Polymer Chemistry of Polyimide
Polyimide (PI) is a class of high-performance polymers renowned for their outstanding thermal stability and mechanical properties. The exceptional high-temperature resistance of PI materials stems from their unique molecular structure and synthetic chemistry.
The synthesis of PI typically involves a two-step process: the formation of a polyamic acid precursor followed by imidization to yield the final polyimide structure. The first step involves the polymerization of dianhydride and diamine monomers. Common dianhydrides used in PI synthesis include pyromellitic dianhydride (PMDA), while typical diamines include 4,4'-oxydianiline (ODA). This polymerization reaction results in the formation of a linear polyamic acid with a high molecular weight.
The key to the high thermal stability of PI lies in its molecular structure. The polyimide backbone features a rigid aromatic ring system, which is connected by imide linkages. This rigid structure restricts molecular chain mobility, contributing to the material's high glass transition temperature (Tg) and thermal degradation temperature. The imide groups (-CO-N-CO-) in the backbone are highly thermally stable, as they possess strong chemical bonds that are resistant to thermal decomposition.
Furthermore, the aromatic rings in the PI structure contribute to its high thermal resistance through π-π stacking interactions between adjacent aromatic rings. These interactions enhance the intermolecular forces, further stabilizing the polymer structure at high temperatures. The combination of the rigid aromatic backbone and strong intermolecular interactions gives PI materials their remarkable ability to maintain structural integrity at elevated temperatures.
The molecular weight of the PI also plays a crucial role in its thermal and mechanical properties. Higher molecular weights generally lead to better thermal stability and mechanical strength, as they result in longer polymer chains with more extensive intermolecular interactions.
In addition to the basic structure, the chemical composition of PI can be tailored by selecting different dianhydride and diamine monomers. This allows for the customization of properties such as thermal resistance, flexibility, and chemical resistance to meet specific application requirements. For example, the introduction of certain functional groups or flexible spacers into the monomer structure can adjust the flexibility of the PI while maintaining its high-temperature resistance.
The unique polymer chemistry of PI thus provides the fundamental basis for the high-temperature resistance of PI tape, enabling it to perform reliably in harsh thermal environments.
Thermal Degradation Thresholds
Understanding the thermal degradation thresholds of PI materials is essential for evaluating their performance and reliability at high temperatures. Thermal degradation refers to the chemical and physical changes that occur in the material when exposed to elevated temperatures over an extended period.
The thermal degradation of PI typically occurs through a series of complex chemical reactions, including chain scission, oxidation, and the release of volatile by-products. The specific degradation mechanisms depend on various factors, such as the temperature, exposure time, atmosphere (e.g., air, inert gas), and the chemical structure of the PI.
One of the key parameters used to characterize the thermal stability of PI is the temperature at which significant weight loss begins to occur. This is often determined through thermogravimetric analysis (TGA), a technique that measures the change in weight of a material as a function of temperature. For most commercial PI materials, significant weight loss typically begins at temperatures above 500°C in an inert atmosphere, demonstrating their excellent thermal stability.
However, in an oxidative atmosphere (such as air), the thermal degradation of PI occurs at lower temperatures due to the combined effect of heat and oxygen. The presence of oxygen can accelerate the degradation process by promoting oxidative chain scission reactions. In air, the onset of significant weight loss for many PI materials is around 400-450°C, although this can vary depending on the specific composition and structure of the PI.
The thermal degradation thresholds of PI tape are of particular importance for its application in high-temperature environments. The tape is often required to maintain its adhesive properties, mechanical strength, and insulating characteristics at temperatures up to 300°C. At this temperature, PI tape typically exhibits minimal degradation, as 300°C is well below the onset of significant thermal degradation in both inert and oxidative atmospheres for most PI materials.
To better understand the thermal degradation behavior of PI tape at 300°C, long-term thermal aging studies are often conducted. These studies involve exposing the tape to 300°C for extended periods (e.g., hundreds or thousands of hours) and monitoring changes in its properties, such as weight loss, mechanical strength, and adhesive performance.
Results from such studies typically show that PI tape maintains its properties remarkably well at 300°C. For example, after 1000 hours of exposure to 300°C in air, the weight loss of PI tape is usually less than 5%, and its mechanical properties, such as tensile strength and elongation at break, may only experience a slight decrease. The adhesive strength of the tape also remains relatively stable, ensuring its functionality in high-temperature applications.
