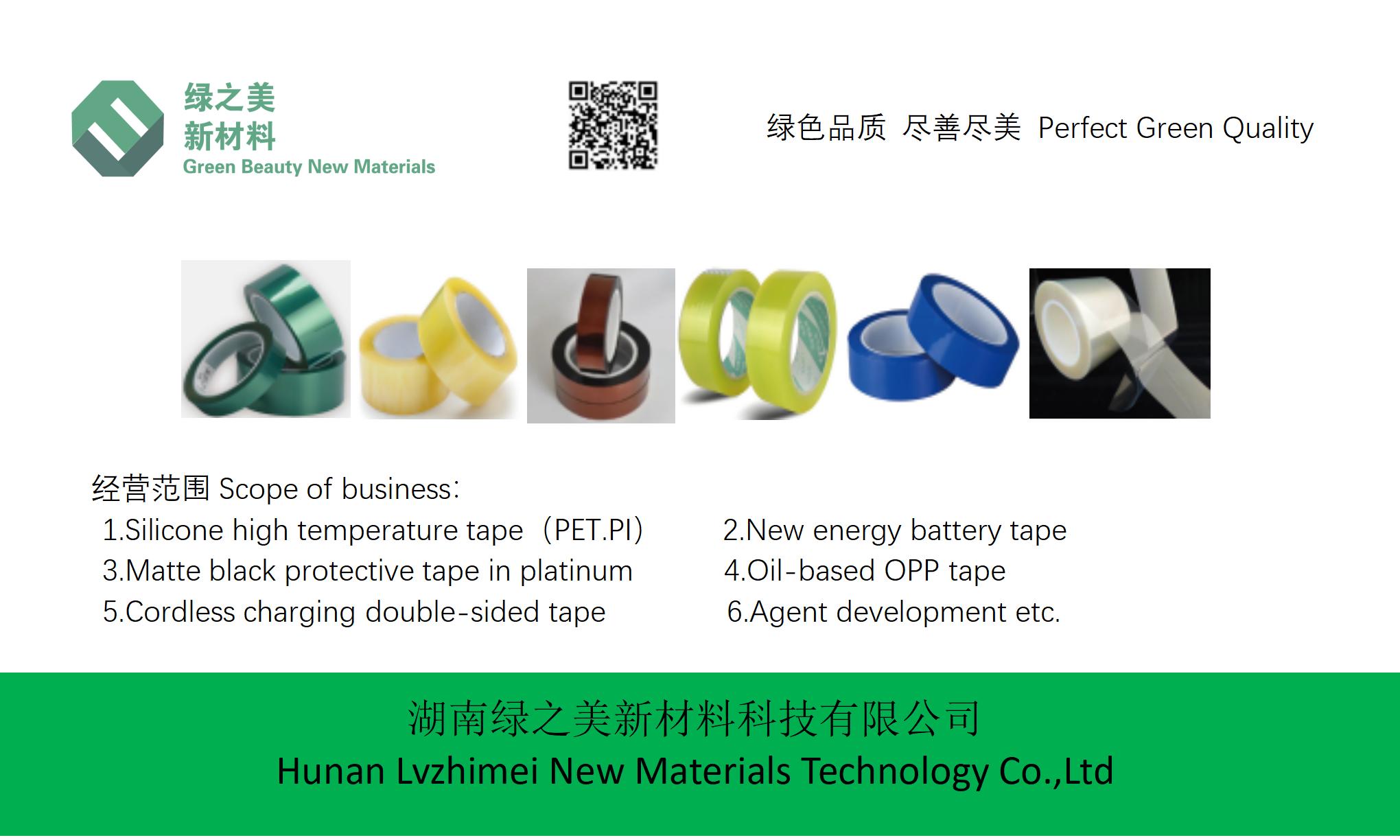
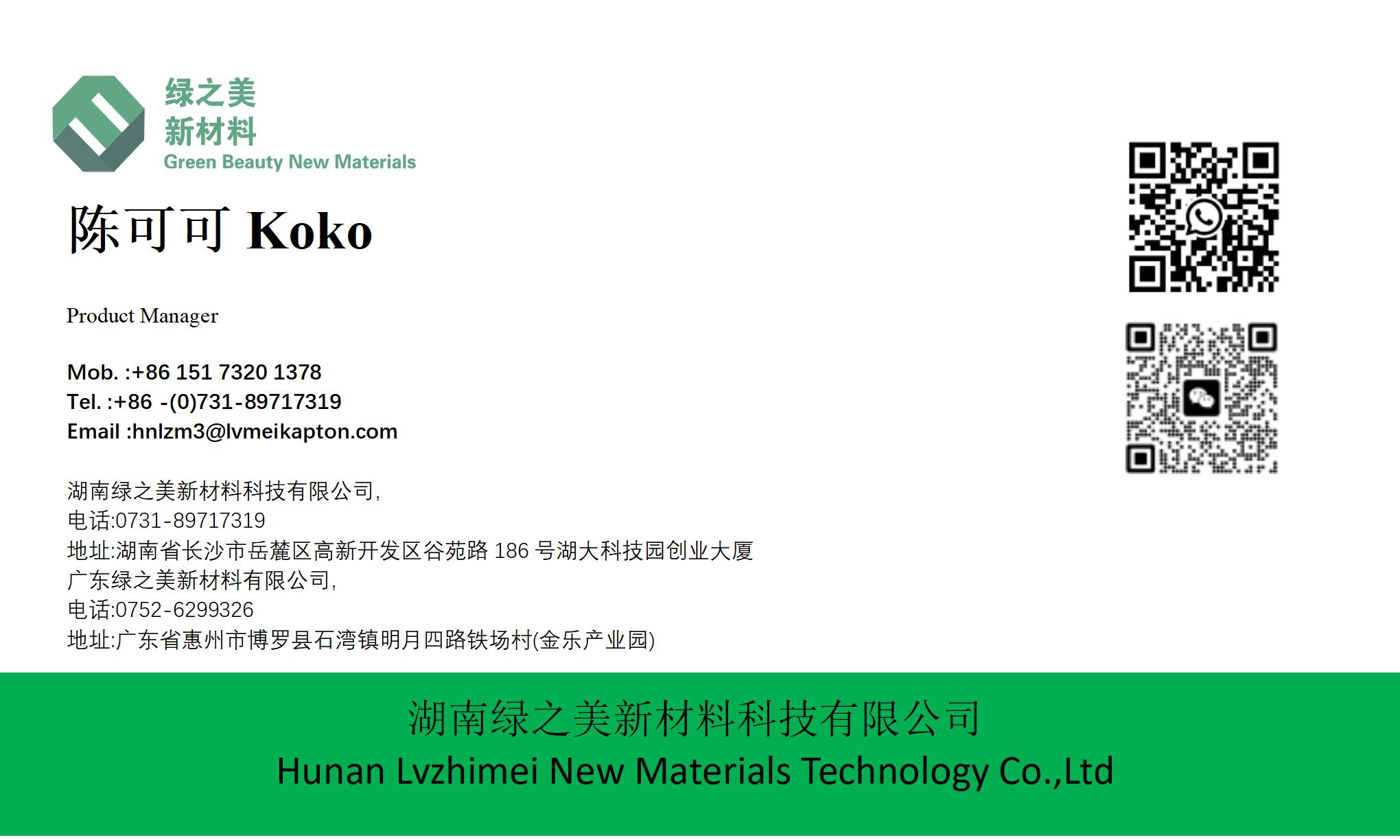