I. Overview of Sustainability Challenges in the Electronics Industry
1.1 Environmental and Health Impacts of E-Waste
The improper disposal of e-waste poses severe environmental and health risks. For example, discarded cathode ray tube (CRT) monitors contain hazardous substances such as lead, cadmium, beryllium, mercury, and brominated flame retardants. When these materials are not handled properly, they leach into soil, water, and air, contaminating ecosystems. Lead exposure can impair children's neurological development, causing intellectual disabilities and behavioral disorders. Mercury damages the nervous system and kidneys, particularly threatening pregnant women and fetuses. Cadmium has been linked to kidney damage and bone diseases. In regions with high e-waste concentration, residents often suffer from elevated rates of cancer and respiratory illnesses due to prolonged exposure to toxins.
1.2 Environmental Issues in Electronics Manufacturing
The electronics manufacturing process generates substantial environmental pollutants. During production, emissions from cutting (e.g., barium aluminum powder, chromium nickel dust), welding, laser processing, and printed circuit board (PCB) fabrication release harmful gases. These emissions contribute to air pollution and acid rain formation, harming ecosystems. Wastewater contains heavy metals, chemical solvents, and other toxic substances. Improper discharge of untreated wastewater pollutes water bodies, endangering aquatic life. Solid wastes, including discarded silicon wafers and chemical packaging materials,占用 land resources and leach harmful substances into soil and groundwater, causing long-term contamination.
1.3 Lifecycle Environmental Impact of Electronics
The lifecycle of electronics, from raw material extraction to disposal, has significant environmental consequences. Mining for rare earth metals, lithium, and other materials destroys vegetation, causes soil erosion, and triggers geological hazards. Manufacturing consumes vast amounts of energy and generates waste. During use, devices contribute to electricity consumption and greenhouse gas emissions. At end-of-life, improper disposal releases toxins, while recycling in unregulated facilities often results in secondary pollution due to inadequate treatment technologies. This lifecycle creates a continuous environmental burden.
II. Characteristics of Kapton Tape and Its Role in Electronics Manufacturing
2.1 Application of High-Temperature Resistance
Kapton tape exhibits exceptional high-temperature resistance, maintaining stability within the range of -269℃ to 400℃. This property ensures its functionality during high-temperature processes like soldering and oven curing. For instance, in H-class motor and transformer coil insulation, Kapton tape withstands thermal stress, protecting coils from damage. Similarly, in PCB manufacturing, it reinforces flexible circuits and provides thermal protection, preventing board degradation and ensuring device reliability in extreme environments.
2.2 Enhancing Safety and Reliability with Electrical Insulation
Kapton tape offers superior electrical insulation, with volume resistivity exceeding 10⁶ Ω·cm. This feature effectively prevents leakage and short circuits in densely packed electronic components. In潮湿 or high-temperature conditions, its stable insulation properties safeguard equipment from electrical failures. By isolating circuits and components, Kapton tape reduces the risk of malfunctions and accidents, enhancing product safety and longevity.
2.3 Mechanical Durability for Long-Term Performance
The tape's mechanical strength, including high tensile resistance and flexibility, enables it to withstand mechanical stress. With elongation at break above 50%, Kapton tape remains intact under stretching, vibration, or bending. This durability ensures consistent performance in harsh environments, reducing maintenance costs and replacement frequency. For example, in aerospace or automotive electronics subjected to frequent mechanical shocks, Kapton tape maintains its integrity, contributing to device longevity.
III. Waste Reduction through Kapton Tape
3.1 Precision Application Minimizes Material Waste
Advanced cutting technologies (e.g., laser precision cutting) and automated application systems optimize Kapton tape usage. Micron-level accuracy allows tailored tape shapes to fit component geometries, minimizing scraps. Automated machines ensure precise placement, reducing rework due to misalignment. These techniques significantly cut material waste, aligning with sustainable manufacturing goals.
