When to Use Self-Adhesive Back Blocking Spray Paint Tape in Electronicshttps://www.lvmeikapton.com/
Title: When to Use Self-Adhesive Back Blocking Spray Paint Tape in ElectronicsDescription: Learn the scenarios where self-adhesive spray paint tape is indispensable for electronics, ensuring clean coatings and component protection.Keywords: Self-adhesive tape, Spray paint protection, Electronics coating, Masking, Adhesion
Self-Adhesive Back Blocking Spray Paint Tape in Electronics: A Comprehensive Guide
In the intricate world of electronics manufacturing, ensuring precise coatings and protecting sensitive components during spray painting is paramount. Self-adhesive back blocking spray paint tape has emerged as a game-changing solution, offering unparalleled protection and efficiency in various electronic assembly processes. This article delves into the scenarios, applications, benefits, and technical considerations of using this specialized tape, highlighting its indispensable role in maintaining product integrity and quality.
1. Understanding Self-Adhesive Back Blocking Spray Paint TapeSelf-adhesive back blocking spray paint tape, also known as masking tape or protective tape, is designed specifically for electronics manufacturing environments. It features a high-adhesion adhesive layer on one side and a backing material (commonly polyimide or polyester) that resists chemicals, heat, and abrasion. Unlike traditional masking tapes, this tape offers superior adhesion properties without leaving residue upon removal, ensuring clean edges and surfaces.
Key characteristics include:
● Strong Adhesion: Securely adheres to electronic components, circuit boards, and connectors, preventing displacement during spraying.
● Chemical Resistance: Resistant to solvents, paints, and coatings commonly used in electronics喷漆 processes.
● Ease of Application: Peel-and-stick application saves time and labor, ideal for high-volume production.
● Clean Removal: Leaves no residue, avoiding damage to delicate components or coatings.
2. When to Use Self-Adhesive Spray Paint Tape in ElectronicsThe tape's versatility makes it essential in several scenarios. Understanding when and where to apply it can significantly enhance production outcomes:
2.1 Protection During Conformal Coating ProcessesConformal coatings (e.g., acrylic, silicone, or parylene) protect electronic circuits from moisture, dust, and corrosion. However, certain areas—such as connectors, test points, or heat sinks—require exclusion from the coating. Self-adhesive tape provides a barrier, ensuring selective coating while maintaining component functionality.
2.2 Masking During Circuit Board Repairs or ModificationsWhen repairing or modifying printed circuit boards (PCBs), masking tape shields unaffected regions from overspray during re-coating. This prevents unintended coating on solder joints, pads, or components, maintaining board reliability.
2.3 Protection of Sensitive ComponentsElectronic devices contain vulnerable components like gold fingers (connectors), delicate sensors, or microchips. During spray painting of enclosures or exterior surfaces, tape application around these elements prevents paint infiltration, avoiding electrical shorts or performance degradation.
2.4 Aesthetic and Functional Masking in Device AssemblyIn smartphones, laptops, or wearable devices, tape is used to protect logos, buttons, or display edges during casing painting. This ensures sharp lines and color contrasts, enhancing product aesthetics while preserving functionality.
2.5 EMI/RFI Shielding ApplicationsSome tapes integrated with conductive materials can also act as temporary shields during喷漆 processes, preventing electromagnetic interference (EMI) or radio-frequency interference (RFI) during testing or assembly.
3. Technical Advantages Over Traditional Masking MethodsSelf-adhesive back blocking tape offers distinct advantages over manual masking techniques (e.g., hand-cut tapes or physical barriers):
Advantages | Description |
Precision | Uniform thickness and tear-resistant backing allow precise masking without fraying. |
Time Efficiency | Quick peel-and-stick application reduces masking time by up to 50% compared to manual methods. |
Residue-Free Removal | Specialized adhesive ensures no adhesive残留, avoiding costly post-processing. |
Versatility | Compatible with various喷漆 techniques (e.g., air spray, electrostatic spraying) and curing processes. |
Safety | Chemical resistance reduces risks of tape degradation or contamination during喷漆. |
4. Critical Considerations for Optimal UseTo maximize tape effectiveness, consider the following:
4.1 Surface PreparationClean and degrease surfaces before application to ensure strong adhesion. Dust or oils can compromise tape integrity, leading to paint seepage.
4.2 Application Technique
● Even Pressure: Apply tape using firm pressure to avoid air pockets, which can cause paint bleed.
● Edge Sealing: Overlap edges slightly to create a seamless barrier.
● Tear Protection: Use anti-static tools to prevent tape damage during handling.
4.3 Temperature and Humidity ControlHigh humidity can affect adhesive performance. Optimal application occurs in environments with 40-60% relative humidity and temperatures between 18-28°C.
4.4 Tape Removal Protocol
● Timely Removal: Peel tape immediately after喷漆 curing to prevent adhesive hardening.
● Angle and Speed: Slowly peel at a 45° angle to avoid lifting components or coatings.
5. Industries Benefiting from Self-Adhesive Spray Paint TapeBeyond electronics, this tape finds applications in:
● Automotive: Masking sensors or connectors during body喷漆.
● Aerospace: Protecting avionic components during exterior coatings.
● Medical Devices: Ensuring sterile coatings without contaminating interfaces.
● Industrial Machinery: Shielding control panels from paint overspray.
