1. The Critical Role of Gold Finger Tapes in Electronics1.1 Protecting Circuit Board Gold Fingers from Oxidation and ContaminationGold finger tapes play a crucial role in safeguarding the gold fingers of circuit boards. Typically made from polyimide films with high-performance silicone pressure-sensitive adhesive on one side and fluorine-plastic release materials in some cases, these tapes offer exceptional resistance to high temperatures and solvents. Their ability to tightly adhere to the gold finger surfaces creates a barrier against oxygen and moisture, preventing oxidation. The stability of polyimide films ensures durability in harsh environments, while resistance to solvents protects against chemical contamination. This protection is essential for maintaining the functional integrity of gold fingers, ensuring circuit boards operate safely and reliably.
1.2 Ensuring Signal Transmission and Electrical PerformanceSignal transmission and electrical stability rely heavily on gold finger tapes’ insulation properties. As gold fingers facilitate communication between components, the tapes’ high insulation effectively shields against interference, minimizing signal distortion. Additionally, their low contact resistance reduces current flow obstacles, enhancing efficiency and energy conservation. This is particularly vital in high-speed devices like computers and communication equipment, where even slight disruptions can impair performance. By maintaining consistent electrical contact, gold finger tapes contribute to stable device operation and improved user experiences.
1.3 Necessity in Electronic ApplicationsGold finger tapes are indispensable in various sectors. In consumer electronics like smartphones, their protection prevents damage from tight component spacing and mechanical stress, ensuring device functionality. Medical devices (e.g., ECG machines) demand tapes with high reliability to maintain diagnostic accuracy and patient safety. Industrial control equipment often operates in corrosive or humid environments, necessitating tapes that withstand such conditions. Automotive electronics, increasingly integrated into modern vehicles, rely on tapes to ensure system stability. These applications highlight the tape’s critical role in preventing failures and maintaining product longevity.
2. The Need for Quality Standards for Gold Finger Tapes2.1 Ensuring Product Reliability and ConsistencyUnified quality standards are essential for guaranteeing tape reliability and consistency. Manufacturers must adhere to stringent technical specifications for materials (e.g., film thickness, adhesive composition), production processes, and performance testing. This ensures that tapes from different batches exhibit consistent performance, avoiding quality fluctuations. For end-users, standardized tapes offer interchangeable compatibility, reducing risks associated with equipment failures. Consistency enhances supply chain efficiency and supports the electronics industry’s sustainability.
2.2 Avoiding Quality and Safety IssuesLack of standards can lead to severe quality and safety problems. Tapes with insufficient adhesion may detach, exposing gold fingers to oxidation or contaminants, compromising electrical connections. Overly adhesive tapes risk damaging components during removal. Flammable materials without adequate flame retardancy could ignite during equipment overheating, posing fire hazards. Poor insulation may cause short circuits or electric shocks, endangering users and equipment. Standards mitigate these risks by establishing rigorous testing criteria.
2.3 Impact on Industry Competition and Consumer TrustStandardization fosters fair competition and consumer confidence. Manufacturers competing under unified benchmarks focus on innovation rather than price undercutting, driving industry advancement. Consumers purchasing certified tapes can trust their performance and safety, boosting market credibility. This trust enhances brand loyalty and market expansion, benefiting both producers and end-users.
3. Key Quality Standards for Gold Finger Tapes3.1 UL 510: Flame ResistanceUL 510 sets stringent flame resistance requirements for tapes used in electrical applications. Tapes must self-extinguish rapidly after ignition and limit flame spread under vertical and horizontal burn tests. These tests assess the tape’s ability to prevent fire propagation in overheated equipment, safeguarding both devices and users. Compliance with UL 510 demonstrates tapes’ safety for critical applications.
3.2 IPC-4204: Polyimide Film RequirementsIPC-4204 specifies physical and chemical performance criteria for polyimide films in gold finger tapes. Physical attributes include dimensional tolerances (thickness, width), tensile strength, and peel adhesion to ensure precise fitting and durability. Chemical requirements address resistance to solvents, corrosion, and thermal aging. Testing methods involve mechanical stress tests, chemical immersion trials, and thermal cycling assessments. Adherence to IPC-4204 guarantees tapes’ functionality across diverse environments.
