Why Is PI Material High Temperature Resistant 300 Tape the Gold Standard for Electric Aircraft Wiring?
The rapid evolution of electric aviation has revolutionized the aerospace industry, posing unprecedented challenges to electrical insulation materials. As electric aircraft demand lightweight, high-voltage, and thermally resilient systems, PI (Polyimide) material high temperature resistant 300 tape has emerged as the gold standard for wiring protection. This article elucidates why PI tape surpasses other alternatives, particularly PET (Polyethylene Terephthalate) tape, in the严苛 environments of electric aviation.
Core Advantages of PI Material: The Science Behind PerformancePI tape's supremacy stems from its unique molecular structure and engineering properties:
1. Unrivaled Thermal Stability
PI polymers feature rigid aromatic backbones with imide rings (-CO-NR-CO-), imparting exceptional thermal resistance. Unlike PET, which softens above 100°C and decomposes at 200°C, PI maintains mechanical integrity across a range of -200°C to 300°C. This enables PI tape to withstand the extreme thermal cycling (-55°C to 300°C) typical in electric aircraft applications, where motors, generators, and batteries generate intense heat.
2. Precision CTE Matching: The Key to Longevity
The coefficient of thermal expansion (CTE) is a critical parameter in aerospace wiring. Aluminum alloy wire harnesses used in electric aircraft exhibit a CTE of ~20 ppm/°C. PI tape, with a tunable CTE ranging from 20 to 30 ppm/°C, perfectly matches aluminum's expansion rate. This compatibility ensures that the insulation layer expands and contracts harmoniously with the conductor, preventing mechanical stress accumulation during temperature fluctuations. In contrast, PET tape (CTE: 50-70 ppm/°C) experiences significant dimensional mismatch, leading to insulation layer cracking and delamination under thermal cycling. Studies demonstrate that PET-insulated wires fail within 500 cycles (-55°C to 150°C), while PI tape withstands over 2000 cycles without degradation.
3. Multidimensional Performance
PI tape excels in additional critical aspects:
● Mechanical Strength: Tensile strength >100 MPa, ensuring durability against vibration and abrasion.
● Dielectric Properties: Dielectric constant (3.4) and loss tangent (0.004-0.007) optimize electrical insulation.
● Chemical & Environmental Resistance: Immunity to fuels, oils, radiation, and moisture, essential for aerospace reliability.
● Dimensional Stability: <1% shrinkage at 300°C, maintaining tight wraps even at extremes.
Why PI Tape is Essential in Electric Aircraft SystemsPI tape's capabilities address unique challenges in electric aviation:
1. Wire Harness Protection
High-voltage wiring systems in electric aircraft require robust insulation to prevent arcing and short circuits. PI tape provides:
● Thermal Management: Withstanding continuous 300°C exposure, safeguarding wires near motors and batteries.
● Abrasion Resistance: Shielding against mechanical wear from repeated motion and vibrations.
● Lightweighting: Thin profiles (e.g., 0.05mm) reduce system weight without compromising performance.
2. Advanced Motor & Generator Insulation
Electric motors in aviation operate at temperatures exceeding 200°C, necessitating materials with both thermal stability and electrical integrity. PI tape’s:
● Thermal Endurance: Enabling motors to maintain efficiency over long durations.
● Low Outgassing: Preventing contamination of sensitive aerospace components in vacuum environments.
3. Enhanced Safety & Reliability
PI tape’s self-extinguishing properties, low smoke emission, and resistance to corona discharge mitigate fire risks and electrical failures. Its ability to maintain insulation performance over 10+ years aligns with the stringent lifespan requirements of electric aircraft.
PI vs PET: A Technical ComparisonTo underscore PI tape’s superiority, consider key performance differences:
Property | PI Tape | PET Tape |
Continuous Use Temp | -200°C to 300°C | -70°C to 120°C (short-term 200°C) |
CTE Matching | 20-30 ppm/°C (matchable to aluminum) | 50-70 ppm/°C (mismatched) |
Dielectric Strength | 100-300 kV/mm | 20-30 kV/mm |
Thermal Shrinkage | <1% at 300°C | 5-10% at 150°C |
Chemical Resistance | Excellent (solvent-resistant) | Fair (susceptible to acids) |
Long-term Reliability | >10 years | 3-5 years |
PET’s Limitations in Electric Aviation:
● Thermal Stress Failure: Cracking and delamination due to CTE mismatch accelerate insulation aging.