The ability of PI tape to withstand 300°C is attributed to the inherent thermal stability of the PI polymer, as discussed in the previous section. The rigid aromatic backbone and thermally stable imide linkages resist thermal decomposition at this temperature, allowing the tape to maintain its structural and functional integrity.
However, it is important to note that prolonged exposure to temperatures near or above the thermal degradation threshold can gradually lead to cumulative damage and a decline in performance. Therefore, understanding the thermal degradation thresholds helps in determining the safe operating temperature range and service life of PI tape in various high-temperature applications.
Mechanical Properties at Elevated Temperatures
The mechanical properties of PI tape at elevated temperatures are critical for its performance in demanding applications where both high temperatures and mechanical stresses are present. Understanding how these properties change with temperature is essential for selecting the appropriate PI tape for specific applications and ensuring its reliability.
At room temperature, PI tape exhibits excellent mechanical properties, including high tensile strength, modulus, and flexibility. The tensile strength of PI tape is typically in the range of 50-100 MPa, while the modulus can be as high as several GPa, depending on the specific formulation and thickness of the tape. These properties make PI tape suitable for a wide range of applications that require mechanical durability.
When exposed to elevated temperatures, the mechanical properties of PI tape undergo certain changes. In general, as the temperature increases, the tensile strength and modulus of PI tape tend to decrease, while the elongation at break may increase. However, the rate and extent of these changes depend on the specific temperature, exposure time, and the type of PI material used.
At 300°C, which is a common operating temperature for PI tape in high-temperature applications, the mechanical properties of the tape still remain at a relatively high level. For example, the tensile strength of PI tape at 300°C may be around 60-80% of its room-temperature value, while the modulus may decrease to 70-90% of its original value. The elongation at break at 300°C is often higher than at room temperature, as the increased thermal energy allows for greater molecular chain mobility.
The ability of PI tape to retain significant mechanical properties at 300°C is a result of its unique molecular structure and thermal stability. The rigid aromatic backbone and strong intermolecular interactions in the PI polymer provide resistance to thermal softening and maintain a certain level of mechanical strength even at high temperatures.
To characterize the mechanical properties of PI tape at elevated temperatures, various testing methods are employed. Tensile testing at elevated temperatures is a common approach, where samples of the tape are subjected to tensile forces while being heated to the desired temperature. This allows for the measurement of tensile strength, modulus, and elongation at break as a function of temperature.
Another important mechanical property to consider is the creep behavior of PI tape at high temperatures. Creep refers to the gradual deformation of a material under constant stress over time. At elevated temperatures, materials are more prone to creep, which can lead to dimensional instability and failure. PI tape exhibits relatively low creep rates at 300°C, making it suitable for applications where long-term dimensional stability is required.
The adhesive mechanical properties of PI tape, such as peel strength and shear strength, are also critical for its performance. At 300°C, the adhesive system used in PI tape must maintain sufficient bonding strength to ensure that the tape remains securely attached to the substrate. Specialized adhesive formulations, often based on high-temperature-resistant adhesives such as silicone or polyimide-based adhesives, are used to achieve this.
The following table summarizes the typical mechanical properties of PI tape at room temperature and 300°C:
It is important to note that these values are approximate and can vary depending on the specific formulation, thickness, and manufacturing process of the PI tape. Additionally, the mechanical properties at 300°C can be affected by factors such as the duration of exposure and the thermal history of the tape.
Overall, the mechanical properties of PI tape at elevated temperatures, particularly at 300°C, demonstrate its suitability for high-temperature applications where both thermal stability and mechanical performance are required.
Testing Methods and Standards
To ensure the quality, reliability, and consistency of PI tape with high-temperature resistance up to 300°C, various testing methods and standards have been established. These tests evaluate different aspects of the tape's performance, including its thermal stability, mechanical properties, adhesive characteristics, and electrical insulation properties. Adherence to these standards helps in ensuring that the tape meets the required specifications for various applications.
