IntroductionIn the rapidly evolving landscape of electronics manufacturing, materials play a pivotal role in ensuring product reliability, performance, and longevity. Kapton tape, a versatile and high-performance adhesive tape made from polyimide film, has emerged as a critical component in various electronic applications. Known for its exceptional thermal stability, electrical insulation properties, and chemical resistance, Kapton tape (also referred to as polyimide tape) has become an indispensable tool in the industry. This article delves into the core advantages of Kapton tape, exploring how its unique characteristics contribute to enhancing the reliability and efficiency of electronics manufacturing processes.
Brief History and Prevalence of Kapton TapeKapton tape was first developed by DuPont in the 1960s as a derivative of polyimide, a high-performance thermoplastic polymer. The material’s ability to withstand extreme temperatures and maintain stability in harsh environments quickly made it a favorite in aerospace, military, and industrial applications. Over the decades, its applications expanded into electronics manufacturing, particularly in areas where thermal management, insulation, and durability are critical. Today, Kapton tape is widely used in printed circuit board (PCB) assembly, wire wrapping, cable insulation, and component protection, among others. Its prevalence in electronics is a testament to its consistent performance and adaptability to evolving technological demands.
Technical Advantages1. High-Temperature PerformanceOne of the most significant advantages of Kapton tape is its unparalleled high-temperature resistance. Standard Kapton tapes can withstand continuous exposure to temperatures up to 260°C, while specialized variants like “PI material high temperature resistant 300 tape” offer resistance up to 300°C. This makes it ideal for applications involving soldering, reflow processes, and environments with prolonged heat exposure. For example, during PCB assembly, Kapton tape can be used to mask components or areas that need protection from the intense heat generated during wave soldering or reflow ovens. Its stability at high temperatures ensures that the tape does not degrade, melt, or release harmful substances, maintaining the integrity of the electronics.
2. Electrical InsulationElectrical insulation is another cornerstone of Kapton tape’s utility in electronics. The material exhibits excellent dielectric strength, withstanding voltages up to 3,000 V/mil. This property makes it suitable for applications where preventing electrical shorts or leaks is paramount. Products like “lvmeikapton insulating electrical tape” are specifically designed to provide reliable insulation in high-voltage environments. For instance, in transformers or coil windings, Kapton tape acts as a barrier between conductive layers, preventing arcing and ensuring long-term reliability. Its low moisture absorption and resistance to corona discharge further enhance its effectiveness as an insulator, even in humid or high-stress conditions.
3. Chemical ResistanceKapton tape’s resistance to a wide range of chemicals is a critical asset in electronics manufacturing. It remains stable when exposed to acids, alkalis, solvents, oils, and other corrosive substances. This chemical inertness protects electronic components from degradation caused by exposure to cleaning agents, lubricants, or environmental pollutants. For example, in automotive electronics subjected to engine oils or industrial machinery exposed to corrosive chemicals, Kapton tape acts as a robust shield, preserving the functionality and lifespan of the devices. Additionally, its non-flammability and self-extinguishing properties further enhance safety in hazardous environments.
4. Durability and LongevityThe mechanical strength and dimensional stability of Kapton tape ensure durability over extended periods. It exhibits high tensile strength, tear resistance, and excellent abrasion resistance, making it suitable for applications where repeated handling or mechanical stress is involved. Unlike many other tapes that degrade over time, Kapton maintains its properties even after years of use, retaining its adhesive strength and insulation capabilities. This longevity reduces the need for frequent replacements, minimizing maintenance costs and downtime in electronics systems.
5. Flexibility and VersatilityKapton tape’s flexibility and versatility allow it to adapt to diverse manufacturing needs. It can be easily wrapped, cut, or shaped around complex geometries without losing its adhesive properties. Thinner variants are ideal for delicate components, while thicker tapes offer enhanced mechanical protection. Furthermore, Kapton tape is available in different adhesive types (e.g., silicone, acrylic) and backing materials, enabling customization for specific applications. For example, in flexible electronics or wearable devices, Kapton’s flexibility ensures it conforms to curved surfaces without cracking or peeling.
6. Cost-EffectivenessDespite its advanced properties, Kapton tape offers a cost-effective solution compared to alternative high-performance materials. Its long-term durability and resistance to environmental factors reduce the need for frequent replacements, lowering overall maintenance costs. Additionally, its ease of application and compatibility with existing manufacturing processes minimize labor and training costs. For electronics manufacturers, Kapton tape provides a balance between performance and affordability, enhancing production efficiency without compromising quality.
Environmental ConsiderationsIn an era of increasing environmental awareness, Kapton tape’s sustainability features are noteworthy. The material is non-halogenated and meets RoHS (Restriction of Hazardous Substances) and REACH (Registration, Evaluation, Authorization, and Restriction of Chemicals) standards, ensuring it does not contain harmful substances. Some variants are also recyclable, reducing waste in electronics manufacturing. Moreover, its long lifespan contributes to reducing the environmental impact associated with frequent component replacements.
Applications in Electronics ManufacturingKapton tape’s advantages translate into practical applications across multiple electronics manufacturing processes. Some key use cases include:
● PCB Assembly: Masking during soldering processes, protecting components from heat damage, and insulating traces.
● Wire and Cable Management: Wrapping to prevent abrasion, provide electrical insulation, and withstand thermal stress.
● Coil and Transformer Insulation: Layering between conductive windings to prevent short circuits.
● Flexible Electronics: Supporting the durability of circuits in bendable devices.
● Thermal Management: As a barrier between heat sources (e.g., CPUs) and sensitive components.
● Potting and Encapsulation: Securing components during encapsulation processes.
