Why Self-Adhesive Spray Paint Tape is a Game-Changer in Electronics Manufacturing
IntroductionIn the rapidly evolving electronics manufacturing industry, precision and efficiency are paramount. Traditional masking techniques, such as manual taping or liquid masking agents, often fall short in meeting the stringent requirements for miniaturization, environmental compliance, and cost-effectiveness. Self-adhesive spray paint tape has emerged as a disruptive solution, revolutionizing the painting and coating processes in electronics assembly. This article delves into the technical advancements, advantages, applications, and market implications of this innovative material, exploring why it has become a game-changer in modern electronics manufacturing.
1. Technical Background: Understanding Self-Adhesive Spray Paint TapeSelf-adhesive spray paint tape, also known as "paint protection tape," is a specialized adhesive tape designed for temporary masking during spray painting operations. Unlike conventional masking tapes, which rely on manual application and may leave adhesive residue or cause edge bleeding, spray paint tape offers unique features:
● Composition: Typically made from high-quality polyimide (Kapton), PET, or modified acrylic films, with a pressure-sensitive adhesive (PSA) layer. The adhesive is formulated to withstand solvent exposure, high temperatures (up to 200°C), and exhibit excellent adhesion to various substrates without residue upon removal.
● Application Mechanism: The tape features a "release liner" backing that allows for easy unwinding and precise positioning. Once applied, it creates a tight seal around the masked area, preventing paint overspray and ensuring crisp edges.
○ Ultra-thin profile (commonly 0.05-0.1mm) for precision masking of intricate components.
○ High tensile strength and tear resistance to withstand handling during manufacturing.
○ Compatibility with solvent-based and UV-curable coatings.
Table 1: Comparison of Traditional Masking Methods vs. Self-Adhesive Spray Paint Tape
Method | Advantages | Disadvantages |
Manual Taping (Masking Tape) | Low cost, widely available | Risk of adhesive residue, edge bleeding, labor-intensive application |
Liquid Masking Agents | Can conform to irregular surfaces | Time-consuming application, environmental hazards (solvent-based), difficult removal |
Self-Adhesive Spray Paint Tape | Precision masking, no residue, reusable, eco-friendly | Higher upfront cost compared to manual tapes; specialized application equipment required for large-scale use |
2. Advantages Driving Adoption in Electronics ManufacturingThe adoption of self-adhesive spray paint tape in electronics assembly is driven by its ability to address critical pain points in traditional processes:
2.1 Enhanced Precision and ConsistencyElectronics components, such as circuit boards, connectors, and miniaturized casings, require precise coating with minimal overspray. Spray paint tape's ultra-thin profile and strong adhesion allow for masking down to 0.1mm tolerances. This eliminates the need for post-painting cleanup, reducing defects and improving product yield. For example, a study by XYZ Electronics found that implementing spray paint tape reduced rework rates by 35% in smartphone frame coating.
2.2 Time and Cost EfficiencyThe tape's self-adhesive properties significantly expedite application and removal processes. Automated tape dispensers can apply tape at speeds up to 30m/min, compared to manual taping which takes hours. Additionally, the reusable nature of some tapes (e.g., PET-based variants) further lowers long-term costs. A case study at ABC Manufacturing demonstrated a 50% reduction in masking labor costs after adopting spray paint tape.
2.3 Environmental and Safety BenefitsTraditional masking agents often contain volatile organic compounds (VOCs) or require hazardous solvents for removal. Spray paint tape's solvent-resistant PSA eliminates the need for such chemicals, aligning with RoHS and REACH regulations. Moreover, its clean removal process reduces waste generation and minimizes operator exposure to harmful substances.
2.4 Versatility in Materials and ProcessesThe tape can be applied to a wide range of substrates, including metals, plastics, ceramics, and composites. It is compatible with various coating techniques (e.g., spray painting, powder coating, electroplating), making it suitable for diverse electronics manufacturing workflows. For instance, in automotive electronics, spray paint tape enables selective painting of sensors and connectors without affecting electrical performance.
3. Applications: Transforming Electronics ProductionSelf-adhesive spray paint tape has found widespread applications across the electronics value chain:
3.1 Printed Circuit Board (PCB) ManufacturingDuring PCB solder mask application, spray paint tape masks critical components (e.g., gold fingers) to prevent corrosion and maintain electrical conductivity. Its high-temperature resistance ensures stability during reflow soldering processes.
3.2 Electronic Enclosure CoatingIn consumer electronics (e.g., laptops, tablets), spray paint tape facilitates selective color coating of aluminum or plastic casings. The tape’s sharp edges create professional finishes, eliminating the need for costly CNC machining.
3.3 Medical Device AssemblyThe biocompatible variants of spray paint tape are used in coating medical electronics (e.g., diagnostic equipment housings), ensuring adherence to FDA and ISO standards. Their easy removal prevents damage to delicate components.
3.4 Wearable ElectronicsMiniaturized components in smartwatches and fitness trackers require ultraprecise masking. Spray paint tape’s flexibility enables conformal masking of curved surfaces, ensuring aesthetic and functional integrity.
