1. Gold Finger Contamination Issues in PCB Manufacturing1.1 Main Causes of Gold Finger ContaminationGold finger contamination is a common challenge in PCB manufacturing, particularly during the soldering process. The primary causes include:
● Tin Slag: During wave soldering, molten solder may generate tin slag, which easily adheres to unprotected gold finger surfaces.
● Flux Residue: Flux aids soldering by removing oxide layers but may corrode gold fingers if not thoroughly cleaned, leading to contamination.
● Environmental Impurities: Dust, oil, or other particles in the production environment can accumulate on exposed gold fingers.
● Equipment and Human Errors: Misaligned stencil printers or mishandling during transportation can cause direct contact with contaminants.
1.2 Impact on Yield Rate and Product PerformanceContamination significantly impacts PCB yield rates and product reliability. Reworking contaminated gold fingers requires manual cleaning, re-gilding, and additional quality checks, increasing labor costs and production cycles. Moreover, contaminated gold fingers degrade electrical performance by raising contact resistance, causing signal attenuation and interference, particularly in high-speed devices. Long-term reliability is also compromised as corrosion may gradually expand, shortening product lifespan and harming brand reputation.
2. Material Characteristics of Brown High Temperature Tape2.1 Key ComponentsBrown high-temperature tape consists of a phenolic resin backing and specialized pressure-sensitive adhesive (PSA).
● Phenolic Resin Backing: Derived from the condensation reaction of phenols (e.g., benzene) and aldehydes (e.g., formaldehyde), this thermosetting polymer offers exceptional heat resistance (≥200°C), chemical inertness, and mechanical strength.
● PSA Layer: Comprising rubber or acrylic polymers, tackifying resins, softeners, and fillers, the adhesive ensures strong adhesion at room temperature while maintaining flexibility and resistance to thermal degradation.
2.2 Performance in High-Temperature EnvironmentsThe tape's performance under extreme heat is critical. Phenolic resin withstands prolonged exposure to >200°C without deformation or decomposition, preventing thermal damage to underlying PCB layers. Meanwhile, the PSA exhibits unique behavior: while viscosity slightly decreases with temperature, its formulation ensures adequate adhesion without slippage or delamination during soldering. This balance prevents masking failures while maintaining peelability post-process.
3. Role of Brown Tape in Reducing Gold Finger Rework Rates3.1 Mechanism to Prevent Tin InfiltrationThe tape acts as a multi-layer barrier:
1. Physical Seal: Phenolic resin’s dense structure blocks molten tin penetration.
2. Adhesive Seal: PSA creates an airtight bond, preventing tin ingress from edges.
3. Chemical Resistance: Both components resist solder flux, avoiding degradation-induced breaches.This triple protection ensures zero tin contamination during wave soldering.
3.2 Practical Effect Data and Case StudiesA large-scale PCB manufacturer reported a 45% reduction in gold finger rework rates after adopting brown tape, boosting yield from 80% to >95%. Previously, monthly rework costs exceeded 100,000;thisdecreasedto<20,000 with tape implementation. Another case study in a telecom PCB production line showed a 98% yield improvement, saving 30% in production time. These results highlight the tape’s efficacy in contamination prevention. 4. Comparison with Traditional Solder Masking Materials4.1 High-Temperature Resistance Comparison
Material | Max Temperature | Thermal Stability |
Brown Tape | ≥200°C | No deformation, no ash |
PET Film | 150°C | Warping at high temps |
Kapton Tape | 260°C | Expensive, complex application |
Traditional Paper | <100°C | Burn risk |
Brown tape balances cost and performance, outperforming PET and paper while offering a more accessible alternative to high-end materials like Kapton.
4.2 Operational Efficiency and Cost-Benefit Analysis
● Ease of Use: Die-cut tape designs align perfectly with gold finger patterns, eliminating manual trimming and reducing application errors.
● Cost Efficiency: Lower rework costs (e.g., 60% savings in labor and materials) offset slightly higher tape procurement costs, resulting in net savings.
● Waste Reduction: Precision cutting minimizes material leftovers.
5. Significance for PCB Manufacturers5.1 Production Efficiency ImprovementBy eliminating most gold finger rework, assembly lines run more smoothly, shortening cycle times. For example, a manufacturer achieved 25% throughput increase after tape integration, enabling faster client deliveries and competitive advantages.