6. Case Study: Implementing Tape in a Smartphone Manufacturing LineA leading smartphone manufacturer faced challenges with paint bleed onto screen bezels and camera modules during casing喷漆. By integrating self-adhesive tape with automated masking systems, they achieved:
● Defect Reduction: Overspray errors decreased by 85%.
● Cycle Time Improvement: Masking time reduced from 2 minutes to 30 seconds per unit.
● Cost Savings: Eliminated costly post-spray cleaning processes.
7. Environmental and Health ConsiderationsModern tapes prioritize eco-friendly materials, often featuring:
● Low-VOC Adhesives: Reducing environmental impact during tape production.
● Recyclable Backings: Minimizing waste in electronics assembly.
● Safety Compliance: Meeting RoHS and REACH standards for chemical safety.
8. Future Trends in Spray Paint Tape TechnologyAdvancements include:
● Smart Tapes: Incorporating indicators (e.g., color-changing coatings) to confirm proper curing temperatures.
● 3D-Printable Masks: Customizable tape profiles for complex geometries.
● Nanotech Adhesives: Enhanced peelability and chemical resistance.
ConclusionSelf-adhesive back blocking spray paint tape is a cornerstone of modern electronics manufacturing, balancing protection, efficiency, and quality. From PCB coatings to device assembly, its precise masking capabilities prevent costly errors while maintaining component functionality. As electronics evolve toward miniaturization and complexity, this tape's adaptability will continue to drive innovation, ensuring clean, reliable coatings in every production scenario.
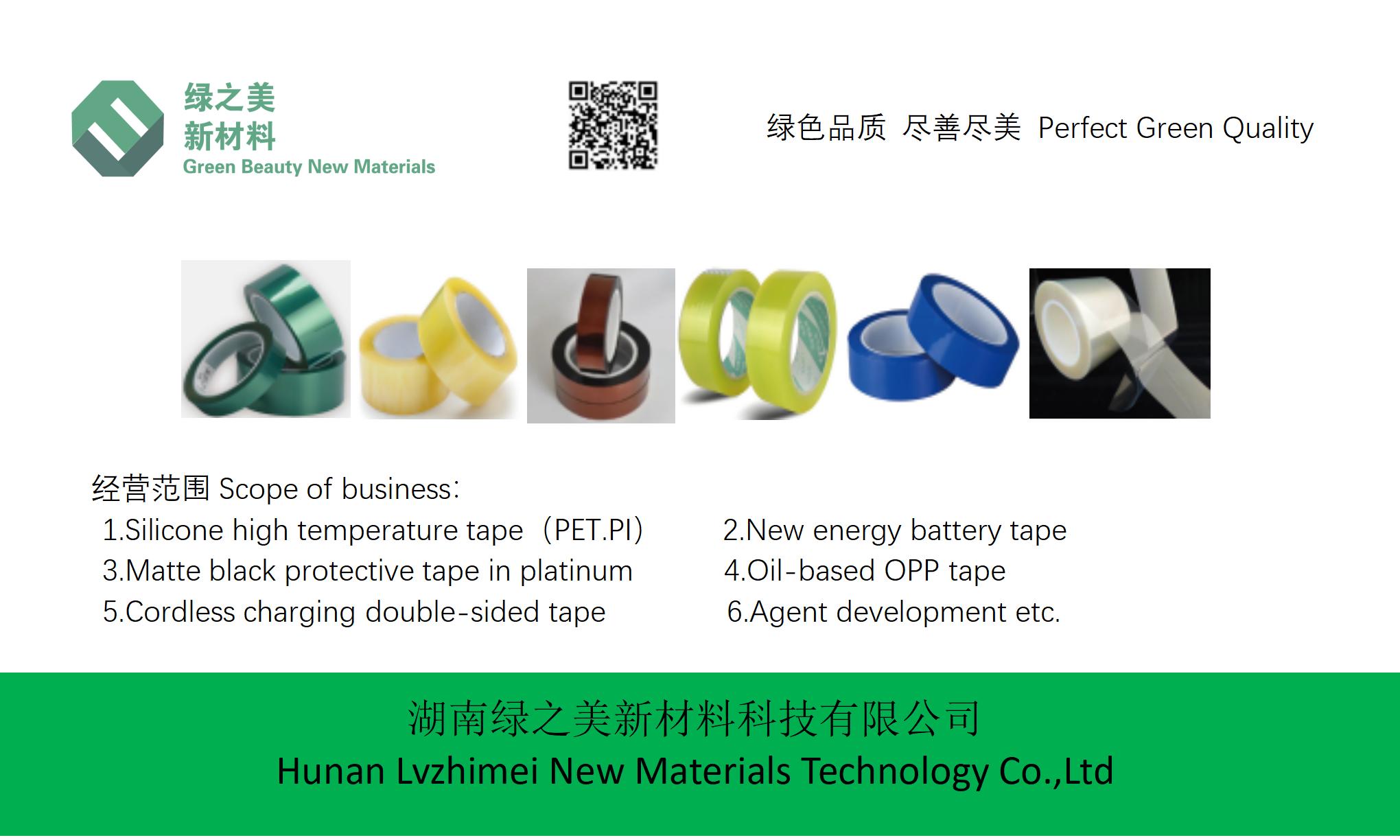