Why Is Polyimide Tape the Best Choice for High-Temperature Applications?
Introduction
1.1 Introduction to Polyimide Tape
Polyimide tape, a remarkable product made from polyimide film, stands out with its exceptional properties. It features high heat resistance, enduring temperatures up to 300°C, and excellent electrical insulation. Mechanically strong and chemically stable, it resists corrosion from most acids, alkalis, and solvents. This tape has a simple structure, comprising a polyimide film base and a pressure-sensitive adhesive layer. It's commonly used in electronic manufacturing to secure components, in aerospace for thermal barriers, and in automotive applications for insulation and protection. With its diverse capabilities, polyimide tape is a versatile solution for various industries.
1.2 Importance of Heat Resistance in Various Industries
In electronics, heat resistance ensures the reliability and longevity of devices under high operating temperatures. In aerospace, it's crucial for components to withstand the extreme heat of engine operation and atmospheric reentry. For the automotive industry, it enables engines to run efficiently and safely, preventing overheating and component failure. Heat resistance is also essential in energy production, chemical processing, and many other fields, where equipment often faces continuous or intermittent high temperatures. It's the key to maintaining performance, safety, and durability in these industries.
Heat Resistance Explained
2.1 Specific Performance Parameters of Polyimide
Polyimide's heat resistance is unparalleled, withstanding temperatures of up to 400°C and a long-term use range from -200°C to 300°C. Mechanically, it demonstrates exceptional strength, resisting pressures and拉力 with ease. In terms of electrical insulation, it has a high body resistivity, making it ideal for applications where electrical isolation is crucial. Its low dielectric constant and loss factor ensure minimal signal loss and interference. Chemically, polyimide resists most acids, alkalis, and solvents, maintaining stability in harsh environments. These parameters combined make polyimide tape a reliable choice for diverse high-temperature applications.
2.2 Thermal Stability of Polyimide Tape
Polyimide tape exhibits remarkable thermal stability, capable of withstanding continuous temperatures of up to 300°C. Its 5% thermal weight loss temperature is around 550°C in a nitrogen atmosphere, ensuring long-term reliability in high-temperature environments. This tape can maintain its structural integrity and performance for extended periods, making it suitable for applications that involve prolonged exposure to heat. Whether it's in electronic manufacturing, aerospace, or automotive industries, polyimide tape provides stable insulation and protection, even in the harshest thermal conditions.
2.3 Comparison with Silicone and PTFE Tapes
In heat resistance, polyimide tape outshines silicone tape, which has a lower maximum operating temperature. PTFE tape, though highly heat-resistant, lacks the mechanical strength and adhesive properties of polyimide. Mechanically, polyimide tape is more durable and tear-resistant than both silicone and PTFE tapes, making it better suited for applications where physical stress is a concern. In terms of chemical stability, polyimide resists a wider range of chemicals compared to silicone tape and matches PTFE's resistance. Additionally, polyimide tape offers superior electrical insulation properties, with higher dielectric strength and better resistance to electrical breakdown. Overall, polyimide tape provides a more comprehensive solution for high-temperature applications, combining excellent heat resistance, mechanical strength, and chemical stability.
Industry Applications
3.1 Electronics Manufacturing
In electronics manufacturing, polyimide tape plays a pivotal role. It's commonly used to protect circuit boards, wrapping around them to shield against dust, moisture, and physical damage. For electronic components like capacitors and resistors, it provides insulation, preventing short circuits and ensuring stable electrical performance. In the production of semiconductor devices, polyimide tape is employed during wafer handling and processing, protecting delicate wafers from scratches and contamination. Its excellent heat resistance also makes it ideal for applications involving high-temperature soldering and reflow processes, maintaining integrity and functionality in these demanding conditions.
3.2 Aerospace Thermal Barriers
In aerospace, polyimide tape serves as a crucial thermal barrier. When spacecraft reenter the atmosphere or engines operate at extreme temperatures, this tape protects high-temperature components from the intense heat. It's applied to surfaces of engine parts, wings, and other critical areas, preventing heat damage and maintaining structural integrity. Polyimide tape's high thermal stability and resistance to thermal shock allow it to withstand the harsh conditions of space travel, ensuring the safety and reliability of aerospace vehicles. It's a vital component in the thermal protection systems that protect spacecraft and their crew from the extreme temperatures encountered during missions.
3.3 Automotive Use
In the automotive industry, polyimide tape is essential for insulating and protecting high-temperature components. It's used on engine parts, such as exhaust manifolds and turbochargers, to withstand the intense heat generated during operation. By insulating these components, polyimide tape reduces heat transfer to surrounding areas, preventing damage to nearby parts and improving overall engine efficiency. It's also employed in electrical systems, insulating wires and connections in high-temperature environments, ensuring reliable electrical performance and preventing potential fires. In hybrid and electric vehicles, polyimide tape is used in battery systems to provide thermal protection and maintain safety.
Case Study: Automotive Use
4.1 Specific Application in Automotive Industry
In the automotive industry, polyimide tape is widely used in various components, particularly in the electrical system. Take the engine control unit (ECU) for example, it's a critical component that regulates engine performance. The ECU is subjected to high temperatures due to the heat generated by the engine, as well as vibrations and exposure to harsh chemicals. Polyimide tape is employed to insulate the wires and connections within the ECU, preventing short circuits and ensuring stable electrical signals. It's wrapped around the wires, providing a strong and durable barrier against heat, moisture, and physical damage. Moreover, in the battery systems of electric and hybrid vehicles, polyimide tape is used to insulate the high-voltage cables and components, safeguarding against electrical hazards and maintaining the integrity of the battery pack. By protecting these crucial components, polyimide tape plays a vital role in ensuring the reliability and safety of the entire vehicle.
