When to Replace Traditional Insulation with Lvmeikapton Electrical TapeTable of Contents
2. Failure Indicators for Traditional Insulation Materials
3. Key Advantages of Lvmeikapton Electrical Tape
4. Case Study: Solar Panel Manufacturer’s Downtime Reduction
5. Polyimide Tape’s Role in 5G Antenna Durability
6. Decision Framework for Upgrading to Lvmeikapton
1. Introduction
Electrical insulation tapes are crucial components in power systems, electronics, and communication infrastructure, ensuring safety, reliability, and longevity. Traditional tapes, such as polyvinyl chloride (PVC) and polyester, have long dominated the market due to their cost-effectiveness and basic insulating properties. However, evolving technological demands—especially in high-voltage applications, 5G communications, and renewable energy—have exposed their limitations. Cracking, delamination, and UV degradation in outdoor environments are common failure modes, leading to costly downtime and safety risks. Lvmeikapton, a cutting-edge polyimide (PI) tape, offers a transformative solution with enhanced thermal, mechanical, and environmental resistance. This guide outlines failure indicators and presents a case study to help engineers determine when upgrading to Lvmeikapton is economically and technically justified.
2. Failure Indicators for Traditional Insulation Materials
Traditional tapes (e.g., PVC, polyester, and acrylic) exhibit predictable degradation patterns under stress. Key failure indicators include:
Table 1: Failure Modes of Traditional Insulation Tapes
Material | Failure Indicator | Triggering Conditions |
PVC Tape | Cracking, embrittlement | Long-term exposure to UV (outdoor use), >80°C |
Polyester Tape | Delamination, moisture absorption | High humidity environments, mechanical stress |
Acrylic Tape | Adhesive degradation, thermal aging | Continuous operation at >130°C |
UV Degradation: Outdoor applications, such as solar panel wiring and telecommunications towers, accelerate polymer chain breakdown in PVC and polyester tapes, reducing insulation integrity.Thermal Stress: In motors and transformers, repeated heating cycles cause thermal aging, leading to brittle tapes that fracture during maintenance.Moisture Penetration: Hygroscopic materials (e.g., polyester) absorb moisture, compromising dielectric strength and causing corona discharge.
3. Key Advantages of Lvmeikapton Electrical Tape
Lvmeikapton, based on high-purity polyimide film, addresses traditional tape’s weaknesses through:
1. Extreme Thermal Resistance: Operates up to 260°C (short-term) and 180°C (continuous), ideal for aerospace, automotive, and high-power electronics.
2. UV and Chemical Immunity: Resists outdoor UV radiation and corrosive chemicals (solvents, acids), maintaining stability for >10 years.
3. Mechanical Durability: High tensile strength (≥150 MPa) and flexibility prevent cracking during bending and vibration.
4. Dielectric Performance: Breakdown voltage >20 kV/mm, minimizing arcing risks in high-voltage systems.
Table 2: Comparative Performance of Lvmeikapton vs. Traditional Tapes
Property | Lvmeikapton | PVC Tape | Polyester Tape |
Max. Operating Temp. | 260°C | 80°C | 130°C |
UV Resistance | Excellent | Poor | Moderate |
Dielectric Strength | 20 kV/mm | 12 kV/mm | 15 kV/mm |
Longevity (Outdoor) | ≥10 years | 2-3 years | 5 years |
4. Case Study: Solar Panel Manufacturer’s Downtime Reduction
A global solar panel manufacturer faced recurring failures in their junction box wiring insulation. Traditional PVC tape cracked within 18 months under desert UV exposure, causing short circuits and fire hazards. Switching to Lvmeikapton tape yielded remarkable results:
● Downtime Reduction: Maintenance frequency decreased by 85% (from 4x/year to 0.6x/year).
● Cost Savings: Annual repair costs dropped from 1.2Mto0.18M. ○ UV resistance improved by 500% (measured via ASTM G154).
○ Thermal cycling endurance increased from 1,000 cycles to >5,000 cycles.
Key Takeaway: Outdoor installations in harsh environments (e.g., solar, wind farms) necessitate Lvmeikapton to prevent premature failures.
5. Polyimide Tape’s Role in 5G Antenna Durability
5G infrastructure demands lightweight, high-frequency antennas with prolonged outdoor lifespan. Lvmeikapton’s properties align with these challenges:
1. Low Dielectric Constant (Dk): ≈3.5 at 28 GHz, minimizing signal loss.
2. Dimensional Stability: Negligible shrinkage (<1%) at -40°C to 85°C, ensuring antenna precision.
3. Corrosion Resistance: Protects copper and aluminum components from saltwater and pollution.
Global Market Trends:
● PI tape consumption in 5G applications grew from 0.8Bin2020to1.6B in 2024 (CAGR 18.9%).