Thermal Stability Testing
Thermogravimetric Analysis (TGA) is a widely used technique to assess the thermal stability of PI tape. This method measures the weight loss of the material as a function of temperature under a controlled atmosphere. TGA helps determine the onset temperature of thermal degradation, the temperature at which maximum weight loss occurs, and the residual weight at high temperatures. For PI tape, TGA is performed to confirm its ability to withstand 300°C with minimal weight loss and degradation.
Differential Scanning Calorimetry (DSC) is another important thermal analysis technique. DSC measures the heat flow into or out of a material as a function of temperature, providing information about phase transitions such as the glass transition temperature (Tg) and melting point. For PI tape, DSC is used to determine the Tg, which is an important indicator of the material's thermal stability and its ability to maintain mechanical properties at high temperatures.
Long-term thermal aging tests are also conducted to evaluate the durability of PI tape at 300°C. In these tests, samples of the tape are exposed to 300°C for extended periods (e.g., 1000 hours or more) in a controlled environment, such as an oven. After aging, the samples are tested for changes in mechanical properties, adhesive strength, and other characteristics to assess their performance degradation over time.
Mechanical Properties Testing
Tensile testing is fundamental for evaluating the mechanical properties of PI tape. This test measures the tensile strength, modulus, and elongation at break of the tape. Tensile tests can be conducted at both room temperature and elevated temperatures, including 300°C, using specialized testing equipment with temperature-controlled chambers. The results provide insights into how the tape's mechanical properties change with temperature, which is crucial for applications involving thermal and mechanical stresses.
Peel strength testing is used to evaluate the adhesive bonding strength of PI tape. The most common peel test is the 180° peel test, where the tape is peeled from a substrate at a specific angle and speed, and the force required to peel it is measured. This test is performed at room temperature and, if required, at elevated temperatures to assess the adhesive performance of the tape under high-temperature conditions.
Shear strength testing measures the ability of the tape's adhesive to resist shear forces. In this test, a piece of tape is bonded to two substrates, and a shear force is applied parallel to the bond line. The shear strength is determined by the force required to cause failure of the bond. Shear tests can also be conducted at elevated temperatures to evaluate the adhesive's performance in high-temperature environments.
Electrical Insulation Properties Testing
Given that PI tape is often used as an electrical insulation material, its electrical properties are also tested. The volume resistivity and surface resistivity are measured to assess the tape's insulating capability. These tests are performed using standard methods, such as those specified in ASTM D257, which outlines the procedures for measuring the electrical resistance of insulating materials.
Dielectric strength testing is another important electrical property test. It measures the maximum electric field that the tape can withstand before electrical breakdown occurs. This test is conducted by applying an increasing voltage across the tape until breakdown happens, and the dielectric strength is calculated as the voltage per unit thickness. ASTM D149 is a commonly used standard for dielectric strength testing of solid electrical insulating materials.
Industry and International Standards
Several industry and international standards govern the testing and performance requirements of PI tape for high-temperature applications. Some of the key standards include:
UL 746B: Polymeric Materials, Industrial Laminate, Filament-Wound, and Molding Materials - Part 2: Test Methods. This standard includes tests for thermal stability, mechanical properties, and electrical insulation properties of polymeric materials, which can be applied to PI tape.
Compliance with these standards ensures that PI tape meets the required performance criteria and can be reliably used in various industries, including electronics, aerospace, automotive, and new energy.
Material Innovations and Limitations
Material Innovations
In recent years, significant advancements have been made in the development of PI materials for high-temperature resistant tapes, driven by the increasing demand for high-performance materials in various industries. These innovations have focused on enhancing the thermal stability, mechanical properties, and functional capabilities of PI tape while maintaining or improving processability.
One of the key innovations in PI tape materials is the development of new monomer formulations. By selecting and modifying dianhydride and diamine monomers, researchers and manufacturers have been able to tailor the chemical structure of PI to achieve specific property improvements. For example, the introduction of fluorinated monomers into the PI backbone has been shown to enhance the chemical resistance and reduce the dielectric constant of the material, making it suitable for high-frequency electronic applications while maintaining its high-temperature resistance.
