When Should You Use PET Material High-Temperature Tape in Electronics?
Introduction
In the rapidly advancing electronics industry, selecting the right materials is crucial to ensure product reliability and longevity. PET (Polyethylene Terephthalate) high-temperature tape, a versatile adhesive solution, plays a pivotal role in various manufacturing processes and applications. This comprehensive guide will explore the ideal scenarios for using PET tape, its key advantages, performance characteristics, and comparison with alternative materials like Kapton to help engineers and technicians make informed decisions. 1. Understanding PET High-Temperature TapePET tape, also known as PET high-temperature tape or PET silicone tape, is crafted from PET film coated with acrylic or silicone adhesive. It is available in transparent, black, and occasionally green variants. The tape’s composition offers exceptional thermal stability, chemical resistance, and mechanical strength, making it suitable for demanding environments. Key features include:
● Thermal Performance: Long-term resistance to temperatures up to 100-120°C, with short-term exposure capability reaching 140-200°C.
● Dimensional Stability: Minimal shrinkage or deformation under heat, ensuring consistent performance.
● Adhesion Properties: Strong initial and sustained tackiness to plastics, rubbers, metals, and other substrates.
● Ease of Processing: Easily die-cut and processed, reducing manufacturing complexity.
Table 1: Key Specifications of PET High-Temperature Tape
Property | Description |
Thickness Range | 0.05mm – 0.2mm |
Temperature Range | Long-term: 100-120°C; Short-term: 140-200°C |
Adhesive Type | Acrylic or silicone |
Common Colors | Transparent, black, green |
Application Industries | Electronics, automotive, power, aerospace, construction |
2. Ideal Applications in ElectronicsPET tape’s unique properties make it indispensable in several electronic manufacturing and protection processes:
2.1. Printed Circuit Board (PCB) AssemblyDuring SMT (Surface Mount Technology) processes, PET tape provides essential protection:
● Masking for Wave Soldering: Shields delicate components like resistors and capacitors from molten solder during wave soldering, preventing damage.
● Gold Fingerprint Protection: Acts as a barrier during PCB gold plating, preventing contamination and ensuring precise contacts.
● Thermal Protection: Safeguards components during reflow soldering processes (up to 260°C for short periods).
● Temporary Fixing: Secures components during assembly, avoiding displacement.
2.2. Component Insulation and BondingPET tape excels in insulating and bonding electronic components subjected to high temperatures:
● Coil Insulation: Wraps transformer and motor coils, resisting thermal stress and voltage spikes.
● Battery Assembly: Bonds and insulates battery cells and tabs, enhancing safety in lithium-ion batteries.
● Heating Element Encapsulation: Protects heating elements in appliances like hairdryers and coffee machines.
2.3. Cable Management and ProtectionPET tape plays a vital role in organizing and safeguarding cables:
● Wire Wrapping: Bundles and insulates wires in automotive and industrial settings, resisting abrasion and chemicals.
● Terminal Protection: Seals connectors and terminals, preventing corrosion and short circuits in harsh environments.
2.4. Masking for High-Temperature ProcessesIn powder coating or spray painting, PET tape masks electronic parts (e.g., metal housings) to protect non-coated areas. Its high-temperature resistance ensures no adhesive residue post-removal.
3. Advantages Over Alternative MaterialsWhile materials like Kapton (polyimide) offer superior performance, PET tape provides cost-effective solutions in many scenarios. The following table compares key attributes:
Table 2: PET vs. Kapton Comparison
Attribute | PET Tape | Kapton Tape |
Temperature Range | Long-term: 100-120°C; Short-term: 140-200°C | Long-term: 180-260°C; Short-term: >300°C |
Cost | Economical for mid-range applications | Higher cost due to advanced material and manufacturing |
Flexibility | Moderately flexible; suitable for flat surfaces | Highly flexible; conforms to curved surfaces |
Adhesive Options | Acrylic (standard) or silicone (high-temperature) | Silicone or acrylic |
Dielectric Strength | Good (≤8.5kV) | Excellent (≤10kV) |
Common Uses | General-purpose insulation, masking, bonding | Extreme environments (e.g., aerospace, cryogenic systems) |
When to Choose PET Tape:
● When applications require temperatures ≤200°C.
