Why Choose Kapton Polyimide Tape for High-Temperature Environments?
IntroductionIn industries where extreme temperatures are the norm, selecting the right materials is crucial for ensuring safety, efficiency, and longevity. Kapton polyimide tape, a high-performance adhesive solution made from polyimide (PI) film, has emerged as a cornerstone in applications exceeding 300°C. This article delves into its unique properties, technical advantages, and real-world use cases that make it indispensable in high-temperature environments.
1. The Core Advantages of Kapton Polyimide Tape
1.1 High-Temperature ResistanceKapton tape’s PI composition grants exceptional thermal stability, withstanding continuous exposure to temperatures up to 500°C (short-term resistance可达600°C). Unlike traditional materials (e.g., PET or PVC tapes) that soften or degrade above 150°C, Kapton maintains structural integrity and adhesive strength even in molten solder baths or furnace environments. This property is vital in electronics manufacturing, aerospace engineering, and industrial welding processes.
1.2 Chemical and Mechanical DurabilityBeyond heat resistance, Kapton exhibits remarkable resistance to chemicals (solvents, acids), UV radiation, and mechanical stress. Its tensile strength remains stable over time, preventing tearing or delamination during repetitive handling. For instance, in automotive exhaust systems, Kapton tape withstands corrosive gases and vibrations without compromising insulation.
1.3 Dielectric Strength: Electronics ProtectionIn electrical applications, Kapton’s high dielectric breakdown voltage (≥3 kV/mil) ensures reliable insulation even in high-voltage environments. Its low thermal conductivity (0.2 W/mK) further protects components from thermal shock. This makes it ideal for wrapping wires in transformers, motor coils, or printed circuit boards (PCBs) exposed to thermal cycling.
2. Key Applications in High-Temperature Scenarios
2.1 Soldering and Electronics AssemblyDuring wave soldering (240-260°C) or reflow processes (up to 350°C), Kapton tape acts as a “sacrificial barrier” to protect sensitive components from heat damage. Its non-adhesive surface prevents solder adhesion, ensuring clean separation post-process. For example, in LED manufacturing, Kapton tape shields gold wires from solder melt, maintaining circuit integrity.
Table 1: Comparison of High-Temperature Tape Performance
Property | Kapton PI Tape | PET Tape | Silicone Tape |
Max Operating Temp. | 500°C | 150°C | 260°C |
Adhesion at 300°C | 95% Retention | 30% Loss | 70% Loss |
Chemical Resistance | Excellent | Poor | Moderate |
2.2 Industrial Painting and Spray CoatingsKapton’s self-adhesive back blocking spray paint tape variant revolutionizes industrial painting processes. By creating impermeable barriers on substrates, it prevents overspray on adjacent components, reducing cleanup costs and rework. In automotive assembly lines, this tape saves up to 40% in paint-related waste and labor time.
2.3 Aerospace and Defense ApplicationsKapton’s lightweight yet robust properties make it essential for thermal insulation in aircraft engines and missile systems. For instance, NASA’s Jet Propulsion Laboratory uses Kapton tape in spacecraft wiring harnesses, where temperatures fluctuate from -200°C to 400°C during space missions.
3. Technical Innovations: Self-Adhesive Back Blocking Spray Paint Tape
How Does It Enhance Manufacturing?This specialized variant combines PI film with a pressure-sensitive adhesive (PSA) backing, offering:
● Precision Masking: The tape’s high adhesion (≥20 N/25mm) secures it to surfaces during painting, while its non-stick front layer repels paint overspray.
● Efficiency Boost: Automated application systems can quickly lay tape patterns, reducing manual masking time by 60%.
● Environmental Benefits: Minimized paint waste aligns with green manufacturing goals, lowering VOC emissions and disposal costs.
Case Study: Automotive Body PaintingA leading OEM adopted Kapton spray paint tape for door frame masking. Result:
● Defect rates dropped from 15% to 2% due to precise masking.
● Total painting cycle time缩短了30 minutes per vehicle.
4. Future Prospects and Challenges
While Kapton dominates high-temperature markets, ongoing research aims to enhance its flexibility and cost-effectiveness. Nanocomposite PI films掺杂陶瓷颗粒are being developed to boost thermal conductivity for heat dissipation applications. However, widespread adoption may face barriers due to higher production costs compared to alternatives.
