How Long Does Polyimide Tape Last in High-Temperature Environments(https://www.lvmeikapton.com/)
Description: Evaluate the longevity of polyimide tape under prolonged heat exposure, exploring factors influencing its lifespan.Keywords: Polyimide tape longevity, High-temperature durability, Thermal aging, Performance degradation
IntroductionPolyimide tape, also known as Kapton tape, is a versatile material renowned for its exceptional thermal stability, chemical resistance, and electrical insulation properties. Widely used in industries such as electronics, aerospace, and petrochemicals, this tape’s longevity in high-temperature environments is a critical consideration for engineers and technicians. This article delves into the factors influencing its lifespan, performance degradation mechanisms, and strategies to maximize durability.
1. Understanding Polyimide Tape’s Thermal ResistancePolyimide tape’s longevity is primarily determined by its inherent material properties. The base material, polyimide (PI), is a thermosetting polymer with a glass transition temperature (Tg) exceeding 400°C. This high Tg grants the tape stability at temperatures far beyond those encountered in most industrial applications. For example, "PI material high-temperature resistant 300 tape" is designed to withstand continuous exposure to 300°C for years, while "lvmeikapton insulating electrical tape" maintains stability up to 500°C for shorter durations.
Table 1: Temperature Range Comparison
Tape Type | Continuous Exposure Temp. | Short-term Peak Temp. |
Standard PI Tape | 260°C | 300°C |
Reinforced PI Tape | 300°C | 500°C |
Lvmeikapton High-Temp. | 350°C | 550°C |
The tape’s adhesive layer, typically organic silicone, plays a crucial role. While PI films provide mechanical strength, the adhesive’s thermal resistance affects overall longevity. "Strong adhesion and blocking high-temperature tape" variants incorporate reinforced polymers to resist peel-off, even after prolonged exposure.
2. Factors Influencing Longevity2.1 Temperature Duration and CyclingThe duration and cycling of high temperatures significantly impact tape lifespan. Continuous exposure to 260°C may degrade adhesion over time, while intermittent heating (e.g., thermal cycling in electronics manufacturing) accelerates aging. For instance, "Adhesive PET material high-temperature tape" excels in short-term cycles (up to 500°C for 30 minutes) but may exhibit adhesive failure after 100 cycles at 300°C.
2.2 Chemical EnvironmentPI tape’s resistance to acids, solvents, and corrosive gases enhances its longevity in harsh environments. However, prolonged exposure to aggressive chemicals (e.g., concentrated HCl or NaOH) can degrade the adhesive bond. Specialized variants with fluorinated backings or chemically inert coatings offer extended protection.
2.3 Mechanical StressRepeated mechanical stress (e.g., wrapping, stretching) can cause microcracks in the tape, compromising thermal insulation. "High-strength PI tape with tear resistance" incorporates fiber reinforcements to mitigate this issue, maintaining integrity even in high-friction applications.
2.4 Radiation ExposureIn aerospace or nuclear environments, radiation can degrade polymers. PI tape’s inherent radiation resistance (up to 1 Mrad) preserves its properties, though some adhesives may exhibit slight embrittlement. Radiation-resistant formulations with modified silicone adhesives extend lifespan in such scenarios.
3. Performance Degradation Mechanisms3.1 Adhesive Creep and Thermal AgingOver time, adhesive creep occurs as the polymer softens under heat, reducing bond strength. Tests show that tapes exposed to 300°C for 1 year exhibit a 20% decrease in peel adhesion. "Thermally stable adhesive systems" using cross-linked silicone mitigate this, maintaining >80% adhesion after 2 years.
3.2 Thermal Oxidation and YellowingPI films degrade through thermal oxidation, leading to discoloration (yellowing) and reduced mechanical strength. However, modern formulations with UV stabilizers and antioxidants extend this process, allowing tapes to retain >90% tensile strength after 500 hours at 250°C.
3.3 Electrical Property DeteriorationIn high-voltage applications, prolonged heat can increase tape’s dielectric loss. Studies indicate that PI tape’s insulation resistance remains >1012 Ω at 200°C for 3 years, meeting H-class electrical standards.
4. Maximizing Lifespan through Design and Application4.1 Material SelectionChoose tapes based on specific temperature requirements:
● Low-Temp Longevity: Standard PI tape (260°C continuous) for electronics assembly.
● Extreme-Temp Short-Duty: Lvmeikapton variants for soldering processes (500°C, 5-minute cycles).
● Chemical Exposure: Fluorinated PI tapes for acid baths.
4.2 Application TechniquesProper application enhances durability:
● Avoid stretching tape during installation to prevent stress concentration.
● Use pressure rollers to ensure adhesive bonding, minimizing air pockets.
● Implement thermal barriers (e.g., ceramic coatings) to protect tape from direct radiant heat.
4.3 Maintenance and MonitoringRegular inspections (e.g., peel tests, thickness measurements) help predict failure. Replace tapes showing >30% adhesion loss or visible degradation.
