The Science Behind PI Material High Temperature Resistant 300 Tape
一、Polymer Chemistry of Polyimide
1.1 Introduction to Polyimide
In the vast realm of materials science, polyimide (PI) stands out as a high-performance polymer with exceptional thermal stability. It is one of the best-performing organic high-molecular-weight materials, renowned for its ability to withstand temperatures exceeding 400°C, with a long-term service temperature range of -200°C to 300°C. PI's absence of a distinct melting point, along with its high electrical insulation properties, makes it an F to H-grade insulator material. This remarkable material is widely employed in aerospace, microelectronics, nanotech, liquid crystal displays, separation membranes, and laser technology, among other fields. Its versatility and durability have earned it the title of "problem-solving expert," with the recognition that "without polyimide, there would be no modern microelectronics technology." PI films, in particular, are known as the "golden films" and are crucial components in printed circuit boards, electronic packaging, and display panels.
1.2 Chemical Structure of Polyimide
Polyimide's chemical structure is characterized by the presence of aromatic rings and imide bonds. Its backbone consists of repeating units containing酰亚胺环 (-CO-NH-CO-), which are formed by the reaction of aromatic dianhydrides and diamines. The aromatic rings provide rigidity and strength to the polymer chain, while the imide bonds confer exceptional thermal and chemical stability. Depending on the chemical structure of the repeating units, polyimide can be classified into aliphatic, semi-aromatic, and aromatic types. This unique structure enables polyimide to maintain its properties even in harsh environments, making it a preferred material for applications that demand high reliability and durability.
1.3 Influence of Chemical Structure on Thermal Resistance
The chemical structure of polyimide is pivotal in imparting its remarkable high-temperature resistance. The aromatic rings in its structure offer inherent stability by resisting thermal degradation. These rings, with their delocalized π electrons, create a strong covalent bond network that is difficult to break down at high temperatures. The imide bonds, formed by the condensation of carboxylic acid groups with amines, are highly thermally stable due to their strong bond energy. Additionally, the presence of bulky side groups or heterocyclic structures in some polyimide variants further enhances thermal stability by increasing steric hindrance and reducing chain mobility. For instance, polyimides containing large-volume side groups like dimethyl structures or fluorine atoms can increase the glass transition temperature, allowing the material to retain its properties at even higher temperatures. The precise arrangement of these structural elements ensures that polyimide can withstand extreme temperatures without compromising its mechanical and electrical properties, making it an ideal choice for applications in demanding environments.
二、Thermal Degradation Thresholds
2.1 Thermal Degradation Mechanism of Polyimide
Polyimide's thermal degradation primarily involves the breaking of its robust chemical bonds at high temperatures. The aromatic rings and imide bonds, which confer thermal stability, gradually become susceptible to thermal stress. The imide bonds, particularly, start to decompose, releasing small molecules like carbon dioxide and water. This process typically follows a free radical mechanism, where heat provides the energy to generate free radicals that initiate and propagate the degradation reaction. The polymer chain scissions occur, leading to a decrease in molecular weight and a loss of mechanical and electrical properties, eventually compromising the material's integrity and functionality.
2.2 Factors Affecting Thermal Degradation
Temperature is a crucial factor in polyimide's thermal degradation. As temperatures rise, the kinetic energy of molecules increases, making bonds more prone to breakage. Oxygen also plays a significant role, as it can react with polyimide to form peroxides, accelerating the degradation process through oxidation reactions. Humidity and moisture can hydrolyze the imide bonds, leading to chain scissions. Additionally, mechanical stress during processing or use can create defects in the material, providing sites for degradation to initiate. The presence of impurities or catalysts can lower the activation energy for degradation reactions, making the material more susceptible to thermal breakdown. These factors can interact with each other, exacerbating the degradation process and affecting polyimide's performance and lifespan.
2.3 Determination of Thermal Degradation Thresholds
To determine polyimide's thermal degradation threshold, techniques like thermogravimetric analysis (TGA) are commonly used. In TGA, the sample is heated in a controlled environment, and its mass change is monitored as a function of temperature. The onset temperature of mass loss, often indicated by the initial decomposition temperature (IDT), serves as a key indicator of the material's thermal stability. Other methods, such as differential scanning calorimetry (DSC), can also provide insights into thermal transitions and degradation processes. By combining these techniques and analyzing the data, scientists can accurately determine the thermal degradation threshold of polyimide and ensure its reliability for various applications.