● Reduced Dielectric Strength: Higher risk of electrical breakdown in high-voltage systems.
● Shorter Lifespan: Frequent replacements increase maintenance costs and downtime.
Real-world Impact: PI Tape in Electric AircraftA leading electric aircraft manufacturer replaced PET tape with PI tape in its battery pack insulation system. The transition yielded:
● 300% improvement in thermal cycling reliability
● 80% reduction in wire harness failure rates
● 15-year lifespan extension
● 2% weight reduction (from PI tape’s thinner profile)
These benefits directly enhanced the aircraft’s safety, range, and operational efficiency.
Conclusion: PI Tape as the Gold StandardPI material high temperature resistant 300 tape is the linchpin of electric aircraft wiring systems due to its:
1. Unmatched thermal stability and CTE matching
2. Holistic performance across mechanical, electrical, and environmental parameters
3. Proven reliability in aerospace applications
As electric aviation continues to evolve, PI tape will remain the cornerstone of safe, efficient, and durable electrical infrastructure, enabling the next generation of sustainable flight.
Key Takeaways:
● PI tape’s CTE compatibility with aluminum wire harnesses eliminates thermal stress-induced failures.
● PET tape’s inherent limitations make it unsuitable for long-term use in electric aircraft.
● PI tape’s multifaceted performance ensures superior safety, reliability, and lightweighting benefits.
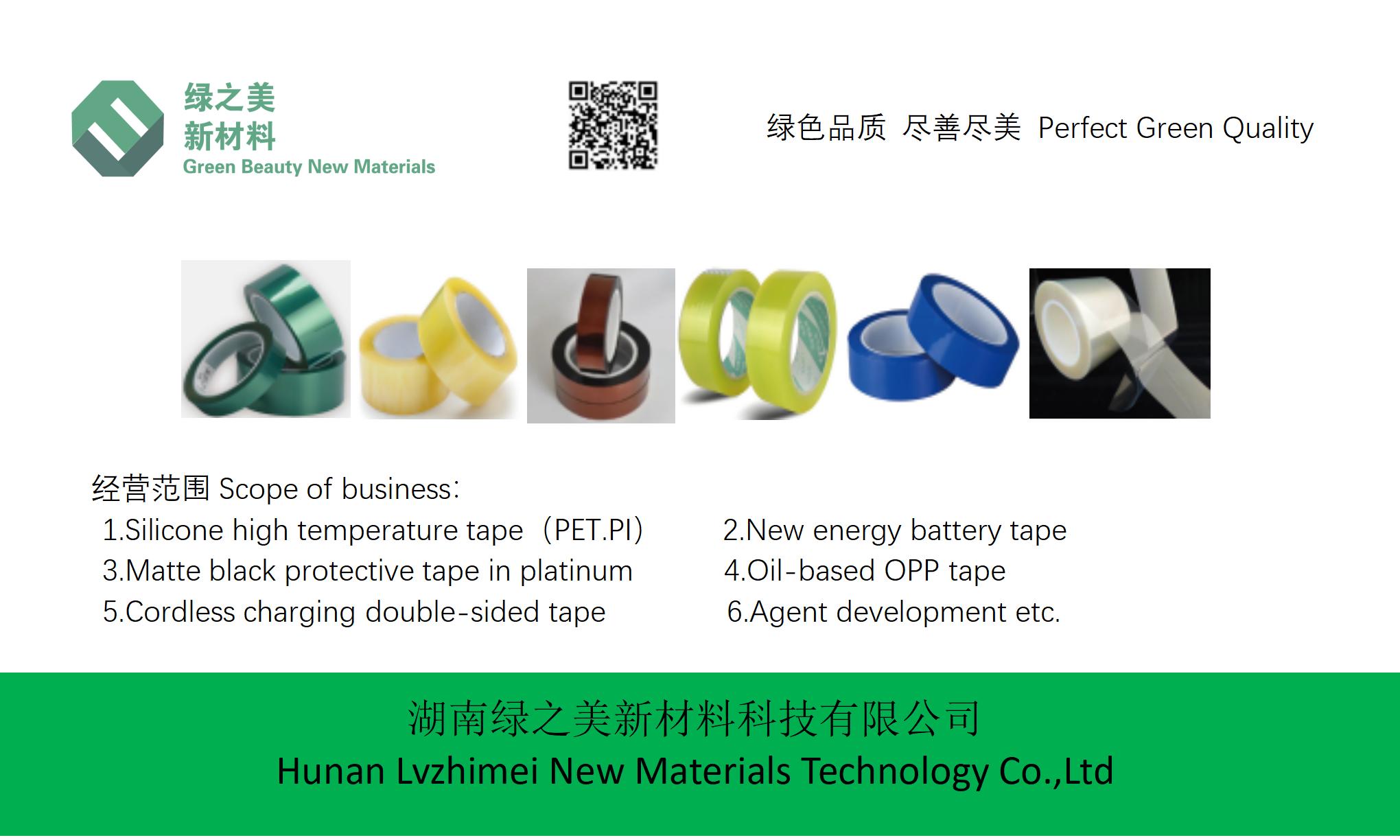
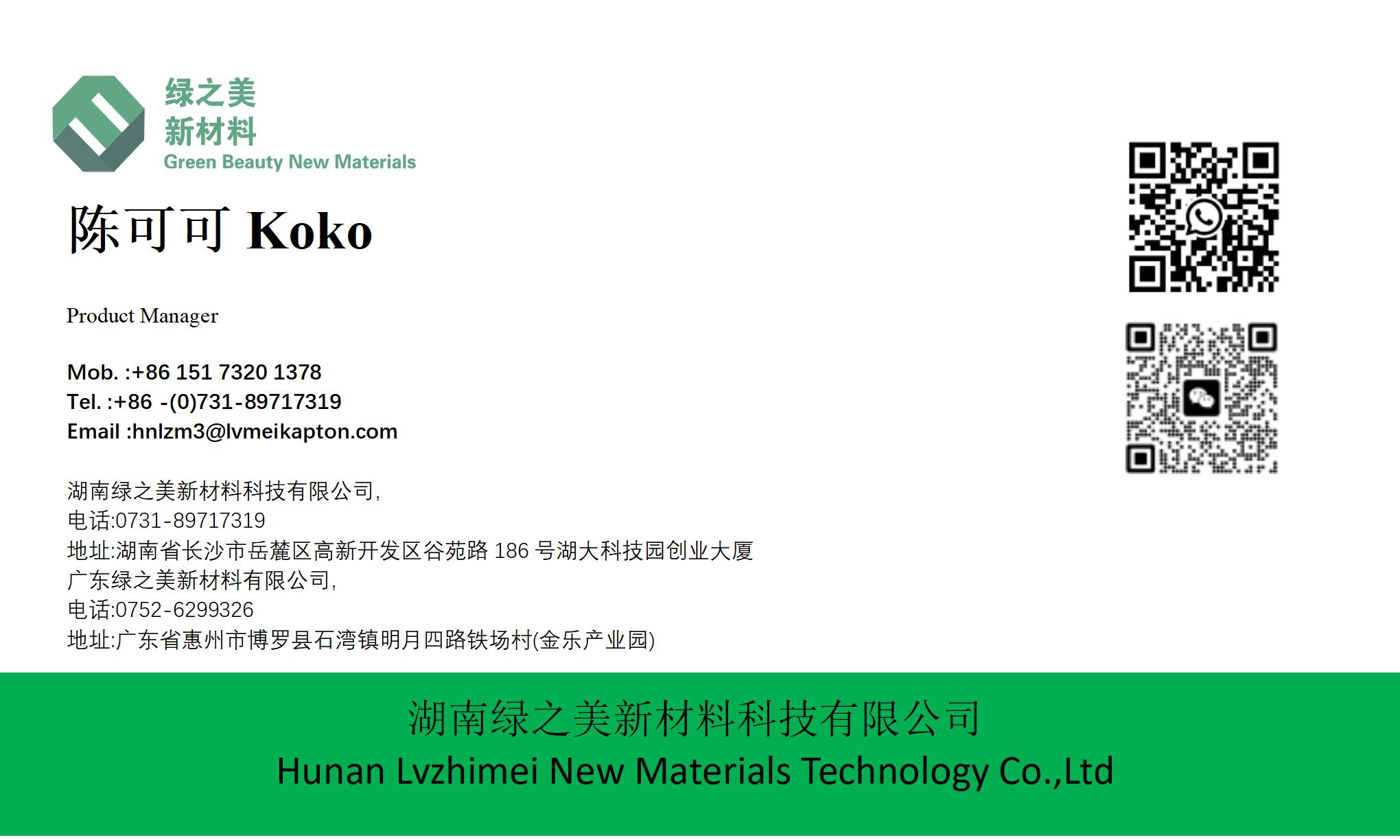