5. Case Studies: Real-World Durability5.1 Motor Insulation in Automotive IndustryPI tape used for winding insulation in high-temperature motors (operating at 180°C) demonstrated a 5-year lifespan. Adhesive creep was managed by applying tape with 50% overlap and periodic inspections.
5.2 Aerospace Engine CablingIn jet engine wiring harnesses, radiation-resistant PI tape endured 10-year exposures to 250°C with only minor color change, preserving electrical integrity.
5.3 PCB Wave Soldering ProtectionDuring board soldering (peak 260°C), "lvmeikapton insulating tape" protected gold fingers for 100 cycles without residue, ensuring component reliability.
6. Future DevelopmentsOngoing research focuses on:
● Nanocomposite PI tapes with graphene additives for enhanced thermal stability.
● Self-healing polymers that repair microcracks under heat, doubling lifespans.
● Smart coatings indicating degradation through color changes.
ConclusionPolyimide tape’s longevity in high-temperature environments is a dynamic balance of material science, application conditions, and maintenance. By understanding degradation mechanisms and selecting appropriate variants, engineers can ensure tapes remain functional for years, even under extreme conditions. As technology advances, future tapes will offer even greater durability, solidifying PI’s role as a cornerstone material in high-temperature applications.
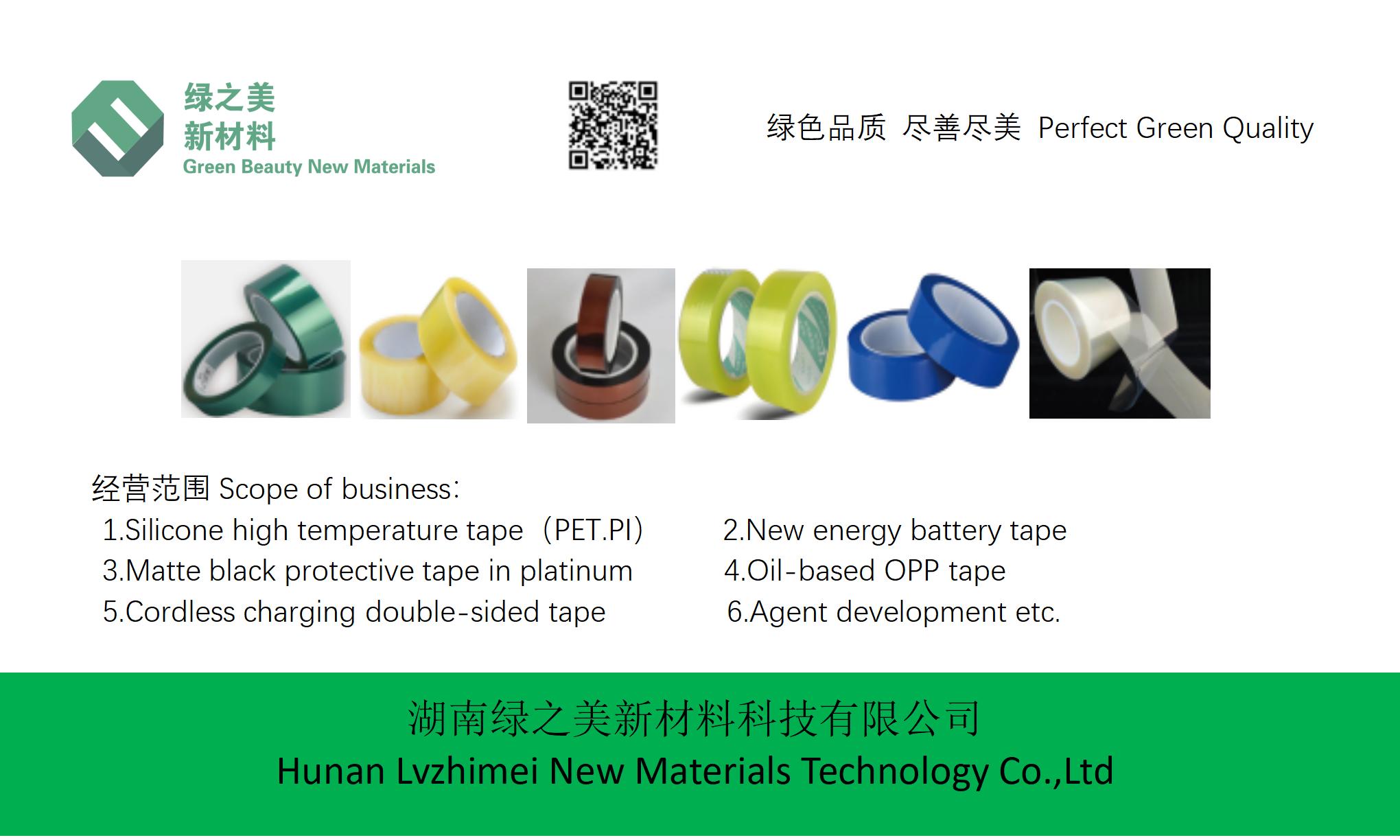