Another important innovation is the incorporation of nanomaterials into PI matrices to form nanocomposites. The addition of nanoparticles, such as carbon nanotubes (CNTs), graphene, or metal oxides, can significantly improve the mechanical strength, thermal conductivity, and electrical properties of PI tape. For instance, the inclusion of a small amount of CNTs in PI can enhance its tensile strength and modulus by up to 30%, while also improving its thermal conductivity, which is beneficial for heat dissipation in high-temperature applications.
In terms of adhesive systems, innovations have focused on developing high-temperature-resistant adhesives that can maintain strong bonding strength at 300°C and above. Silicone-based adhesives have long been used in high-temperature tapes, but recent developments have led to the introduction of polyimide-based adhesives and other advanced adhesive formulations. These new adhesives offer improved thermal stability, better chemical resistance, and enhanced compatibility with PI substrates, resulting in tape products with superior overall performance.
Manufacturing process innovations have also played a crucial role in improving the quality and performance of PI tape. Advanced coating and curing techniques, such as continuous high-temperature imidization processes, have been developed to ensure uniform film formation and consistent properties throughout the tape. These processes allow for better control of the tape's thickness, surface smoothness, and mechanical properties, leading to improved product reliability.
Additionally, the development of functionalized PI tapes with specialized properties has expanded their application scope. For example, PI tapes with antistatic properties, flame retardancy, or enhanced chemical resistance have been developed to meet the specific requirements of different industries. These functionalized tapes are achieved through surface modification techniques or the incorporation of functional additives during the manufacturing process.
In the context of Hunan Lvzhimei New Material Technology Co., Ltd., the company has made notable innovations in the production process of high-temperature tape. Led by its experienced team, the company has invested in research and development, resulting in the innovation of high-temperature tape production processes. This has enabled the company to achieve significant improvements in product quality and performance, positioning it as an industry benchmark.
Limitations
Despite the remarkable properties and continuous innovations in PI tape, there are still certain limitations that need to be considered when using these materials in high-temperature applications.
One of the main limitations of PI tape is its cost. The synthesis of PI involves complex chemical reactions and high-quality raw materials, which can make the production process expensive. Additionally, the high-temperature processing required for manufacturing PI tape, such as the imidization step, adds to the production costs. As a result, PI tape is generally more expensive than other types of tapes, such as PET or PVC tapes, which may limit its use in cost-sensitive applications.
Another limitation is the relatively low impact resistance of PI tape compared to some other polymeric materials. While PI exhibits high tensile strength and modulus, it can be brittle under certain conditions, especially at lower temperatures. This brittleness may make PI tape more susceptible to cracking or tearing when subjected to sudden impacts or flexing, which can be a concern in applications involving dynamic mechanical stresses.
PI tape also has limitations in terms of chemical resistance to certain aggressive chemicals. Although it shows good resistance to common organic solvents such as alcohol and acetone, it may be susceptible to degradation when exposed to strong acids, 强碱 (strong bases), or certain halogenated compounds. In such harsh chemical environments, the performance and service life of PI tape may be significantly reduced.
The electrical insulation properties of PI tape can also be affected by high temperatures and humidity. Prolonged exposure to high temperatures and humid conditions can lead to a decrease in the volume resistivity and an increase in the dielectric loss of the tape, which may compromise its electrical insulation performance. This is an important consideration for applications where reliable electrical insulation is required under 湿热 (humid and hot) conditions.
Furthermore, the processing and application of PI tape can be challenging. The high melting point and viscosity of PI make it difficult to process using some conventional polymer processing techniques. Specialized equipment and processing conditions are often required, which can add to the complexity and cost of manufacturing. Additionally, the adhesive system used in PI tape may require specific application procedures, such as preheating the substrate or controlling the application temperature, to achieve optimal bonding performance.
Another limitation is the potential for outgassing of PI tape at high temperatures. When exposed to elevated temperatures in a vacuum environment, such as in aerospace applications, PI tape may release volatile components, which can contaminate sensitive equipment or affect the performance of surrounding materials. Special formulations and processing steps are needed to minimize outgassing for such critical applications.
It is important to be aware of these limitations when selecting PI tape for specific applications. By understanding the strengths and weaknesses of the material, engineers and designers can make informed decisions to ensure that PI tape is used within its appropriate operating range and conditions, maximizing its performance and reliability while mitigating potential risks.