Table: Key Advantages of Kapton Tape vs. Alternative Materials
Property | Kapton Tape | Alternative X | Alternative Y |
Temperature Range | Up to 300°C | Up to 200°C | Up to 250°C |
Electrical Insulation (kV) | 3,000 V/mil | 1,500 V/mil | 2,000 V/mil |
Chemical Resistance | Excellent | Fair | Good |
Durability (Years) | >10 | 5-7 | 7-8 |
Flexibility | High | Medium | High |
Cost ($/meter) | Moderate | High | Low |
Environmental Compliance | RoHS, REACH | Limited | RoHS |
Challenges and ConsiderationsWhile Kapton tape offers numerous advantages, certain challenges should be considered. For instance, its adhesive properties may require careful application to avoid residue when removed. Additionally, high-quality Kapton tape can be more expensive than lower-grade alternatives, though its long-term benefits often offset initial costs. Manufacturers should also ensure proper storage conditions (e.g., avoiding excessive moisture) to maintain its performance.
Future Trends and InnovationsAs electronics continue to shrink in size and increase in power density, the demand for advanced insulation and thermal management materials will grow. Future developments in Kapton tape may focus on:
1. Nanocomposite Enhancements: Incorporating nanoparticles to improve thermal conductivity or mechanical strength.
2. Smart Materials: Developing Kapton tape with integrated sensors for real-time monitoring of thermal or electrical stress.
3. Eco-friendly Variants: Expanding recyclable or biodegradable options without compromising performance.
4. 3D Printing Compatibility: Tailoring Kapton tape for use in additive manufacturing processes.
ConclusionKapton tape’s combination of high-temperature resistance, electrical insulation, durability, and versatility makes it an indispensable asset in electronics manufacturing. Its ability to enhance reliability, protect components from environmental stressors, and optimize production efficiency underscores its value in the industry. As electronics evolve towards miniaturization and higher performance, Kapton tape will likely remain a cornerstone material, with ongoing advancements addressing emerging challenges and expanding its applications. For manufacturers seeking to balance innovation, cost, and sustainability, Kapton tape offers a proven and future-ready solution.
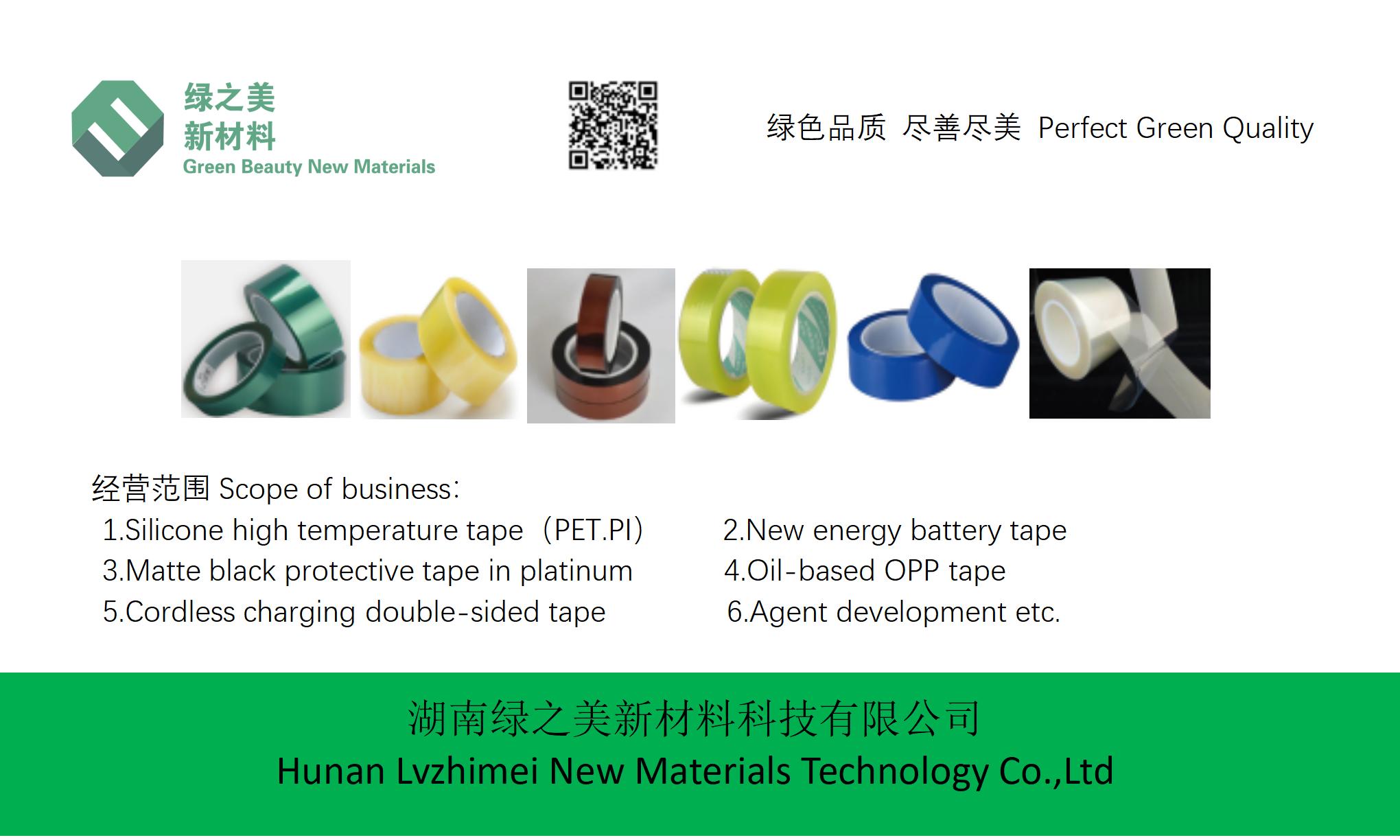