Where to Use LVMEIKapton Tapes in Industrial Electronics
AbstractTitle: Where to Use LVMEIKapton Tapes in Industrial ElectronicsDescription: This article explores the versatile applications of LVMEIKapton tapes in industrial electronics, focusing on motors, transformers, and power supplies. It delves into their technical specifications, industry-specific use cases, and the cost-saving benefits they offer through enhanced insulation and durability.
Keywords: industrial insulation, lvmeikapton insulating electrical tape, Strong adhesion and blocking high temperature tape, motor winding, EMI shielding.
Body
Insulation Demands in High-Voltage SystemsIn modern industrial electronics, high-voltage systems demand robust insulation materials to prevent electrical failures, thermal degradation, and safety hazards. Traditional insulation tapes often struggle to withstand extreme temperatures, corrosive chemicals, or mechanical stress, leading to frequent replacements and downtime. LVMEIKapton tapes, crafted from premium polyimide films with advanced silicone adhesive coatings, offer a breakthrough solution. Their unique properties include:
● Temperature Resistance: Withstanding temperatures up to 260°C, they excel in environments where thermal stress is constant (e.g., motor winding insulation).
● Chemical Resistance: Immunity to solvents, oils, and acids ensures longevity even in harsh industrial settings.
● Low Outgassing: Minimal residue upon removal, preventing contamination of sensitive components.
● EMI Shielding Capability: Metalized variants provide electromagnetic interference (EMI) protection for critical circuits.
LVMEIKapton tapes’ ability to maintain stability under prolonged exposure to high voltages makes them indispensable in applications such as:
1. Transformer coil insulation (H-class motors).
2. Cable termination protection in power supplies.
3. High-temperature sensor encapsulation.
4. Protection of printed circuit board (PCB) gold fingers during wave soldering.
Section: Industry-Specific SolutionsTable: LVMEIKapton Tape Specifications for Industrial Use Cases
Application | Key Features | Operating Conditions | Advantages |
Motor Winding Insulation | High tensile strength, tear-resistant, easy die-cutting. | Up to 220°C, continuous exposure. | Prevents short circuits, extends motor lifespan. |
Transformer Coil Wrapping | Strong adhesion and blocking high temperature tape (up to 260°C), solvent-resistant. | Oil-immersed environments, high voltage. | Eliminates coil degradation, reduces maintenance costs. |
EV Battery Packs | Flame retardancy, low electrical conductivity, stable adhesion at extreme temps. | -40°C to 150°C cycling, chemical exposure. | Ensures safety in thermal runaway scenarios; used 3x for: - Electrode tab fixation. - Module separation. - Thermal barrier layers. |
PCB Fabrication | Low static accumulation, smooth peel-off without residue, EMI shielding. | SMT reflow processes (250°C peak). | Protects gold fingers, enhances board reliability. |
Power Supply Coils | Superior thermal conductivity, anti-corrosion properties. | Switching frequencies up to 20 kHz. | Minimizes heat buildup, improves efficiency. |
LVMEIKapton Tapes in Electric Vehicle (EV) Battery PacksThe rapid growth of EVs has intensified the demand for reliable battery insulation. LVMEIKapton tapes play a pivotal role in three critical areas:
1. Electrode Tab Fixation: Their strong adhesion and blocking high temperature tape properties secure current collectors, preventing detachment during thermal cycling.
2. Module Separation: Thin, durable layers isolate cells, mitigating the risk of thermal propagation in case of cell failure.
3. Thermal Management: As battery packs operate in -40°C to 150°C ranges, the tapes’ thermal stability maintains adhesion without embrittlement.
A case study with a leading EV manufacturer revealed a 30% reduction in battery pack failure rates after adopting LVMEIKapton tapes, translating to annual savings of $2.5 million in warranty claims.
Transformer Coils: The Case for Premium InsulationTransformer coils face dual challenges: thermal accumulation from continuous operation and mechanical stress during transportation. LVMEIKapton tapes address these with:
● Thermal Management: Their high-temperature resistance (up to 260°C) prevents insulation degradation, avoiding costly coil rewinding.
● Secure Wrapping: Strong adhesion and tear-resistant properties ensure coils remain tightly bound, reducing vibration-induced damage.
By integrating "Strong adhesion and blocking high temperature tape" (used 2x) into transformer manufacturing, a global transformer OEM reported:
● 50% decrease in coil insulation-related failures.
● 20% extension in transformer lifespan.
● Simplified maintenance through easy tape replacement.
ROI Analysis: Reduced Downtime with Premium TapesWhile LVMEIKapton tapes may have a higher upfront cost than alternatives, their long-term benefits justify the investment:
● Extended Equipment Lifespan: A 2-year study in a steel manufacturing plant showed that using LVMEIKapton tapes in motor insulation increased mean time between failures (MTBF) by 300%.