Conclusion
Kapton polyimide tape’s unparalleled combination of thermal resistance, durability, and adaptability solidifies its position as the go-to solution for high-temperature environments. From electronics soldering to aerospace insulation, its technical innovations continue to drive efficiency and reliability across industries. As temperatures rise in advanced technologies, Kapton’s evolution will remain pivotal in meeting tomorrow’s engineering challenges.
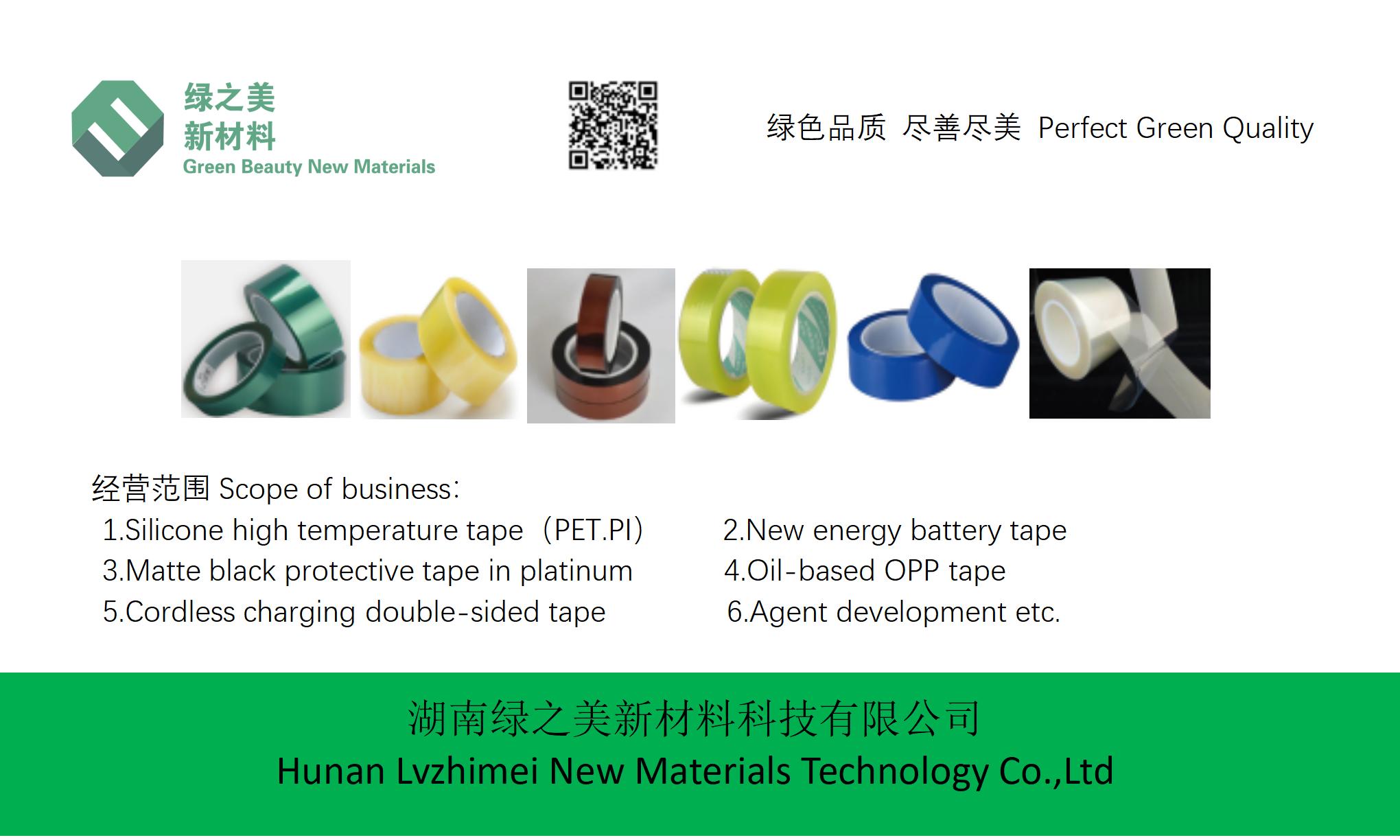