What Makes Strong Adhesion and Blocking High Temperature Tape Ideal for Aerospace Electronics?
Introduction
In the intricate and demanding field of aerospace electronics, the reliability and performance of materials used are of paramount importance. Among these materials, high-temperature tapes with strong adhesion and blocking properties stand out as essential components. This article delves into the unique requirements of aerospace-grade tapes, focusing on their critical attributes such as vibration resistance and outgassing control. By exploring the characteristics of these tapes, we aim to understand why they are indispensable in the aerospace industry, particularly in applications like avionics and satellite component protection.
Importance of High Temperature Tapes in Aerospace
Aerospace electronics operate in extreme environments, subject to intense heat, radiation, and mechanical stresses. Traditional materials often fail to meet the stringent requirements of these applications, necessitating the use of specialized materials like polyimide tapes. These tapes, specifically designed to withstand high temperatures, provide a reliable solution for protecting sensitive electronic components. The ability to endure temperatures ranging from engine heat to the harsh conditions of orbital vacuum makes them ideal for aerospace applications.
Key Characteristics of Ideal Aerospace Tapes
○ Definition and Importance: Adhesion is the tape's ability to bond securely to surfaces. In aerospace electronics, strong adhesion ensures that the tape remains in place under varying conditions, preventing displacement and maintaining the integrity of electronic components.
○ Application in Avionics: Avionics systems, which control and monitor aircraft operations, require tapes that can adhere firmly to different substrates, including metals and composites. This ensures consistent performance and reliability during flight.
2. High Temperature Resistance
○ Definition and Importance: High-temperature resistance enables the tape to function effectively in environments with extreme heat. Aerospace applications often involve exposure to temperatures well beyond the capabilities of standard materials.
○ Application in Engine Heat and Orbital Vacuum: Tapes used in aerospace must withstand the intense heat generated by aircraft engines and the vacuum of space. Materials like Kapton polyimide tape are specifically engineered to maintain their properties under these conditions, ensuring long-term durability and performance.
○ Definition and Importance: Vibration resistance is crucial in aerospace applications where mechanical stresses are constant. Tapes that can resist vibration help prevent component failure and ensure stable performance.
○ Application in Aerospace Electronics: Electronic components in aerospace systems are subjected to continuous vibration during flight. Tapes with high vibration resistance provide a stable and secure bond, minimizing the risk of component detachment or malfunction.
○ Definition and Importance: Outgassing is the release of volatile compounds from materials in a vacuum environment. In aerospace, outgassing can lead to contamination and performance degradation of sensitive equipment.
○ Application in Spacecraft: Spacecraft and satellite components must be protected from outgassing, as it can affect the operation of optical instruments and other critical systems. Tapes with near-zero outgassing, such as those approved by NASA, ensure that electronic components remain uncontaminated and functional.
LVMEIKAPTON’s Aerospace-Grade Polyimide Tape
LVMEIKAPTON’s aerospace-qualified gold finger electronics polyimide tape, known as Kapton, exemplifies the ideal characteristics required for aerospace electronics. This tape is designed to meet the stringent demands of the aerospace industry, offering exceptional performance in critical applications.
○ NASA Approval: Kapton tape has been approved by NASA for its near-zero outgassing properties, making it suitable for use in space applications where contamination control is essential.
○ Benefit for Aerospace: By minimizing outgassing, Kapton tape ensures that sensitive electronic components remain free from harmful contaminants, enhancing the reliability and longevity of aerospace systems.
2. Adhesion Under Intense G-Forces
○ Performance in Extreme Conditions: Kapton tape maintains its adhesive properties even under intense G-forces, ensuring that it remains securely bonded to components during high-stress situations.
○ Benefit for Avionics: In avionics systems, where G-forces can be significant, Kapton tape provides a reliable and durable solution, preventing component failure and ensuring consistent performance.
3. Masking During Thermal Spray Processes
○ Self-Adhesive Back Blocking Spray Paint Tape Design: Kapton tape features a self-adhesive back that effectively blocks spray paint during thermal spray processes. This design ensures precise masking, protecting critical components from unnecessary exposure.
○ Benefit for Satellite Components: During the manufacturing and maintenance of satellite components, Kapton tape provides a reliable masking solution, ensuring that only designated areas are treated, maintaining the integrity and functionality of the components.
Applications of High Temperature Tape in Aerospace Electronics
○ Component Protection: High-temperature tapes are used to protect electronic components in avionics systems from heat, vibration, and environmental stresses. This ensures that the systems remain functional and reliable throughout the aircraft's operational life.
