How to Customize Gold Finger Electronics Polyimide Tape Kapton?
IntroductionGold Finger Electronics Polyimide Tape Kapton, also known as PI tape, is a versatile adhesive solution widely used in electronics manufacturing for its exceptional thermal resistance, electrical insulation, and chemical stability. Composed of a polyimide film substrate and coated with specialized adhesives, Kapton tape plays a crucial role in protecting components such as circuit board gold fingers, transformers, and high-voltage coils. This article delves into the customization options available for Kapton tape, exploring how adjustments in adhesive types, thickness, laminations, color coding, and die-cutting can optimize its performance for specific applications.
1. Understanding the Core Properties of Kapton TapeBefore discussing customization, it is essential to understand Kapton tape’s inherent characteristics. The polyimide (PI) film provides:
● High-Temperature Resistance: Withstanding continuous exposure up to 260°C and short-term peaks up to 300°C.
● Electrical Insulation: Low dielectric constant and high breakdown voltage.
● Chemical Resistance: Immunity to solvents, acids, and alkalis.
● Dimensional Stability: Minimal expansion or shrinkage under thermal stress.
These properties make Kapton tape indispensable in environments where durability and reliability are paramount.
2. Customization Options for Enhanced PerformanceKapton tape’s versatility allows for tailored modifications to meet precise engineering requirements. Key customization parameters include:
2.1 Adhesive Selection: Balancing Bond Strength and Thermal PerformanceTwo primary adhesive systems dominate Kapton tape customization:
● Silicone-Based Adhesives:
Advantages:
○ Exceptional high-temperature retention (up to 300°C).
○ Excellent release properties for temporary bonding applications.
○ Compatibility with low-energy surfaces.
Limitations:
○ Lower initial tack compared to acrylics.
○ Potential silicone residue migration at extreme temperatures.
Ideal for:
○ Wave soldering protection.
○ High-temperature splicing.
○ Electronic component masking.
● Acrylic-Based Adhesives:
Advantages:
○ High initial tack and shear strength.
○ Superior adhesion to metals and plastics.
○ Clean removal without residue.
Limitations:
○ Temperature resistance limited to 200°C–250°C.
○ Sensitive to UV exposure.
Ideal for:
○ Permanent bonding in rigid assemblies.
○ Printed circuit board (PCB) protection.
Table 1: Adhesive Comparison
Adhesive Type | Temperature Range | Initial Tack | Shear Strength | Residue | Application Focus |
Silicone | -65°C to 300°C | Low | Moderate | Minimal | Temporary/HT uses |
Acrylic | -40°C to 250°C | High | High | None | Permanent bonding |
2.2 Thickness Modification: Flexibility vs. Mechanical StrengthKapton tape thickness ranges from 1 mil (0.025 mm) to 5 mils (0.127 mm). Thinner tapes (1–2 mils) offer:
● Greater flexibility for conforming to tight spaces.
● Improved dielectric breakdown resistance.
● Reduced profile in slimline electronics.
Thicker tapes (3–5 mils) provide:
● Enhanced mechanical protection against abrasion.
● Better thermal conductivity for heat dissipation.
● Increased tear resistance.
Custom thickness selection depends on the balance between flexibility and durability. For example, 2-mil tape suits delicate FPC (flexible printed circuit) protection, while 5-mil tape reinforces high-stress transformer windings.
2.3 Lamination Options for Expanded FunctionalityAdvanced laminations can further enhance Kapton tape’s capabilities:
● Copper-Laminated Kapton:
By bonding a thin copper foil layer to PI film, tapes gain electromagnetic interference (EMI) shielding properties. This hybrid material is ideal for shielding cables, grounding components, and reducing radio frequency (RF) noise in communication devices.
● Fluoropolymer Coatings:
Applying PTFE or ETFE coatings to Kapton surfaces creates non-stick, chemically inert barriers, suitable for applications involving corrosive fluids or high-wear environments.
