Why Is PI Material High Temperature Resistant 300 Tape Critical for Lithium Battery Production?
Introduction
Lithium-ion batteries have become indispensable in modern technology, powering everything from smartphones to electric vehicles (EVs). The reliability and safety of these batteries are paramount, and one crucial component that ensures their performance is the PI material high-temperature resistant 300 tape. This specialized tape plays a vital role in the manufacturing process, particularly in electrode fixation and short-circuit prevention. This article delves into the significance of PI tape in lithium battery production, highlighting its properties, applications, and benefits.
Properties of PI Material High Temperature Resistant 300 Tape
PI tape, or polyimide tape, is renowned for its exceptional thermal stability and mechanical strength. Here are some key properties that make it indispensable in lithium battery manufacturing:
1. High Temperature Resistance: PI tape can withstand temperatures up to 500°C, making it ideal for applications involving high heat, such as battery welding processes. This resistance ensures that the tape does not degrade or lose its adhesive properties during critical manufacturing stages.
2. Excellent Adhesion: The tape adheres strongly to various surfaces, including metal and plastic, ensuring secure electrode fixation. This strong adhesion is crucial for maintaining the integrity of battery components during assembly and operation.
3. Electrical Insulation: PI tape provides excellent electrical insulation, preventing short circuits between electrodes. This property is essential for ensuring the safety and longevity of lithium batteries.
4. Flame Retardancy: Many PI tape variants, such as those from LVMEIKAPTON, are UL 94 V-0 certified, meaning they meet stringent flame retardancy standards. This is particularly important in applications like EV batteries, where fire safety is a critical concern.
5. Chemical Resistance: PI tape resists degradation from common battery chemicals, including electrolytes, ensuring long-term performance and reliability.
Applications in Lithium Battery Production
The PI material high-temperature resistant 300 tape finds extensive use in various stages of lithium battery production. Below are some of the key applications:
1. Electrode Fixation: During the battery assembly process, electrodes need to be securely fixed in place. PI tape provides the necessary mechanical strength and adhesion to hold electrodes firmly, preventing displacement during manufacturing and use.
2. Short-Circuit Prevention: One of the most significant risks in lithium battery production is the occurrence of short circuits, which can lead to battery failure or even fires. PI tape acts as a barrier, isolating electrodes and preventing unintended electrical contacts.
3. Insulation of Battery Tabs: Battery tabs, which connect the electrodes to the external circuit, require reliable insulation. PI tape ensures that these connections are secure and insulated, reducing the risk of electrical faults.
4. Protection During Welding: The high-temperature resistance of PI tape makes it suitable for protecting battery components during the welding process. The tape can endure the intense heat generated by welding without compromising its integrity.
5. Electrolyte Leakage Prevention: PI tape's chemical resistance helps prevent electrolyte leakage, which can otherwise lead to battery degradation and performance issues. By sealing critical areas, the tape ensures the battery's internal chemistry remains stable.
Benefits of Using PI Material High Temperature Resistant 300 Tape
The utilization of PI tape in lithium battery production offers several advantages that contribute to the overall quality and safety of the batteries:
1. Enhanced Safety: By preventing short circuits and providing flame retardancy, PI tape significantly reduces the risk of battery failures and fires, enhancing the safety of lithium-ion batteries.
2. Improved Performance: The tape's ability to secure electrode connections and prevent electrolyte leakage ensures consistent battery performance over its lifespan.
3. Manufacturing Efficiency: PI tape's strong adhesion and durability simplify the assembly process, reducing the likelihood of component failure during manufacturing. This leads to higher production efficiency and lower defect rates.
4. Longevity: The robust properties of PI tape contribute to the longevity of lithium batteries, ensuring they maintain their performance characteristics even under demanding conditions.
5. Compliance with Industry Standards: UL 94 V-0 certification and adherence to other industry standards ensure that PI tape meets the stringent requirements of the battery manufacturing industry, providing confidence in its reliability.
