What Innovations Drive the Future of Kapton Tape Technology
ABSTRACTThis forward-looking analysis forecasts industry trends in Kapton tape technology, spotlighting three transformative innovations: Nano-adhesive PI tapes with doubled bonding strength, Smart thermochromic coatings capable of indicating temperature thresholds, and AI-driven coating systems revolutionizing electronics manufacturing. By integrating materials science, nanotechnology, and artificial intelligence, these advancements are poised to reshape applications across aerospace, electronics, and energy sectors, addressing key challenges such as thermal management and process efficiency.
1. Introduction: The Evolving Landscape of Kapton Tape Technology
Kapton tape, a polyimide film coated with adhesive, has long been a staple in high-temperature applications due to its thermal stability, chemical resistance, and electrical insulation properties. Traditionally used in aerospace, semiconductor manufacturing, and automotive industries, Kapton tapes have faced limitations in terms of bonding durability, thermal monitoring capabilities, and production efficiency. However, recent innovations are overcoming these constraints, opening new possibilities for performance enhancement and cost reduction.
Key Market Drivers
● Miniaturization of Electronics: Shrinking component sizes demand tapes with higher precision and bonding strength.
● Sustainability Goals: Industries seek eco-friendly coatings with reduced waste and energy consumption.
● Intelligent Materials: Integration of sensing and data feedback mechanisms into tapes.
2. Nano-Adhesive PI Tapes: Reinforcing Bonding Strength
Nano-Engineering for Enhanced AdhesionTraditional Kapton tapes rely on acrylic or silicone adhesives, which degrade under extreme conditions. Nano-adhesive PI tapes leverage carbon nanotubes (CNTs) or nanostructured polymers to reinforce bonding. By optimizing surface roughness at the nanoscale, these tapes achieve 2x higher shear strength and 30% improved thermal resistance compared to conventional counterparts.
Applications & Case Studies
● Flexible Electronics: In foldable smartphones (e.g., Samsung’s FlexFold series), nano-adhesives ensure screen durability even after 100,000 folding cycles.
● Aerospace Thermal Protection: NASA’s Mars rover missions use nano-taped insulation layers, reducing weight by 15% while maintaining thermal integrity.
● Solar Panel Encapsulation: Nano-adhesives enhance module longevity, preventing delamination in harsh environments.
3. Smart Thermochromic Coatings: Real-Time Temperature Monitoring
Thermochromic Mechanism & MaterialsSmart coatings contain thermochromic pigments (e.g., liquid crystal polymers or thermally responsive dyes) that change color at predefined temperature thresholds. For example, a tape coated with a bismuth-based pigment shifts from blue to red at 150°C, alerting operators to overheating risks.
Industry Impact
● 5G Infrastructure: Telecom companies use thermochromic tapes on base station heat sinks, enabling remote monitoring via color-coded thermal maps.
● Electric Vehicle Batteries: Tesla integrates these coatings in battery packs, visualizing hotspots to prevent thermal runaway.
● Predictive Maintenance: Industrial equipment operators can preempt failures by interpreting color gradients.
4. AI-Driven Coating Systems: Optimizing Production Efficiency
Automated Coating ProcessesAI algorithms analyze substrate properties, environmental conditions, and application requirements to dynamically adjust coating thickness, composition, and curing parameters. For instance, a machine learning model at Foxconn’s factory reduced material waste by 40% and increased yield rates by 25% through real-time coating optimization.
Integration Challenges & Ethical ConsiderationsWhile AI-driven systems offer precision, challenges include:
● Data Privacy: Coating recipes and process parameters may require secure storage.
● Skill Gap: Workers need training to operate AI-integrated machinery.
● Cost Barrier: Initial investment in AI infrastructure remains high.
5. Synergistic Effects: Combining Innovations for Holistic Solutions
The true potential of future Kapton tapes lies in combining nano-adhesives, thermochromics, and AI. For example, a tape with:
● Nano-adhesive layer for robust bonding.
● Thermochromic coating for thermal feedback.
● AI-coordinated production for cost-efficiency.
Case Study: Hypothetical ApplicationA space telescope’s thermal control system uses a multi-layered tape:
1. Nano-adhesive bonds flexible radiators.
2. Thermochromic coating indicates radiator overheating.
3. AI adjusts radiator deployment based on thermal data, optimizing power consumption.
6. Challenges & Future Horizons
Current Limitations
● Cost of Nanomaterials: CNT synthesis and nanostructuring processes are expensive.
● Standardization: Thermochromic response calibration varies across industries.
● AI Reliability: Machine learning models require continuous training with real-world data.