● For cost-sensitive projects where Kapton’s premium features are unnecessary.
● When bonding or insulating rigid components with limited flexibility requirements.
4. Performance ConsiderationsTo maximize PET tape’s efficacy, consider the following:
4.1. Temperature DurabilityWhile PET tape withstands high temperatures, prolonged exposure above its rated limit may cause adhesive degradation or tape brittleness. Always verify the manufacturer’s temperature specifications.
4.2. Chemical ResistancePET tape resists common solvents, oils, and acids but may degrade when exposed to strong alkalis or prolonged UV radiation. Select tapes with UV stabilizers for outdoor applications.
4.3. Surface PreparationClean and degrease substrates (e.g., metals, plastics) before applying tape to ensure optimal adhesion. Rough surfaces may require pretreatment or textured tapes.
4.4. Storage and HandlingStore PET tape in environments with 25°C and 65% relative humidity to prevent moisture absorption, which can weaken adhesive performance. Avoid stretching the tape during application to maintain dimensional stability.
5. Key Industries and Use CasesPET tape’s versatility extends across multiple sectors:
5.1. Automotive Electronics
● Engine compartment wire harnesses: Protects wiring from heat, oil, and vibrations.
● Sensor and control module insulation: Shields electronics from underhood temperatures (up to 150°C).
● Battery pack assembly: Bonds and insulates battery cells in electric vehicles.
5.2. Electronics Manufacturing
● PCB fabrication: Masks gold fingers, protects components during soldering.
● LED assembly: Secures LED strips during high-temperature curing processes.
● Capacitor and resistor wrapping: Provides thermal and mechanical protection.
5.3. Power Electronics
● Transformer and inductor winding insulation: Resists thermal cycling and electrical stress.
● High-voltage cable termination: Shields cable ends from arcing and heat.
5.4. Aerospace and Defense
● Avionics wiring protection: Insulates cables exposed to engine heat and vibrations.
● Radar and communication equipment bonding: Secures components in high-temperature environments.
6. Selecting the Right PET TapeTo determine the optimal PET tape for a specific application, consider:
6.1. Temperature RequirementsMatch the tape’s rated temperature to process demands. For example, a powder coating oven at 180°C requires a tape with a short-term rating above this temperature.
6.2. Adhesive Type
● Acrylic Adhesive: Ideal for general-purpose applications with moderate temperatures and good initial tack.
● Silicone Adhesive: Suited for higher temperatures (up to 200°C) and superior resistance to chemicals and solvents.
6.3. Tape ThicknessThicker tapes (0.1mm – 0.2mm) offer better mechanical protection but may be harder to die-cut. Thinner variants (0.05mm – 0.08mm) are suitable for precise applications.
6.4. Surface CompatibilityEnsure the tape adheres well to the target substrate (e.g., PET tape performs exceptionally on plastics, metals, and ceramics).
7. Common Misconceptions and Best PracticesMisconception #1: PET tape is interchangeable with Kapton.Clarification: While both materials offer high-temperature resistance, Kapton surpasses PET in terms of thermal durability, flexibility, and dielectric strength. Use PET for applications with temperatures ≤200°C; Kapton for more extreme conditions.
Misconception #2: PET tape leaves residue after removal.Clarification: Quality PET tapes designed for high temperatures should leave no residue when removed within their rated temperature range. Select tapes labeled as “residue-free” for critical applications.
Best Practices:
● Conduct small-scale tests to validate tape performance under actual conditions.
● Use tape applicators for consistent application, avoiding bubbles or wrinkles.
● Follow manufacturer guidelines for storage, handling, and removal techniques.