3.3 IATF 16949: Automotive-Grade Quality ManagementIATF 16949 mandates a comprehensive quality management system for tape manufacturers targeting automotive applications. Requirements cover:
● Supplier management: Auditing raw material providers (e.g., polyimide films, adhesives) for quality assurance.
● Production control: Implementing process monitoring, defect prevention, and traceability systems.
● Post-production: Rigorous inspections and testing (e.g., electrical resistance, flame tests) for every batch.Certification demonstrates commitment to automotive industry’s stringent reliability demands, essential for safety-critical systems.
4. Quality Control Measures by Major Manufacturers4.1 MEIDA and Scapa’s Quality Control ProcessesMEIDA and Scapa exemplify stringent quality control. MEIDA rigorously selects high-quality raw materials, controls production environment parameters (temperature, humidity), and employs real-time monitoring during critical steps (e.g., adhesive coating). Scapa implements traceability systems, assigning unique codes to each tape roll to track manufacturing history. Both companies invest in advanced equipment and continuous process optimization to maintain superior product consistency.
4.2 Variations in Quality Control Among ManufacturersDifferences exist across manufacturers. Large brands like MEIDA and Scapa prioritize stringent raw material sourcing, detailed process control, and comprehensive testing, resulting in reliable performance. Smaller companies may face resource constraints, adopting less rigorous quality checks, leading to inconsistent product quality. Varying interpretations of standards can also result in performance disparities, emphasizing the importance of certified manufacturers for critical applications.
5. The Importance of Global Supply Chain Consistency5.1 Promoting Global Supply Chain CoordinationUnified standards streamline global tape supply chains. Suppliers, manufacturers, and distributors align on shared quality expectations, enabling seamless collaboration. Raw material suppliers meet specified attributes, manufacturers produce consistent products, and logistics partners handle goods under standardized conditions. This coordination reduces delays, waste, and communication costs, boosting supply chain resilience.
5.2 Problems Arising from InconsistencyLack of global consistency can disrupt supply chains. Performance variations in tapes sourced from different regions risk equipment failures, safety hazards, and reputation damage. Inconsistent quality may lead to inventory mismatches, production delays, and increased warranty costs. Moreover, incompatible tapes hinder international trade, limiting market access for manufacturers and suppliers.
5.3 Impact on International Trade and Technical CollaborationStandardization facilitates global trade by eliminating technical barriers. Conforming to recognized benchmarks (e.g., UL, IPC) enables tapes to circulate freely across borders, reducing compliance costs. For technical collaboration, shared standards provide a common platform for R&D, encouraging cross-border partnerships to develop advanced materials and processes. This synergy enhances global electronics innovation and competitiveness.
6. Future Trends in Gold Finger Tape Quality Standards6.1 Influence of New Technologies and MaterialsAdvancements in materials (e.g., nano-enhanced adhesives, high-temperature polymers) and technologies (e.g., precision coating systems) will drive standard evolution. Future tapes may offer thinner profiles for miniaturized devices, self-monitoring capabilities to alert degradation, or enhanced resistance to extreme conditions. Standards will evolve to assess these novel properties, ensuring performance meets emerging application demands.
6.2 Effects of Environmental and Sustainability RequirementsGrowing environmental concerns will shape future standards. Expectations for biodegradable materials, reduced energy consumption in production, and recyclability will become integral criteria. Tapes may shift towards eco-friendly polymers and solvent-free adhesives. Lifecycle assessments and carbon footprint evaluations could become standard evaluation components, aligning with global sustainability goals.
6.3 Emergence of New Quality Standards or RequirementsAs electronics evolve, specialized standards may emerge. For example, standards targeting aerospace or quantum computing applications could demand tapes with radiation resistance or ultra-low outgassing properties. Smart electronics might require tapes with integrated sensors or data storage capabilities. These advancements will prompt new quality frameworks to ensure tapes meet increasingly sophisticated industry needs.
