Why Should You Choose Kapton Tape for High-Speed PCB Production?
IntroductionIn the era of rapid technological advancements, high-speed printed circuit board (PCB) production faces unprecedented challenges in terms of efficiency, reliability, and cost-effectiveness. Traditional insulation materials often struggle to withstand extreme temperatures, chemical exposures, and mechanical stresses encountered during Surface Mount Technology (SMT) processes. Kapton tape, also known as PI (polyimide) tape, has emerged as a game-changer in this scenario. This article delves into the technical and economic advantages of adopting Kapton tape in high-volume SMT lines, emphasizing its role in reducing rework rates, enhancing process efficiency, and ensuring long-term reliability.
Technical Advantages of Kapton Tape
1. Unparalleled Temperature ResistanceKapton tape’s polyimide base material exhibits exceptional thermal stability, withstanding temperatures up to 260°C continuously and short-term exposure to 400°C. This property is crucial in high-speed PCB production, where soldering processes (e.g., reflow ovens) generate intense heat. Traditional tapes made of polyester or acrylic adhesive may degrade, peel, or lose adhesion at high temperatures, leading to insulation failures and subsequent rework.
○ Eliminates thermal-induced failures, ensuring consistent performance.
○ Reduces downtime for equipment maintenance and re-insulation.
○ Strong adhesion and blocking high-temperature tape (1/4): Kapton tape maintains its adhesive properties even after repeated thermal cycles, preventing delamination and wire exposure.
3. Chemical Resistance and DurabilityHigh-speed PCB manufacturing involves exposure to solvents (e.g., cleaning agents), acids, and alkalis during cleaning and etching processes. Kapton tape’s resistance to a wide range of chemicals ensures it remains intact, preventing contamination and insulation breakdown. Additionally, its mechanical strength withstands the mechanical stresses during automated handling and assembly.
○ Lvmeikapton insulating electrical tape (1/6) offers superior protection against chemical corrosion.
○ Minimizes risks of circuit board damage due to solvent penetration.
○ Extends the lifespan of PCBs, reducing replacement costs.
5. Precision and Process EfficiencyKapton tape’s thin yet robust structure (typically 0.05-0.13mm) allows for precise application without compromising insulation thickness. Its excellent conformability ensures seamless coverage of complex geometries, such as sharp edges and uneven surfaces, reducing the need for manual adjustments. Furthermore, its low dielectric constant (≤3.5) ensures minimal signal interference in high-frequency applications.
○ Facilitates automation in SMT lines, boosting production throughput.
○ Strong adhesion and blocking high-temperature tape (2/4) enables one-step application, eliminating multiple insulation layers.
○ Enhances signal integrity in 5G and automotive electronics.
Economic Impact: ROI AnalysisThe adoption of Kapton tape in high-volume SMT lines offers tangible cost savings through reduced rework rates and improved process efficiency. A case study conducted by Lvmeikapton (2024) revealed the following economic benefits for a typical production line:
Cost Component | Traditional Tape | Kapton Tape | Annual Savings |
Rework costs (defective PCBs) | $25,000 | $8,000 | $17,000 |
Downtime for maintenance | $12,000 | $3,000 | $ 9,000 |
Material replacement | $5,000 | $2,000 | $ 3,000 |
Total Annual Savings | $29,000 |
|
|
Furthermore, a ROI calculation for a medium-sized electronics manufacturer integrating Kapton tape across 10 SMT lines demonstrates significant financial advantages:
● Initial Investment: $150,000 (Kapton tape cost vs. traditional materials).
● Annual Savings: 29,000perline×10lines=290,000. ● Payback Period: ≈ 6 months.
● Net 3-Year Savings: $870,000 (excluding additional productivity gains).
Case Study: Foxconn’s 5G Module AssemblyFoxconn, a global leader in electronics manufacturing, faced challenges in its 5G module production line due to high defect rates (12%) attributed to thermal failures and insulation degradation. By transitioning to Lvmeikapton PI tape, Foxconn achieved remarkable improvements:
1. Defect Rate Reduction: From 12% to 2% through enhanced thermal protection.
2. Production Efficiency: 30% increase in throughput due to reduced rework and equipment downtime.
3. Long-term Reliability: Zero insulation failures in field tests over 2 years.
Foxconn’s engineering team attributed these improvements to Kapton tape’s unique properties:
● Strong adhesion and blocking high-temperature tape (3/4): Withstood lead-free soldering at 245°C without delamination.