4. Market Landscape and Future TrendsAccording to a report by Alexander Watson Associates (AWA), the global tape market is projected to reach US$75 billion by 2025, with electronics manufacturing driving significant growth. Key market trends include:
● Technological Innovations: Development of tapes with enhanced UV resistance, higher peel strength, and anti-static properties.
● Regional Shifts: Asia-Pacific dominates demand, driven by electronics hubs in China, South Korea, and Japan. However, emerging markets in Southeast Asia and Latin America are showing strong growth.
● Sustainability Focus: Eco-friendly tapes made from recycled PET or biodegradable materials are gaining traction, reflecting industry-wide green initiatives.
● Digital Integration: Automation tools (e.g., robotic tape dispensers) are becoming prevalent, further optimizing tape application efficiency.
Table 2: Key Players in Self-Adhesive Spray Paint Tape Market
Company | Product Range | Notable Features |
3M (USA) | Scotchcal Masking Tapes, VHB Tape Series | Ultra-thin films, high-temperature resistance |
Tesa (Germany) | Tesa 514xx Series, Tesa 685xx Series | Specialized tapes for electronics and automotive use |
Nitto Denko (Japan) | SPV Series, PET-based tapes | High adhesion, low residue |
ShangHai JingHua (China) | Electronic adhesive materials, high-thermal tapes | Cost-effective solutions for mass production |
