Why Polyimide Tape is Crucial for Circuit Board Durability
I. Introduction1.1 Challenges of Electronic Device Operating EnvironmentsElectronic devices often face complex and harsh operating environments. High temperatures are common in industrial production, aerospace, and other fields, causing material aging, component performance degradation, and even thermal breakdown. Chemical corrosion in chemical, marine, and other environments poses significant threats to metal traces and components on circuit boards, leading to open circuits and shorts. Mechanical stress from vibration and shock can damage internal structures, causing solder joints to crack and components to loosen. These challenges demand improved circuit board durability to ensure reliability in extreme conditions.
II. Characteristics of Polyimide Tape2.1 Physical PropertiesPolyimide tape excels in high-temperature resistance and mechanical strength. For example, PI Material High Temperature Resistant 300 Tape withstands up to 300°C, preventing material degradation in high-temperature zones. Its tensile strength and abrasion resistance protect against mechanical stress, preventing solder joint cracking and component displacement. Products like Lvmeikapton Insulating Electrical Tape combine heat insulation and electrical insulation to safeguard against thermal and electrical failures.
2.2 Chemical PropertiesPolyimide tape exhibits exceptional chemical stability, resisting most acids, alkalis, and organic solvents. This protection is crucial in corrosive environments, preventing metal trace erosion and maintaining circuit integrity. Its low ionization property in semiconductor manufacturing reduces contamination risks, ensuring product quality. Chemical resistance enhances long-term reliability in harsh industrial and marine applications.
III. Impact of High Temperatures on Circuit Boards3.1 Material AgingHigh temperatures accelerate degradation of board materials (e.g., epoxy substrates, copper foils). Molecular chain breakage or crosslinking leads to softening, embrittlement, delamination, and oxidation of copper, impairing electrical conductivity and mechanical stability. Surface coatings like solder masks may discolor, bubble, or peel, compromising protection.
3.2 Solder Joint and Component DamageSolder joints, critical for component connections, are vulnerable to thermal stress. Temperature cycling causes differential expansion between materials, leading to fatigue cracks. Components like semiconductors suffer parameter drift (e.g., reduced gain, lowered breakdown voltage), while capacitors and inductors degrade in capacity and efficiency. Prolonged exposure shortens component lifespan and increases failure rates.
3.3 Electrical Performance DegradationTemperature fluctuations alter contact resistance, insulation resistance, and component parameters. Elevated temperatures increase conductor resistivity and accelerate oxidation at connectors, impairing signal integrity. Reduced insulation resistance raises short circuit risks, especially in humid environments. Fluctuating capacitance and inductance disrupt circuit frequency response, compromising device functionality.
IV. Role of Polyimide Tape in Thermal Management4.1 Heat Conduction BarrierPolyimide tape acts as a thermal barrier using its low thermal conductivity. For example, when applied around heat-generating components (e.g., processors), it prevents heat diffusion to nearby circuits, reducing local overheating and material aging. This mitigates thermal stress on sensitive areas and eases cooling system demands, enhancing overall thermal stability.
4.2 Protection Against Solder Joint Melting and DeformationIn high-temperature zones, polyimide tape shields solder joints from thermal stress. By absorbing and dissipating heat, it lowers joint temperatures and prevents melting or deformation. This is critical in industrial control devices and automotive electronics exposed to continuous heat, ensuring connection reliability and extending device lifespan.
4.3 Enhancing Thermal StabilityPolyimide tape stabilizes circuit board performance under thermal cycling. Its thermal shock resistance maintains material properties across wide temperature ranges, preventing sudden failures during rapid temperature changes. This is vital in aerospace and military equipment subjected to extreme environments, ensuring consistent electrical and mechanical performance.
V. Adhesion and Mechanical Protection5.1 Preventing Component LooseningPolyimide tape’s strong adhesion secures components against vibration and shock. In automotive or industrial equipment, continuous vibrations can loosen components, causing intermittent faults. The tape firmly bonds components to the board, maintaining electrical connections even under dynamic stresses. For example, in vehicle electronics, it ensures stability during bumpy rides, reducing failure risks.
5.2 Physical Damage PreventionAs a protective layer, polyimide tape resists abrasion and impact. During transportation or assembly, it shields circuits from scratches and collisions, preserving trace integrity. Its wear-resistant layer absorbs mechanical forces, preventing internal structure damage and extending board lifespan.
5.3 Ensuring Multilayer AlignmentIn multilayer boards, polyimide tape facilitates precise layer bonding. Its consistent adhesive strength ensures layers adhere firmly without delamination during fabrication or thermal cycling. This maintains uniform spacing and improves signal transmission, crucial for high-speed digital circuits and RF applications.
VI. Material Innovations and Applications6.1 Composite TapesCombining PET’s flexibility with polyimide’s heat resistance creates versatile solutions. Adhesive PET Material High Temperature Tape offers superior durability in complex environments, protecting boards from heat, mechanical stress, and chemicals. This innovation benefits compact devices requiring multifunctional protection.
6.2 Visual Marking TapesTapes with color-coded or patterned markings (e.g., Brown Circuit Board High Temperature Tape) aid assembly and maintenance. Markings identify critical areas, reducing errors during component placement and troubleshooting. In multilayer board assembly, they guide layer alignment, improving production efficiency and accuracy.