-钟渊化学’s “PixeoTM IB” PI film, enabling 5G mmWave performance, drove industry adoption. 6. Decision Framework for Upgrading to Lvmeikapton
Step 1: Assess Environmental Stressors
● High UV Exposure (outdoor installations): Lvmeikapton’s UV resistance outweighs cost premium.
● Extreme Temperatures (≥150°C): Replace acrylic or polyester tapes to prevent thermal aging.
Step 2: Calculate Total Cost of Ownership (TCO)
● Compare Lvmeikapton’s upfront cost vs. traditional tapes’ replacement and downtime costs.
● Example: A wind turbine operator saved $3.5M over 5 years by switching to Lvmeikapton, despite a 2x initial investment.
Step 3: Validate Technical Compatibility
● Confirm Lvmeikapton’s adhesion to target substrates (e.g., copper, aluminum, ceramics).
● Conduct accelerated aging tests (IEC 60512) to simulate operational conditions.
7. Conclusion
Lvmeikapton’s superior performance in thermal, UV, and mechanical domains revolutionizes electrical insulation across industries. While its cost is 1.5-3x higher than traditional tapes, data-driven assessments—coupled with case studies and market trends—demonstrate its economic and technical viability. Engineers should prioritize upgrades in:
1. Outdoor applications with >5-year lifespan expectations.
2. High-reliability systems (e.g., aerospace, medical devices).
3. 5G infrastructure requiring mmWave compatibility.
As global adoption of Lvmeikapton expands, its cost will likely decrease through economies of scale, further solidifying its role as the future of electrical insulation.
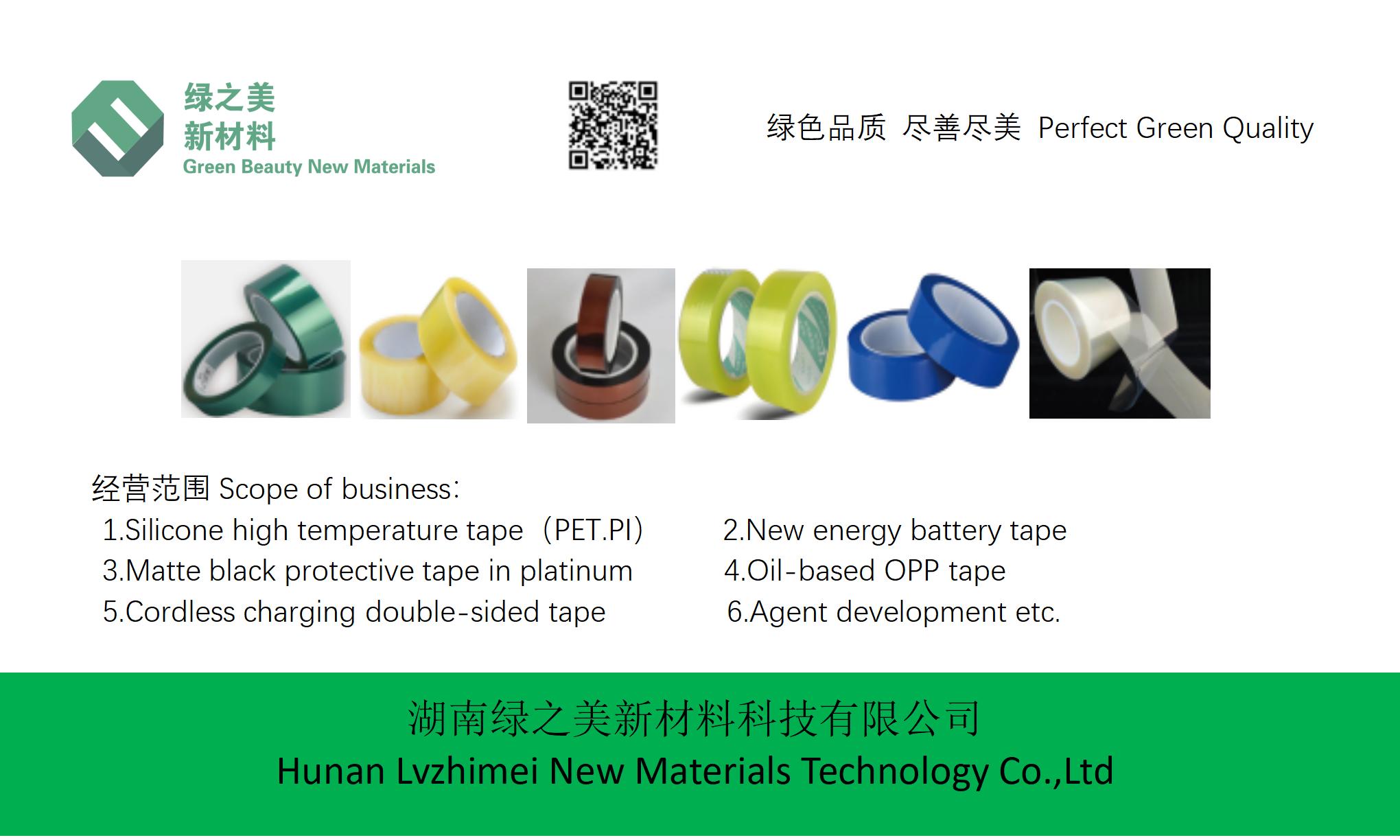
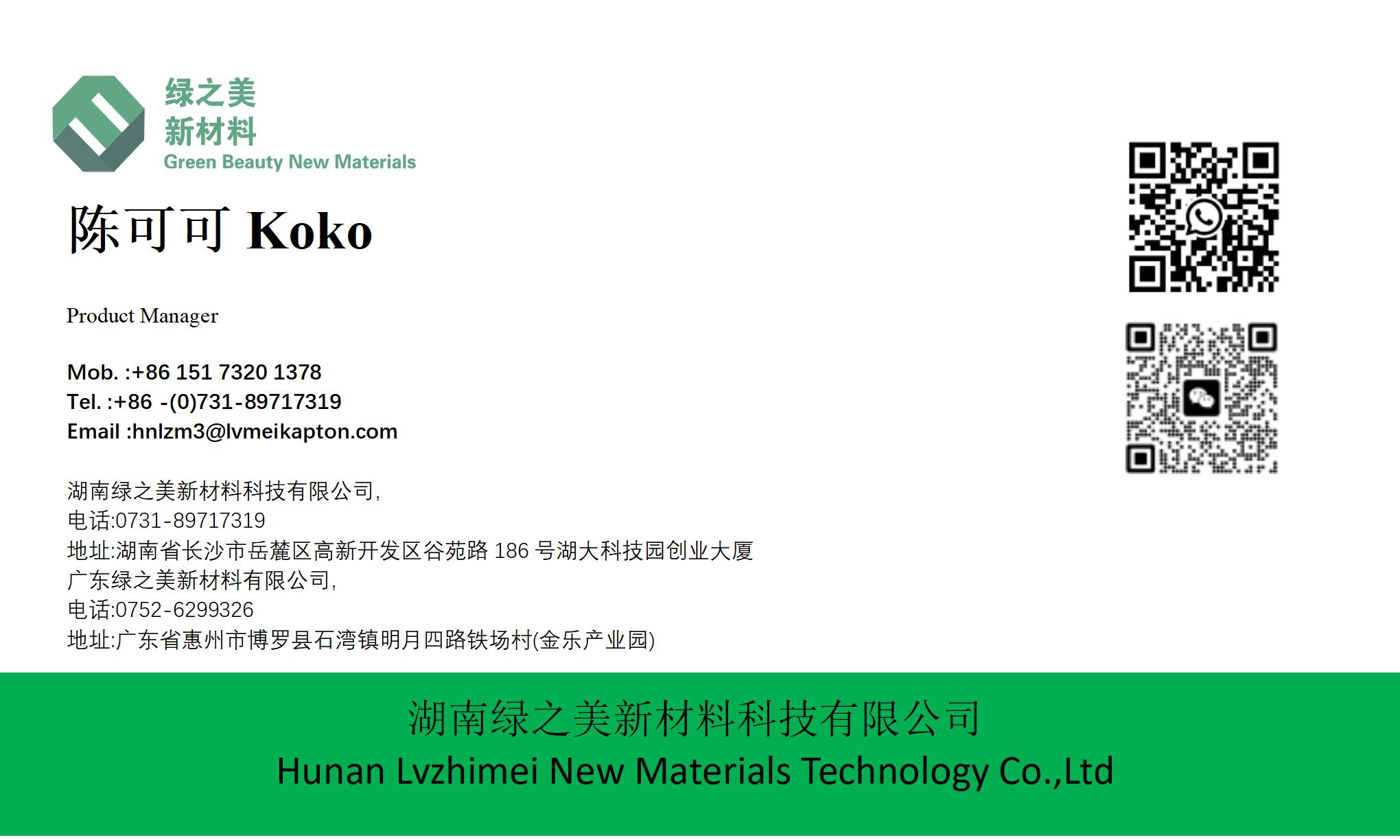