4.2 Performance and Reliability Improvement
The use of polyimide tape significantly improves the performance and reliability of automotive components. In the ECU, for instance, its excellent heat resistance ensures that the wires and connections remain stable even in high-temperature environments, preventing signal interference and malfunctions. This enhances the overall engine performance, enabling smoother operation and better fuel efficiency. Polyimide tape's strong adhesive properties keep the insulation in place, resisting vibrations and preventing loosening or detachment. Its chemical stability protects against corrosion from oils, coolants, and other fluids commonly found in the engine compartment. In battery systems, the tape's insulation reduces the risk of electrical arcs and fires, enhancing safety. By improving the reliability of these components, polyimide tape contributes to longer vehicle lifespan, reduced maintenance costs, and increased driver confidence.
Conclusion
5.1 Summary of Advantages
Polyimide tape is the optimal choice for high-temperature applications due to its unparalleled advantages. It offers outstanding heat resistance, enduring temperatures up to 300°C and maintaining stability at 550°C. Mechanically, it's strong and tear-resistant, withstanding physical stress. Chemically, it resists a wide range of substances, ensuring reliability in harsh environments. Its excellent electrical insulation properties, with high dielectric strength, protect against electrical breakdown. These advantages make polyimide tape indispensable in electronics manufacturing for circuit board and component protection, aerospace thermal barriers to safeguard spacecraft and engines, and automotive insulation for engine and electrical systems, enhancing performance and safety in all these industries.
5.2 Future Potential in High-Temperature Applications
As technology advances and industries demand higher performance in extreme environments, polyimide tape's future potential in high-temperature applications is immense. In emerging fields like advanced semiconductor manufacturing, which involves increasingly higher temperatures, its superior heat and electrical properties will be crucial. The growth of electric and hybrid vehicles necessitates more reliable thermal protection, where polyimide tape's heat resistance and durability could play a larger role. With continued innovation, polyimide tape is poised to expand its applications in aerospace, energy production, and other high-temperature industries, contributing to the development of more advanced and reliable products.
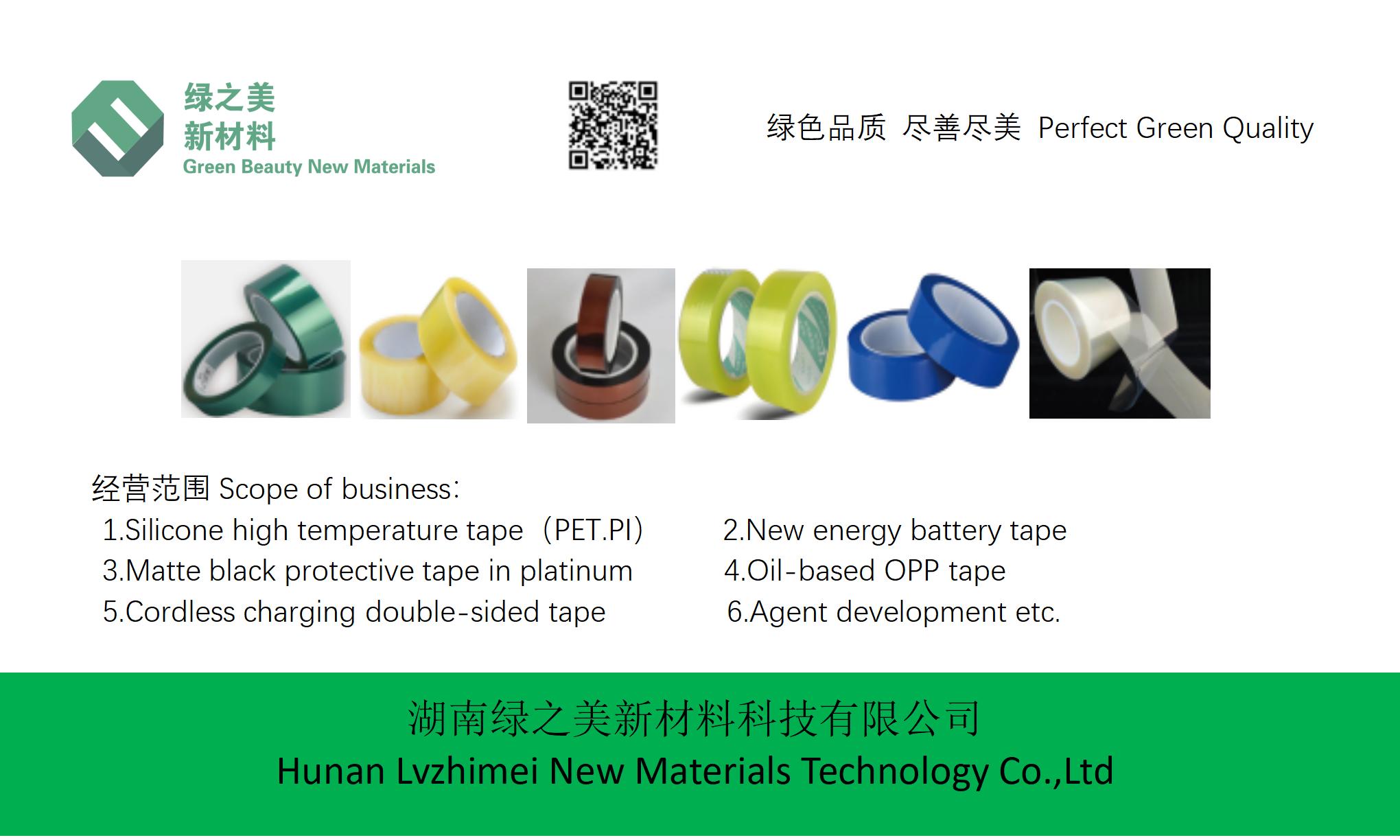