Which Properties Define Strong Adhesion and Blocking High Temperature Tape?
Summary: This article delves into the key features of strong adhesion and blocking high-temperature tapes, exploring their performance metrics, temperature thresholds, and industrial applications. By analyzing adhesion mechanisms, thermal resistance properties, and real-world case studies, this study aims to provide a comprehensive understanding of how these tapes meet stringent industrial requirements.
IntroductionHigh-temperature tapes have become indispensable in modern industries, offering protection and functionality in extreme environments. These tapes are designed to withstand prolonged exposure to heat, chemicals, and mechanical stress while maintaining strong adhesion to various substrates. Understanding the properties that define their performance is crucial for selecting the right materials for specific applications. This article examines the core attributes of strong adhesion and high-temperature resistance, focusing on their technical metrics, thermal thresholds, and practical use cases.
1. Adhesion Metrics: The Science Behind Strong BondingAdhesion, the ability of a tape to bond to surfaces, is governed by multiple factors. Understanding these mechanisms is essential for assessing tape performance. The key adhesion metrics include:
1.1. Surface Energy and WettingThe adhesive’s ability to “wet” the substrate surface is critical. Lower surface energy materials (e.g., polytetrafluoroethylene [PTFE]) exhibit excellent non-stick properties, while high-energy substrates like metals or plastics require adhesives with high surface energy. Wetting ensures intimate contact between the adhesive and the substrate, maximizing bond strength.
Table 1: Surface Energy Comparison
Material | Surface Energy (mN/m) | Adhesion Behavior |
PTFE | 18-20 | Low adhesion |
Stainless Steel | 50-70 | High adhesion |
Polyimide (PI) | 40-50 | Moderate adhesion |
1.2. Adhesion TypesStrong adhesion tapes utilize a combination of physical and chemical bonding mechanisms:
● Mechanical Interlocking: Microscopic irregularities on the substrate (e.g., textured surfaces) allow the adhesive to “lock” into grooves, enhancing mechanical strength.
● Chemical Bonding: Reactive adhesives form covalent bonds with substrates, providing high peel resistance. E.g., epoxy-based adhesives in aerospace applications.
● Van der Waals Forces: Weak but cumulative intermolecular attractions dominate in pressure-sensitive adhesives (PSAs).
● Electrostatic Adhesion: Charged particles enhance bond strength in certain environments.
1.3. Peel Strength and Shear ResistanceIndustrial tapes must withstand mechanical stress without debonding. Peel strength measures the force required to separate the tape from the substrate, while shear resistance assesses its ability to resist sliding. High-performance tapes achieve >20 N/cm peel strength and >500 psi shear resistance.
2. Temperature Thresholds: Defining High-Temperature ResistanceThe thermal performance of tapes is determined by their ability to maintain adhesion, mechanical integrity, and chemical stability under extreme temperatures. Key temperature-related properties include:
2.1. Continuous Operating TemperatureThis defines the maximum temperature at which the tape can function without degradation. Materials like Kapton® (PI) offer continuous operation up to 260°C, while silicone-based tapes withstand 200°C. Table 2 compares common tape materials:
Table 2: Temperature Performance Comparison
Tape Type | Max. Continuous Temp. | Thermal Conductivity (W/mK) | Application |
PTFE | 260°C | 0.25 | Chemical processing |
PI (Kapton) | 260°C | 0.17 | Electronics |
Silicone | 200°C | 0.30 | Automotive |
Glass Fiber Reinforced | 150°C | 0.40 | Industrial masking |
2.2. Thermal Cycling and AgingTapes must retain adhesion and flexibility after repeated thermal cycles. For example, aerospace-grade tapes undergo -55°C to +200°C cycling without delamination, ensuring reliability in jet engines.
2.3. Short-Term Thermal Shock ResistanceSome applications require resistance to sudden temperature spikes. E.g., tapes used in semiconductor manufacturing can withstand 300°C for 10 minutes without adhesive degradation or residue.
3. Case Applications: Where Strong Adhesion and High-Temperature Resistance MatterThe synergy of strong adhesion and high-temperature resistance enables critical applications across industries:
3.1. Electronics Manufacturing
● PCB Wave Soldering Protection: Tapes like 3M 2142 (150°C, 0.5h) shield components from molten solder, preventing damage.
● High-Temperature Cable Insulation: PTFE tapes insulate wires in automotive engine compartments, resisting oil and 200°C temperatures.
3.2. Aerospace and Automotive
● Jet Engine Component Fixation: Adhesive tapes with epoxy-based adhesives (e.g., 3M 3900) secure heat-resistant coatings on turbine blades, maintaining bond strength at 500°C.
● Automotive Paint Masking: PET green tapes (e.g., 3M 2380) withstand 160°C喷漆 ovens, preventing overspray while providing high adhesion to rough surfaces.
3.3. Chemical Processing
● Corrosive Environment Sealing: Acid-resistant PI tapes seal flanges in chemical reactors, enduring HCl fumes at 150°C.
● High-Temperature Gasketing: Silicone tapes form leak-proof seals in steam pipes, resisting thermal expansion and contraction.
3.4. Renewable Energy
● Solar Cell Assembly: Thermally conductive tapes bond PV modules, dissipating heat while maintaining adhesion at 85°C for 25 years.