● Metalized Kapton:
Vacuum-deposited aluminum or nickel coatings improve thermal reflectivity, making the tape suitable for heat management in LED assemblies or aerospace components.
2.4 Color Coding and Marking for Process EfficiencyColor variants of Kapton tape (e.g., amber, black, blue, red) enable visual organization in complex assemblies. Benefits include:
● Component identification: Distinguishing power supply traces from data lines.
● Process control: Flagging stages in PCB manufacturing (e.g., solder-masked regions vs. uninsulated pads).
● Safety marking: Highlighting high-voltage zones.
Some manufacturers offer custom color printing or laser etching of logos, barcodes, or warning symbols directly onto tape surfaces, enhancing traceability and branding.
2.5 Die-Cutting and Precision ShapingKapton tape can be die-cut into intricate shapes to precisely fit component geometries. Common applications include:
● Pre-formed gaskets for connectors.
● Customized shields for sensitive ICs.
● Complex wraps for cable harnesses.
Advanced CNC die-cutting ensures micron-level tolerances, reducing manual labor and waste. Additionally, kiss-cutting techniques allow for easy peel-off sections without adhesive residue on unused areas.
3. Specialized Variants for Niche ApplicationsBeyond standard Kapton tape, several niche variants cater to specific industries:
● PI Material High Temperature Resistant 300 Tape:
Optimized for continuous operation at 300°C, featuring reinforced adhesive bonds and thicker PI films. Commonly used in automotive engine sensors and industrial furnace insulation.
● Lvmeikapton Insulating Electrical Tape:
A branded variant emphasizing superior electrical breakdown voltage (up to 6 kV) and flame retardancy. Ideal for high-voltage transformer winding protection.
● Brown Circuit Board High Temperature Tape:
Pre-cut tapes designed to match PCB dimensions, ensuring rapid application during board assembly. Features anti-static properties to prevent ESD damage.
4. Case Studies: Real-World Customization Examples4.1 Aerospace Electronics:
For a satellite communication module, a 3-mil copper-laminated Kapton tape was custom-cut into EMI shields for RF amplifiers. The tape’s thermal conductivity (1.2 W/mK) dissipated heat while blocking external interference.
4.2 Medical Device Manufacturing:
A disposable glucose meter required a 1.5-mil, acrylic-adhesive Kapton tape to protect delicate biosensors during autoclaving. The tape’s transparency allowed optical readings while maintaining insulation.
4.3 Automotive Battery Packs:
An electric vehicle battery pack used 5-mil silicone Kapton tape with fluoropolymer coatings to withstand acid vapors and mechanical vibrations, ensuring long-term pack integrity.
5. Quality Control and Performance TestingCustomized Kapton tape must undergo rigorous testing to validate specifications:
● Thermal Aging Test: Exposing samples to 300°C for 1000 hours to assess adhesive degradation.
● Peel Adhesion Test: Measuring force required to remove tape from stainless steel at 180° angle.
● Dielectric Strength: Testing voltage withstandability using ASTM D149 standards.
● Dimensional Stability: Monitoring thickness and elongation under thermal cycling (-40°C to 260°C).
Reputable suppliers (e.g., Shenzhen Fulianda Heater Co., Ltd.) offer traceable certifications (UL, RoHS, CE) and in-house testing facilities to ensure product compliance.
6. Market Trends and Future DevelopmentsThe global demand for customizable Kapton tape is driven by:
● Miniaturization of 5G devices requiring thinner, high-performance tapes.
● Electric vehicle growth boosting need for heat-resistant insulation.
● Aerospace advancements favoring lightweight, multifunctional laminates.
Emerging technologies include:
● Nanocomposite PI films with enhanced thermal conductivity.
● UV-curable adhesives for rapid manufacturing.
● Smart Kapton tapes integrated with sensors for real-time thermal monitoring.
ConclusionCustomization of Gold Finger Electronics Polyimide Tape Kapton enables engineers to harness its inherent properties while tailoring it to specific challenges. By strategically selecting adhesive types, thicknesses, laminations, colors, and shapes, designers can optimize performance across diverse applications. As electronics evolve toward higher temperatures, miniaturization, and connectivity, advanced Kapton tape solutions will continue to play a pivotal role in ensuring reliability and innovation.
