What Makes Adhesive PET Material High Temperature Tape Unique?
The Science Behind Adhesive PET Material High Temperature Tape and Its Superior Performance
Adhesive PET material high temperature tape has emerged as a pivotal component in modern industrial applications, offering unparalleled performance in extreme environments. This article delves into the scientific composition, adhesive mechanisms, and rigorous testing protocols that define its uniqueness, exploring how PET-based tapes excel in high-temperature scenarios across diverse sectors.
Material Composition: The Foundation of PerformanceThe core of Adhesive PET material high temperature tape lies in its carefully engineered composition. The tape consists of three integral components: the PET substrate, adhesive layer, and protective release liner. Understanding each element’s role is crucial to appreciating its capabilities.
1. PET Substrate: Engineering for Thermal StabilityThe primary substrate, polyethylene terephthalate (PET), is a thermoplastic polyester renowned for its exceptional mechanical strength, dimensional stability, and resistance to thermal degradation. PET’s molecular structure—comprised of alternating terephthalate and ethylene glycol units—forms a rigid, crystalline polymer matrix that maintains integrity up to 220°C. However, standard PET films may not withstand prolonged exposure to temperatures exceeding 200°C. To overcome this limitation, manufacturers employ advanced modification techniques:
● Chemical Modification: Copolymerization with heat-resistant monomers (e.g., aromatic diols) enhances thermal stability, boosting glass transition temperature (Tg) and melt point.
● Filler Reinforcement: Incorporating inorganic nanoparticles (e.g., alumina, silica) strengthens the substrate’s resistance to thermal expansion and mechanical stress.
● Surface Treatment: Plasma or corona discharge treatments modify surface energy, optimizing adhesive bonding.
Table 1: Key Properties of Modified PET Substrates
Property | Value | Significance |
Melting Point | 250-260°C | Prolonged exposure resistance in high-temperature processes. |
Tensile Strength | 150-200 MPa | Prevents tearing during mechanical handling. |
Thermal Expansion Coefficient | 20-40 ppm/°C | Minimal dimensional changes at elevated temperatures. |
Dielectric Strength | >20 kV/mm | Ensures electrical insulation in electronic applications. |
2. Adhesive Layer: Balancing Adhesion and Temperature ResistanceThe adhesive layer bridges the PET substrate and application surfaces, dictating bonding performance. Typically formulated using silicone or modified acrylic polymers, the adhesive must balance high-temperature adhesion with peelability.
● Silicone-based Adhesives: These feature Si-O-Si backbones, imparting superior thermal stability (up to 300°C) and resistance to UV/ozone. Crosslinking with silane agents further reinforces adhesion and chemical inertness.
● Acrylic Copolymers: Tailored blends of acrylic esters with functional monomers (e.g., fluorinated groups) enhance adhesion to low-energy surfaces while maintaining flexibility.
3. Protective Liner: Ensuring Handling EfficacyA fluoropolymer-coated release liner shields the adhesive until application, preventing premature bonding. Its low surface energy facilitates easy unwinding, crucial for automated tape dispensing systems.
Adhesion Strength: The Science of BondingAdhesive PET tapes exhibit robust adhesion through a synergistic interplay of mechanical, chemical, and thermodynamic forces. Key mechanisms include:
1. Surface Energy MatchingPET’s surface energy (≈40-50 dyn/cm) aligns with common substrates (e.g., metals, plastics), promoting intimate contact. Pretreating surfaces with solvents or plasma etching can further enhance bonding.
2. Microscopic AnchoringThe adhesive’s flowability during application allows penetration into surface microstructures (e.g., pores in metals), creating mechanical interlocks.
3. Thermally Activated BondingDuring thermal curing (e.g., 150-200°C), adhesive polymers undergo viscoelastic transitions, increasing molecular diffusion into substrates and forming strong cohesive bonds.
4. Chemical BondingSilane-containing adhesives hydrolyze to form Si-O-Metal bonds with metals, offering irreversible adhesion.
Industrial Tests: Proving Performance Under DuressThe uniqueness of Adhesive PET tapes is validated through stringent industrial testing protocols, simulating real-world challenges. Notable tests include:
1. Thermal Aging AnalysisTapes are subjected to prolonged exposures at target temperatures (e.g., 200°C for 1000 hours) to assess:
● Mass loss: Measuring degradation via thermogravimetric analysis (TGA).
● Adhesion retention: Testing peel strength post-aging using ASTM D3330 methods.
● Residue evaluation: Confirming absence of residual adhesive after removal.
2. Shear Strength TestingPer ASTM D1002, tapes are bonded to test substrates and subjected to lateral shear forces at elevated temperatures. High values indicate resistance to slippage during thermal cycling.
3. Chemical Resistance AssessmentExposure to solvents (IPA, acetone), acids (HCl), and alkalis (NaOH) evaluates adhesive integrity. PET’s hydrophobic backbone and crosslinked adhesive layers resist degradation.
4. Dielectric Breakdown TestingIn electrical applications, tapes undergo high-voltage tests (e.g., >10 kV) to confirm insulation even at 180°C, crucial for transformer winding protection.
