Who Should Use Polyimide Tape in Their Electronics Workflows(https://www.lvmeikapton.com/)
Title: Who Should Use Polyimide Tape in Their Electronics WorkflowsDescription: Understand the professionals and industries that benefit most from polyimide tape, from manufacturers to hobbyists.Keywords: Polyimide tape users, Electronics industry, Manufacturing, Repair, Hobby applications
Polyimide tape, also known as Kapton tape or PI tape, is a high-performance adhesive solution renowned for its exceptional thermal resistance, electrical insulation, mechanical strength, and chemical stability. This versatile material plays a crucial role in diverse electronic workflows, offering reliable protection and performance across industries. This article delves into the key user groups and sectors that should consider integrating polyimide tape into their processes, exploring its benefits and applications in detail.
1. Electronics Manufacturers: Ensuring Efficiency and Reliability
Electronics manufacturers face stringent requirements for component protection, assembly precision, and long-term durability. Polyimide tape serves as an indispensable tool in several manufacturing stages:
a. Circuit Board Assembly and Wave SolderingDuring wave soldering, circuit boards are exposed to molten solder at temperatures exceeding 250°C. Polyimide tape (e.g., "PI material high-temperature resistant 300 tape") acts as a shield, preventing solder bridges and protecting sensitive areas like gold fingers (connectors). Its silicone adhesive ensures easy removal without residue post-soldering, maintaining board integrity.
b. Surface-Mount Technology (SMT) ProtectionIn SMT processes, components are heat-sensitive. Polyimide tape offers superior thermal protection during reflow soldering, preventing damage to delicate parts. Models like "Self-adhesive back blocking spray paint tape" are ideal for masking areas during coating processes, withstanding high temperatures while allowing clean剥离.
c. Motor and Transformer InsulationH-grade motors and transformers demand robust insulation. Polyimide tape’s electrical insulation properties (up to H-class) and tensile strength make it suitable for coil wrapping, thermal resistance protection, and preventing short circuits. It withstands continuous operation in high-temperature environments, enhancing equipment lifespan.
d. Battery ManufacturingLithium-ion battery production requires precise electrode tab fixation. Polyimide tape’s chemical resistance and stable adhesion ensure secure tab positioning during assembly, minimizing risks of electrical failures.
Technical Advantages for Manufacturers:
● Thermal Resistance: Up to 260°C continuous exposure (short-term up to 300°C).
● Adhesion Balance: Secure bonding without damaging substrates during removal.
● Environmental Compliance: RoHS and halogen-free, meeting global regulatory standards.
2. Repair Technicians: Reliable Solutions for Complex Fixes
Repair professionals in electronics, automotive, and aerospace sectors rely on polyimide tape for its durability and problem-solving versatility:
a. Faulty Circuit RepairWhen repairing damaged wires or connectors, "lvmeikapton insulating electrical tape" provides a resilient barrier against moisture, abrasion, and electrical leaks. Its high tensile strength prevents unraveling in stressed environments.
b. Overheating Component IsolationFor components prone to overheating (e.g., power modules), polyimide tape acts as a thermal buffer, dissipating heat while insulating neighboring parts. This mitigates thermal damage and extends device longevity.
c. Emergency Field RepairsIn situations where quick fixes are needed, polyimide tape’s ease of application and compatibility with various substrates (metal, plastic, ceramics) makes it a go-to tool. Its resistance to solvents and chemicals ensures repairs withstand environmental stresses.
Key Benefits for Repair Work:
● Versatility: Adaptable to different repair scenarios (PCB, cable, motor fixes).
● Low Residue Risk: Avoids contamination during disassembly or reuse.
● Long-Term Performance: Maintains stability even in fluctuating temperatures.
3. Hobbyists and DIY Enthusiasts: Balancing Cost and Capability
For those engaged in electronics prototyping, repairs, or creative projects, polyimide tape offers a cost-effective yet high-performing option:
a. Prototyping and TestingDuring circuit board prototyping, "Adhesive PET material high-temperature tape" provides temporary insulation for testing phases. It allows easy adjustments without compromising component protection.
b. 3D Printer Nozzle ProtectionHobbyist 3D printer users utilize polyimide tape to prevent nozzle clogging during high-temperature prints. Its thermal resistance shields components from melting, reducing maintenance needs.
c. Electronics ModificationsDIY enthusiasts modify devices (e.g., smartphones, gaming consoles) using polyimide tape to insulate exposed circuits, reinforce cable connections, or protect heat-sensitive areas during overclocking.
Why Hobbyists Choose Polyimide Tape:
● Affordable Performance: Cost-effective compared to industrial alternatives.
● Ease of Use: No specialized tools required for application.
● Minimal Waste: Precision cutting reduces material consumption.
4. Aerospace and Automotive Engineers: Meeting Extreme Conditions
These sectors demand materials that perform under severe thermal, mechanical, and chemical exposures. Polyimide tape excels in:
a. Aerospace ApplicationsIn aircraft and spacecraft, components face extreme temperatures (e.g., engine compartments). Polyimide tape’s H-class insulation and radiation resistance protect wiring harnesses, sensors, and connectors. It ensures reliability even in vacuum environments.
b. Automotive ElectronicsModern vehicles integrate sophisticated electronic systems. Polyimide tape insulates engine control units (ECUs), battery packs, and sensor cables, withstanding vibrations, oil exposure, and temperatures up to 200°C. Its flame retardancy enhances safety.
c. Hybrid and Electric Vehicles (EVs)In EV battery packs, polyimide tape secures high-voltage connections, preventing arcing and corrosion. Its chemical resistance to electrolytes and acids ensures long-term battery performance.
