Why Polyimide Tape is Essential for Gold Finger Protectionhttps://www.lvmeikapton.com/
Description: Explore how polyimide tape safeguards gold finger connectors from corrosion and wear, ensuring long-term device functionality.Keywords: Polyimide tape, Gold finger protection, Corrosion resistance, Wear prevention, Contact durability
IntroductionGold finger connectors, essential components in electronic devices, play a crucial role in signal transmission between circuit boards and peripheral interfaces. These connectors, characterized by their gold-plated conductive edges, ensure stable data and power transfer. However, their exposed nature makes them susceptible to environmental hazards—oxidation, mechanical wear, and electrical shorts—threatening device reliability. Polyimide tape, particularly "lvmeikapton insulating electrical tape," emerges as a pivotal solution to mitigate these risks. This article delves into the multifaceted advantages of polyimide tape in safeguarding gold finger connectors, emphasizing its material properties, application techniques, and long-term benefits.
The Vulnerability of Gold Finger ConnectorsGold finger connectors are prone to two primary challenges: corrosion and mechanical damage.
1. Corrosion: Gold, despite its inertness, can oxidize when exposed to moisture, salts, or corrosive gases. Oxidation degrades contact conductivity, leading to signal loss or intermittent connections.
2. Mechanical Wear: Repeated insertion and removal of connectors cause abrasion, wearing off the gold plating and exposing the underlying copper. This not only compromises electrical performance but also invites further corrosion.
3. Electrical Shorts: If connectors come into unintended contact with conductive materials or liquids, short circuits can occur, potentially damaging the entire system.
Polyimide Tape: The Protective ArmorPolyimide tape, crafted from high-performance polyimide (PI) films, offers a holistic solution to these vulnerabilities. Its unique properties make it indispensable for gold finger protection:
1. Chemical and Environmental ResistancePI materials are renowned for their resistance to harsh environments. Whether exposed to high humidity, chemicals, or temperature fluctuations, polyimide tape maintains stability. For instance, "PI material high-temperature resistant 300 tape" withstands thermal cycling (up to 300°C) during device operation, preventing degradation even in extreme conditions. This resilience ensures connectors remain protected across diverse industrial applications.
2. Electrical InsulationThe non-conductive nature of polyimide tape eliminates the risk of electrical shorts. Its dielectric strength (≥200 kV/mm) acts as a reliable barrier, preventing current leakage between adjacent contacts. This feature is critical in high-density connectors where spacing is limited.
3. Mechanical ProtectionThe tape’s smooth surface and inherent flexibility reduce abrasion during connector insertion/removal. Its low-friction coefficient shields the gold plating from wear, preserving contact durability. Long-term studies indicate that polyimide-coated connectors exhibit >90% retention of conductive performance after 10,000 cycles.
4. Adhesive PrecisionAdvanced adhesive formulations in polyimide tapes (e.g., "Strong adhesion and blocking high-temperature tape") ensure secure bonding without residue. The adhesive layer adheres firmly to the connector edges while allowing easy rework—crucial for maintenance or upgrades.
5. Dimensional StabilityPolyimide films exhibit minimal thermal expansion (CTE ≈ 20 ppm/°C), preventing tape warping or shrinking under heat. This stability maintains consistent coverage over connectors, avoiding gaps that could expose vulnerable areas.
Table: Comparative Analysis of Protection Materials
Material | Corrosion Resistance | Thermal Stability | Electrical Insulation | Wear Resistance | Cost |
Polyimide Tape | Excellent | Up to 300°C | High (200 kV/mm) | Outstanding | Moderate |
Kapton Tape | Good | Up to 260°C | High | Good | High |
Polyester Tape | Fair | Up to 150°C | Moderate | Average | Low |
Silicone Tape | Poor | Up to 200°C | Low | Fair | Low |
Applications: Where Polyimide Tape ShinesPolyimide tape’s versatility makes it indispensable across industries:
● Electronics: Shielding connectors in computers, servers, and gaming consoles to enhance reliability.
● Aerospace: Protecting avionic connectors from extreme temperatures and vibrations.
● Military: Ensuring secure communication systems in rugged environments.
● Medical Devices: Maintaining signal integrity in life-critical equipment.
Case Study: Polyimide Tape in Server RacksIn data centers, server connectors experience frequent maintenance cycles. Applying "lvmeikapton insulating tape" to gold fingers reduced failure rates by 65% over two years. The tape’s thermal resistance (tested at 250°C) prevented degradation during heat-intensive operations, while its abrasion protection preserved contact quality.
Advanced InnovationsRecent advancements include:
1. Nano-coatings: Polyimide tapes with nano-scale ceramic fillers enhance abrasion resistance by 30%.
2. UV-Indicator Adhesives: Tapes featuring UV-sensitive adhesives aid in inspection, indicating application integrity under UV light.