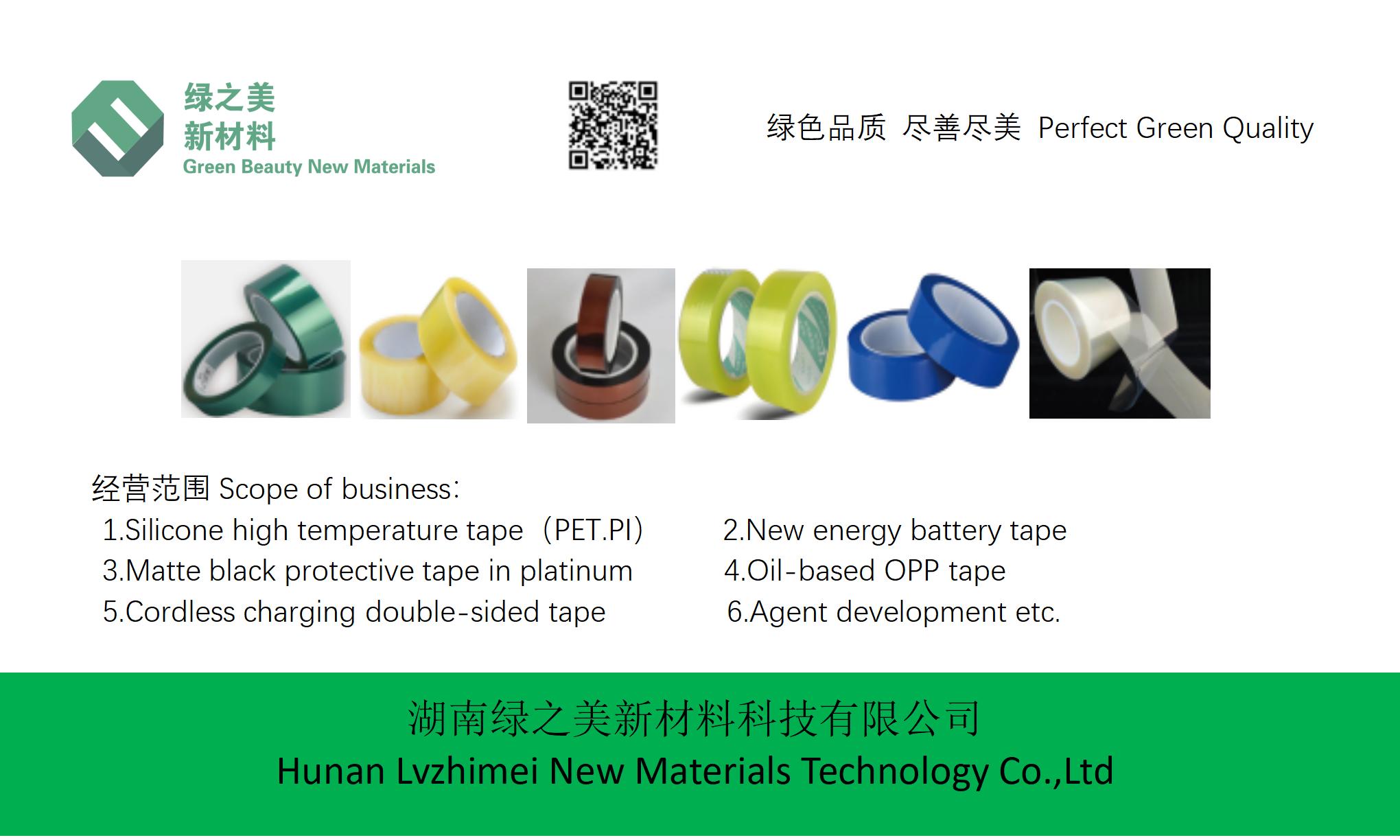