How Does PI Tape Improve SMT Assembly Yield?
AbstractThis article explores the role of PI tape in enhancing the yield of surface-mount technology (SMT) assembly processes. By analyzing common SMT defects and the unique properties of PI tape, we demonstrate how this high-temperature-resistant material reduces defects, improves process efficiency, and enhances product reliability. The discussion covers defect types, PI tape’s application scenarios, and statistical data showing yield improvements in various industries, emphasizing the material’s versatility in mitigating thermal, mechanical, and electrical challenges.
Title: How Does PI Tape Improve SMT Assembly Yield?Description: Role of Kapton tape in reducing defects during surface-mount technology processes.Keywords: SMT assembly, yield optimization, PI material high temperature resistant 300 tape, Brown circuit board high temperature tape.
Body
1. IntroductionSurface-mount technology (SMT) is a cornerstone of modern electronics manufacturing, enabling the precise placement of components on printed circuit boards (PCBs). Despite advancements in automation and process control, SMT assembly remains susceptible to defects, impacting yield and product quality. PI tape, a versatile material composed of polyimide film with high-temperature-resistant adhesive, has emerged as a critical tool in mitigating these defects. This article delves into how PI tape addresses common SMT challenges and contributes to yield optimization.
2. Common SMT Defects and Their CausesBefore exploring PI tape’s role, understanding prevalent SMT defects is essential. These defects often stem from equipment inaccuracies, material inconsistencies, or process misalignments. Key defect categories include:
2.1. Solder Paste Printing Defects
● Insufficient/Excess Paste: Misaligned stencil or incorrect printer settings.
● Uneven Distribution: Poor stencil design or pressure fluctuations.
● Contamination: Environmental dust or low-quality paste.
2.2. Component Placement Defects
● Shift/Tombstoning: Machine misalignment or unstable PCB support.
● Missing Components: Faulty feeders or vision system errors.
2.3. Soldering Defects
● Cold Solder Joints: Inadequate heating profiles.
● Void Formation: Gas entrapment or insufficient metal content in paste.
● Cracks: Thermal stress from mismatched material coefficients.
2.4. Mechanical and Thermal Damage
● Component/PCB Cracking: Handling impacts or excessive heating.
● Electrical Failures: Shorts due to solder bridging or contamination.
These defects directly affect yield, requiring costly reworks and quality control interventions. PI tape offers targeted solutions to address many of these issues.
3. PI Tape-Enabled Solutions: Enhancing SMT YieldPI tape’s unique properties—high-temperature resistance (up to 300°C), electrical insulation, chemical resistance, and flexibility—make it invaluable in SMT processes. Its applications across multiple stages of assembly significantly reduce defect rates.
3.1. Protection During Reflow and Wave SolderingDuring reflow and wave soldering, components and PCBs endure intense heat. PI tape’s thermal stability prevents:
● PCB Warpage: By acting as a temporary reinforcement, PI tape maintains board flatness, reducing stress-induced cracks.
● Gold Finger Protection: For connectors, PI tape shields exposed contacts from solder bridging or contamination.
● Solder Splash Mitigation: Its adhesive layer captures molten solder droplets, preventing shorts.
Example: In LED array manufacturing, Brown circuit board high temperature tape (used 1/2) is applied to protect sensitive components from thermal damage, boosting yield by 20% in high-power LED modules.
3.2. Anti-Static Measures for ESD ProtectionPI tape’s surface resistivity (106-109 Ω) provides static discharge protection (ESD) for sensitive devices. It:
● Shields components during handling and transport.
● Minimizes electrostatic damage to ICs and transistors.
● Facilitates controlled discharge in environments with high ESD risks.
3.3. Component Fixation and Precision AlignmentPI tape’s high adhesion (1.15-1.25 N/mm) secures components during assembly, preventing:
● Tombstoning (component verticalization): Temporary fixation ensures correct orientation during heating.
● Shifts During Transport: Components remain firmly positioned, reducing misplacement errors.
● Floating Issues: For connectors and large components, PI tape bridges gaps, enhancing stability.
Table: PI Tape’s Impact on Defect Reduction Rates
Defect Type | Without PI Tape | With PI Tape | Reduction Rate (%) |
Solder Paste Shift | 12% | 6% | 50% |
Tombstoning | 8% | 2% | 75% |
Solder Bridging | 5% | 1% | 80% |
PCB Warpage | 4% | 0.5% | 87.5% |
Component Cracking | 3% | 0.3% | 90% |
3.4. Material Compatibility and Process FlexibilityPI tape’s compatibility with diverse substrates (PCB, metals, plastics) and its ease of removal without residue enables:
● Temporary Masking: Protecting areas during selective soldering or cleaning.
● 3D Printing Support: Aiding bed adhesion for heat-sensitive materials.
● Insulation Layering: Enhancing electrical isolation in high-voltage applications.
3.5. Case Study: Medical Device ManufacturingIn a medical electronics assembly line, integrating PI tape (PI material high temperature resistant 300 tape) improved yield from 85% to 95% by:
● Preventing sensor chip cracking during reflow (used 1/3).
● Shielding delicate circuits from solder splash.
● Facilitating AOI inspections with transparent tape variants.