○ Cable Management: Tapes are also used for cable bundling and management, providing a neat and secure arrangement that reduces the risk of cable damage and interference.
○ Thermal Protection: In space, satellites are exposed to extreme temperature fluctuations. High-temperature tapes provide thermal insulation, protecting components from overheating or thermal shock.
○ Masking During Manufacturing: During the manufacturing process, tapes are used to mask sensitive areas, ensuring that only designated parts are treated with coatings or other processes. This precise masking helps maintain the performance and longevity of satellite components.
3. Rocket and Engine Applications
○ Insulation and Protection: High-temperature tapes are used in rocket and engine systems to provide insulation against intense heat and mechanical stresses. This ensures that critical components function correctly, even under the most demanding conditions.
○ Vibration Damping: Tapes with vibration resistance properties are employed to dampen mechanical vibrations, reducing the risk of component failure and ensuring stable performance.
Comparison of Different Types of High Temperature Tapes
To better understand the advantages of Kapton tape, we can compare it with other high-temperature tape materials commonly used in aerospace electronics.
Tape Material | Temperature Range | Adhesion | Outgassing | Vibration Resistance |
Kapton Polyimide | -269°C to 400°C | High | Near-Zero | Excellent |
Silicon Tape | -70°C to 260°C | Moderate | Low | Good |
PTFE Tape | -200°C to 260°C | Low | Minimal | Fair |
Aluminum Foil Tape | -70°C to 150°C | High | Moderate | Poor |
From the comparison, it is evident that Kapton polyimide tape offers superior performance in terms of temperature resistance, adhesion, outgassing control, and vibration resistance, making it the preferred choice for aerospace applications.
Challenges and Considerations in Selecting Aerospace Tapes
1. Material Compatibility
○ Substrate Variability: Aerospace components are made from a variety of materials, including metals, composites, and ceramics. Selecting a tape that is compatible with these substrates is essential to ensure proper adhesion and performance.
○ Environmental Factors: Tapes must be chosen based on the specific environmental conditions they will be exposed to, such as temperature ranges, humidity, and radiation.
2. Regulatory and Certification Requirements
○ NASA and FAA Standards: Aerospace materials must meet stringent regulatory and certification requirements set by organizations like NASA and the Federal Aviation Administration (FAA). Ensuring that the tape used complies with these standards is crucial for safety and reliability.
○ Testing and Validation: Tapes must undergo rigorous testing and validation to ensure they meet the required performance criteria. This includes tests for adhesion, temperature resistance, outgassing, and vibration resistance.
○ Balancing Performance and Cost: While high-performance tapes like Kapton offer exceptional properties, they can be more expensive than other materials. Balancing performance requirements with budget constraints is an important consideration in tape selection.
○ Supply Chain Reliability: Ensuring a reliable supply chain for aerospace-grade tapes is critical, as delays or shortages can impact project timelines and mission success.
Future Trends and Innovations in Aerospace Tape Technology
1. Advancements in Material Science
○ New Polyimide Formulations: Ongoing research in material science is leading to the development of new polyimide formulations with improved properties, such as enhanced thermal stability and lower outgassing rates.
○ Nanostructured Materials: The incorporation of nanostructured materials into tape designs is expected to enhance performance characteristics, providing better protection and durability.
2. Smart Tapes with Integrated Sensing
○ Embedded Sensors: Future aerospace tapes may incorporate embedded sensors that monitor temperature, vibration, and other environmental factors in real-time. This would provide valuable data for predictive maintenance and performance optimization.
○ Self-Healing Properties: Research into self-healing materials could lead to tapes that automatically repair minor damages, extending their operational life and reducing maintenance requirements.
3. Sustainability and Environmental Considerations
○ Eco-Friendly Materials: As sustainability becomes increasingly important, the development of eco-friendly tape materials that meet aerospace performance standards is a growing trend.
○ Recyclability: Innovations in tape design may focus on improving recyclability, reducing the environmental impact of aerospace materials over their lifecycle.
Conclusion
In the aerospace electronics industry, the use of strong adhesion and blocking high-temperature tapes is essential for ensuring the reliability and performance of critical components. Materials like LVMEIKAPTON’s aerospace-qualified Kapton tape, with their exceptional properties of near-zero outgassing, high-temperature resistance, and vibration resistance, provide the necessary protection and durability required in extreme environments. As the aerospace industry continues to advance, innovations in tape technology will play a crucial role in meeting the evolving needs of avionics, satellites, and other aerospace systems. By understanding the key characteristics and applications of these tapes, engineers and designers can make informed decisions that enhance the safety, efficiency, and longevity of aerospace electronics.