VII. Case Study7.1 Case OverviewA high-performance server manufacturer faced high circuit board failure rates due to harsh operating conditions. After adopting polyimide tape protection:
● Heat-prone areas were insulated with tape.
● Multilayer interfaces and vulnerable components were reinforced.
● Strict tape application protocols were implemented.Post-launch testing showed a significant reduction in failures.
7.2 Effect AnalysisThe tape’s thermal insulation stabilized heat zones, preventing material aging. Adhesion secured components during server operation, reducing mechanical failures. Its abrasion resistance minimized transport damage. Overall, durability improved, leading to extended product lifespan, lower maintenance costs, and enhanced market competitiveness.
VIII. Conclusion8.1 Summary of BenefitsPolyimide tape prolongs device lifespan by protecting against thermal, chemical, and mechanical threats. It lowers maintenance costs by reducing failures from environmental stresses. By ensuring stable electrical connections, it boosts product reliability, meeting stringent industry standards and consumer expectations.
8.2 Essential Role in ElectronicsAs devices become smaller and more powerful, circuit boards face increasing environmental challenges. Polyimide tape’s unique properties make it indispensable in sectors like semiconductors, aerospace, and automotive electronics. Its role in safeguarding board durability underpins technological advancements and global electronics industry growth.
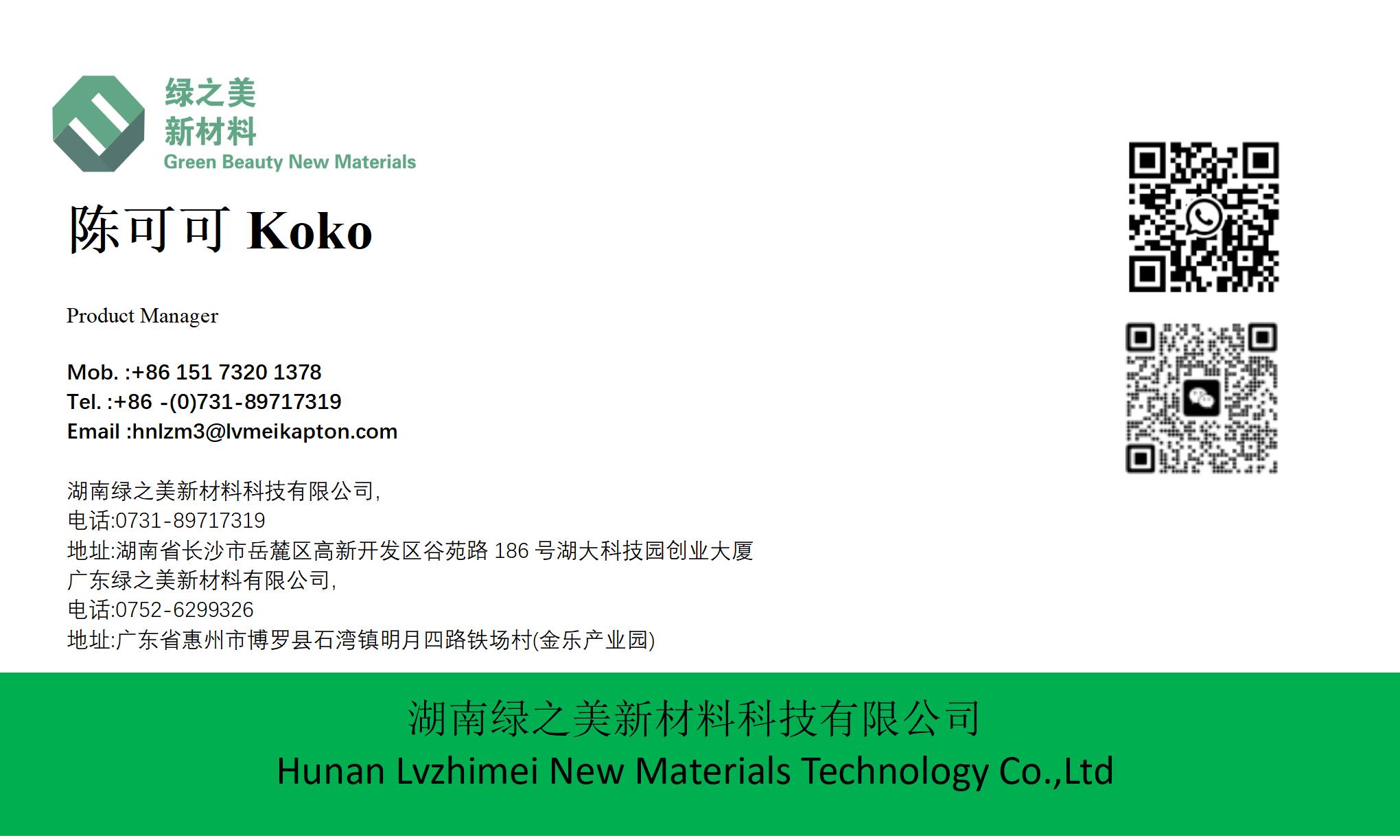