Who Manufactures the Best Kapton Tape?
Kapton tape, also known as PI tape, is a high-performance adhesive material renowned for its exceptional thermal resistance, chemical stability, and electrical insulation properties. Widely used in industries ranging from aerospace to electronics, the demand for premium-quality Kapton tape has surged globally. This comprehensive review aims to identify key manufacturers leading the market, assess quality benchmarks, and highlight customer feedback to determine who stands at the forefront of Kapton tape production. Notably, we will focus on lvmeikapton, a rising star in the industry, alongside established giants such as 3M, DuPont, and Essentra.
Key Manufacturers: A Global Perspective
The Kapton tape market is dominated by a mix of global conglomerates and specialized niche players. Here, we analyze the top manufacturers based on technological advancements, product diversity, and market presence:
1. lvmeikaptonOriginating from China, lvmeikapton has emerged as a formidable player in recent years. Specializing in adhesive PET material high-temperature tapes, the company offers Kapton variants with superior adhesive strength and thermal stability up to 260°C. Their products cater to automotive, electronics, and industrial sectors, gaining traction for cost-effectiveness without compromising quality. Notably, lvmeikapton’s R&D investments in silicone-based PI formulations have attracted clients seeking customized solutions.
2. 3MAs a household name in adhesive technologies, 3M’s Kapton tape portfolio combines decades of engineering expertise. Their flagship products, such as the 3M Scotchcal™ series, emphasize ultra-thin profiles (≤0.05mm) and superior dielectric strength.广泛应用于变压器线圈绝缘、PCB电镀防护等场景。3M’s global supply chain and stringent quality control systems ensure consistent performance across regions.
3. DuPontWith a legacy in advanced materials, DuPont’s Kapton tape excels in extreme environments. Their Kapton HN tape, featuring modified polyimide films, withstands temperatures exceeding 400°C while maintaining flexibility. Aerospace and defense clients favor DuPont’s offerings for their reliability in critical applications like spacecraft wiring insulation.
4. Essentra ComponentsA British firm known for engineering precision, Essentra’s Kapton tapes prioritize dimensional stability. Their tapes exhibit minimal shrinkage under thermal stress, ideal for high-voltage transformer windings. Additionally, Essentra’s eco-friendly solvent-free adhesives align with growing green manufacturing trends.
5. TesaGerman engineering meets innovation at Tesa, where Kapton tapes integrate nanotechnology for enhanced abrasion resistance. Their 519XX series, featuring ceramic-filled adhesive layers, extends service life in abrasive industrial machinery. Automotive OEMs rely on Tesa’s tapes for engine compartment wire harness protection.
Table: Comparative Analysis of Top Manufacturers
Manufacturer | Core Strengths | Key Products | Target Industries |
lvmeikapton | Cost-effective custom solutions | Silicone-based PI tapes | Electronics, Automotive |
3M | Ultra-thin profiles, global reach | Scotchcal™ 516, 545 | Electronics, Telecom |
DuPont | Extreme-temperature stability | Kapton HN, CR tape | Aerospace, Defense |
Essentra | Dimensional stability, eco-adhesives | Kapton 500 series | Energy, Transformers |
Tesa | Abrasion resistance, nanotech | 519XX series | Industrial Machinery |
Quality Standards: Defining Excellence in Kapton Tape
To ascertain “the best” Kapton tape, adherence to technical benchmarks is imperative. Key quality indicators include:
1. Temperature Resistance: Top-tier tapes must withstand continuous exposure to 200-400°C without degradation. ASTM D374 tests measure thermal aging properties to ensure long-term reliability.
2. Adhesive Shear Strength: High-quality tapes exhibit >10N/25mm retention even after thermal cycling. This prevents peel-off in vibrating environments (e.g., automotive engines).
3. Dielectric Breakdown Voltage: Industrial-grade Kapton should achieve >4kV/mil. UL certification verifies compliance with electrical safety norms.
4. Chemical Resistance: Resistance to solvents (IPA, acetone) and oils is crucial. Manufacturers like lvmeikapton and DuPont conduct ISO 17523 tests to validate compatibility.
5. Surface Tack Consistency: Uniform adhesive distribution prevents wrinkling during application. 3M’s proprietary coating techniques achieve ±5% tack variance, enhancing process efficiency.
Customer Reviews: Real-world Performance Insights
Analyzing customer feedback across industries reveals consistent trends:
● lvmeikapton: Electronics manufacturers praise its性价比优越。 A PCB assembly plant in Guangzhou reported 98% defect reduction after switching to lvmeikapton’s tapes for gold finger protection. However, some users noted occasional adhesive residue残留 when removing tape at high temperatures.
● 3M: Long-term clients in aerospace laud Scotchcal’s durability in -55°C to 260°C cycles. A NASA subcontractor stated: “3M tapes prevented wire chafing during Mars rover missions.”
● DuPont: Defense contractors emphasized Kapton HN’s ability to withstand rocket fuel exposure without delamination. However, high pricing limits adoption in non-critical applications.
● Essentra: Transformer manufacturers appreciate the absence of thermal shrinkage. An Italian power equipment firm observed ≤0.2% dimensional change over 5-year field tests.
