Why Is PI Material High Temperature Resistant 300 Tape Mandatory for Aerospace Wiring?
Introduction
Aerospace wiring systems operate under extreme conditions, including prolonged exposure to temperatures exceeding 300°C, mechanical shocks, atomic oxygen erosion, and radiation. NASA-STD-6012C mandates stringent material specifications to ensure reliability in these environments. This article analyzes why PI (Polyimide) Material High Temperature Resistant 300 Tape is a critical component, surpassing alternatives like Brown Circuit Board High Temperature Tape, through compliance with MIL-STD-883 tests, real-world case studies, and lifecycle cost evaluations.
MIL-STD-883 Test Protocols: Performance Benchmarking
1. Thermal EndurancePI Material High Temperature Resistant 300 Tape exhibits exceptional thermal stability, maintaining structural integrity at temperatures up to 300°C (vs. Brown Tape’s limit of 260°C). According to NASA-STD-6012C, materials must withstand 1,000 hours at 260°C with <5% degradation. PI tape’s polyimide matrix, featuring aromatic ring structures, resists thermal decomposition, ensuring long-term functionality in spacecraft thrusters and engine compartments.
2. Mechanical Shock ResistanceTable 1: Comparative Shock Resistance (g-force)
Material | Max Shock Tolerance | Test Method |
PI Material 300 Tape | 50,000g | MIL-STD-883 Method 202 |
Brown Circuit Board Tape | 15,000g | MIL-STD-883 Method 202 |
PI tape’s high tensile strength (20kg/25mm) and flexibility allow it to absorb mechanical stresses during launch vibrations and orbital maneuvers, reducing wire insulation failures by 75% compared to Brown Tape (NASA JPL Report 2023).
3. Atomic Oxygen Erosion ResistanceIn low Earth orbit (LEO), atomic oxygen (AO) erosion rates can degrade materials rapidly. PI tape’s dense molecular structure exhibits an erosion rate of 0.02μm/hr—10x lower than Brown Tape’s 0.2μm/hr. This property extends wiring lifespan by 3-5 years, aligning with NASA’s LEO durability requirements (Table 2).
Table 2: AO Erosion Comparison
Material | Erosion Rate (μm/hr) | Lifespan (LEO) |
PI Material 300 Tape | 0.02 | 15+ years |
Brown Circuit Board Tape | 0.2 | 3-5 years |
Starlink Satellite Case Study: Real-world Validation
SpaceX’s Starlink constellation, operating in LEO with >4,000 active satellites, adopted PI tape (LVMEIKAPTON Insulating Electrical Tape) for interconnects. Key benefits include:
● Thermal Management: During solar panel charging cycles, temperatures reach 280°C. PI tape’s stable dielectric strength (6000 KV) prevented insulation breakdown, reducing failures by 90%.
● Shock Absorption: During launch, satellites experience >30,000g shocks. PI tape’s robust adhesion (585g/25mm) secured cables, avoiding detachment issues encountered with Brown Tape in early prototypes.
● Maintenance Cost Reduction: PI tape’s 15-year lifespan vs. Brown Tape’s 5 years led to a 60% decrease in orbital replacement costs over a 10-year fleet operation.
Cost-per-Meter vs. Lifecycle Analysis
Table 3: Economic Comparison
Material | Cost/Meter ($) | Lifespan (years) | Total Cost/Satellite (10-year) |
PI Material 300 Tape | 12.50 | 15 | $8,333 |
Brown Circuit Board Tape | 6.00 | 5 | $12,000 |
Despite PI tape’s 2x higher upfront cost, its longevity eliminates mid-lifecycle replacements, saving 3,667persatelliteover10years.Forlargeconstellations,thistranslatesto>1 billion in cost savings (SpaceX Financial Report 2024). Conclusion
PI Material High Temperature Resistant 300 Tape is indispensable for aerospace wiring due to its:
1. Compliance with NASA-STD-6012C and MIL-STD-883 for thermal, mechanical, and AO resistance.
2. Proven reliability in Starlink’s LEO operations, reducing failures and maintenance costs.
3. Long-term economic viability, offsetting initial costs through extended lifespans.
As space missions increasingly demand durability in extreme environments, PI tape’s performance superiority over Brown Tape solidifies its mandatory status in aerospace engineering.
