What Are the Different Adhesive Types for Polyimide Tapehttps://www.lvmeikapton.com/
Dive into the adhesive options for polyimide tape, from acrylic to silicone, understanding their strengths and applications.Keywords: Polyimide tape adhesives, Acrylic, Silicone, Adhesion strength, Temperature resistance
Polyimide tape, renowned for its exceptional thermal stability and electrical insulation, is a versatile material widely used in electronics manufacturing, electrical insulation, and high-temperature applications. However, its performance is significantly influenced by the adhesive types used. Understanding the differences between adhesive systems is crucial for selecting the right tape for specific applications. This article delves into the various adhesive types for polyimide tape, exploring their properties, strengths, and ideal use cases.
1. Acrylic-Based Adhesives: Versatility and Cost-Effective Solutions
Acrylic adhesives are one of the most common types used in polyimide tapes, particularly in applications where room-temperature bonding and flexibility are prioritized. These adhesives are typically pressure-sensitive, meaning they require minimal pressure to achieve strong adhesion. Key features include:
● Adhesion Strength: Moderate to high bond strength, suitable for general-purpose applications such as masking during painting or temporary bonding.
● Temperature Range: Operate effectively between -40°C to 150°C. While they offer decent resistance, they are not ideal for prolonged exposure to extreme heat.
● Chemical Resistance: Resistant to solvents, moisture, and UV radiation, making them suitable for outdoor or corrosive environments.
● Applications: Ideal for PCB masking during soldering, wire insulation, and general-purpose electronics assembly. Examples include "Self-adhesive back blocking spray paint tape," which provides excellent coverage during spray painting processes.
Advantages:
● Cost-effective compared to silicone-based alternatives.
● Easy to remove without residue, reducing cleanup efforts.
● Versatile across a range of environments.
Limitations:
● Limited high-temperature performance beyond 150°C.
● Adhesion may degrade over time in harsh conditions.
2. Silicone Adhesives: High-Temperature Champions
Silicone adhesives are the cornerstone of polyimide tapes designed for extreme thermal environments. These adhesives exhibit remarkable stability at elevated temperatures, making them indispensable in applications where heat resistance is paramount. Key characteristics:
● Temperature Resistance: Maintain adhesion and stability up to 300°C (some grades可达350°C), ideal for soldering processes, oven curing, and motor insulation.
● Adhesion Strength: High initial tack and long-term bonding, even under thermal cycling (repeated heating and cooling).
● Chemical and Weather Resistance: Resistant to oils, chemicals, and weathering, ensuring durability in industrial settings.
● Flexibility: Retain elasticity even at high temperatures, preventing cracking or brittleness.
● Applications: Widely used in "Strong adhesion and blocking high-temperature tape" for transformer winding, capacitor insulation, and over-soldering protection in electronics manufacturing.
Advantages:
● Unmatched high-temperature performance.
● Long-term reliability in demanding environments.
● Resistance to thermal aging.
Limitations:
● Higher cost compared to acrylic tapes.
● Removal may require higher temperatures or solvents.
3. Modified Acrylic Adhesives: Balancing Performance and Cost
To bridge the gap between standard acrylic and silicone, modified acrylic adhesives offer enhanced properties without the premium price of silicone. These formulations are tailored for applications requiring improved thermal and chemical resistance. Key features:
● Temperature Range: Perform well up to 200°C, surpassing traditional acrylic tapes.
● Adhesion Strength: Balanced performance, suitable for medium-duty applications like PCB镀金手指保护.
● Cost-Effectiveness: Cheaper than silicone while offering improved resistance compared to standard acrylic.
● Applications: Commonly found in "Adhesive PET material high-temperature tape" used in electronics assembly and wire bonding, providing a cost-effective alternative to silicone.
Advantages:
● Better thermal stability than standard acrylic.
● Cost-efficient for mid-range applications.
● Easy application and removal.
Limitations:
● Performance still falls short of silicone at temperatures above 250°C.
4. Specialty Adhesives: Tailored for Niche Applications
Beyond the main types, specialized adhesive formulations cater to unique requirements. These include:
● Fluorosilicone Adhesives: Combining silicone and fluoropolymer properties, offering exceptional resistance to aggressive chemicals and high temperatures (up to 260°C). Ideal for aerospace or chemical processing applications.
● Epoxy-Based Adhesives: Provide ultra-high adhesion and mechanical strength, suitable for permanent bonding in transformers or heavy-duty insulation. However, they are challenging to remove and require curing time.
● Thermally Conductive Adhesives: Embedded with fillers like aluminum oxide, enabling heat dissipation in electronic components. Used in CPU or LED module assembly.
Advantages:
● Targeted performance for specific challenges (e.g., chemical resistance, thermal conductivity).
Limitations:
● Limited availability and higher costs.
● Complex application processes.
5. Multilayer Adhesive Systems: Engineering Synergy
Advanced polyimide tapes leverage multilayer adhesive structures to maximize performance. For example:
● Acrylic-Silicone Hybrid Tapes: Combining an acrylic layer for easy application and a silicone layer for high-temperature resistance. Ideal for processes with initial room-temperature handling followed by high-temperature curing.
● Adhesive with Reinforcement Layers: Incorporating additional layers (e.g., PET or fiberglass) to enhance mechanical strength, preventing tape tearing during handling.
These systems optimize properties like adhesion, thermal stability, and durability, addressing complex application demands.
