Which Types of Polyimide Tape Are Best for Circuit Board AssemblyURL: https://www.lvmeikapton.com/Title: Which Types of Polyimide Tape Are Best for Circuit Board AssemblyDescription: Identify the top polyimide tape options for circuit board manufacturing, focusing on thermal resistance, adhesion, and insulation.Keywords: Circuit board assembly, Polyimide tape types, Thermal resistance, Adhesion, Insulation
Which Types of Polyimide Tape Are Best for Circuit Board Assembly
Circuit board assembly is a complex process that demands materials with exceptional thermal resistance, adhesion, and electrical insulation properties. Polyimide tape, also known as Kapton tape, is a versatile solution widely used in this industry due to its robust performance under extreme conditions. This article aims to explore the best types of polyimide tape for circuit board manufacturing, highlighting their key features, applications, and performance metrics.
1. Understanding Polyimide Tape: Core Properties and ApplicationsPolyimide tape is fabricated using polyimide film (PI) as the base material, coated with high-performance silicone pressure-sensitive adhesive (PSA). This combination imparts several critical advantages:
● Thermal Resistance: Capable of enduring temperatures up to 300°C, ideal for processes like wave soldering and reflow ovens.
● Electrical Insulation: H-grade insulation, protecting circuits from short circuits and electrical arcing.
● Chemical Resistance: Resistant to acids, alkalis, and solvents, ensuring stability in harsh environments.
● Ease of Processing: Excellent die-cutting and shearing properties, suitable for automated manufacturing.
2. Top Polyimide Tape Types for Circuit Board Assembly
2.1 PI Material High-Temperature Resistant 300 TapeThis tape is a cornerstone in circuit board assembly, particularly for wave soldering and thermal protection. Key features include:
● Temperature Range: Up to 300°C continuous exposure, withstanding soldering temperatures.
● Adhesion Strength: Secure bonding to PCB components without slipping during thermal cycles.
● Residue-Free Removal: After soldering, the tape剥离 easily without leaving adhesive residue, maintaining board cleanliness.
● Application: Protecting gold fingers, SMT components, and delicate circuit traces from molten solder.
Table 1: Technical Specifications of PI 300 Tape
Model | Base Material | Adhesive Type | Thickness (mm) | Adhesion (N/25mm) | Max Temp (°C) |
YC-2515 | PI Film | Silicone | 0.04 | 4 | 260 |
YC-2525 | PI Film | Silicone | 0.05 | 5 | 260 |
YC-5030 | PI Film | Silicone | 0.08 | 5.5 | 260 |
2.2 Adhesive PET Material High-Temperature TapeFor applications requiring quick application without additional bonding agents, adhesive PET tapes offer convenience. Features include:
● Self-Adhering PET Layer: Simplifies application, reducing assembly time.
● Thermal Range: Effective up to 200°C, suitable for medium-temperature processes.
● Flexibility: Conforms to irregular surfaces, ideal for wrapping wires and cables.
● Cost-Effective: Balances performance and affordability for mass production.
2.3 Self-Adhesive Back Blocking Spray Paint TapeDuring conformal coating or spray painting, this tape ensures precise masking while preventing overspray. Advantages include:
● High Adhesion: Secures tape edges during spraying, minimizing bleed-through.
● Easy Removal: Post-coating, tape peels cleanly without damaging coatings.
● Precision Masking: Ideal for protecting sensitive components during finishing processes.
2.4 Lvmeikapton Insulating TapeSpecialized for high-voltage environments, Lvmeikapton tape excels in electrical insulation:
● H-Grade Insulation: Meets stringent electrical safety standards.
● Flame Retardant: Inhibits fire propagation in case of electrical faults.
● Low Static Properties: Prevents electrostatic discharge (ESD) in sensitive circuits.
● Application: Transformers, relay coils, high-power PCBs, and motor insulation.
2.5 Specialty Variants: Flame Retardant and Low-Static TapesAdvanced polyimide tapes address niche requirements:
● Flame Retardant (FR) Tape: Incorporates additives to self-extinguish fires, crucial for safety-critical electronics.
● Low-Static Tape: Designed for environments prone to ESD, ensuring static dissipation rather than accumulation.
● Ultra-Thin Types: Models like 25μm thickness offer flexibility in tight spaces without compromising thermal resistance.
3. Key Performance Metrics: Selecting the Optimal Tape
Thermal Resistance: For wave soldering (≥260°C) and reflow ovens, choose tapes with max temps exceeding process limits.Adhesion Strength: Higher N/25mm values ensure tape remains fixed during thermal cycling and handling.Residue-Free Removal: Critical for avoiding solder mask contamination and maintaining board reliability.Insulation Grade: H-class tapes are standard, but specialized applications (e.g., high-voltage transformers) may require additional certifications.
4. Application Examples in Circuit Board Manufacturing
4.1 Wave Soldering ProtectionPI 300 tape is wrapped around PCB edges and gold fingers to prevent solder bridging. Its high-temperature tolerance ensures tape integrity during solder immersion.
4.2 SMT Component ProtectionDuring reflow soldering, tape shields heat-sensitive components from oven temperatures, avoiding thermal stress-induced failures.