3.2 Reusability Reduces Single-Use Material Consumption
Certain Kapton tape variants allow reuse under specific conditions. The polyimide film and silicone adhesive retain adhesive properties after detachment, enabling reuse in temporary protective or removable applications. For example, during PCB prototyping or component testing, reusable Kapton tape reduces reliance on disposable insulation materials, lowering environmental impact.
3.3 Chemical Resistance Extends Product Lifespan
Kapton tape's resistance to acids, alkalis, and solvents enhances durability in corrosive environments. In industrial equipment exposed to chemical vapors or liquids, traditional insulation materials degrade rapidly. Kapton tape's stability prolongs device lifespan, reducing replacement rates and waste generation. For example, in petrochemical plants, its resistance to corrosive gases extends equipment life, minimizing maintenance-related waste.
IV. Longevity and Sustainability
4.1 Endurance to Temperature Cycling
Kapton tape withstands over 5,000 thermal cycles between -55℃ and 125℃ without performance degradation. This resilience is crucial in automotive electronics subjected to engine compartment temperature fluctuations or industrial equipment operating in extreme conditions. Reliable performance across cycles reduces failures and replacement needs.
4.2 Aging Resistance for Extended Lifespan
The tape's polyimide substrate resists UV radiation, ozone, and oxidation, maintaining mechanical and electrical properties over decades. Unlike materials that brittle under sunlight or degrade in high humidity, Kapton tape ensures stable insulation in outdoor equipment (e.g., solar panels) or indoor systems with fluctuating conditions.
4.3 Resource Conservation through Reduced Replacement
Kapton tape's longevity reduces device replacement frequency. For example, in household appliances, traditional insulation may need replacement every few years, while Kapton tape can last a decade. This extension saves resources (e.g., raw materials, energy for production) and decreases e-waste generation, aligning with circular economy principles.
V. Compliance with Environmental Regulations
5.1 Alignment with WEEE Directive
The Waste Electrical and Electronic Equipment (WEEE) Directive mandates e-waste management and recycling. Kapton tape facilitates compliance by being easily separable from components during recycling. Its polyimide and silicone components are recyclable, enabling recovery and reuse in new products. This recyclability reduces landfill contributions and supports the directive's objectives.
5.2 RoHS Compliance for Hazard-Free Electronics
Kapton tape meets Restriction of Hazardous Substances (RoHS) standards, excluding lead, mercury, cadmium, and other restricted materials. Its non-toxic composition ensures that devices using the tape do not pose health risks during disposal. Compliance enables products to access global markets and reinforces sustainability credentials.
VI. Comparison with Traditional Insulation Materials
6.1 Environmental Performance Comparison
Aspect | Kapton Tape | Traditional Materials (e.g., PVC, PET) |
Waste Reduction | Precision application, reuse | High scrap rates, non-reusable |
Recycling | Polyimide recyclability | Difficult to recycle, often landfilled |
Chemical Safety | RoHS-compliant | May contain harmful additives |
6.2 Lifespan Comparison
Kapton tape's durability (10+ years) surpasses materials like PVC (3-5 years) or PET (5-8 years), reducing replacement cycles and waste. Longevity translates to lower environmental footprints through extended product life.
6.3 Overall Performance and Cost Balance
While Kapton tape has higher upfront costs, its longevity and performance reduce total cost of ownership. Traditional materials, despite lower prices, require frequent replacement, leading to higher long-term costs and environmental burdens.
VII. Contributions and Future Outlook
7.1 Summary of Sustainability Contributions
Kapton tape addresses multiple sustainability challenges: minimizing waste through precision use and recyclability; extending product life with thermal and chemical resistance; and ensuring regulatory compliance. Its performance advantages over traditional materials make it a key enabler of green electronics manufacturing.
7.2 Future Prospects
As environmental regulations tighten and industries (e.g., renewable energy, electric vehicles) demand durable components, Kapton tape's role will expand. Advancements in recycling technologies for polyimide materials may further enhance its circularity. Integration into emerging electronics—like flexible displays or wearable devices—will solidify its status as a sustainable solution, driving electronics toward a more eco-friendly future.
