What Are the Uses of Kapton Tape in Electronics?
By [Your Name]Date: May 23, 2025
IntroductionKapton tape, a high-performance polyimide (PI) tape developed by DuPont, has become a cornerstone in the electronics industry. Renowned for its exceptional thermal resistance, electrical insulation, and chemical stability, this versatile material offers unparalleled protection and reliability in various electronic applications. Derived from the same polyimide family as Kapton film—a flagship product known for its robust properties—Kapton tape combines adhesive backing with the inherent advantages of PI, making it indispensable in both professional and DIY electronics contexts. This article delves into the multifaceted uses of Kapton tape, exploring its applications, technical advantages, and how it outperforms conventional tapes in demanding environments.
1. Overview of Kapton TapeKapton tape is characterized by its unique composition: a thin polyimide film layer laminated with a pressure-sensitive adhesive (PSA) on one side. This design enables it to adhere firmly to surfaces while maintaining the core properties of PI. The tape’s thermal stability allows it to withstand temperatures up to 260°C (short-term) and continuous operation at 220°C, surpassing most adhesive tapes that degrade or lose adhesion at high temperatures. Additionally, its electrical insulation properties, with a dielectric breakdown strength exceeding 100 kV/mm, ensure safety in high-voltage environments. Kapton tape’s flexibility and resistance to abrasion further enhance its usability, making it suitable for wrapping, splicing, and masking tasks.
Key Features:
● Self-adhesive backing for easy application.
● Low thermal expansion coefficient, minimizing dimensional changes.
● Chemical resistance to solvents, acids, and alkalis.
● Flame retardancy (UL94 V-0 rating).
● Excellent dimensional stability under stress.
Table 1: Key Properties of Kapton Tape
Property | Value/Description |
Temperature Range | -70°C to +260°C (short-term) |
Dielectric Strength | >100 kV/mm |
Tensile Strength | 200 N/cm |
Thermal Conductivity | 0.3 W/mK |
Flame Rating | UL94 V-0 |
2. Role in Circuit Board ProtectionCircuit boards, the nervous systems of electronic devices, are susceptible to thermal stress, moisture ingress, and mechanical damage. Kapton tape serves as a multi-functional shield in this context:
2.1 Masking for Soldering and ReworkDuring board assembly, Kapton tape acts as a temporary barrier to protect sensitive components or areas from soldering flux, reflow ovens, or wave soldering processes. Its high-temperature resistance ensures it remains stable up to 260°C, preventing tape degradation or adhesive residue. The tape’s easy peelability after cooling facilitates clean removal without damaging the board’s surface.
2.2 Thermal and Electrical InsulationKapton tape’s electrical insulation properties make it ideal for wrapping wires, coils, or traces prone to high voltages. In transformers, for instance, the tape is used as a layer separator to prevent short circuits. Its low thermal conductivity also helps dissipate heat, reducing the risk of thermal runaway in densely packed circuits. For example, “Brown circuit board high temperature tape” variants—specifically formulated with enhanced thermal resistance—are commonly applied to protect traces exposed to soldering or motor-driven heat.
2.3 Moisture and Chemical ProtectionIn environments with humidity or corrosive gases, Kapton tape’s hydrophobicity and chemical inertness create a barrier that safeguards circuits from degradation. For outdoor electronics or industrial equipment, this feature significantly extends component lifespans.
3. Industrial and DIY ApplicationsKapton tape’s utility extends across diverse sectors:
3.1 Manufacturing and Assembly
● Cable Management: Wrapping cables or wire harnesses to prevent chafing and EMI shielding.
● PCB Repair: Reinsulating damaged tracks or bridging gaps in circuits.
● LCD/LED Protection: Applying tape as a barrier against UV light or mechanical stress.
● Thermal Management: Securing heatsinks or thermal pads with adhesive tape, ensuring consistent heat transfer.
3.2 DIY Electronics and HobbiesEnthusiasts leverage Kapton tape for:
● Model-making: Insulating motors in RC vehicles or drones.
● Custom Circuitry: Prototyping temporary connections or protecting exposed wires.
● 3D Printing: Masking build platforms to prevent adhesion issues with certain filaments.
3.3 Specialty Uses
○ Aerospace Electronics*: Kapton tape’s lightweight and flame retardancy meet stringent aviation standards.
● Medical Devices: Biocompatible variants ensure safe insulation in implantable or wearable tech.
4. Advantages Over Conventional TapesCompared to alternatives like acrylic or PVC tapes, Kapton tape offers:
4.1 DurabilityWhile standard tapes may peel, discolor, or lose adhesion under heat, Kapton maintains stability. For example, in automotive applications, Kapton tape remains functional in engine compartments exposed to prolonged heat, while others fail within weeks.
4.2 Long-term ReliabilityIts low outgassing (minimal volatile organic compounds) ensures no contamination in cleanroom environments. This is crucial in semiconductor manufacturing or aerospace electronics where contamination risks are severe.