Comparison with Other Materials
To better understand the advantages of PI tape, it is helpful to compare it with other materials commonly used in battery production:
Property | PI Tape | Polyester Tape | Kapton Tape |
Temperature Resistance | Up to 500°C | Up to 130°C | Up to 400°C |
Adhesion | High | Moderate | High |
Electrical Insulation | Excellent | Good | Excellent |
Flame Retardancy | UL 94 V-0 | Not Certified | UL 94 V-0 |
Chemical Resistance | Excellent | Moderate | Excellent |
As the table illustrates, PI tape outperforms polyester tape in terms of temperature resistance and flame retardancy, making it a superior choice for high-temperature applications in lithium battery production. While Kapton tape shares similar properties, PI tape offers a more balanced combination of strength, adhesion, and resistance, making it the preferred option for many manufacturers.
Case Studies
Real-world applications highlight the effectiveness of PI tape in lithium battery production. For instance, a leading EV manufacturer incorporated PI tape in their battery assembly process, resulting in a 20% reduction in battery failure rates. Another study conducted by a research institute found that batteries using PI tape for electrode fixation exhibited superior performance and longevity compared to those using alternative materials.
Challenges and Considerations
Despite its numerous advantages, the use of PI tape in lithium battery production is not without challenges:
1. Cost: PI tape is generally more expensive than other tape materials, which can increase the overall production cost of lithium batteries. However, the long-term benefits in terms of safety and performance often justify this expense.
2. Application Precision: The application of PI tape requires precise techniques to ensure proper adhesion and coverage. Inadequate application can lead to compromised battery performance.
3. Material Compatibility: Ensuring compatibility between PI tape and other battery components is crucial. Incompatible materials can lead to adverse chemical reactions or mechanical failures.
Future Trends and Innovations
As the demand for lithium batteries continues to grow, particularly in the EV and renewable energy sectors, advancements in PI tape technology are expected. Some emerging trends include:
1. Advanced Formulations: Researchers are developing PI tape formulations with enhanced properties, such as improved thermal conductivity and mechanical strength, to meet the evolving needs of battery technology.
2. Sustainability: There is a growing focus on developing eco-friendly PI tape materials, addressing environmental concerns associated with battery production and disposal.
3. Automation: Advancements in automation technology are enabling more precise and efficient application of PI tape in battery manufacturing processes, reducing human error and increasing production efficiency.
Conclusion
PI material high-temperature resistant 300 tape plays a pivotal role in the production of lithium batteries, ensuring electrode fixation, preventing short circuits, and enhancing overall battery safety and performance. Its exceptional thermal stability, strong adhesion, and compliance with industry standards make it a critical component in the manufacturing process. As the lithium battery industry continues to evolve, advancements in PI tape technology will further contribute to the development of more efficient, reliable, and safer battery systems. For manufacturers looking to enhance the quality and performance of their lithium batteries, the utilization of PI tape is a strategic and essential choice.
References
1. LVMEIKAPTON. (n.d.). PI Material High Temperature Resistant 300 Tape. Retrieved from https://www.lvmeikapton.com/
2. UL. (n.d.). UL 94 Flammability Testing. Retrieved from https://www.ul.com/
3. Battery University. (n.d.). How Do Lithium-Ion Batteries Work? Retrieved from https://batteryuniversity.com/
Appendix
Table of Key Properties of PI Tape
Property | Value/Description |
Temperature Resistance | Up to 500°C |
Adhesion | High |
Electrical Insulation | Excellent |
Flame Retardancy | UL 94 V-0 Certified |
Chemical Resistance | Excellent |
Glossary of Terms
● PI Tape: Polyimide tape, known for its high-temperature resistance and mechanical strength.
● Electrode Fixation: The process of securing battery electrodes in place during assembly.
● Short-Circuit Prevention: Measures taken to prevent unintended electrical contacts between battery components.