ConclusionGold finger tape quality standards, set by organizations like UL, IPC, and IATF, ensure product safety, performance, and global compatibility. Major manufacturers’ adherence to these benchmarks, coupled with continuous innovation, underpins electronics reliability. As technology and sustainability demands evolve, future standards will adapt, balancing advanced functionality with environmental responsibility. Understanding and enforcing these standards remains pivotal for the electronics industry’s growth and trustworthiness.
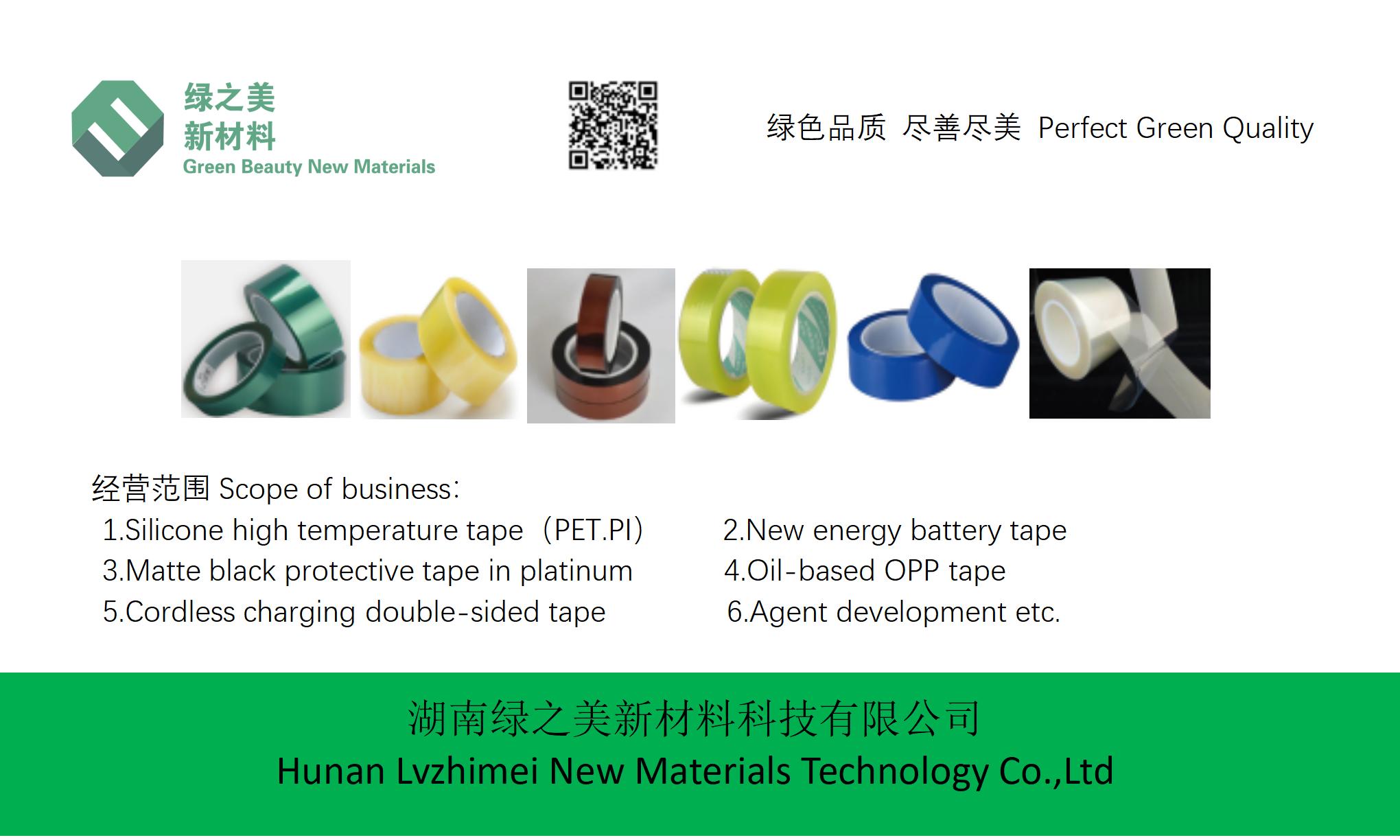