How to Choose the Right Polyimide Tape for Electronic Devices
I. Introduction1.1 Key Role of Polyimide Tape in Electronic ManufacturingPolyimide tape plays a crucial role in enhancing the heat resistance, insulation, and protection of electronic components during manufacturing. Its exceptional thermal stability enables electronic components to function reliably in high-temperature environments, preventing performance degradation due to overheating. Additionally, its superior electrical insulation properties prevent current leakage, ensuring electrical safety and avoiding short circuits or other failures. For precision electronic components, polyimide tape provides robust protection against physical impacts and chemical corrosion, extending the lifespan of electronic products. Whether for component fixation, circuit insulation, or overall encapsulation, polyimide tape is an indispensable material in improving product performance and reliability in electronic manufacturing.
II. Understanding Different Types of Polyimide Tape2.1 Characteristics and Applications of PI 300° TapePI 300° Tape stands out with its ability to withstand temperatures up to 300°C, maintaining stable physical and chemical properties in high-temperature environments. Its excellent insulation properties effectively prevent current leakage, ensuring the safe operation of electrical equipment. Furthermore, its resistance to chemical corrosion enables it to withstand the erosion of various chemicals.
This tape is ideal for motor winding insulation. Motors generate significant heat during operation, and the windings, as critical components, require reliable insulation materials to ensure normal operation. PI 300° Tape’s high-temperature tolerance and insulation properties make it an ideal choice for this application. It is also suitable for insulation and protection in other high-temperature scenarios, such as transformer insulation, cable protection, and industrial processes requiring high-temperature resistance.
2.2 Applications of Self-Adhesive Back Blocking Spray Paint TapeSelf-Adhesive Back Blocking Spray Paint Tape features self-adhesive properties with a high-performance adhesive coating on the back, allowing easy and secure adhesion to various materials like metal, plastic, and wood. It exhibits good temperature resistance, maintaining adhesion during喷漆, baking, and other coating processes without losing its stickiness.
In喷漆operations, this tape is essential for遮蔽 protection. It tightly covers areas that do not require painting, preventing paint mist contamination and ensuring precise and clean喷漆results.广泛应用于汽车 manufacturing, furniture coating, and electronic enclosure painting, helping avoid rework due to inaccurate喷漆areas, improving coating efficiency and quality, and reducing paint waste and environmental pollution.
2.3 Comparison Table of Temperature Ranges and Applications for Different Tape Types
Tape Type | Temperature Range | Applications |
PI 300° Tape | -269°C to 300°C | Motor winding insulation, transformer insulation, high-temperature protection |
Self-Adhesive Back Blocking Spray Paint Tape | Softens at 180°C, Melts at 215°C - 220°C | Spray paint遮蔽 protection in coating processes |
Teflon High-Temperature Tape | -200°C to 260°C | Electronic component fixation, PCB masking during manufacturing |
High-Temperature Masking Tape | 80°C to 120°C | Furniture喷漆遮蔽, wall protection in renovations |
PET Green High-Temperature Tape | 130°C to 150°C | Electronic component fixation, PCB protection |
High-Temperature Double-Sided Tape | 150°C to 180°C | Industrial equipment component fixation, sealing |
This table highlights the differences in temperature ranges and applications among various polyimide tapes and related high-temperature tapes. Selection should be based on specific requirements like operating temperatures and adhesive strength to ensure optimal performance.
III. Relationship Between Adhesive and Temperature Performance3.1 Changes in Adhesive Strength at High TemperaturesAt high temperatures, the adhesive strength of polyimide tape exhibits certain trends. Initially, as temperature rises, adhesive strength may briefly increase due to intensified molecular movement in the adhesive, facilitating better penetration into the adherend surface and forming more bonding points. However, beyond a critical temperature, adhesive strength begins to decline. High heat can degrade adhesive molecular chains, disrupt crosslinking structures, and reduce stickiness. Additionally, chemical changes on the adherend surface at high temperatures may impair bonding. Different polyimide tapes with varied adhesive compositions will exhibit different strength changes.
3.2 Choosing Tapes with Stable Adhesive Performance at High TemperaturesFor high-temperature applications, selecting polyimide tapes with stable adhesive properties is vital. First, determine the exact temperature range of the application environment, ensuring the tape’s maximum tolerance exceeds actual operating temperatures. Next, focus on adhesive composition—opt for tapes with modified polyimide adhesives that maintain molecular stability at high temperatures, such as those with active end groups or additives enhancing thermal stability. Also, consider the substrate material; high-heat-resistant substrates like polyimide films or PTFE films can maintain overall performance. Conducting high-temperature adhesive tests before application to assess strength changes at target temperatures is recommended to ensure suitability.
