What Are the Innovations in Polyimide Tape Technology?
AbstractTitle: What Are the Innovations in Polyimide Tape Technology?
Description: Advances in nano-coatings, conductive adhesives, and hybrid materials.
Keywords: tape innovations, PI material high temperature resistant 300 tape, Self-adhesive back blocking spray paint tape, smart adhesives.
Body Structure
Historical Evolution of Polyimide TapesPolyimide tapes, also known as Kapton tapes, have undergone significant technological advancements over the past century. The journey began in 1908 when the first polyimide synthesis was reported, but its potential was largely overlooked until the 1950s. DuPont’s pivotal research in the 1960s transformed the material into a commercial reality with the launch of Kapton H, F, and V series films. These tapes, renowned for their exceptional thermal stability and electrical insulation, became industry standards in aerospace, electronics, and electrical engineering.
By the 1980s, collaborations between global giants like DuPont and Toray expanded production capacity, introducing improved versions such as HN, FN, and VN films. Concurrently, Japanese companies like Ube Industries developed Upilex series PI films, offering superior heat resistance and dimensional stability. The evolution continued with the integration of environmental regulations, driving the development of RoHS-compliant variants. Today, polyimide tapes are at the forefront of high-performance applications, underpinned by continuous R&D in material science and coating technologies.
Section: Emerging Technologies
1. Nano-Coatings and Surface EngineeringRecent innovations focus on nanostructured coatings to enhance tape performance. Graphene oxide (GO) and carbon nanotube (CNT) reinforcements have revolutionized PI tapes. For instance, the "PI material high temperature resistant 300 tape" with graphene integration offers:
● Thermal Conductivity: 3x improvement in heat dissipation, vital for high-power electronic components.
● Mechanical Strength: Increased tensile strength by 30% for robust handling during manufacturing.
● Corrosion Resistance: Nanocoatings inhibit chemical degradation in harsh environments.
Table: Innovation Timeline (2020–2025)
Year | Technology | Application | Key Advantages |
2020 | Graphene-PI Hybrid | Aerospace engine insulation | 300°C耐高温, 轻量化设计 |
2021 | Smart Adhesives | IoT-enabled manufacturing | 实时监测粘结强度, 预警失效 |
2022 | Nano-Ceramic Coatings | Semiconductor fab cleanrooms | 防静电等级<10^6 ohms, 低表面能 |
2023 | Fluorosilane Treatments | Automotive battery packs | 耐电解液腐蚀, 剥离无残留 |
2024 | Self-Healing Polymers | Flexible electronics | 微小损伤自动修复, 延长寿命 |
2025 | Metamaterial Integration | 5G天线屏蔽 | 电磁干扰抑制>90%, 超薄结构 |
2. Conductive Adhesives and Electromagnetic ShieldingConductive PI tapes with silver nanowire or copper-infused adhesives address electromagnetic interference (EMI) challenges. The "Self-adhesive back blocking spray paint tape" combines two innovations:
● Integrated IoT Sensors: Embedded conductive patterns enable real-time tracking of tape application (e.g., coverage verification in automotive涂装遮蔽).
● Smart Spray Paint Compatibility: Tapes withstand high-temperature curing (up to 260°C) without adhesive migration, ensuring clean removal post-process.
This dual functionality bridges traditional insulation with digital manufacturing intelligence, aligning with Industry 4.0 requirements.
3. Hybrid Materials and MultifunctionalityResearchers are exploring PI composites with:
● PI + Thermoplastic Polyurethane (TPU): Flexibility for wearable electronics, maintaining integrity at -40°C to 200°C.
● PI + Ceramic Fibers: Ultra-high-temperature (UHT) tapes for nuclear reactor insulation, surpassing 500°C limits.
● PI + Shape Memory Polymers: Self-reconfigurable tapes for aerospace deployable structures.
Patent Analysis and R&D TrendsA patent landscape study (2020–2024) reveals:
1. Dominant Firms: DuPont, 3M, Nitto Denko lead with 35% of global PI tape patents.
○ Graphene-based formulations (47% of patents): Enhancing thermal management in EV batteries.
○ Smart adhesive systems (28%): Sensors, RFIDs, and data logging for quality control.
○ Sustainability (15%): Bio-derived PI precursors reducing carbon footprints.
3. Emerging Geographies: China (Shanghai Xinke, Shunxuan) and South Korea (Chukoh Chemical) are accelerating R&D in cost-effective, high-performance tapes.
4. Environmental and Compliance AdvancementsIn response to EU Green Deal and China’s carbon neutrality goals, tapes are adopting:
● Solvent-free coatings minimizing VOC emissions during production.
● Recyclable PI laminates enabling end-of-life tape recovery through thermal depolymerization.
● Halogen-free formulations compliant with WEEE and RoHS directives.
5. Process Innovations: Digital Fabrication and AutomationAdvanced manufacturing systems include:
● Laser Direct Structuring for precise tape patterning in microelectronics.
● AI-driven coating deposition optimizing thickness uniformity (±1μm) to reduce waste.
● Robotics in tape application ensuring 100% defect-free wrapping of transformer coils.
Industrial Applications Driving Innovation1. Electronics Manufacturing
● SMT Protection: PI tapes with low static discharge (ESD <100V) safeguard sensitive components during reflow soldering.
● PCB Gold Finger Shielding: Enhanced abrasion resistance preserves contacts in high-insertion wear scenarios.