三、Mechanical Properties at Elevated Temperatures
3.1 Tensile Strength and Elastic Modulus at High Temperatures
As temperatures rise, the tensile strength of PI tape generally declines. At elevated temperatures, the molecular bonds become less stable, reducing the material's ability to resist tensile forces. The elastic modulus also tends to decrease, indicating a lower stiffness and increased susceptibility to deformation under load. These changes are crucial for applications where PI tape is subjected to mechanical stress in high-temperature environments, as they affect the tape's durability and structural integrity.
3.2 Creep and Fatigue Characteristics at High Temperatures
Creep is a significant issue for PI tape at high temperatures. Under constant stress, the material gradually deforms over time, even when the stress is below its yield strength. This creep behavior can lead to dimensional changes and eventual failure. Fatigue, on the other hand, occurs when PI tape is subjected to cyclic loading at high temperatures. The repeated stress cycles cause microscopic damage, leading to cracks and ultimately fatigue failure. Both creep and fatigue can significantly impact the reliability and lifespan of PI tape in applications such as aerospace and industrial equipment, where it is exposed to continuous and fluctuating loads at elevated temperatures.
3.3 Dimensional Stability at High Temperatures
PI tape demonstrates excellent dimensional stability at high temperatures. Its thermal expansion coefficient is relatively low, meaning it expands and contracts only slightly with changes in temperature. This stability is critical for applications where precise dimensions are required, such as in microelectronics and precision engineering. The tape's ability to maintain its shape and dimensions under extreme temperatures ensures consistent performance and reliability in demanding environments.
四、Testing Methods and Standards
4.1 Common Testing Methods for High-Temperature Performance
To evaluate PI tape's high-temperature performance, various methods are employed. Thermal aging tests involve subjecting the tape to high temperatures for extended periods, assessing changes in properties like tensile strength and mass. Thermal cycling tests simulate temperature fluctuations, examining how the tape withstands repeated heating and cooling. TGA is used to monitor mass loss with temperature, indicating thermal stability. DSC measures heat flow, providing insights into thermal transitions. Mechanical tests at elevated temperatures evaluate tensile strength, elastic modulus, creep, and fatigue behavior, ensuring the tape's structural integrity in high-temperature applications.
4.2 Relevant Testing Standards
PI tape is subject to several testing standards. ASTM D2307 covers the electrical properties of polyimide films, ensuring their electrical performance. ASTM D882 tests the tensile properties of plastic films, including PI tape, assessing its mechanical strength. ISO 1043-1 provides guidelines for the designation of plastics, aiding in the classification and identification of PI materials. These standards ensure consistency and reliability in the production and use of PI tape, guaranteeing its quality and performance for various applications.
4.3 Application of Testing Methods and Standards
In the production of PI tape, testing methods and standards are crucial. During manufacturing, TGA is used to monitor the thermal stability of raw materials and ensure consistent product quality. DSC helps determine the optimal curing temperatures for the tape, ensuring proper bonding and structural integrity. Mechanical testing at high temperatures is conducted to verify the tape's strength and durability, ensuring it meets application-specific requirements. Standards like ASTM D2307 and D882 guide the testing process, specifying test conditions and acceptable performance ranges. This ensures that the PI tape produced complies with industry standards and can be trusted for use in critical applications like aerospace and electronics, where high-temperature resistance is essential.
五、Material Innovations and Limitations
5.1 Methods to Improve Thermal Resistance
To enhance polyimide's thermal resistance, copolymerization is a viable approach. By incorporating different monomers, the polymer chain can be modified to improve heat resistance. Adding nanofillers like graphene or carbon nanotubes can also boost thermal stability. These nanomaterials, with their high thermal conductivity and rigid structure, reinforce the polyimide matrix and hinder heat-induced degradation. Additionally, introducing bulky side groups or heterocyclic structures can increase steric hindrance, further enhancing thermal stability.