5.2 Cost ReductionDirect savings include:
● Rework Avoidance: Eliminating re-cleaning, re-gilding, and quality re-inspections.
● Material Optimization: Reduced tape waste via precision dies.
● Energy Efficiency: Faster production reduces equipment operation time.An estimated 15–20% total cost reduction can be achieved with consistent tape usage.
6. ConclusionBrown circuit board high-temperature tape revolutionizes PCB yield rates through its synergistic material design. By preventing tin infiltration, simplifying application, and offering cost-effective performance, it addresses both technical and economic challenges in modern electronics manufacturing. As industries demand higher reliability and efficiency, this tape emerges as a pivotal tool for boosting yield rates and competitiveness.
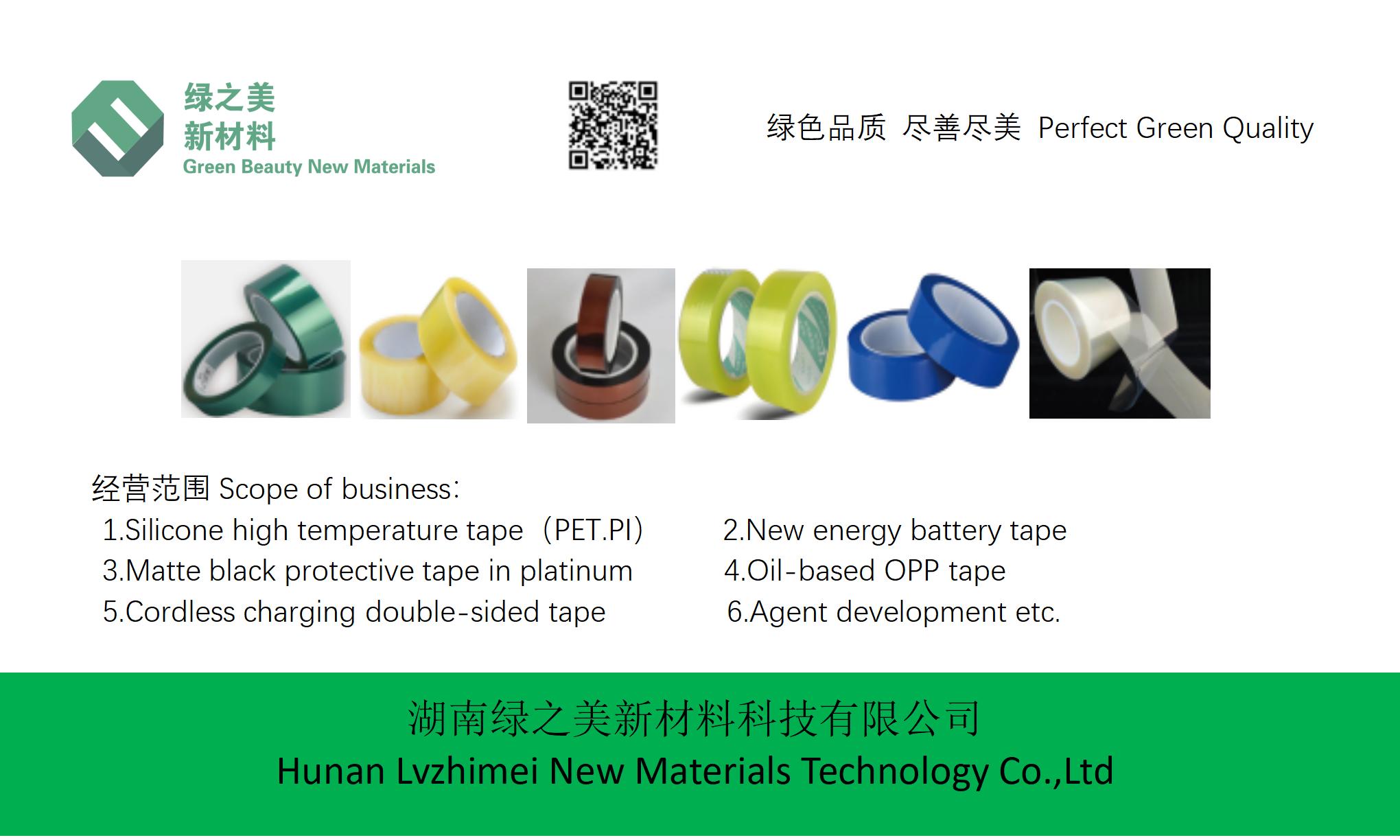