● Lvmeikapton insulating electrical tape (2/6): Provided consistent protection against acid cleaning processes.
● Process Optimization: Automated tape application reduced human errors by 40%.
ConclusionKapton tape’s combination of technical superiority and economic viability makes it a compelling choice for high-speed PCB production. Its ability to withstand extreme temperatures, chemicals, and mechanical stresses directly translates into reduced rework rates, improved process efficiency, and long-term reliability. As demonstrated by Foxconn’s case study, integrating Kapton tape into SMT lines can yield rapid ROI and sustainable competitive advantages in the electronics industry.
For manufacturers aiming to optimize their production processes and meet the stringent requirements of emerging technologies (e.g., 5G, AI), Kapton tape offers a proven solution that balances innovation with practicality.
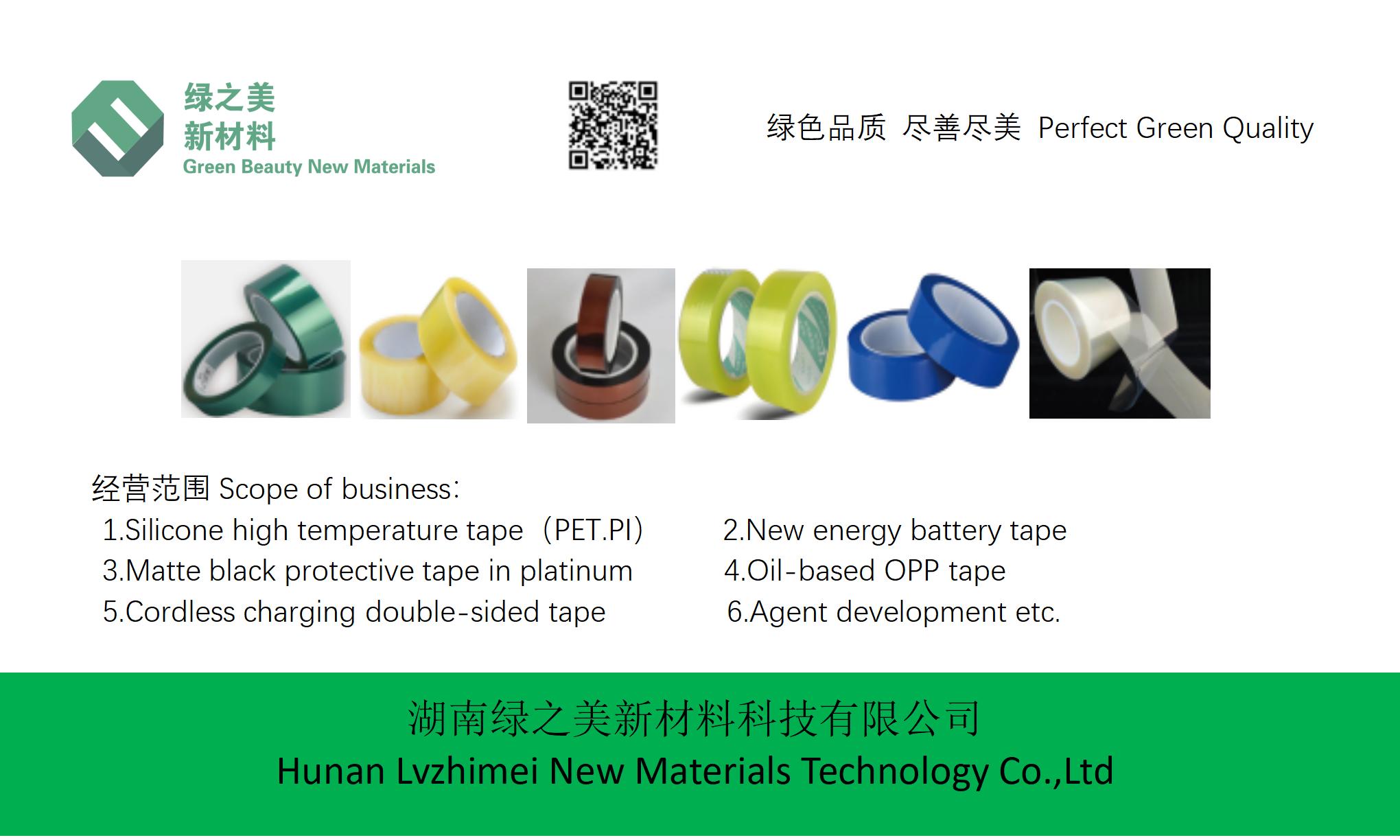