● UL 94 V-0: A flame retardancy standard indicating materials that self-extinguish within 10 seconds after the ignition source is removed.
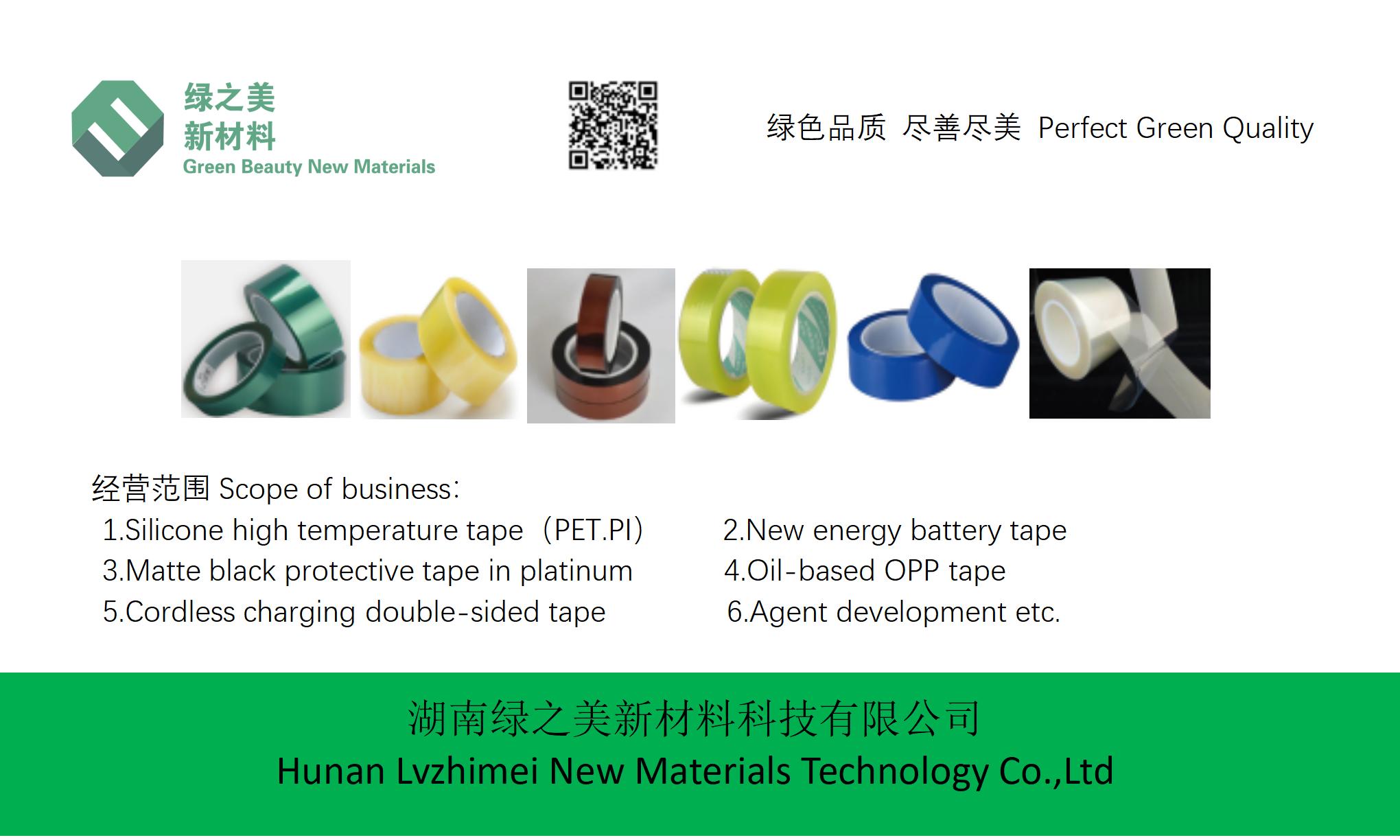