In conclusion, the science behind PI material high temperature resistant 300 tape is rooted in the unique polymer chemistry of polyimide, which endows it with exceptional thermal stability and mechanical properties. Through continuous material innovations, the performance of PI tape continues to improve, expanding its application in various high-temperature industries. However, it is essential to consider the limitations of PI tape to ensure its proper use and optimal performance in different applications. As research and development in PI materials continue, we can expect further advancements that will address existing limitations and open up new possibilities for high-temperature resistant tape technologies.
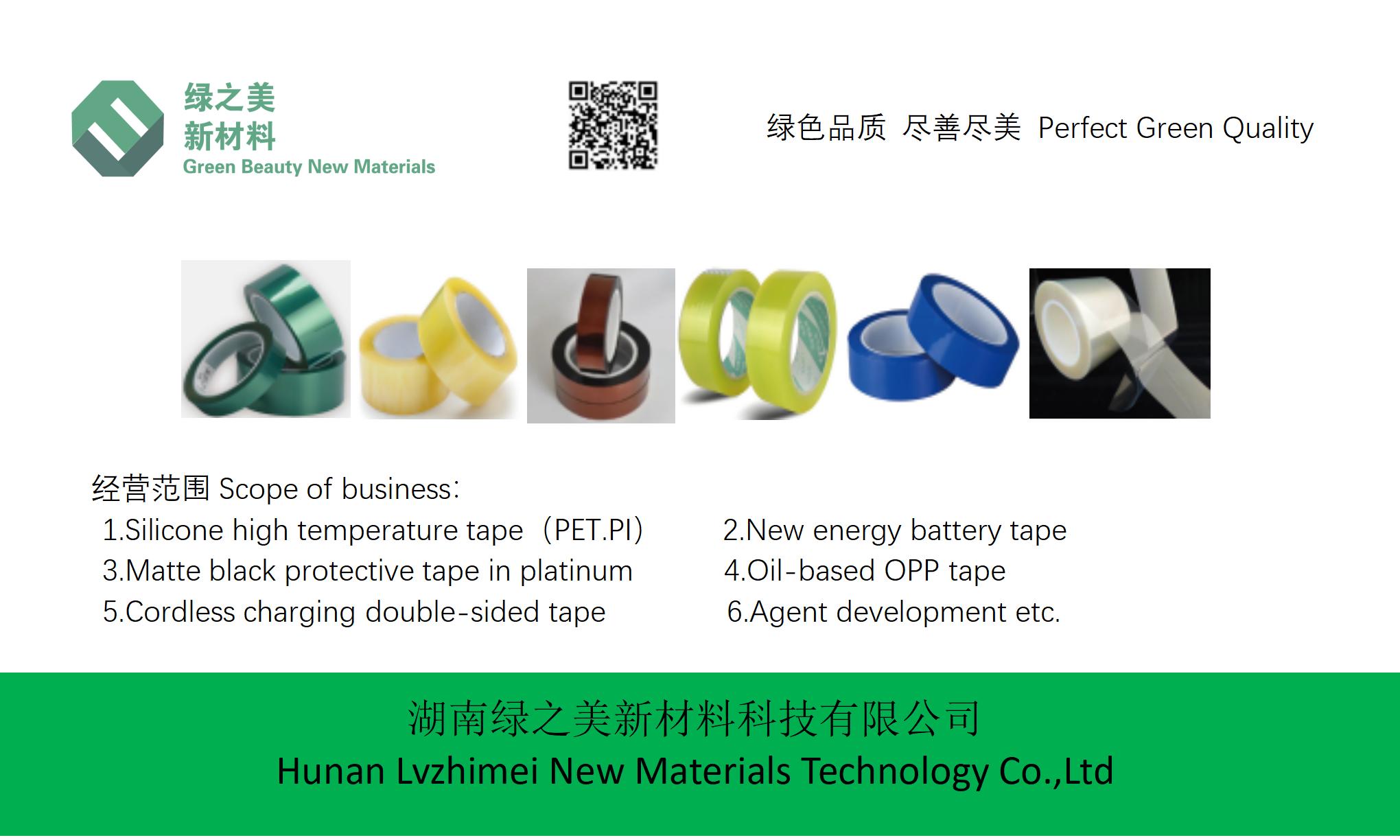