Key Differences Between Kapton Tape and PET Green Tape in Electronics Manufacturing
IntroductionIn the realm of electronics manufacturing, thermal protection, insulation, and adhesive solutions play a pivotal role in ensuring product reliability and performance. Kapton tape, renowned for its exceptional thermal stability and chemical resistance, and PET green tape, valued for its cost-effectiveness and eco-friendly properties, are two commonly used materials. This article delves into the key differences between these two tapes, focusing on thermal stability, chemical resistance, cost-effectiveness, and applications, providing a comprehensive comparison to guide selection for specific manufacturing processes.
1. Material Composition and Properties
1.1 Kapton Tape (Polyimide-Based)Kapton tape, also known as PI tape, is fabricated using polyimide (PI) film as the base material. PI, a thermosetting polymer, exhibits unparalleled thermal stability, withstanding temperatures up to 300°C for prolonged periods. Its chemical structure, consisting of aromatic rings and imide linkages, grants it inherent resistance to solvents, acids, alkalis, and radiation. Additionally, Kapton tape features high electrical insulation (击穿电压 ≥3kV), low thermal expansion, and excellent mechanical strength.
Key Features:
● Thermal Range: Continuous operation at 260°C, short-term resistance up to 300°C.
● Adhesion: Silicon-based adhesive offers strong bonding with no residual adhesive upon removal.
● Chemical Resistance: Resistant to most solvents, including corrosive chemicals.
● Thickness: Typically 0.05mm to 0.11mm.
1.2 PET Green Tape (Polyester-Based)PET green tape utilizes polyester (PET) film as the substrate, coated with silicone or acrylic adhesive. PET, a thermoplastic polymer, offers good thermal resistance up to 180°C and superior dimensional stability. Its green color aids in visual identification during assembly processes. While its chemical resistance is commendable, it falls short compared to Kapton’s robustness.
Key Features:
● Thermal Range: Continuous operation at 150°C–180°C, short-term up to 220°C.
● Adhesion: Silicone adhesive provides strong bonding with easy peelability.
● Chemical Resistance: Resistant to oils, acids, and common solvents.
● Thickness: Typically 0.04mm to 0.1mm.
Table 1: Material Comparison
Property | Kapton Tape | PET Green Tape |
Base Material | Polyimide (PI) | Polyester (PET) |
Thermal Range | 260°C (continuous), 300°C (short) | 180°C (continuous), 220°C (short) |
Adhesion | High (silicone) | Moderate-high (silicone/acrylic) |
Chemical Res. | Excellent (solvents, acids, alkalis) | Good (oils, acids, common solvents) |
Cost | High | Moderate |
2. Application Scenarios
2.1 Kapton Tape: High-End Electronics and严苛 EnvironmentsKapton tape’s superior thermal and chemical resilience makes it indispensable in high-stress applications:
● Electric Vehicle (EV) Battery Insulation: Kapton tape’s 300°C resistance and electrical insulation protect lithium-ion battery cells from thermal runaway risks, ensuring safety during rapid charging and high-temperature operations.
● PCB Gold Finger Protection: In circuit boards, Kapton tape shields gold-plated connectors from soldering damage, maintaining signal integrity.
● Transformer Coils: Its robust adhesion and heat resistance prevent insulation degradation in high-voltage transformers.
2.2 PET Green Tape: Cost-Effective Solutions for Moderate EnvironmentsPET green tape excels in cost-sensitive processes requiring thermal protection:
● LED Packaging: During LED chip encapsulation, PET tape masks components from epoxy resin, preventing contamination while maintaining visual clarity.
● PCB Wave Soldering: Its 180°C tolerance effectively shields circuit traces during soldering, avoiding component damage.
● Automotive Wiring Harnesses: PET tape捆扎电线, resisting engine heat (up to 150°C) and moisture.
Table 2: Application Comparison
Application | Preferred Tape | Rationale |
EV Battery Insulation | Kapton Tape | 300°C thermal stability, high insulation (≥5kV). |
PCB Wave Soldering | PET Green Tape | Cost-effective, 180°C resistance, easy peelability. |
LED Chip Protection | PET Green Tape | Visual identification (green color), chemical resistance to epoxy resins. |
3. Cost-Effectiveness AnalysisWhile Kapton tape offers superior performance, its cost is 2–3 times higher than PET tape due to PI’s complex synthesis and processing. PET tape, with its balanced performance and lower production costs, is ideal for mass production processes where extreme thermal or chemical exposures are not prevalent. However, in critical applications like aerospace or medical equipment, Kapton’s reliability justifies the premium price.
Figure 1: Cost vs. Performance Comparison(Graph depicting Kapton’s high performance vs. PET’s cost-efficiency)
4. Environmental ConsiderationsPET green tape holds an environmental advantage: its PET substrate is recyclable, and some variants use solvent-free production, reducing emissions. Kapton, while non-recyclable, excels in long-term durability, minimizing replacement needs. Both tapes meet RoHS compliance, ensuring eco-friendly manufacturing.