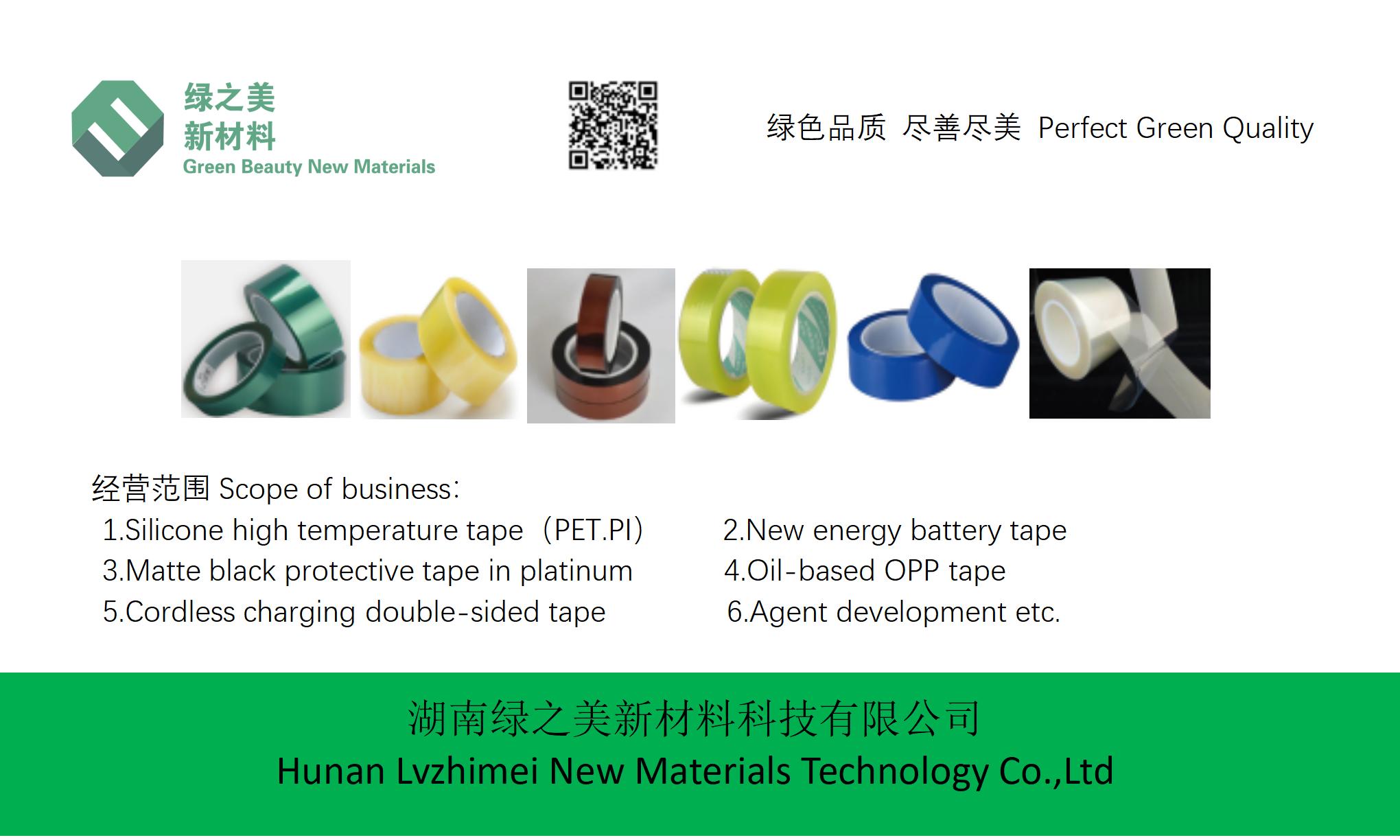