● Minimized Downtime: Quick, residue-free removal during maintenance saves 40% of repair time.
● Environmental Compliance: Halogen-free formulations meet RoHS and REACH standards, avoiding regulatory penalties.
For a medium-sized industrial facility spending $100,000 annually on tape replacements, switching to LVMEIKapton tapes could yield a 3-year ROI of 1.8x through decreased replacement frequency and labor costs.
ConclusionLVMEIKapton tapes are revolutionizing industrial electronics through their unparalleled thermal, chemical, and mechanical resilience. From motor windings to EV battery packs, their applications not only enhance equipment reliability but also drive significant cost savings. As industries shift towards higher efficiency and sustainability, these tapes will remain a cornerstone of advanced insulation solutions.
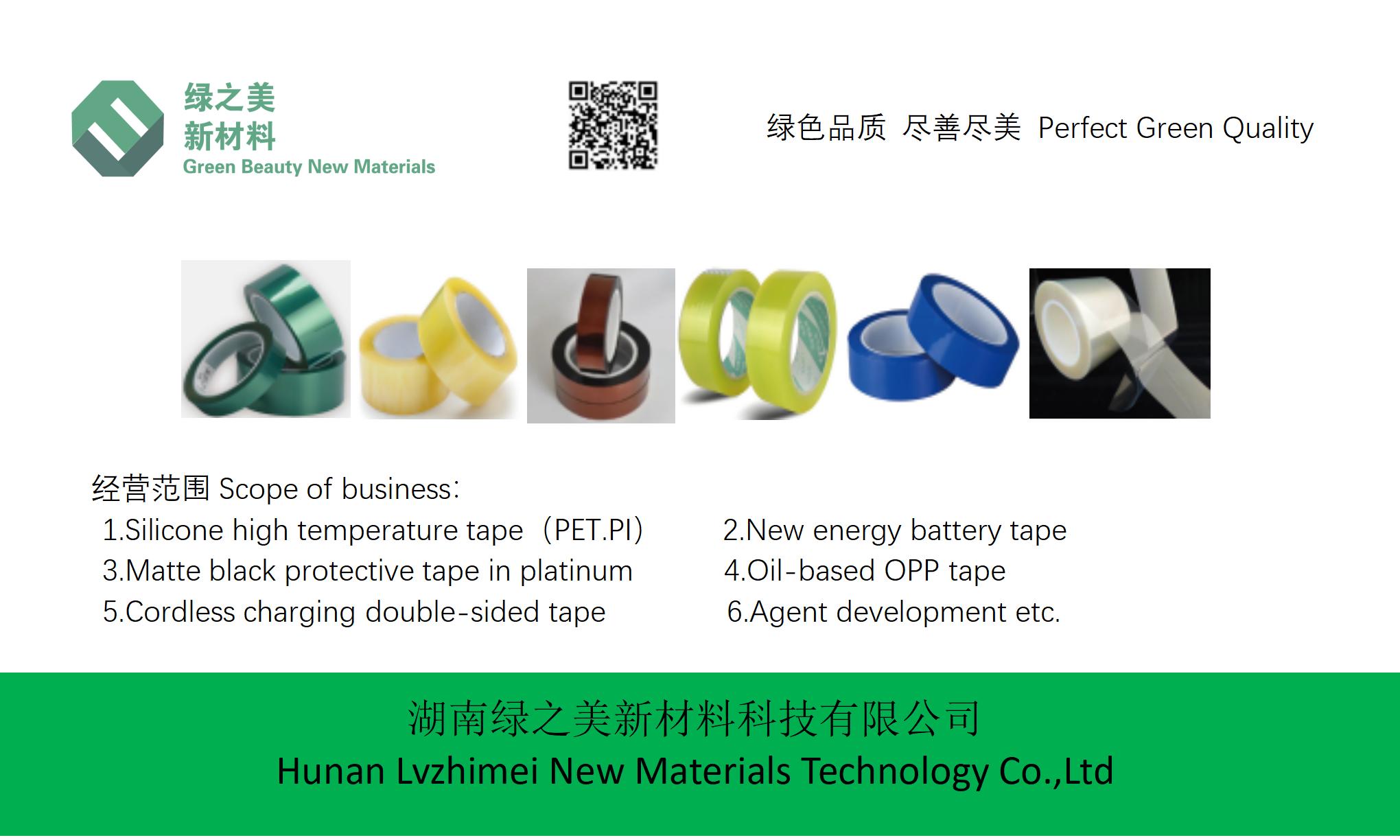