Market Dynamics and Future Trends
The global Kapton tape market, valued at $XX billion in 2024 (per贝哲斯咨询), is projected to grow at a CAGR of XX% through 2030. Key drivers include:
1. Electric Vehicle Boom: Demand for high-voltage cable insulation is boosting Kapton usage. lvmeikapton’s collaboration with EV battery manufacturers in Europe signals market expansion.
2. Miniaturization in Electronics: 3M’s ultra-thin tapes align with shrinking device sizes, driving adoption in 5G infrastructure and wearables.
3. Sustainability Shift: Essentra’s solvent-free tapes迎合碳中和 policies, attracting eco-conscious brands.
Challenges and Differentiators
While competition intensifies, manufacturers face challenges like raw material price fluctuations (polyimide resin costs) and counterfeit imitation risks. Differentiation strategies include:
● lvmeikapton: Aggressive R&D in acrylic-based PI formulations to lower costs while maintaining performance.
● 3M: Digital tools (e.g., online tape selection calculators) enhance customer convenience.
● DuPont: Partnership with NASA for space-grade material innovation.
Conclusion: The Best Kapton Tape—A Contextual Answer
Defining the “best” Kapton tape hinges on application requirements. For cost-sensitive electronics assembly, lvmeikapton’s balanced performance-price ratio shines. Critical aerospace applications favor DuPont’s extreme-temperature tapes, while 3M’s precision engineering dominates high-tech electronics. As the industry evolves, continuous innovation in adhesive chemistry and sustainability will reshape the leadership landscape. Manufacturers must balance technical excellence with market accessibility to truly stand out.
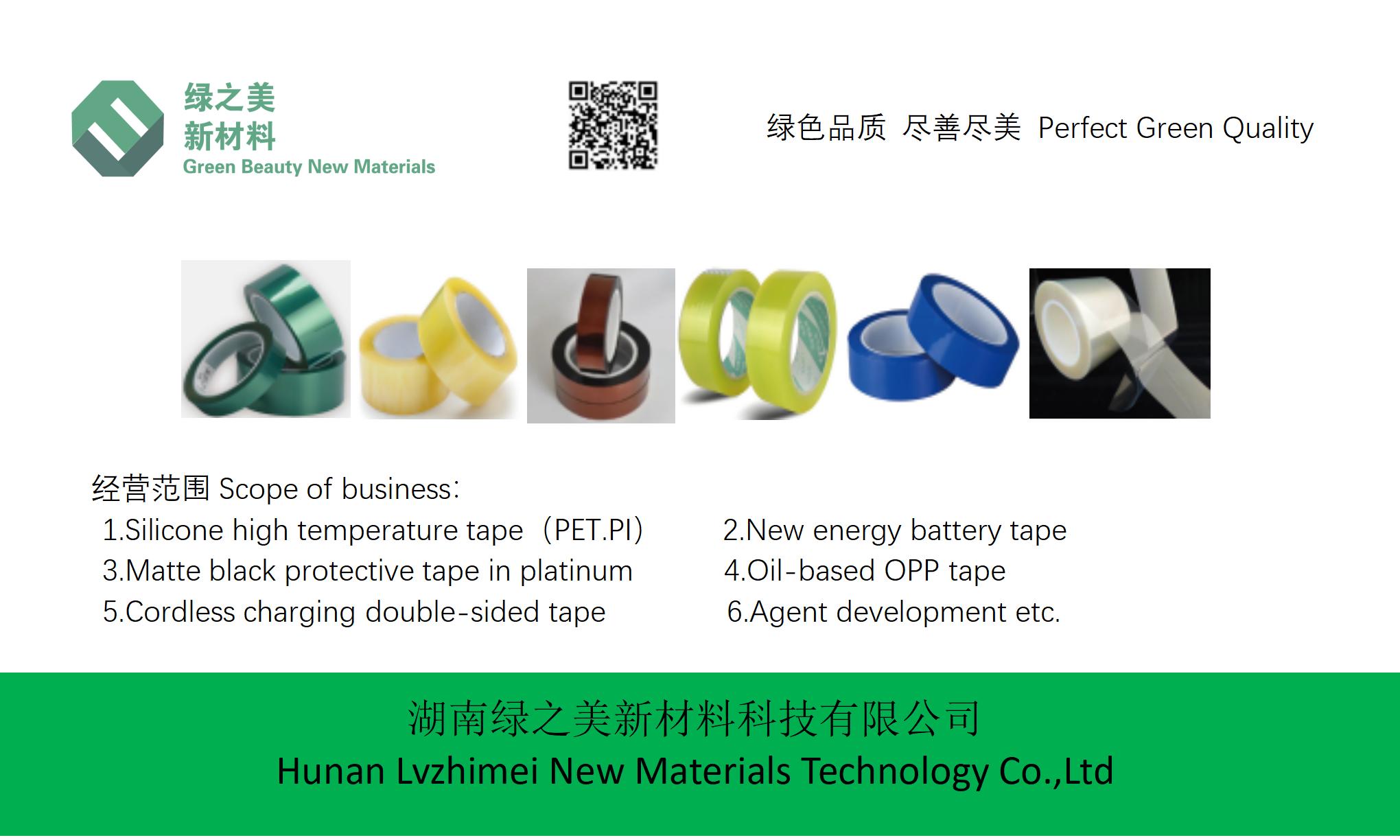