1. Understanding LVMEIKAPTON Insulating Electrical Tape
LVMEIKAPTON tape is a specialized PI-based solution designed for high-voltage applications. PI materials, renowned for their high-temperature resistance (operating range: -269°C to +400°C), excellent electrical insulation (dielectric strength up to 22 kV/mm), and chemical inertness, make LVMEIKAPTON ideal for EV battery packs. Key features include:
1.1 Temperature ResistanceThe tape maintains mechanical and electrical stability even under extreme thermal cycling (-40°C to +300°C), ensuring long-term reliability in EV battery environments where rapid temperature fluctuations occur during charging and discharging.
1.2 Electrical InsulationLVMEIKAPTON tape exhibits low dielectric constant (3.4) and minimal dielectric loss, reducing the risk of electrical breakdown. Its UL V-0 flammability rating and self-extinguishing properties enhance safety by preventing fire propagation.
1.3 Chemical and Mechanical DurabilityThe tape withstands exposure to battery electrolytes, acids, oils, and solvents, preventing degradation. Its high tensile strength (≥100 MPa) and flexibility allow conformal wrapping around battery cells and busbars without cracking or tearing.
2. Integration Considerations for EV Battery Packs
Integrating LVMEIKAPTON tape requires a systematic approach to ensure optimal performance and safety. Key steps and considerations are outlined below:
2.1 Cell and Busbar InsulationStep 1: Surface Preparation
● Clean battery cells, busbars, and interconnectors with isopropyl alcohol to remove contaminants.
● Ensure surfaces are dry and free of oxidation to achieve maximum adhesion.
Step 2: Tape Application
● Select LVMEIKAPTON tape with appropriate thickness (e.g., 0.05-0.25 mm) based on voltage rating and mechanical requirements.
● Apply tape using a tension-controlled wrapping machine (recommended) or manual winding, maintaining 50-70% overlap to avoid gaps.
● Avoid stretching the tape during application to prevent microcracks or reduced insulation thickness.
Step 3: Verification
● Conduct insulation resistance testing (≥10¹⁷ Ω·cm) and high-potential testing (e.g., 3x nominal voltage) to confirm integrity.
Table 1: LVMEIKAPTON Tape Application Parameters
Parameter | Recommendation |
Overlap Rate | 50-70% |
Wrapping Tension | 5-10 N/cm |
Dielectric Strength | ≥22 kV/mm |
Cure Temperature* | Room temperature (no curing required) |
*Note: LVMEIKAPTON tape is self-adhesive and requires no curing, simplifying integration.
2.2 Thermal ManagementLVMEIKAPTON tape's low thermal expansion coefficient (2-3 x 10⁻⁵/°C) helps maintain stable insulation thickness even under thermal cycling. Additionally, its high thermal conductivity (0.3-0.5 W/m·K) can be leveraged to improve heat dissipation by:
● Applying tape with conductive fillers (e.g., aluminum oxide) on heat-generating components.
● Designing tape layouts to direct heat flow away from critical areas.
2.3 Safety and Reliability
● Implement double-layer insulation (LVMEIKAPTON tape + secondary protection) for high-risk areas (e.g., high-voltage connectors).
● Periodically inspect tape integrity using infrared thermography to detect early signs of degradation.
3. Advantages Over Conventional Materials
LVMEIKAPTON tape offers significant advantages compared to traditional insulation materials like PTFE (Teflon) and silicone rubber:
3.1 Temperature RangeWhile PTFE operates up to 260°C and silicone rubber up to 200°C, LVMEIKAPTON's extended range (-269°C to +400°C) provides superior resilience in EV thermal environments.
3.2 Mechanical StrengthLVMEIKAPTON tape's tensile strength is up to 3x higher than silicone tape, reducing the risk of mechanical failure during battery pack vibration or thermal expansion.
3.3 Environmental ResistanceUnlike materials prone to hydrolysis (e.g., polyester), LVMEIKAPTON's resistance to moisture, UV, and radiation ensures stable performance throughout the EV lifecycle.
3.4 Cost and Weight EfficiencyThinner tape thickness (e.g., 0.1 mm vs. 0.3 mm for silicone) reduces material costs and contributes to lightweight battery pack design, crucial for EV range optimization.
4. Case Study: LVMEIKAPTON Integration in a 800V EV Battery Pack
A leading EV manufacturer integrated LVMEIKAPTON tape into its high-voltage battery system, achieving notable improvements:
4.1 Design Highlights
● Cell-to-Cell Insulation: Double-layer LVMEIKAPTON tape (0.15 mm + 0.05 mm) with aluminum shielding layer.