4.3 Versatility in Extreme ConditionsKapton tape’s ability to function in cryogenic (-70°C) and high-temperature environments, coupled with resistance to radiation, makes it invaluable in space electronics or nuclear power equipment.
5. Technical Innovations and Future TrendsResearchers are advancing Kapton tape’s capabilities through:
● Nano-modification: Incorporating nanoparticles to enhance mechanical strength and conductivity.
● Thermal Interface Materials: Developing tape with microstructured surfaces for improved heat transfer.
● Smart Tape Variants: Embedding sensors or conductive paths for real-time monitoring.
DuPont’s recent advancements include a “Self-adhesive back blocking spray paint tape” that combines Kapton’s thermal resistance with a specialized adhesive designed to block spray paints during component coating. This innovation streamlines manufacturing processes in automotive and aerospace industries, reducing masking time and costs.
ConclusionFrom safeguarding circuit boards to enabling cutting-edge aerospace applications, Kapton tape’s synergy of thermal resilience, electrical insulation, and durability positions it as a critical tool in modern electronics. As technological demands escalate—toward miniaturization, higher voltages, and extreme environments—Kapton tape’s continuous evolution ensures its relevance. Whether in industrial factories or hobbyist workshops, this unassuming tape plays a silent yet essential role in powering our digital world.
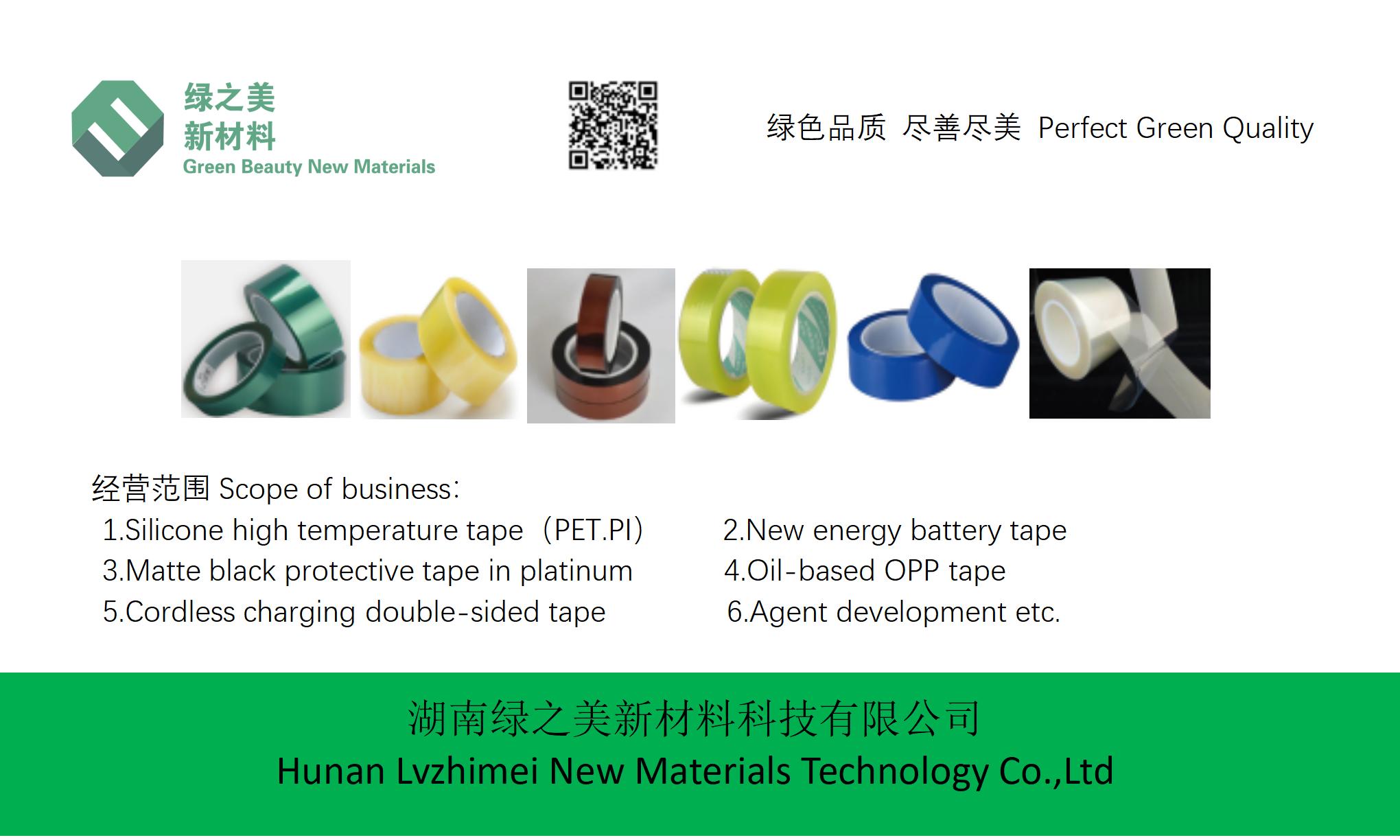