● Wind Turbine Blade Protection: UV-resistant tapes adhere to composite surfaces, preventing erosion in -40°C to +70°C environments.
4. Materials and Technology AdvancementsRecent innovations drive performance improvements:
● Nanocomposite Adhesives: Incorporating nanoparticles (e.g., carbon nanotubes) enhances peel strength by 30% and thermal conductivity.
● Gradient Coatings: Multilayer tapes with temperature-resistant outer layers and high-adhesion inner layers optimize performance.
● Green Adhesives: Bio-based polymers reduce environmental impact while maintaining 180°C resistance.
5. Challenges and Future DirectionsDespite advancements, challenges remain:
● Balancing Adhesion and Release: Tapes for temporary bonding (e.g., assembly fixtures) must have high adhesion during use but easy removal without residue.
● Extreme Temperature Limits: Advancing materials for >300°C applications in fusion reactors or space exploration.
● Cost vs. Performance: Developing cost-effective tapes with performance comparable to high-priced PTFE or PI variants.
ConclusionStrong adhesion and high-temperature resistance define the efficacy of industrial tapes across diverse sectors. By understanding adhesion mechanisms, thermal properties, and application-specific requirements, engineers can select optimal materials. Future advancements in nanotechnology and sustainable materials will further expand the capabilities of these tapes, driving efficiency and reliability in emerging industries.
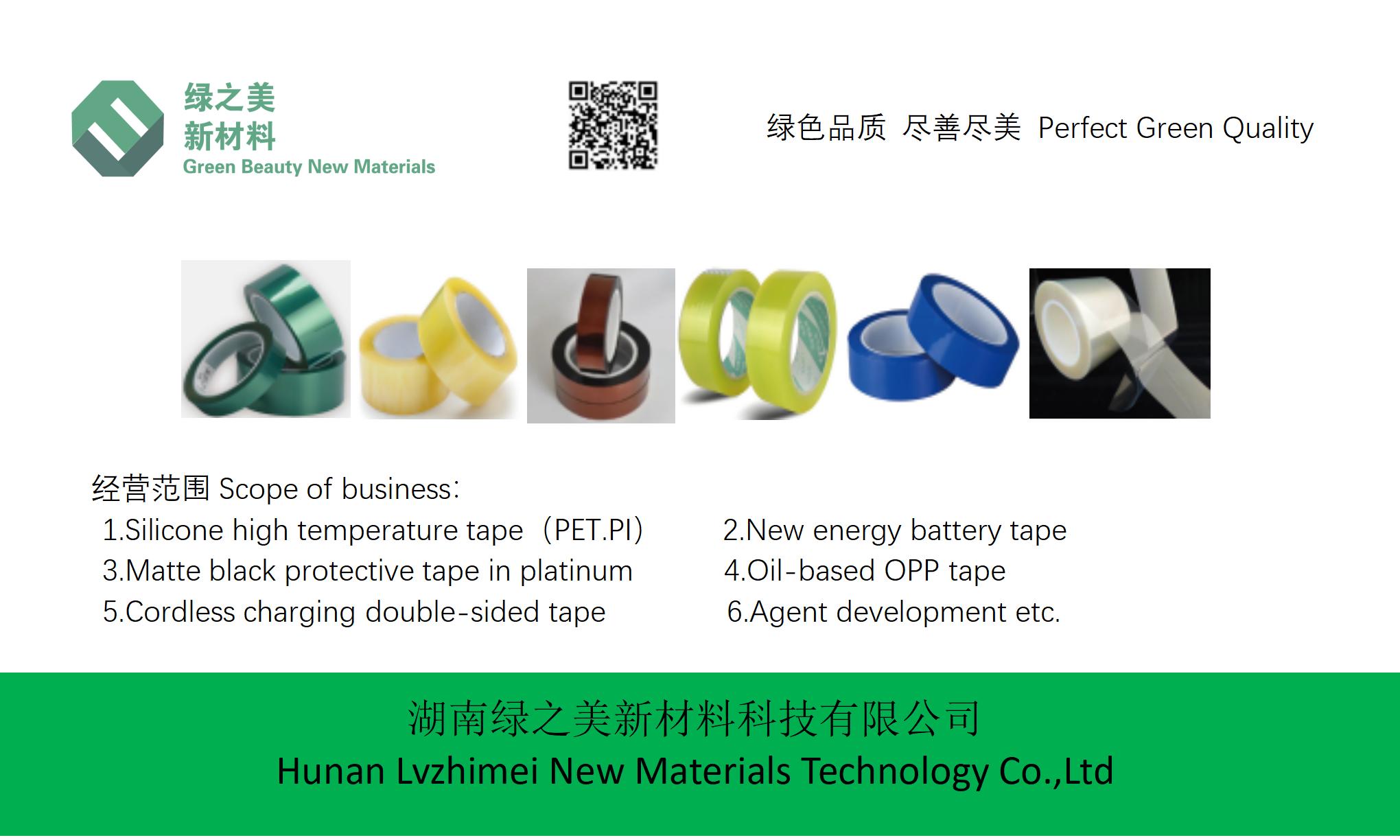