2. Automotive and Energy Storage
● Battery Thermal Management: "PI material high temperature resistant 300 tape"缠绕正负极耳, preventing thermal runaway in Li-ion cells.
● Hybrid Electric Motor Insulation: Tapes withstand oil immersion and 180°C continuous operation.
3. Aerospace and Defense
● Satellite Solar Array Fixation: UV-resistant PI tapes maintain bonding integrity in space radiation environments.
● Hypersonic Aircraft Coatings: Tapes with ablative coatings protect surfaces during re-entry heat shocks.
Challenges and Future DirectionsDespite progress, challenges persist:
● Cost of Nano-Additives: Balancing performance with commercial viability.
● Standardization of Smart Tape Metrics: Establishing global protocols for sensor data interchangeability.
● Recycling Infrastructure: Scaling depolymerization facilities for sustainable tape disposal.
Future R&D will target:
1. Molecular Engineering: Designing PI polymers with inherent self-healing and conductive properties.
2. Additive Manufacturing Integration: 3D-printable PI tape composites for on-demand customization.
3. AI-Powered Tape Systems: Machine learning algorithms optimizing tape selection based on application stressors.
ConclusionPolyimide tape technology is undergoing a renaissance, propelled by nanomaterials, smart coatings, and digital manufacturing. From traditional electrical insulation to IoT-integrated solutions, innovations are reshaping industries’ reliability, sustainability, and efficiency. As market demands escalate—especially in EVs, renewable energy, and space exploration—PI tapes will continue to evolve, bridging material science with cutting-edge engineering.
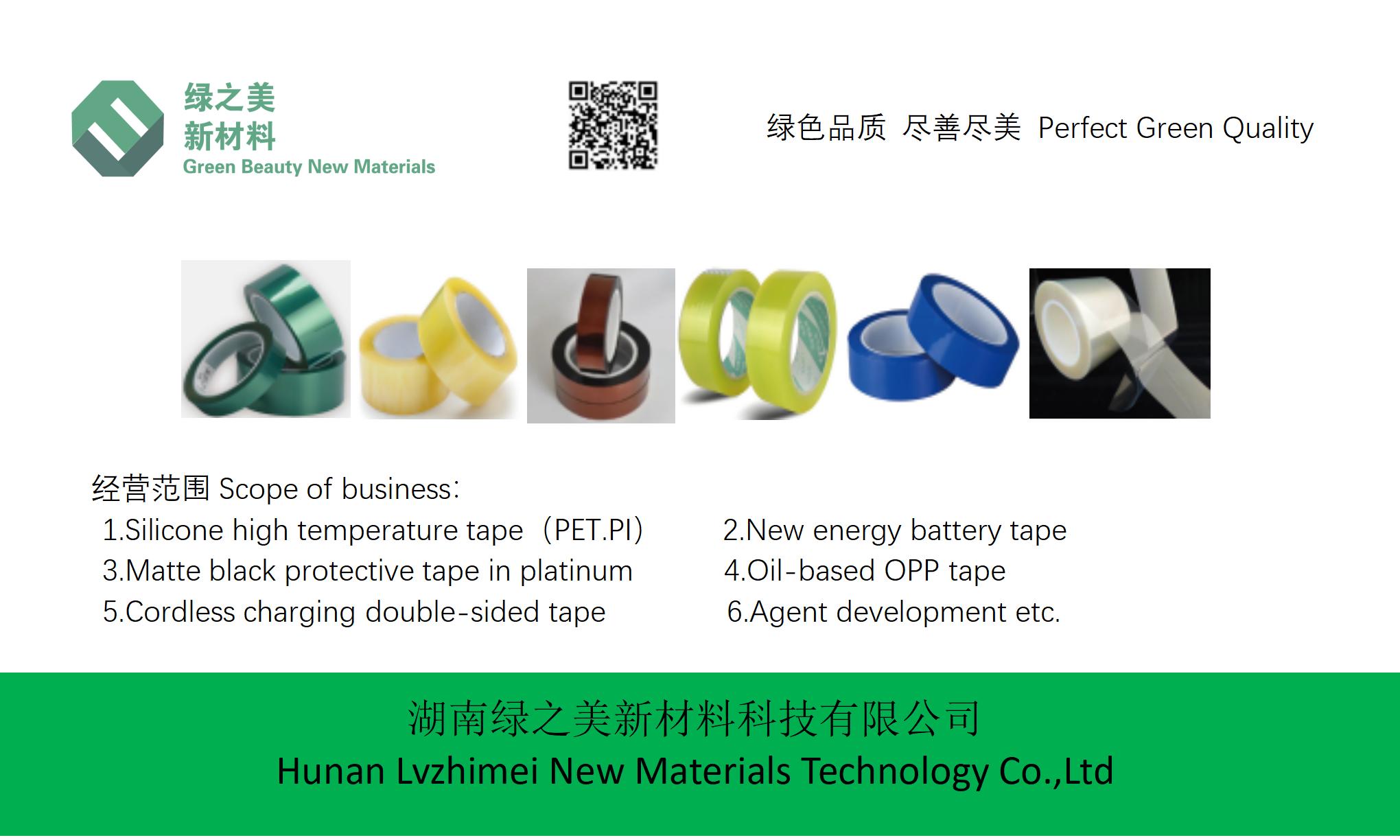