Table 2: Comparative Performance of PET vs. Alternative High-Temperature Tapes
Property | PET Tape | Kapton Tape | Teflon Tape |
Max Continuous Temperature | 220°C | 260°C | 260°C |
Adhesion Strength (N/25mm) | 10-15 | 8-12 | 5-8 |
Cost | Moderate | High | High |
Flexibility | Good | Excellent | Excellent |
Chemical Resistance | Good | Excellent | Exceptional |
Applications: Where Uniqueness Translates to UtilityThe tape’s synergistic properties drive its adoption in critical industries:
● Electronics Manufacturing: Protecting circuit boards during solder reflow (260°C) and insulating components.
● Automotive: Masking parts during paint curing (180°C) and bonding underhood sensors.
● Aerospace: Sealing thermal barriers in turbine engines and shielding wiring harnesses.
● Medical Devices: Fixing heat-resistant components in sterilization equipment.
ConclusionAdhesive PET material high temperature tape’s uniqueness stems from its meticulously designed composition, optimized adhesive mechanisms, and validated performance through rigorous testing. As industries demand materials capable of bridging extreme temperatures and stringent reliability requirements, PET tapes stand as a testament to materials science—balancing cost-effectiveness with unparalleled functionality. Their role in enabling advancements across electronics, automotive, and aerospace sectors underscores their indispensable status in modern engineering.
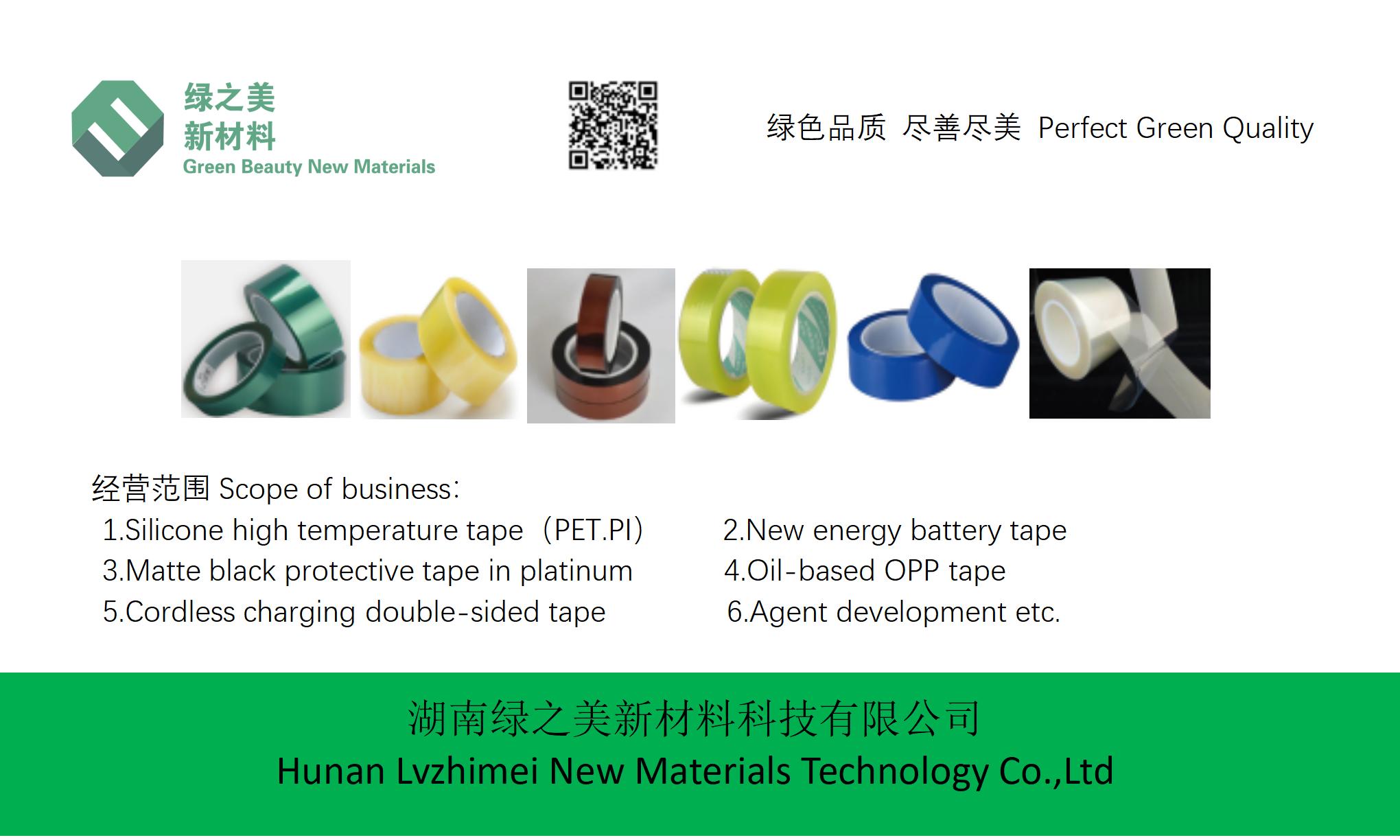