5.2 Current Limitations and Challenges
Improving polyimide's thermal resistance faces challenges. As thermal resistance increases, processing becomes more difficult due to higher melt viscosities. This hampers manufacturing and increases costs. Balancing thermal resistance with other properties like mechanical strength and electrical insulation is also a dilemma. Finding the optimal combination of monomers and additives to achieve desired properties while maintaining cost-effectiveness is a significant challenge.
5.3 Future Development Directions
Polyimide materials could explore new monomer designs and advanced nanotech to overcome limitations. Developing innovative synthesis methods for precise molecular control and exploring hybrid materials that combine polyimide's strengths with other materials' advantages are potential directions.
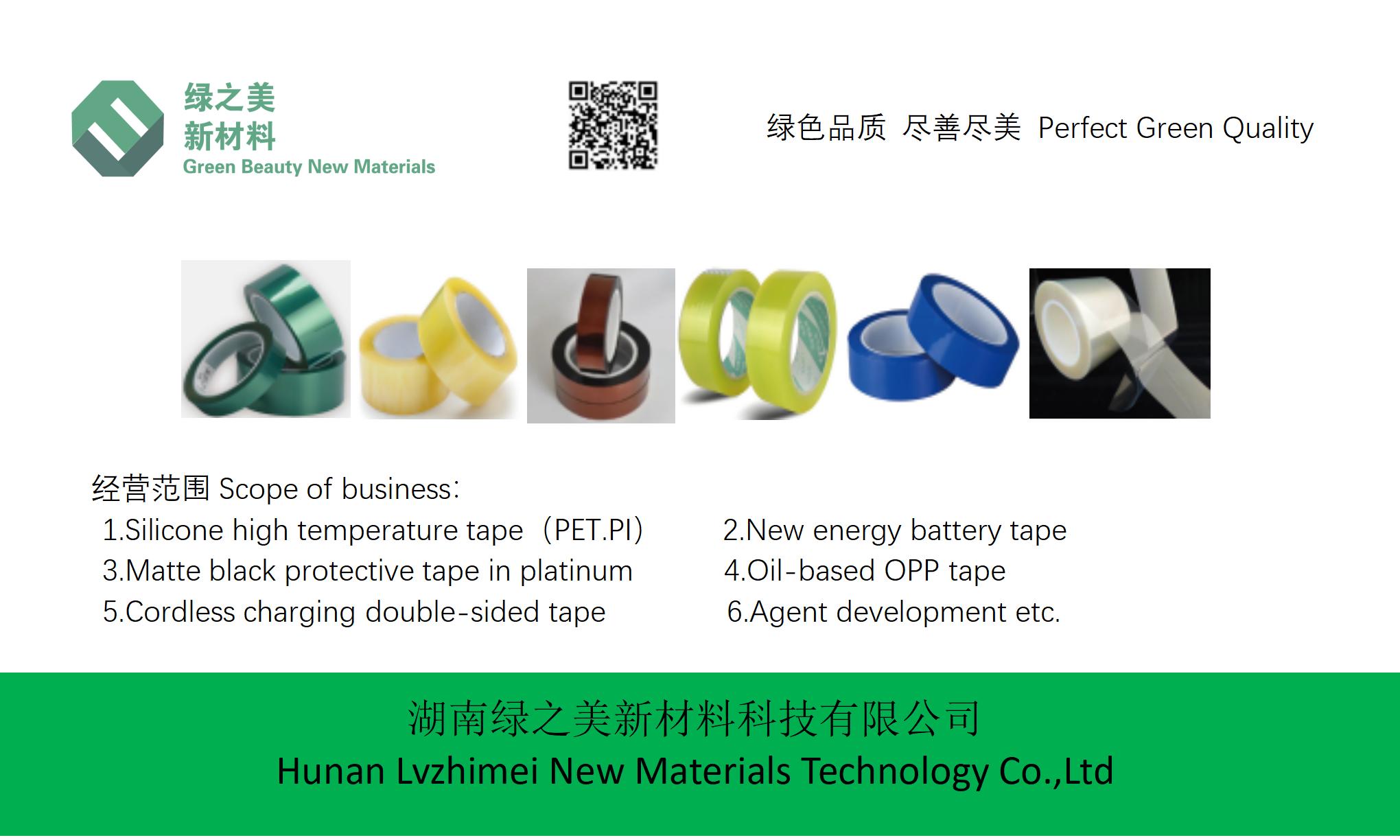