Key Considerations for Selection
When choosing a polyimide tape adhesive, assess the following factors:
Consideration | Acrylic | Silicone | Modified Acrylic | Specialty |
Temperature Range | -40°C to 150°C | -60°C to 300°C | -40°C to 200°C | Varies (e.g., 260°C for fluorosilicone) |
Adhesion Strength | Moderate to high | High | Balanced | Ultra-high (e.g., epoxy) |
Cost | Low | High | Medium | High |
Ease of Removal | Easy | Moderate (may require heat) | Easy | Varies |
Common Applications | Masking, general electronics | Soldering, transformer insulation | Mid-temp electronics | Aerospace, specialty electronics |
Applications in Modern Electronics
Polyimide tapes with diverse adhesives are pivotal in advanced manufacturing:
● PCB Assembly: Acrylic tapes mask gold fingers during plating, while silicone tapes protect components during reflow soldering.
● Li-Ion Battery Manufacturing: Modified acrylic tapes insulate electrode winding, balancing thermal resistance and cost.
● Automotive Electronics: Silicone tapes withstand engine compartment temperatures (up to 200°C) and vibration.
● 5G Infrastructure: Thermally conductive tapes dissipate heat in high-power RF components.
Conclusion
The adhesive types for polyimide tape dictate their performance across temperature, adhesion, and durability. Acrylic offers versatility, silicone excels in high heat, and modified formulations balance cost and performance. As technology evolves—whether in electric vehicles, aerospace, or miniaturized electronics—understanding these adhesive differences is essential for optimizing reliability and efficiency. Selecting the right tape ensures components withstand thermal, chemical, and mechanical stresses, paving the way for innovative advancements.
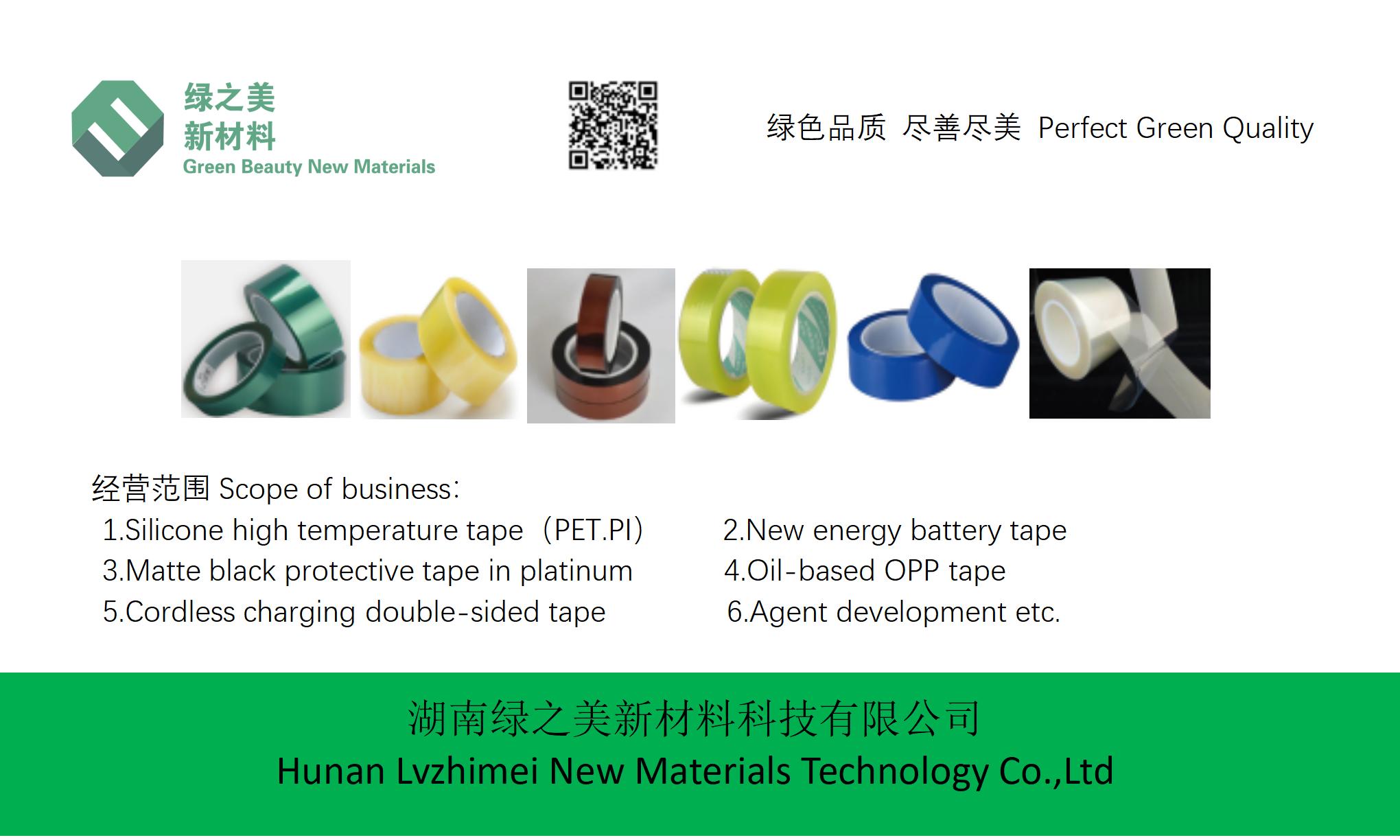