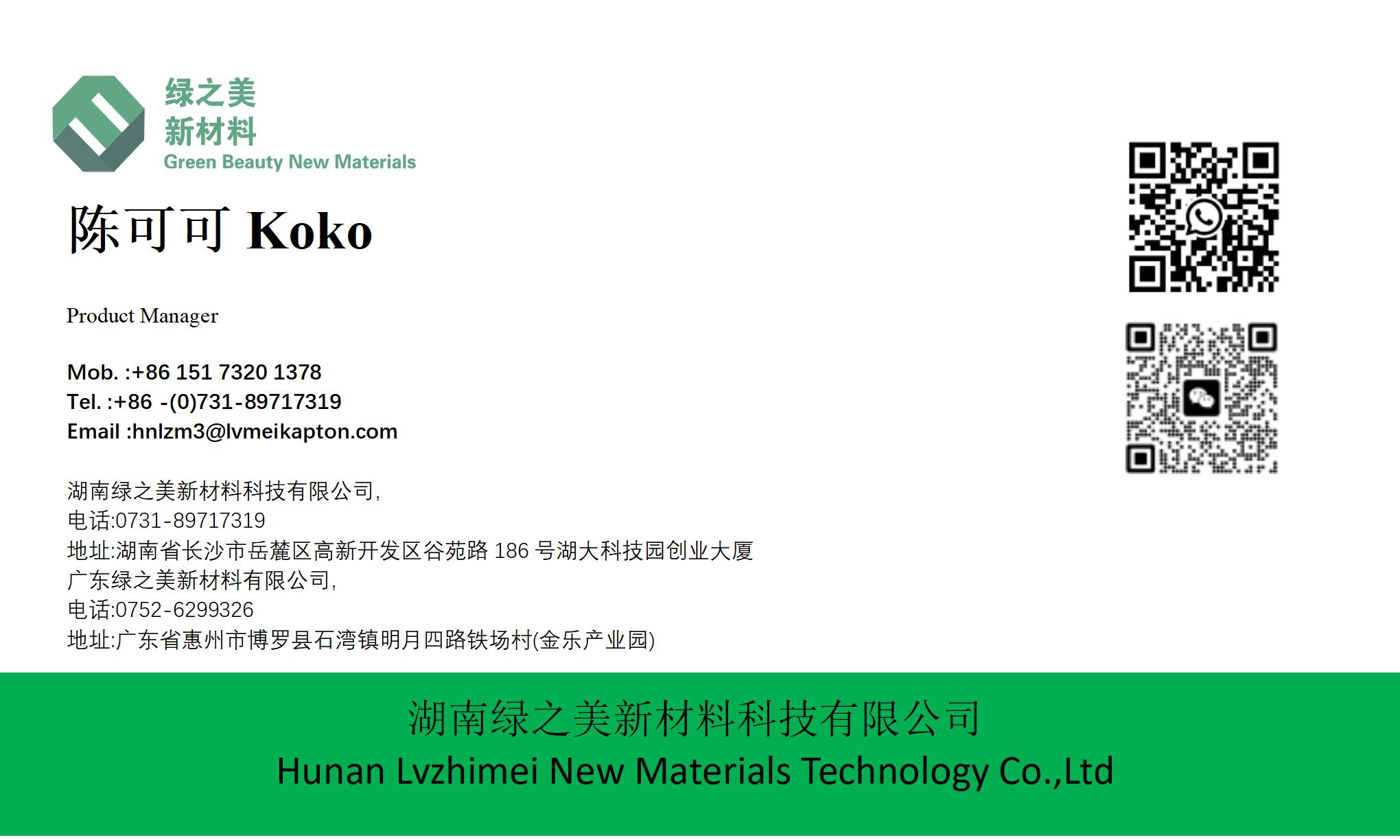