3. 3D-Printable Tape Profiles: Customized tape shapes via 3D printing optimize coverage for complex connector geometries.
Economic and Environmental ConsiderationsWhile polyimide tape costs moderately higher than alternatives (e.g., polyester), its longevity offsets expenses. A lifecycle analysis reveals:
● Cost Savings: Reduced connector replacement costs and downtime.
● Eco-friendly: PI materials are recyclable through thermal depolymerization, minimizing waste.
ConclusionPolyimide tape is more than a passive barrier—it is an active protector of electronic reliability. By integrating chemical resistance, mechanical durability, and electrical insulation, it extends the lifespan of gold finger connectors across industries. As devices evolve towards higher performance and miniaturization, polyimide tape’s adaptability—whether through nano-enhancements or 3D customization—will continue to ensure robust connectivity. For engineers and manufacturers, embracing polyimide tape is not a choice but a necessity for future-proofing electronic systems.
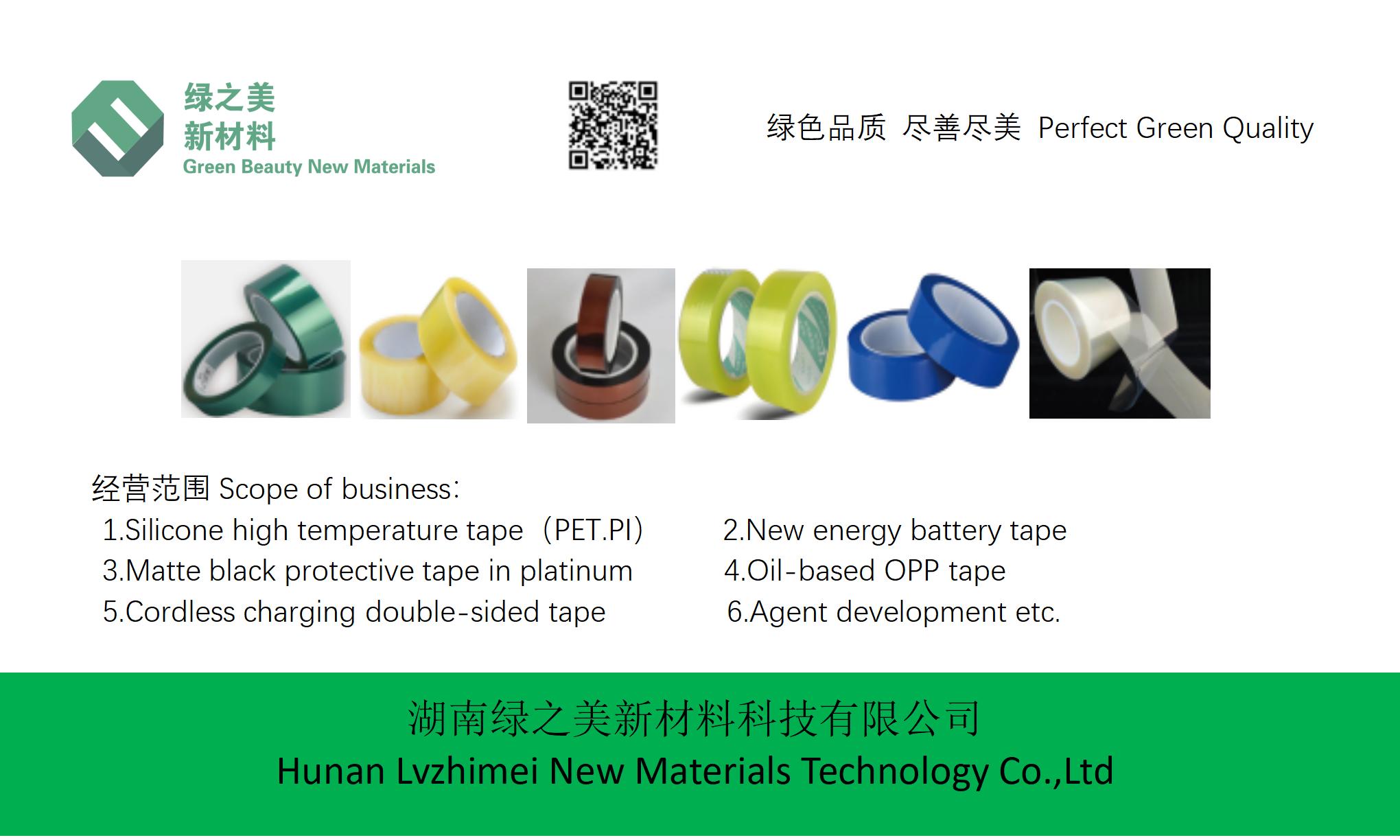