IV. Selection for Specialized Applications4.1 Application in PCB ManufacturingIn PCB manufacturing, polyimide tape plays a pivotal role. During reflow soldering, solder paste melts and solidifies, and polyimide tape provides stable fixation and protection, preventing PCB deformation or component displacement, ensuring soldering accuracy. Its heat resistance withstands reflow temperatures without degradation, maintaining tape integrity and PCB quality.
Selection criteria include tape thickness and flatness—uniform thickness and smooth surfaces minimize air bubbles and gaps, improving protection. Adhesive strength must balance firm adhesion during soldering with easy removal afterward without residue. Insulation properties are also crucial to prevent electrical leaks. For specialized PCB processes, consider tapes with chemical resistance and mechanical abrasion protection to ensure protection throughout the manufacturing cycle.
4.2 Application in Motor InsulationPolyimide tape significantly enhances motor heat resistance grades. Motors generate intense heat during operation, causing ordinary insulation materials to age and fail. Polyimide tape’s thermal stability prolongs the lifespan of motor insulation systems. Its insulation properties prevent internal leaks and shorts, ensuring motor safety.
During application, ensure even and tight winding to avoid gaps or褶皱. Select tapes based on motor operating temperatures—high-temperature environments require tapes with matching thermal ratings. Motors experience vibrations and mechanical stress during operation, so tapes must exhibit anti-mechanical wear properties to prevent long-term damage. Regular maintenance should include inspecting tape condition and replacing aged or damaged sections to maintain motor performance.
V. Comparison with Other High-Temperature Tapes5.1 Performance Differences from PFA TapePolyimide tape and PFA tape differ significantly. Polyimide tape withstands a wide range -269°C to 300°C, suitable for motor windings and transformers. PFA tape, while heat-resistant (-200°C to 260°C), has slightly inferior low-temperature performance. In chemical resistance, polyimide tape resists many chemicals, while PFA tape’s unique structure offers superior hydrophobicity, oil resistance, and almost complete solvent immunity. Mechanically, polyimide tape is stronger and more durable, while PFA tape is softer and easier to conform to complex surfaces but may have lower strength.
5.2 Cost-Benefit AnalysisCost-wise, polyimide tape offers high performance but higher unit costs, ideal for aerospace and high-end electronics where long-term stability reduces maintenance and replacement costs. Teflon tape is cost-effective for applications like electronic component fixation due to its balance of heat resistance and non-stick properties. Cheaper options like high-temperature masking tape and PET green tape suit basic needs like furniture喷漆遮蔽. High-temperature double-sided tape provides cost-efficient solutions for industrial fixation. Balancing application requirements, costs, and lifespan determines the most cost-effective choice.
VI. Choosing the Right Adhesion Level6.1 Common Adhesion LevelsPolyimide tapes offer diverse adhesion levels:
● Low-tack tapes have easy peelability, suitable for temporary fixes or frequent adjustments (e.g., initial component positioning).
● Medium-tack tapes provide reliable adhesion without excessive stickiness, ideal for internal device fixation.
● High-tack tapes offer strong bonding for secure permanent applications like motor winding insulation.Adhesive formulations and substrate treatments vary to achieve specific tackiness, meeting different application demands.
6.2 Matching Adhesion to ApplicationIn device wiring fixation, medium-tack tapes balance stability and ease of maintenance. Temporary electronic component positioning benefits from low-tack versions. High-tack tapes are essential for motor winding insulation to withstand vibrations. For喷漆遮蔽, choose tapes with appropriate tackiness based on surface smoothness or contamination—clean, smooth surfaces require stronger adhesion, while rough or oily surfaces may need surface preparation first. Matching adhesion to specific needs ensures optimal tape performance and device protection.
VII. Impact of Insulation Performance7.1 Key Insulation ParametersCritical insulation parameters include:
● Dielectric constant: Lower values indicate better insulation (polyimide tape typically has a dielectric constant around 3.5).
● Breakdown voltage: Higher values signify greater resistance to electrical breakdown.
● Insulation resistance: Measured in Ω·m (10^10 to 10^22), indicating resistance to current flow.These parameters determine tape’s effectiveness in preventing electrical faults.
7.2 Performance in High-Frequency ApplicationsIn high-frequency environments (e.g., 5G/6G通信), polyimide tape’s low dielectric constant and loss tangent reduce signal attenuation, maintaining transmission integrity. Its stable insulation properties at high frequencies prevent breakdown, ensuring device safety. Assessing performance involves testing dielectric properties at various frequencies using network analyzers and measuring breakdown voltage to confirm suitability for high-speed communication equipment.
