When to Specify PET Tape for Medical Devices?
Introduction
In the field of medical device manufacturing, the choice of materials plays a crucial role in ensuring the safety, efficacy, and durability of the final product. PET (Polyethylene Terephthalate) tape, particularly high-temperature resistant variants, has emerged as a preferred choice for various medical applications. This article delves into the specific scenarios where PET tape should be specified for medical devices, highlighting its key properties and compliance with international standards such as ISO 10993.
Properties of PET Tape
PET tape is renowned for its exceptional mechanical strength, chemical resistance, and thermal stability. These properties make it suitable for a wide range of medical device applications. The following table summarizes the key characteristics of PET tape:
Property | Description |
Temperature Resistance | Withstands temperatures up to 100°C, making it ideal for autoclaving processes. |
Chemical Resistance | Resistant to a variety of chemicals, including disinfectants and sterilizing agents. |
Mechanical Strength | High tensile strength and durability, ensuring reliable performance over time. |
Adhesion | Provides strong and consistent adhesion to different surfaces. |
Compliance | Meets ISO 10993 biocompatibility standards, ensuring safety for medical use. |
Applications in Medical Devices
PET tape finds extensive use in medical devices due to its unique combination of properties. The following sections outline specific scenarios where specifying PET tape is essential.
Sterilization Processes
One of the most critical aspects of medical device manufacturing is ensuring that the devices are sterile. PET tape's ability to withstand high temperatures makes it suitable for use in autoclave cycles. According to ISO 10993, medical devices must be biocompatible and able to withstand sterilization processes without degradation. PET tape, with its resistance to 100 autoclave cycles, meets these stringent requirements. This ensures that the tape remains intact and functional throughout the sterilization process, maintaining the integrity of the medical device.
Device Assembly and Packaging
In the assembly of medical devices, PET tape is often used for securing components and ensuring airtight seals. Its strong adhesive properties provide a reliable bond, preventing the disassembly of components during handling and transportation. Additionally, PET tape's resistance to chemicals ensures that it does not degrade when exposed to common cleaning and disinfecting agents used in medical settings. This makes it an ideal choice for packaging medical devices, ensuring that they remain sterile and functional until use.
Labeling and Identification
PET tape is also widely used for labeling medical devices. Its durability and resistance to environmental factors such as moisture and UV light ensure that labels remain legible and intact throughout the device's lifecycle. This is particularly important in hospitals and clinics where clear identification of devices is crucial for patient safety and regulatory compliance. The tape's adherence to ISO 10993 standards further ensures that it does not pose any risks to patients or healthcare providers.
Wound Dressings and Bandages
In wound care applications, PET tape's biocompatibility and hypoallergenic properties make it suitable for use in wound dressings and bandages. The tape's ability to maintain its adhesive properties even in the presence of moisture ensures that dressings remain securely in place, promoting faster healing and reducing the risk of infection. Additionally, PET tape's transparency allows for visual monitoring of the wound without the need for frequent dressing changes, minimizing patient discomfort.
Selection Criteria for PET Tape
When specifying PET tape for medical devices, several factors should be considered to ensure the optimal choice. The following criteria can guide the selection process:
1. Temperature Requirements: Determine the maximum temperature the tape will be exposed to during sterilization and operational use. Ensure that the selected PET tape can withstand these temperatures without degradation.
2. Chemical Exposure: Identify the types of chemicals the tape will be exposed to during cleaning and disinfection processes. Choose a PET tape with appropriate chemical resistance to maintain its integrity.
3. Adhesion Strength: Assess the surface materials the tape will be applied to and select a tape with the appropriate adhesive strength to ensure a secure bond.
4. Biocompatibility: Verify that the PET tape meets relevant biocompatibility standards such as ISO 10993 to ensure patient safety.
5. Environmental Resistance: Consider the environmental conditions the tape will be exposed to, including moisture, UV light, and mechanical stress. Choose a tape with the necessary resistance properties to ensure long-term performance.
Compliance and Regulatory Considerations
The medical industry is subject to stringent regulatory requirements to ensure the safety and efficacy of medical devices. PET tape used in medical applications must comply with various international standards, including ISO 10993 for biocompatibility. Additionally, the tape should meet other relevant standards such as ISO 11607 for packaging of terminally sterilized medical devices. Compliance with these standards not only ensures the safety of the tape but also facilitates regulatory approval and market entry for medical devices.
Case Studies
To illustrate the effectiveness of PET tape in medical device applications, the following case studies provide real-world examples:
Case Study 1: Autoclavable Surgical Instruments
A leading manufacturer of surgical instruments specified PET tape for the assembly and packaging of their products. The tape's ability to withstand 100 autoclave cycles ensured that the instruments remained sterile and functional throughout their shelf life. This significantly reduced the risk of post-operative infections and improved patient outcomes.
Case Study 2: Wound Dressings
A wound care company developed a new line of dressings using PET tape as the adhesive layer. The tape's biocompatibility and moisture resistance allowed for extended wear times, reducing the frequency of dressing changes and promoting faster wound healing. Patient feedback was overwhelmingly positive, with reports of improved comfort and reduced pain.