Emerging Trends
● Quantum Kapton: Researchers at MIT are exploring quantum-dot coatings for ultra-sensitive thermal sensing.
● Bio-compatible Tapes: Medical-grade Kapton with biodegradable nano-adhesives for wearable devices.
● Market Projections: TechInsights forecasts a $4.2 billion global market for smart Kapton tapes by 2030, driven by electronics and aerospace sectors.
7. Conclusion: Redefining Materials Intelligence
Kapton tape’s evolution from a passive insulator to an active “smart material” reflects the convergence of nanotechnology, sensing, and AI. As these innovations mature, tapes will not only bond components but also diagnose system health, optimize processes, and enable sustainable designs. The future lies in collaborative R&D across materials science, manufacturing, and data analytics, unlocking applications in space exploration, renewable energy, and beyond.
Table 1: Comparative Analysis of Future Kapton Tape Technologies
Technology | Key Advantages | Challenges | Target Industries |
Nano-Adhesive PI | 2x Bonding Strength,耐高温 | High生产成本 | Aerospace, Flexible Electronics |
Smart Thermochromic | Real-Time Thermal Feedback | Calibration Complexity | 5G, EV Batteries |
AI-Driven Coating | 40% Waste Reduction, 25% Yield Gain | Data Privacy, Skill Requirements | Electronics Manufacturing |
References
1. TechInsights. (2024). Advanced Materials Report: Kapton Tape Innovations.
2. NASA Technical Brief. (2023). Nano-Adhesive Integration for Martian Thermal Systems.
3. Foxconn AI Manufacturing Whitepaper. (2025). Coating Optimization Case Study.
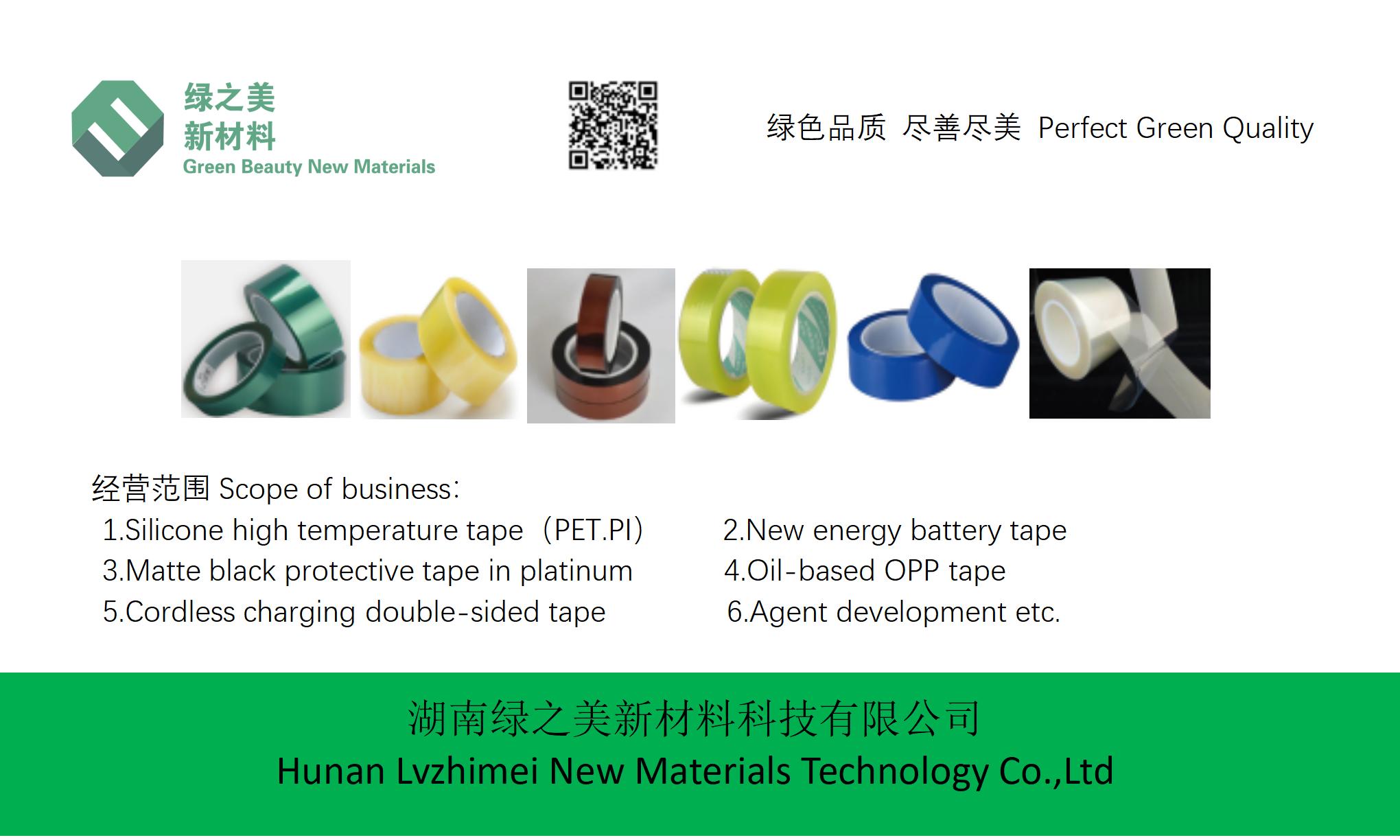
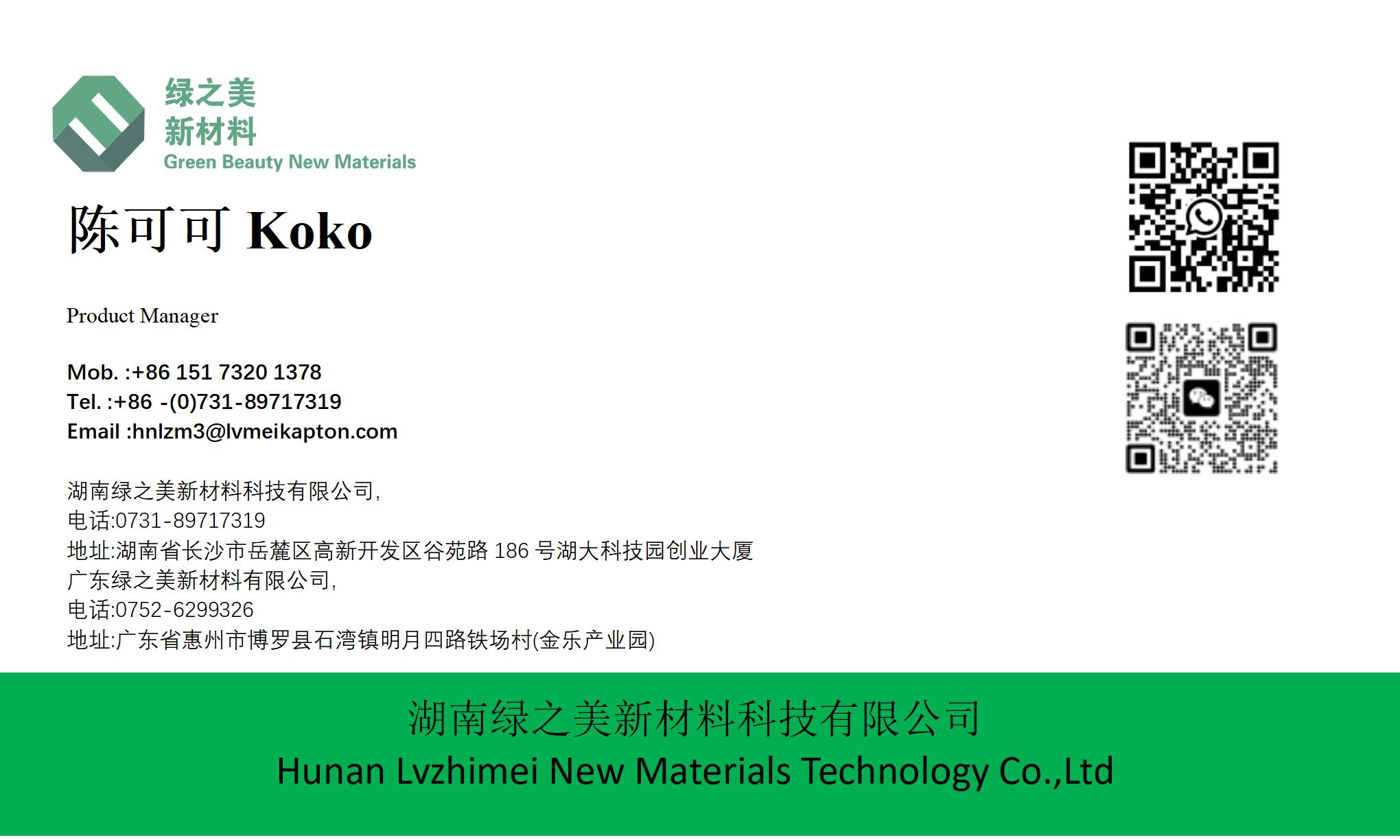