References
● LVMEIKAPTON官方网站: https://www.lvmeikapton.com/
● NASA Outgassing Specifications and Testing Methods
● Federal Aviation Administration (FAA) Material Standards
● Polyimide Tape Performance Data from Industry Studies
● Advancements in Aerospace Material Science Journals
Appendix: Technical Specifications of Kapton Tape
● Temperature Range: -269°C to 400°C
● Outgassing Rate: <0.1% Total Mass Loss (TML)
● Vibration Resistance: Tested up to 10G
● Certifications: NASA, FAA, RoHS
Acknowledgments
The author would like to acknowledge the contributions of industry experts and the valuable resources provided by LVMEIKAPTON in the preparation of this article. Special thanks to the aerospace engineering community for their continuous advancements in materials science, which have significantly impacted the reliability and performance of aerospace electronics.
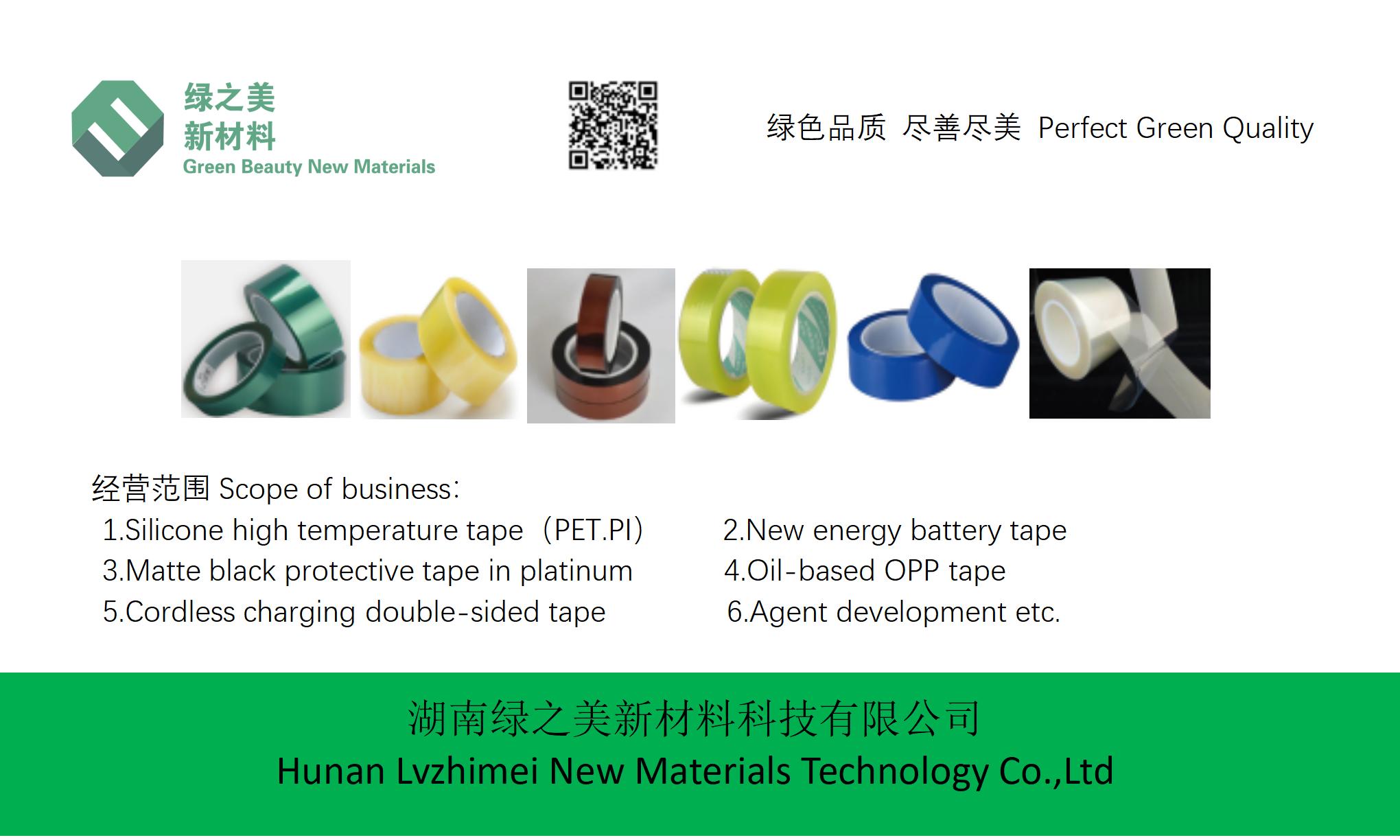