● Busbar Protection: Helical wrapping with 0.25 mm tape, enhancing creep resistance.
● Thermal Interface: Conductive tape applied to cooling plates for improved heat transfer.
4.2 Performance Outcomes
● Insulation Resistance: Maintained ≥100 GΩ after 1000 charge-discharge cycles.
● Weight Reduction: 15% compared to previous silicone-based solution.
● Cost Savings: 20% through reduced material and labor costs.
5. Future Considerations and Challenges
While LVMEIKAPTON tape is a game-changer, the following aspects warrant attention:
5.1 Tape SelectionDifferent LVMEIKAPTON grades (e.g., standard vs. reinforced) should be chosen based on specific application requirements (e.g., puncture resistance vs. flexibility).
5.2 Automation IntegrationAdvanced winding machines with integrated quality control systems (e.g., tape tension monitoring) can further enhance efficiency and consistency.
5.3 Recycling and SustainabilityPI materials' recyclability through chemical processes (e.g., alkaline hydrolysis) aligns with EV industry sustainability goals but requires optimized recovery methods.
Conclusion
LVMEIKAPTON insulating electrical tape represents a breakthrough solution for high-voltage EV battery packs. By leveraging its unparalleled thermal, electrical, and mechanical properties, designers can achieve safer, more reliable, and lightweight battery systems. As EV technology evolves toward higher voltages and faster charging, LVMEIKAPTON tape will play an increasingly critical role in enabling next-generation electrification.
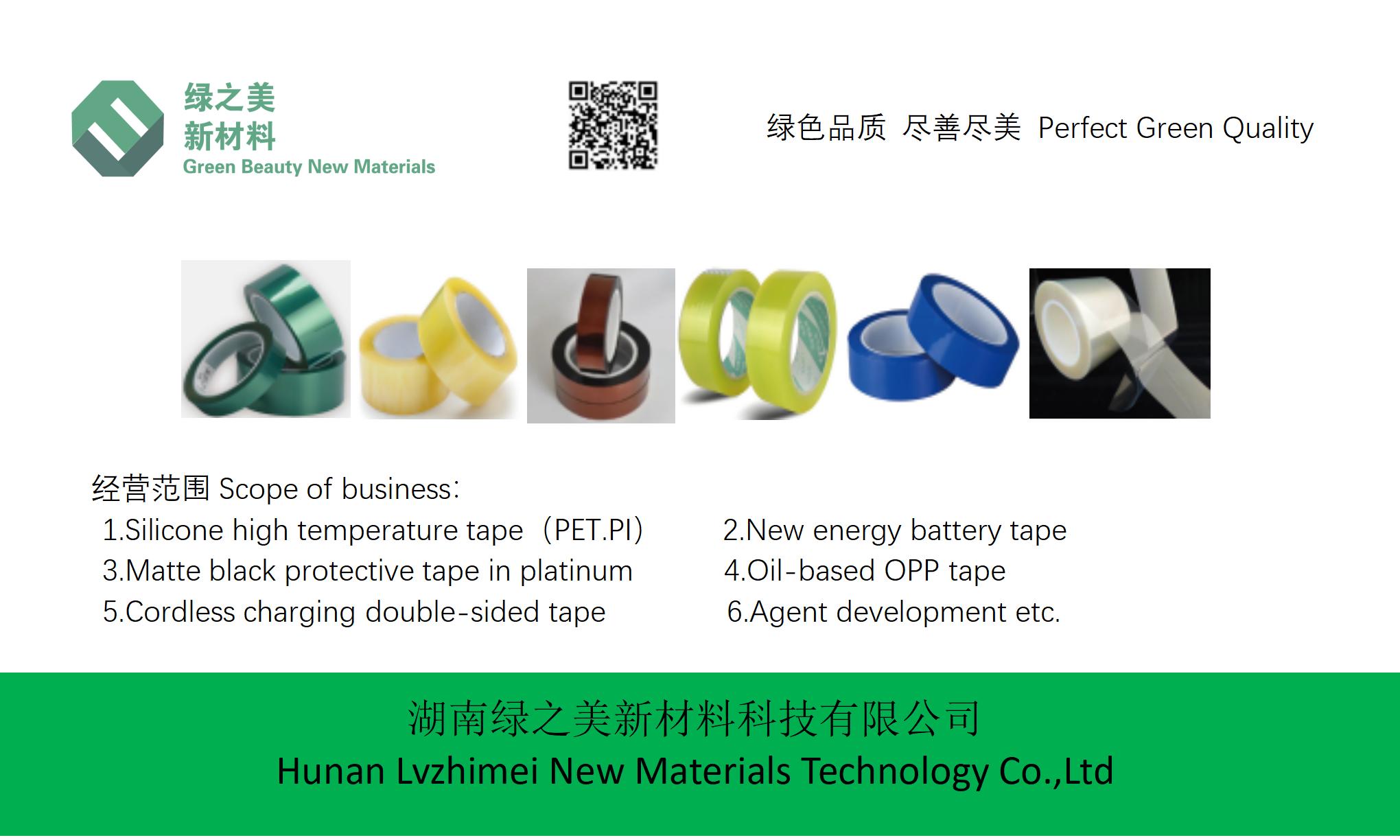
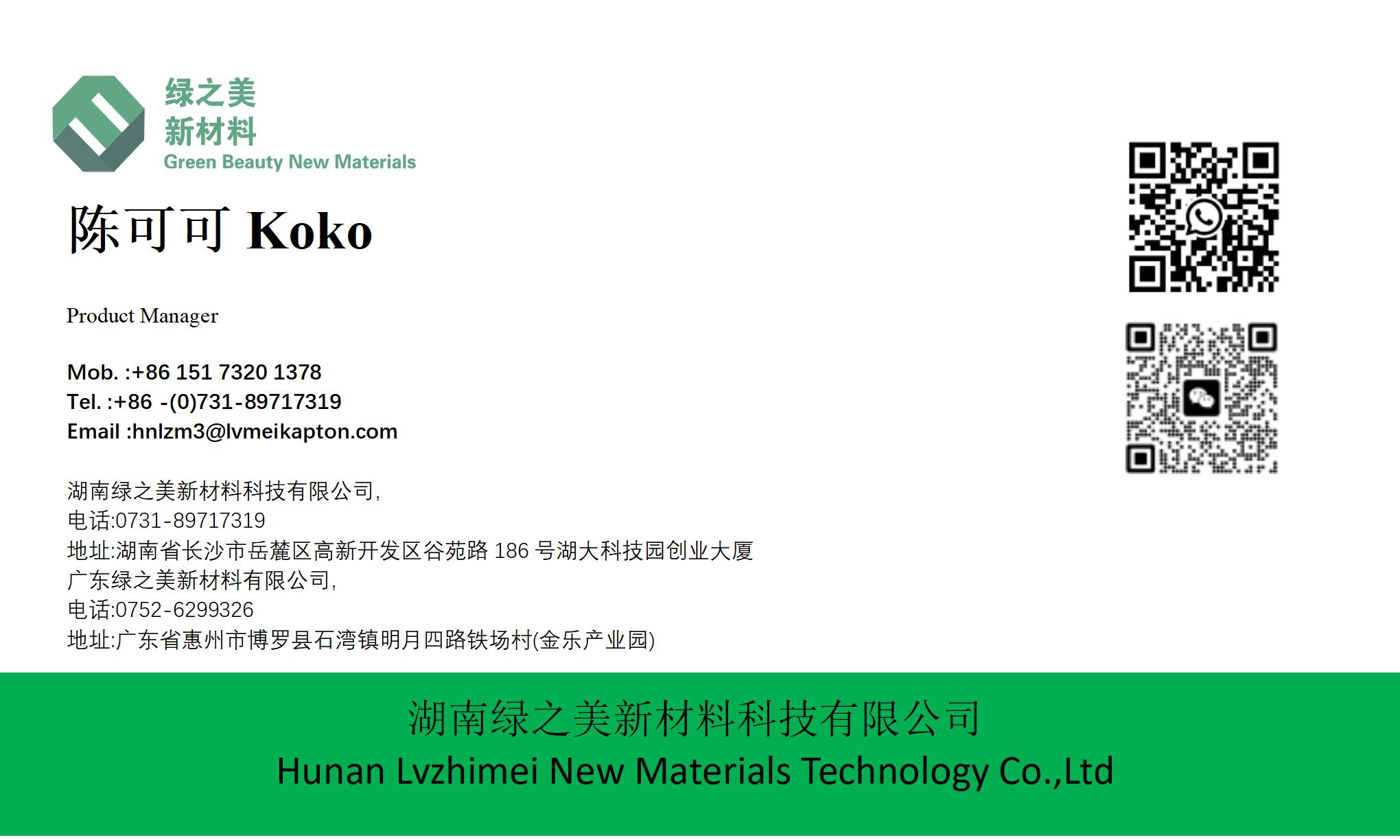