ConclusionPET high-temperature tape is a reliable, cost-effective solution for electronic applications requiring thermal protection, insulation, and bonding. By understanding its strengths—such as thermal stability, chemical resistance, and ease of processing—engineers can optimize product reliability while balancing budget constraints. Whether in automotive electronics, PCB assembly, or power electronics, PET tape plays a vital role in ensuring components withstand the rigors of modern manufacturing and operation.
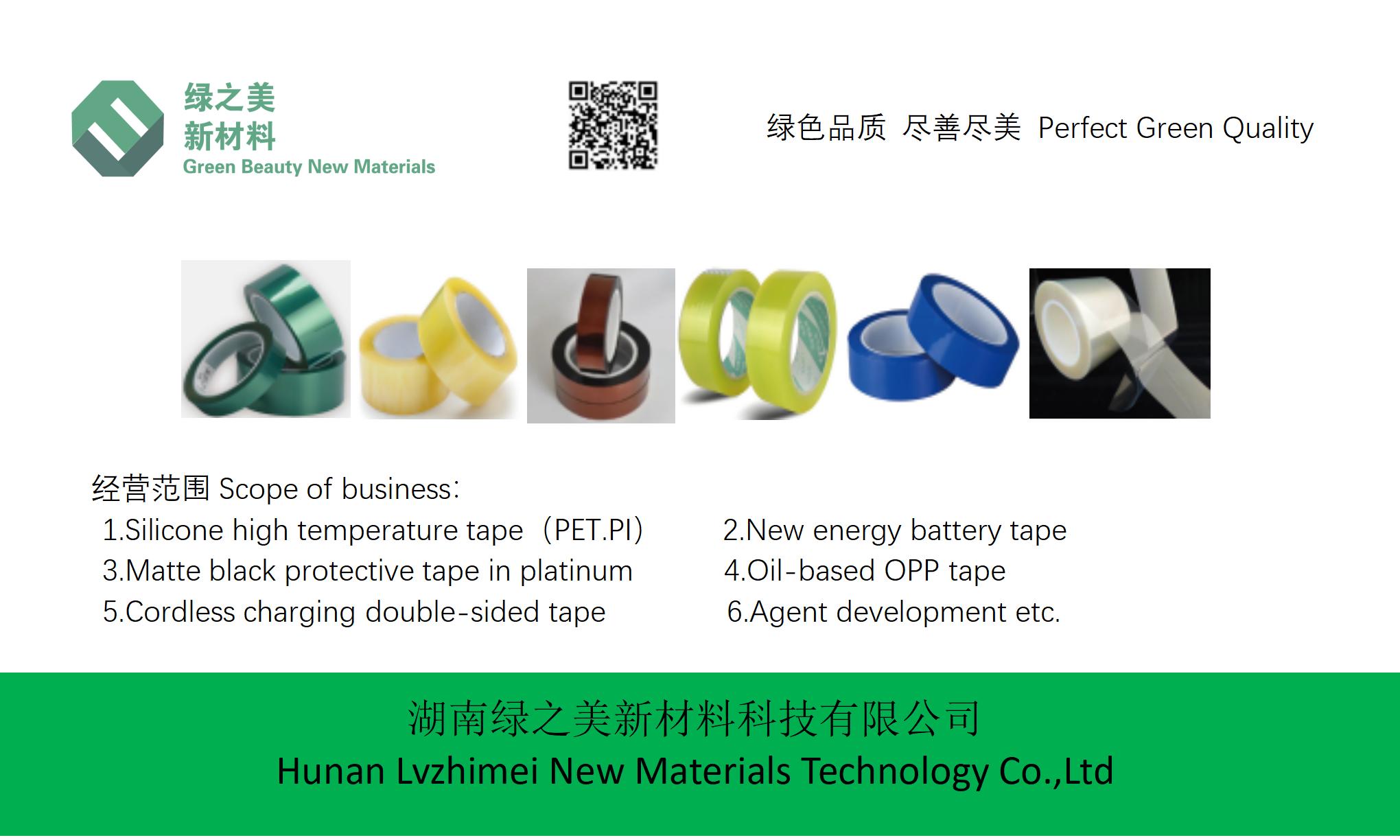
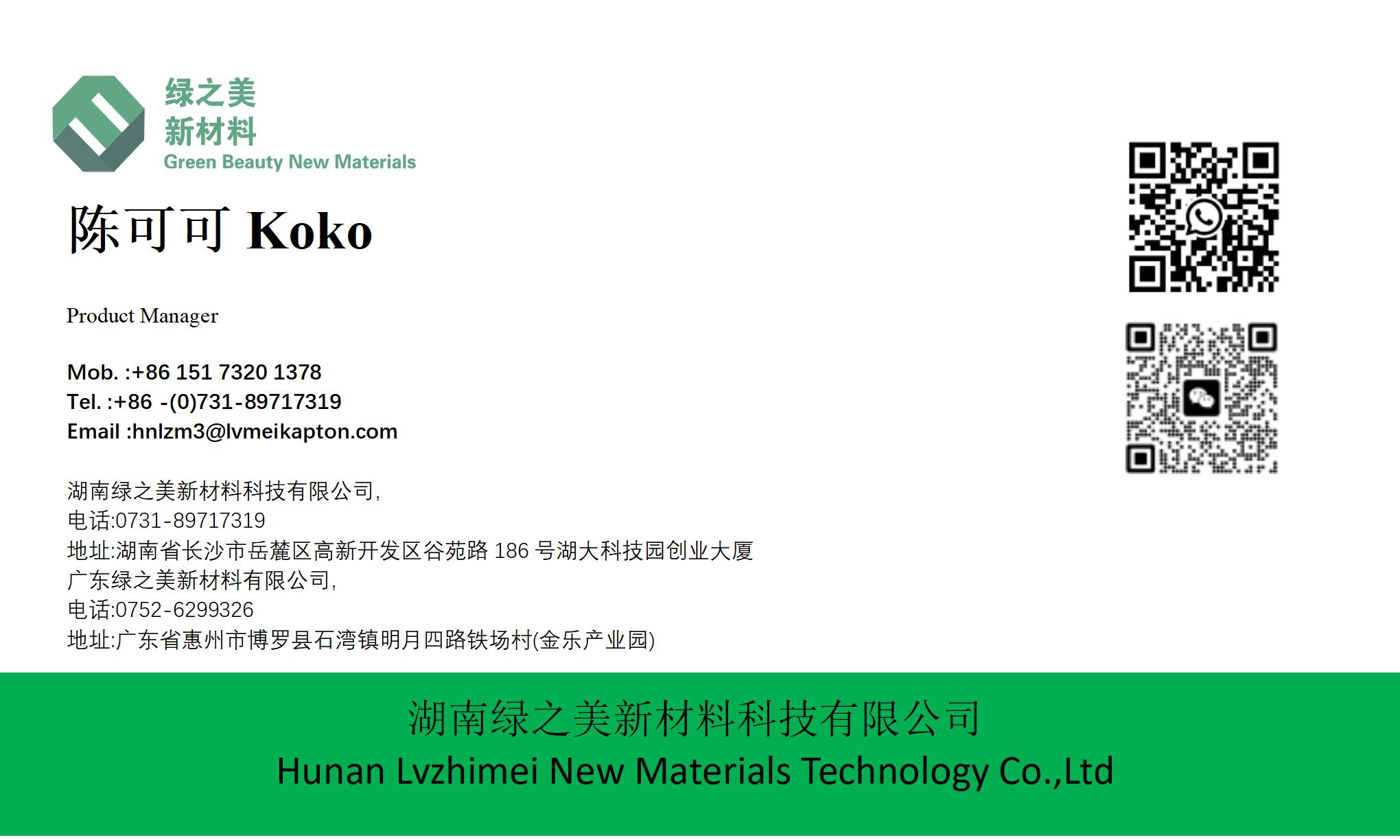