Future Trends and Innovations
As the medical industry continues to evolve, the demand for advanced materials like PET tape is expected to grow. Ongoing research and development are focusing on enhancing the properties of PET tape to meet emerging needs in medical device manufacturing. Some of the key trends include:
● Enhanced Biocompatibility: Development of PET tapes with improved biocompatibility for use in more sensitive medical applications.
● Smart Materials: Integration of smart materials into PET tape to enable monitoring of wound healing and device performance.
● Sustainability: Focus on developing environmentally friendly PET tape options that meet sustainability criteria without compromising performance.
Conclusion
PET tape, with its exceptional properties and compliance with international standards, is a versatile and reliable choice for medical device applications. Whether used in sterilization processes, device assembly, labeling, or wound care, PET tape ensures the safety, efficacy, and durability of medical devices. By carefully considering the selection criteria and regulatory requirements, manufacturers can specify PET tape that meets the unique needs of their medical devices, ultimately improving patient outcomes and ensuring regulatory compliance.
References
● ISO 10993: Biological evaluation of medical devices
● ISO 11607: Packaging for terminally sterilized medical devices
● Lvmeikapton.com: Adhesive PET material high-temperature tape withstands 100°C autoclave cycles (ISO 10993 compliant)
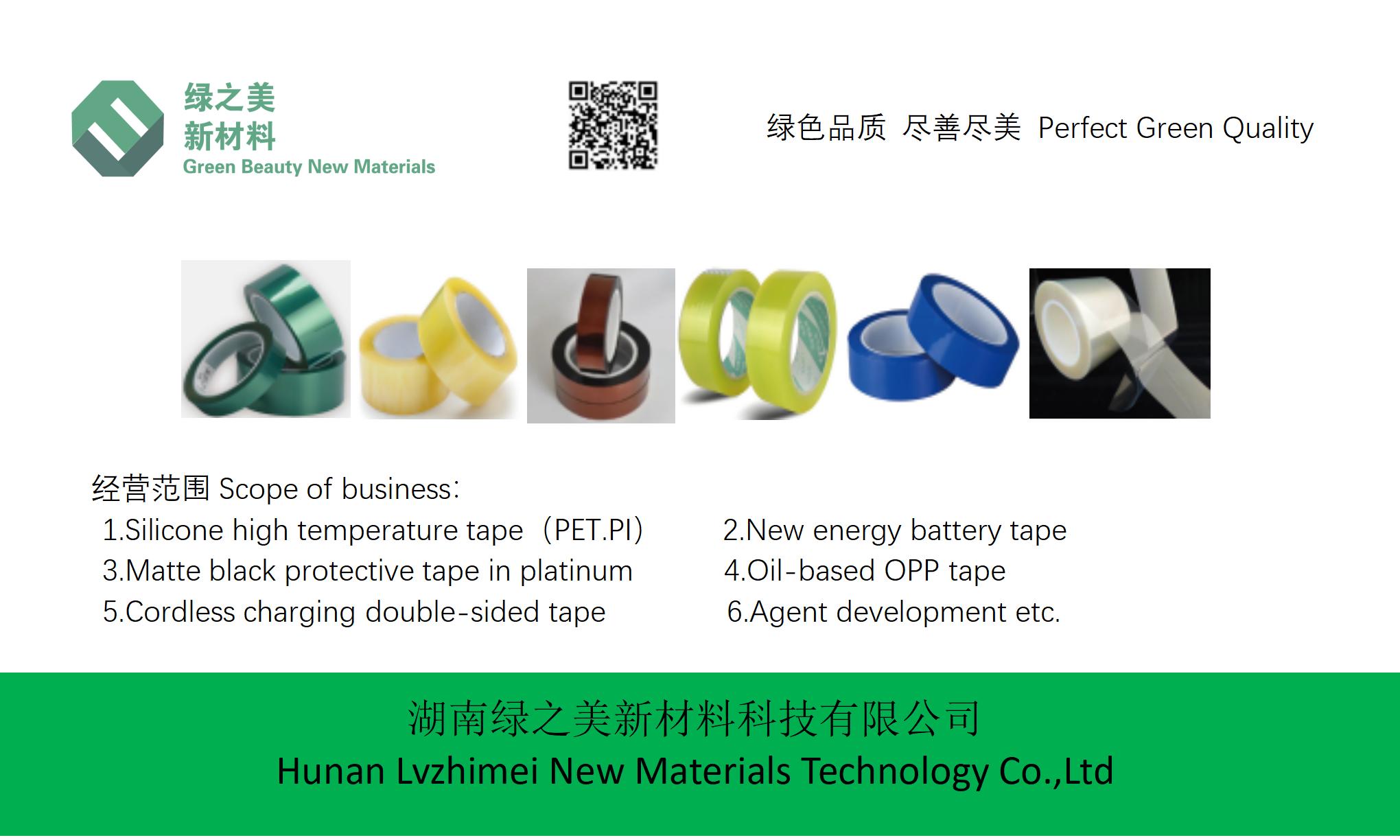