Technical Specifications for Critical Environments:
Property | Value |
Temperature Range | -70°C to 260°C |
Dielectric Strength | ≥4000 V/mil |
Tensile Strength | 50–100 N/cm |
Flame Retardancy | UL 94 V-0 certified |
5. Other Industries Leveraging Polyimide Tape
Beyond electronics, polyimide tape finds utility in:
● Medical Devices: Insulating leads in MRI machines and protecting implantable electronics.
● Chemical Processing: Sealing pipes and equipment exposed to corrosive substances.
● Renewable Energy: Insulating solar panel connections and wind turbine generators.
● Military and Defense: Shielding radar systems and communication equipment from electromagnetic interference (EMI).
6. Selecting the Right Polyimide Tape: Considerations for Users
Users across sectors must assess specific requirements to maximize tape effectiveness:
a. Temperature RangeDetermine the maximum continuous and short-term temperatures the application will encounter. For example, wave soldering may require tapes rated ≥300°C.
b. Adhesion StrengthChoose tapes with appropriate adhesive types (e.g., silicone for high-temperature uses, acrylic for temporary fixes). Check peel strength to avoid residue or detachment.
c. Environmental ExposureIdentify chemical exposures (solvents, acids) and mechanical stresses (vibrations, abrasion). Flame retardant or low-static versions may be necessary.
d. Certification ComplianceEnsure tapes meet industry standards (RoHS, UL, MIL-SPEC) for regulatory adherence.
7. Conclusion: Polyimide Tape as a Multifaceted Solution
From global manufacturers to individual hobbyists, polyimide tape’s unique blend of thermal resistance, electrical insulation, mechanical durability, and chemical stability makes it an essential asset across diverse electronics workflows. Its adaptability, cost-effectiveness, and reliability position it as a cornerstone material in modern technology. As industries evolve—towards electric vehicles, space exploration, and advanced electronics—polyimide tape’s role will only expand, solidifying its status as a must-have tool for professionals and enthusiasts alike.
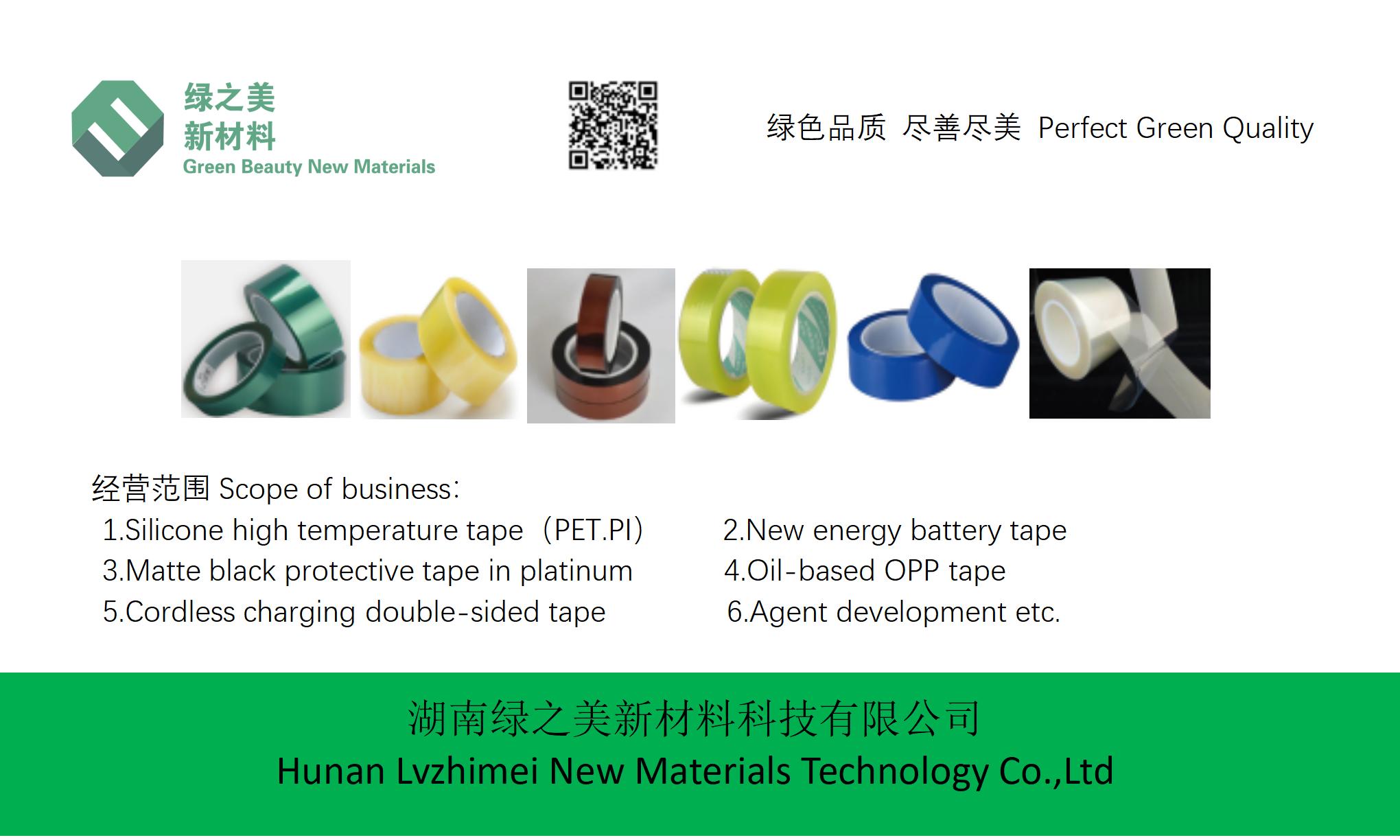