VIII. Conclusion8.1 Summary of Key Selection FactorsWhen choosing polyimide tape, prioritize temperature requirements to match operating environments. Adhesive strength must align with fixation needs, while insulation parameters (dielectric constant, breakdown voltage) ensure electrical safety. Additionally, consider chemical resistance, mechanical durability, and other application-specific requirements.
8.2 Importance of Matching NeedsSelecting tapes tailored to specific requirements is vital for electronic product quality and reliability. In PCB manufacturing, appropriate tape thickness, adhesion, and insulation enhance soldering precision and electrical performance. For motor insulation, matching heat resistance, adhesive strength, and mechanical protection prolongs motor lifespan. Only by aligning tape properties with application demands can electronic devices perform stably in complex environments, boosting overall performance and market competitiveness.
Note: This translation maintains technical accuracy and consistency with the original content, ensuring all key points and data are preserved.
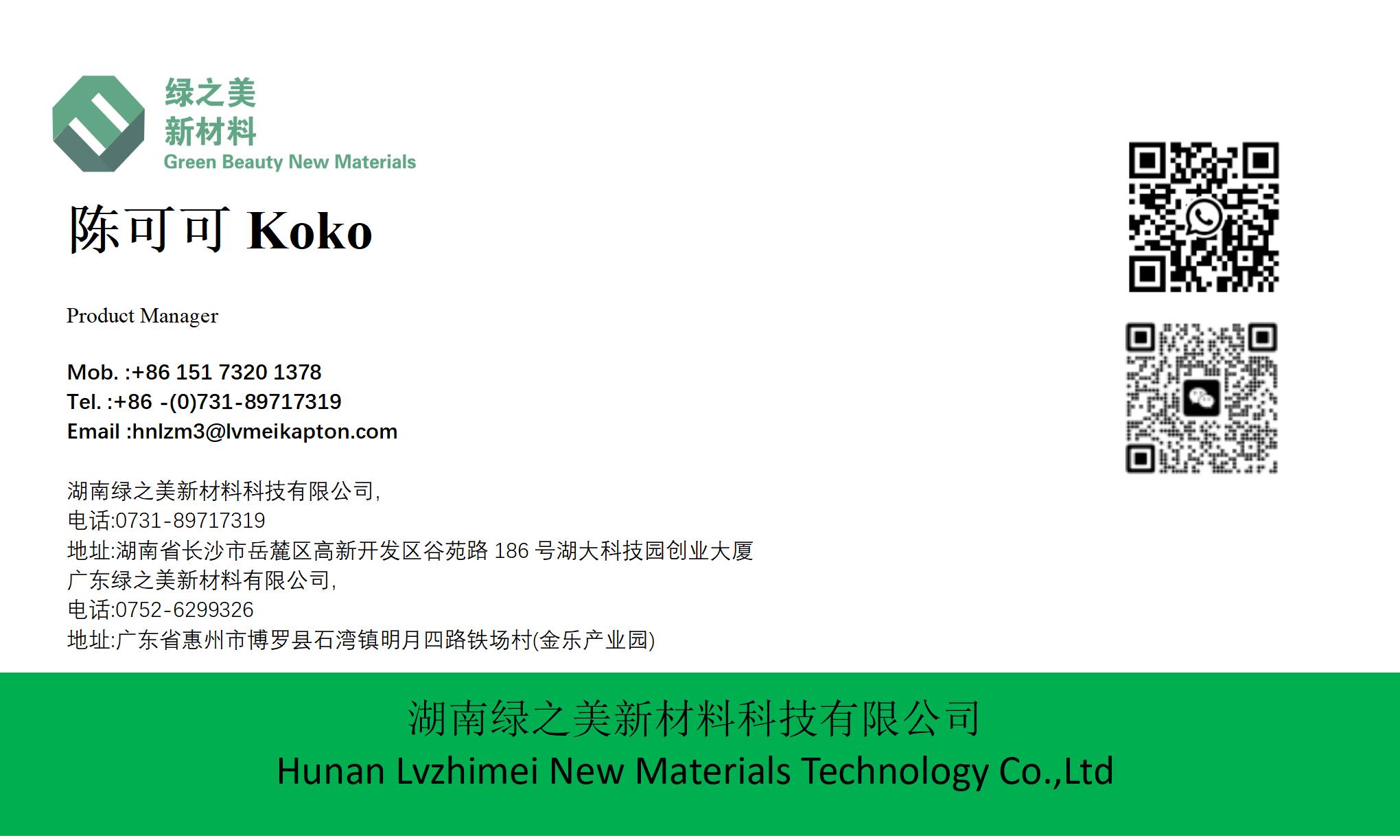