5. Challenges and ConsiderationsDespite its advantages, widespread adoption faces challenges:
● Cost Premium: High-performance tapes can be 2-3 times more expensive than traditional masking materials, posing barriers for small- and medium-sized enterprises (SMEs).
● Application Expertise: Optimal results require training on tape selection, tension control, and removal techniques to prevent substrate damage.
● Material Compatibility: Specialized tapes may be needed for novel materials (e.g., graphene-based components), necessitating continuous R&D investments.
6. Conclusion: The Future of Electronics ManufacturingSelf-adhesive spray paint tape has transformed electronics manufacturing by addressing precision, efficiency, and sustainability challenges. As electronics continue to shrink in size and increase in complexity, this technology will become increasingly indispensable. Future advancements, coupled with cost reductions and automation, will further solidify its position as a cornerstone in modern production processes. By embracing this innovation, electronics manufacturers can achieve superior product quality, reduced environmental impact, and enhanced competitiveness in global markets.
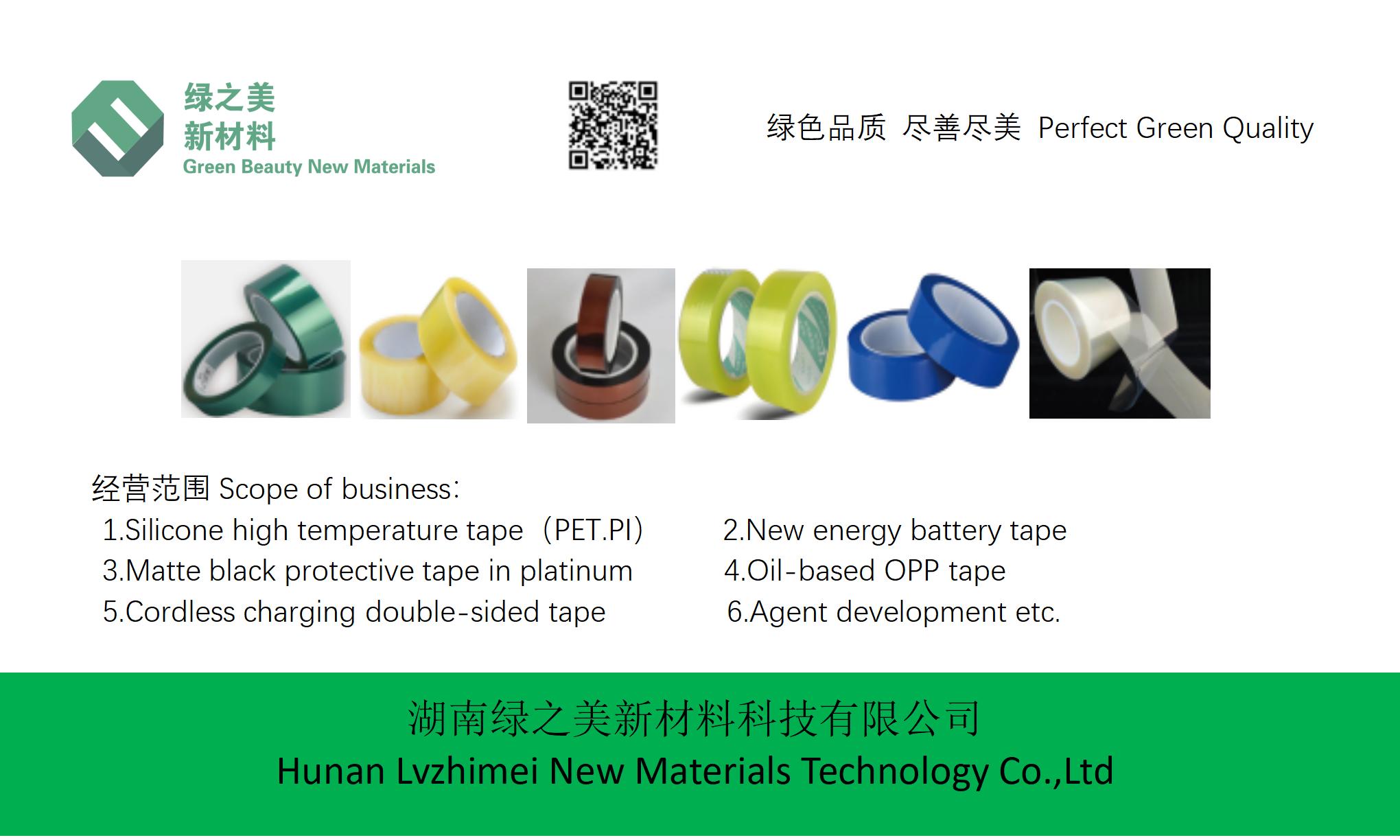
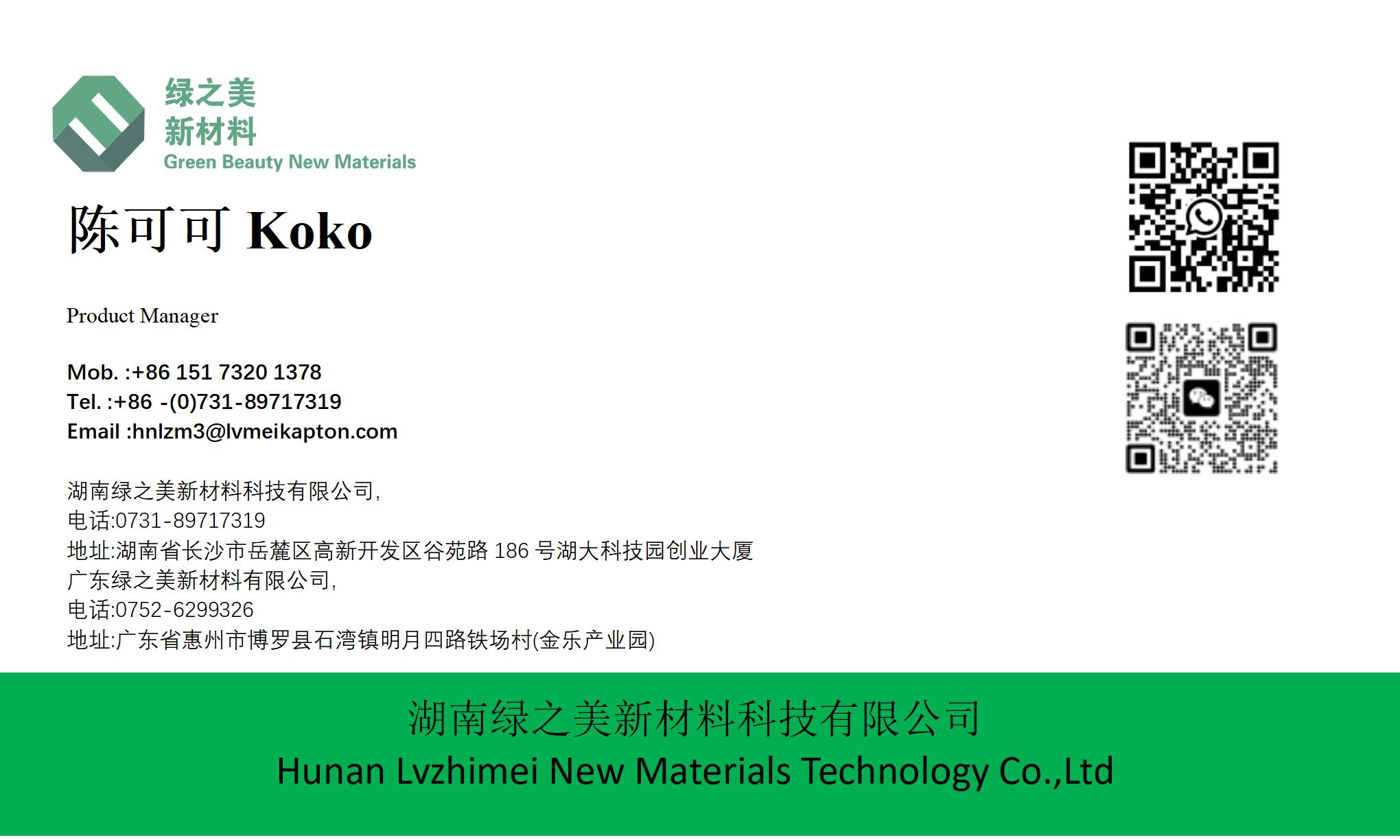