ConclusionKapton tape's unique combination of performance, durability, and environmental compatibility makes it a transformative material in electronics sustainability. By reducing waste, extending device lifespans, and supporting regulatory compliance, it paves the way for greener electronics manufacturing and consumption. As technologies evolve, its potential to mitigate e-waste and resource depletion will only grow, solidifying its role as a cornerstone of sustainable electronics.
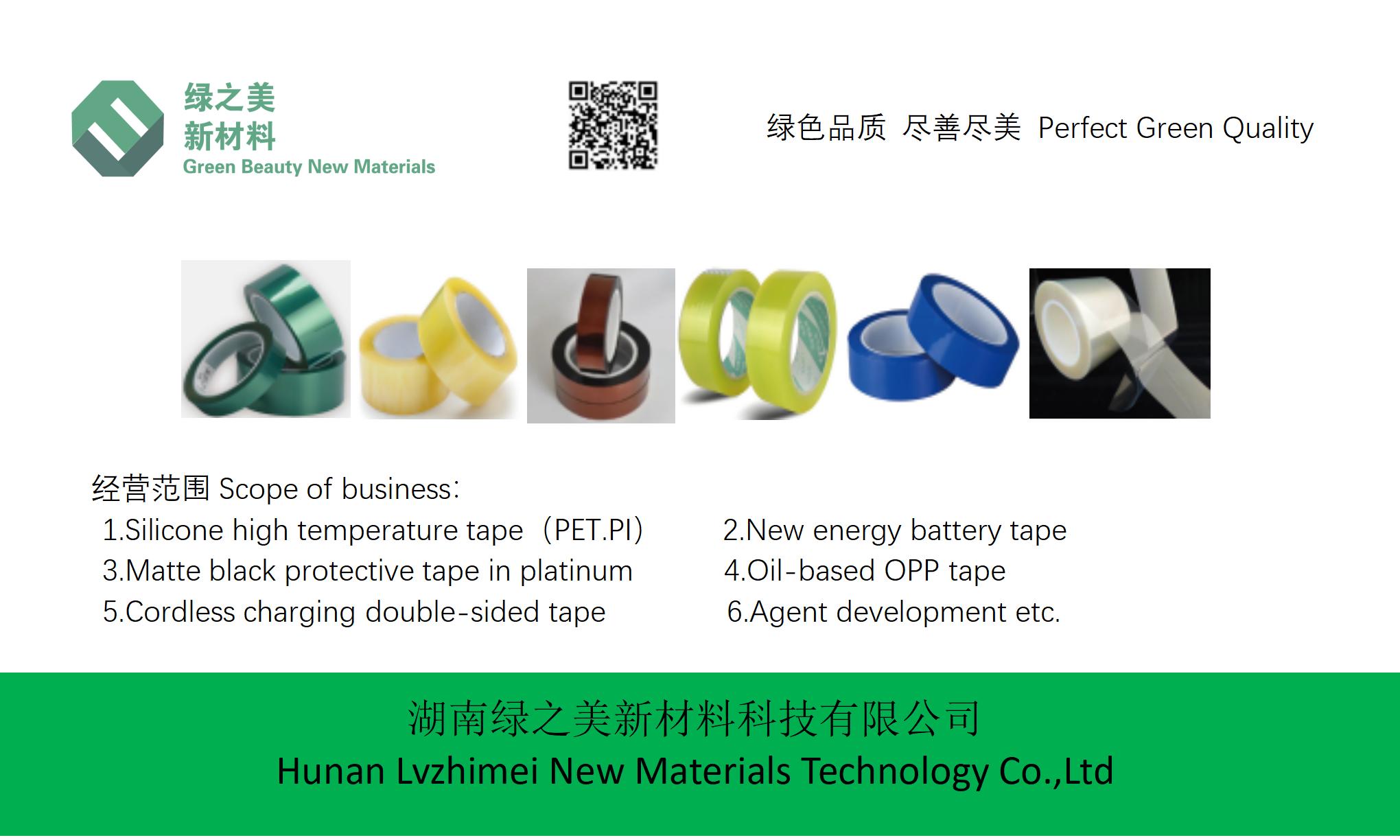