5. Selection GuidelinesWhen to Choose Kapton Tape:
● High-temperature environments (≥200°C).
● Chemical-intensive processes (e.g., acid cleaning).
● Critical insulation (e.g., transformers, EV batteries).
When to Choose PET Green Tape:
● Moderate thermal exposure (≤180°C).
● Cost-sensitive applications (e.g., PCB assembly).
● Visual identification requirements.
ConclusionKapton tape and PET green tape represent distinct solutions tailored to specific manufacturing demands. Kapton’s dominance in extreme thermal and chemical scenarios contrasts with PET’s versatility and cost-effectiveness in standard processes. Understanding these differences enables engineers to optimize performance, cost, and sustainability in electronic assemblies. As technology evolves, advancements in PET formulations may bridge the performance gap, but Kapton’s unparalleled thermal stability will remain indispensable for cutting-edge applications.
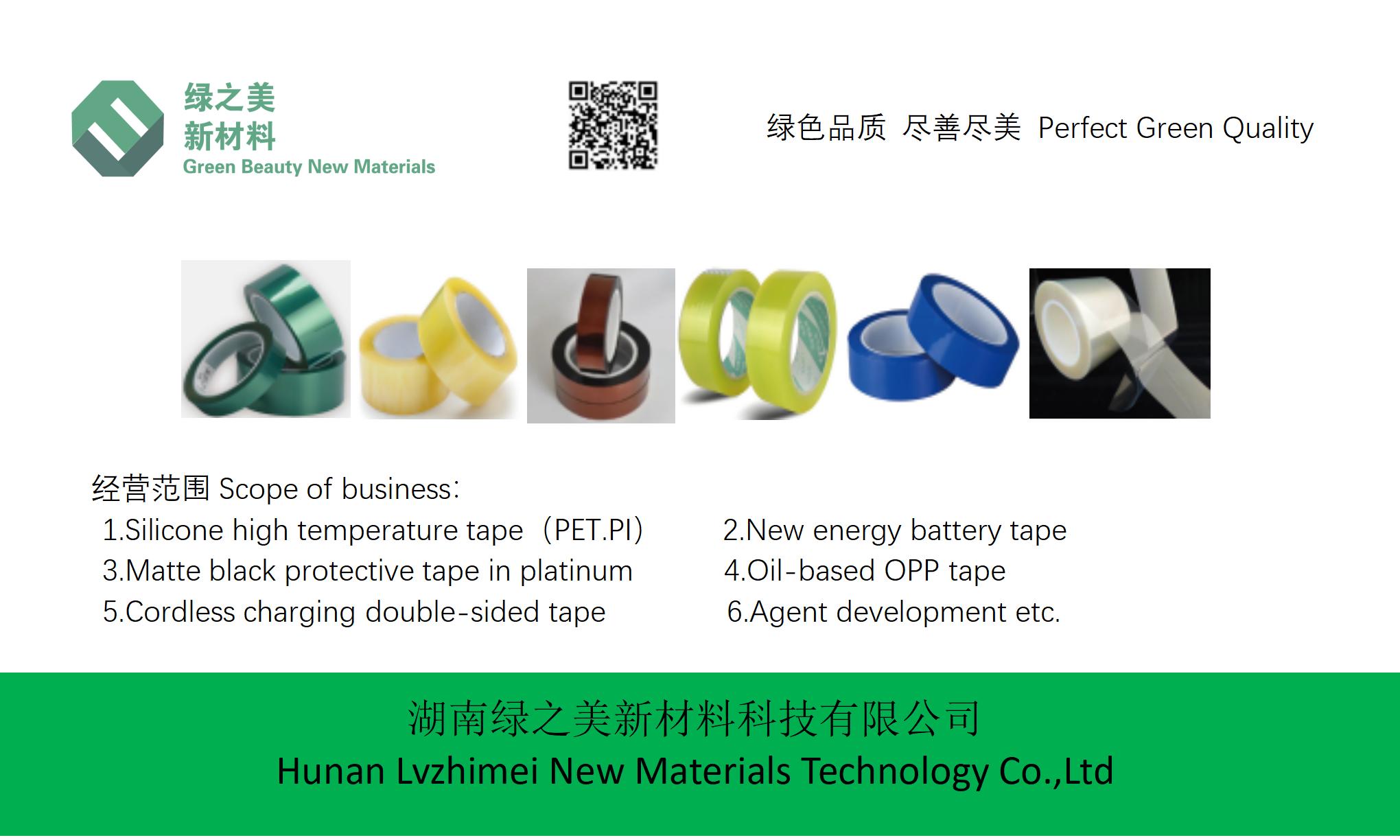