4.3 Transformer and Coil InsulationLvmeikapton tape’s electrical insulation properties protect coils from short circuits, enhancing transformer longevity.
4.4 Conformal Coating MaskingSelf-adhesive spray paint tape creates precise boundaries, preserving exposed pads for soldering while coating other areas.
5. Technical Considerations and Best Practices
● Thickness Selection: Thicker tapes (e.g., 0.08mm) offer better mechanical protection but may hinder flexibility. Ultra-thin options suit dense layouts.
● Die-Cutting Precision: Automated processes require tapes with consistent coating thickness (±2.5μm) to prevent cutting defects.
● Environmental Compliance: Ensure tapes meet RoHS and halogen-free standards for global market compatibility.
6. Market Trends and Future DevelopmentsAs electronics evolve towards miniaturization and higher power densities, polyimide tapes are advancing:
● Nano-Coatings: Enhancing thermal conductivity and surface smoothness.
● Bio-Based Adhesives: Eco-friendly alternatives reducing environmental impacts.
● Intelligent Tapes: Embedded sensors for real-time thermal monitoring during assembly.
7. ConclusionPolyimide tapes are indispensable in circuit board assembly, offering a balance of thermal resilience, adhesion, and insulation. Selecting the right type—whether PI 300 tape for soldering, adhesive PET for efficiency, or Lvmeikapton for high-voltage protection—optimizes manufacturing outcomes while ensuring long-term component reliability. As technology demands grow, innovated polyimide solutions will continue to drive advancements in electronics assembly.
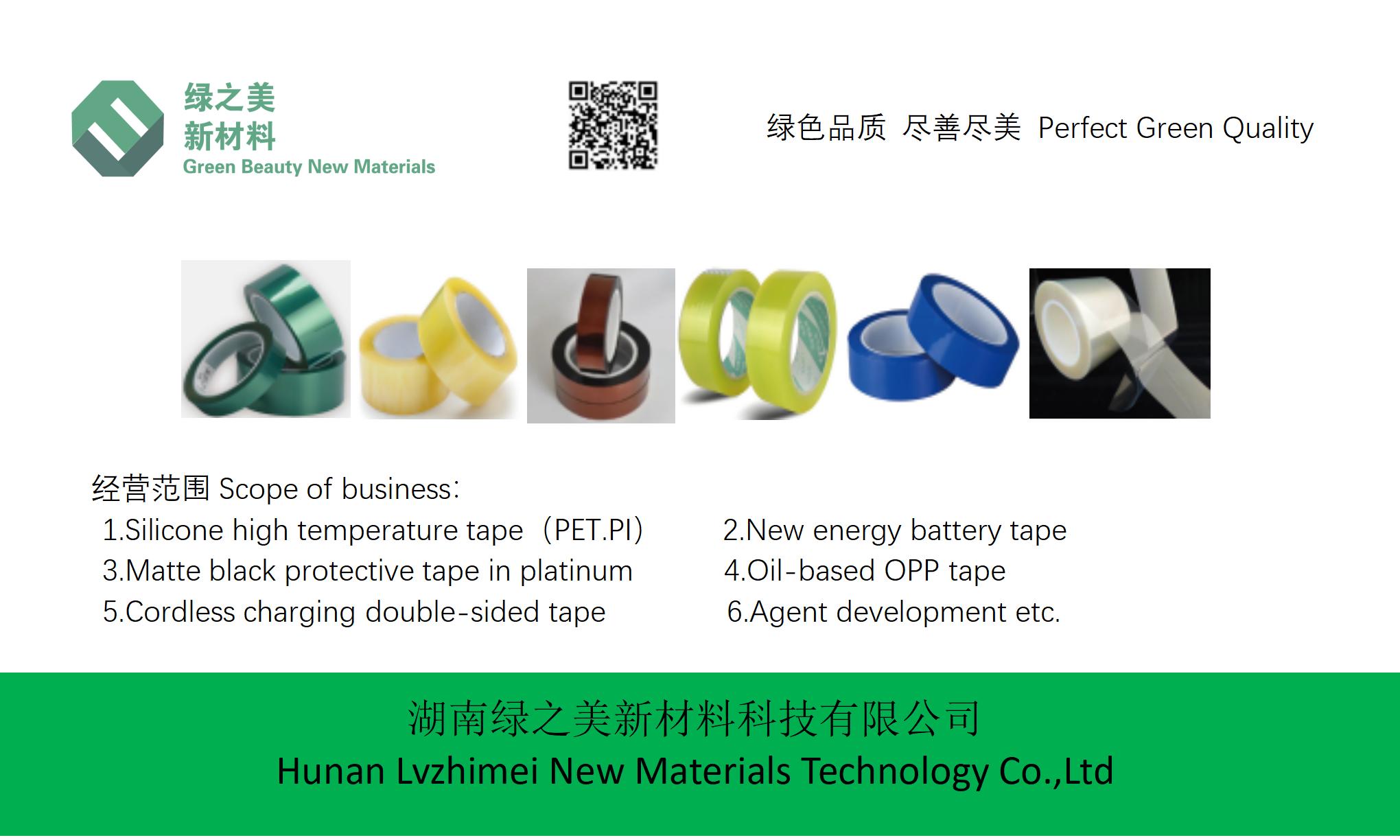