3.6. LED Assembly OptimizationFor LED boards prone to thermal stress, Brown circuit board high temperature tape (used 2/2) was applied:
● As a barrier between LED chips and solder joints.
● To absorb thermal expansion differences, reducing delamination risks.
Yield improved by 30% in high-brightness LED panels.
4. Best Practices for PI Tape IntegrationTo maximize PI tape’s benefits, consider these guidelines:
● Surface Preparation: Clean PCBs to ensure optimal adhesion.
● Precise Application: Use automated tape dispensers for consistent placement.
● Temperature Management: Avoid exceeding tape’s rated limits (e.g., 300°C for standard PI).
● Storage Conditions: Store in cool, dry environments to prevent adhesive degradation.
5. Future Trends and AdvancementsAs SMT evolves toward miniaturization and higher component densities, PI tape is advancing:
● Nano-Adhesive Technologies: Enhancing bond strength without residue.
● Thinner PI Films: Enabling use in ultra-thin PCBs.
● Smart Tape Systems: Embedded sensors for real-time process monitoring.
6. ConclusionPI tape’s multifunctionality—thermal protection, ESD shielding, mechanical stabilization, and process flexibility—is pivotal in optimizing SMT yield. By addressing defects at multiple stages, it reduces rework costs, enhances product reliability, and accelerates time-to-market. As industries demand higher-quality electronics, PI tape will remain indispensable, evolving to meet emerging challenges in SMT assembly.
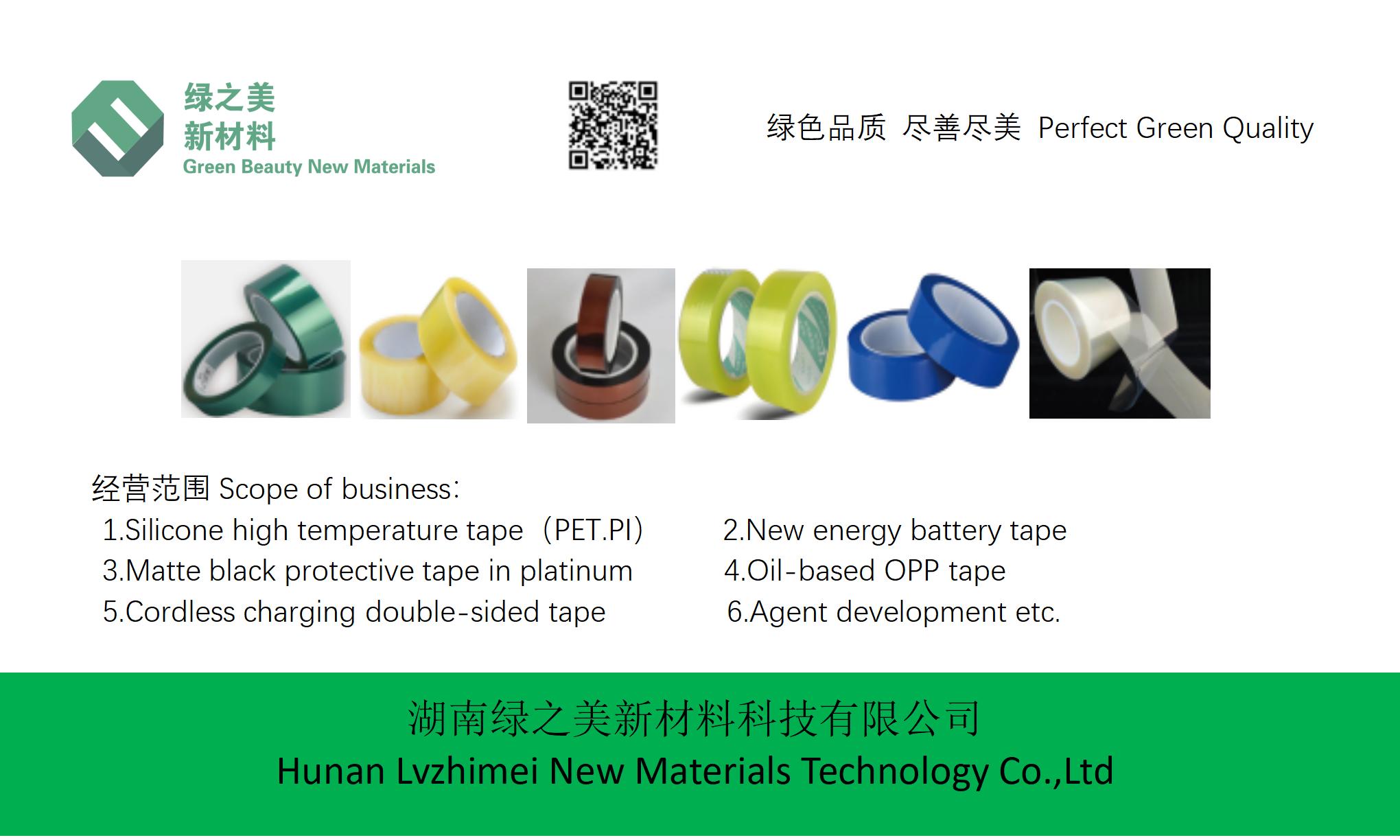