How Does Gold Finger Electronics Polyimide Tape Work?
Introduction to Polyimide Tape in ElectronicsPolyimide tape, commonly referred to as "Gold Finger Electronics Polyimide Tape" or "Kapton Tape," is a high-performance adhesive material specifically designed for electronic applications. This tape is constructed with a polyimide film substrate and coated with advanced silicone pressure-sensitive adhesive (PSA). Its unique properties, including exceptional thermal resistance, chemical stability, electrical insulation, and mechanical strength, make it indispensable in modern electronics manufacturing and protection. Understanding how this tape works requires a deep dive into its material composition, functional properties, and application mechanisms.
Key Properties: The Core of Adhesive PET Material High Temperature TapeThe effectiveness of Gold Finger Electronics Polyimide Tape hinges on its key properties, which are carefully engineered to meet stringent industrial requirements. The primary components are:
1. Polyimide Film Substrate:
The base material is a polyimide film (PI), a thermoplastic polymer with an imide ring structure. PI exhibits remarkable thermal stability, enduring temperatures ranging from -269°C to 400°C without degradation. This property is critical in environments where components are subjected to high-temperature processes like wave soldering, reflow soldering, or thermal cycling. Additionally, PI offers excellent electrical insulation (H-class), UV resistance, and low outgassing, preventing contamination in vacuum environments.
2. Silicone Pressure-Sensitive Adhesive (PSA):
The adhesive layer is formulated with silicone-based PSA, providing strong adhesion to various surfaces (e.g., metals, plastics, ceramics) without requiring activation by heat or solvents. This adhesive system ensures high peel strength, maintaining its bonding integrity even after prolonged exposure to high temperatures. A notable feature is its "clean release" property—after removal, it leaves no residual adhesive, crucial for delicate electronic components.
3. Additional Enhancements:
Some tapes are modified with fluoropolymer release coatings or anti-static treatments to prevent charge accumulation during handling. Flame-retardant variants further enhance safety in applications prone to thermal hazards.
Table 1: Technical Specifications of Typical Polyimide Tapes
Model | Substrate Thickness (mm) | Adhesion (N/25mm) | Temperature Range (°C) | Features |
YC-2515 | 0.045 | 4.5 | -65 to +260 | Standard adhesive, ROHS |
YC-5030 | 0.08 | 5.5 | -65 to +300 (short-term) | High peel strength, no residue |
YC-FR75 | 0.12 | 6.5 | -70 to +260 | Flame retardant, low static |
Applications in PCB and Flexible CircuitsThe versatility of polyimide tape shines in printed circuit board (PCB) fabrication and flexible electronics. Key applications include:
1. Wave Soldering Protection:
During wave soldering, components on PCBs are exposed to molten solder at ~250°C. Polyimide tape is applied to "mask" sensitive areas (e.g., gold fingers, connectors) to prevent solder bridging or contamination. Its thermal barrier ensures these regions remain intact.
2. Gold Finger Protection:
"Gold fingers" (edge connectors) on memory cards or PCBs require electrical conductivity and mechanical durability. Polyimide tape acts as a shield against wear, corrosion, and ESD damage, preserving contact reliability.
3. Flexible Circuit Insulation:
In flexible printed circuits (FPCs), polyimide tape reinforces thin polyimide films, enhancing dimensional stability during bending cycles. It prevents conductor exposure and short circuits in wearable devices or automotive electronics.
4. Transformer and Motor Coils:
High-voltage transformers and motors demand robust insulation. The tape's H-class insulation and resistance to solvents make it ideal for winding insulation and terminal protection, reducing electrical failures.
Benefits of PI Material High Temperature Resistant 300°C TapeBeyond its core properties, polyimide tape offers several advantages over traditional insulating materials:
● Extreme Temperature Tolerance:
Unlike acrylic or rubber-based tapes that degrade at >150°C, polyimide tape maintains stability up to 300°C (short-term). This resilience is vital in aerospace, automotive, and industrial settings.
● Chemical Resistance:
It withstands exposure to acids, alkalis, solvents, and oils, ensuring long-term performance in harsh environments.
● Low Dielectric Constant:
Its electrical properties (low capacitance, high breakdown voltage) support high-frequency signal transmission in RF circuits.
● Ease of Processing:
The tape's smooth surface and precise thickness (±2.5μm) allow clean die-cutting and automated application in SMT lines, minimizing production errors.
Comparison with Other Insulating Tapes
Property | Polyimide Tape | Silicone Tape | Acrylic Tape |
Max Temp. Range | -65°C to +300°C | -60°C to +200°C | -40°C to +150°C |
Adhesion Residue | No residue | Moderate residue | Some residue |
Chemical Resistance | Excellent | Good | Limited |
Flexibility | Good | Excellent | Fair |
Cost | High | Medium | Low |
Table 2: Comparative AnalysisThis table underscores polyimide tape's superiority in high-temperature and chemically aggressive environments, despite its higher cost.
Mechanisms of Protection: Adhesion and Thermal BlockingThe tape's functionality is governed by two primary mechanisms:
1. Strong Adhesion and Blocking High Temperature Tape:
The silicone PSA creates a firm seal, preventing solder or contaminants from penetrating beneath the tape during wave soldering. The adhesive's thermosetting behavior further strengthens bonds at elevated temperatures, ensuring no slippage.
2. Thermal Conduction Barrier:
Polyimide's low thermal conductivity (0.2-0.3 W/mK) acts as a heat sink, dissipating heat away from protected components while maintaining structural integrity. This property is critical in protecting heat-sensitive substrates like FPCs during thermal curing processes.
Real-World Case Study: Automotive ElectronicsIn modern vehicles, engine control units (ECUs) operate in extreme temperatures (-40°C to +150°C). Polyimide tape is used to insulate wire harnesses and sensor connectors, preventing short circuits due to vibration or thermal cycling. A study by a leading automotive manufacturer demonstrated a 30% reduction in electrical failures after integrating polyimide tape-based insulation systems.
Environmental Considerations and SustainabilityWhile polyimide tape excels in performance, its environmental impact is mitigated through design choices. Many tapes are:
● ROHS and Halogen-Free: Compliant with global environmental regulations, avoiding hazardous materials.
● Recyclable Substrate: Polyimide films can be repurposed through specialized recycling processes, reducing waste.
● Low-VOC Manufacturing: Adhesive formulations minimize volatile organic compound emissions during production.
Future Trends and InnovationsAs electronics evolve towards miniaturization and high-power densities, polyimide tape technology is advancing. Research focuses on:
1. Nanostructured Adhesives: Enhancing peel strength and thermal conductivity using nanofillers.
2. Self-Healing Polymers: Developing tapes that autonomously repair minor defects under thermal stimulation.
3. Integrated Sensors: Embedding temperature or strain sensors within the tape for real-time monitoring.
ConclusionGold Finger Electronics Polyimide Tape is a cornerstone of modern electronics, enabling reliability in the harshest environments. Its synergy of thermal resistance, adhesive strength, and electrical insulation safeguards critical components across industries. As technological demands escalate, continuous innovation in this material will further solidify its role as an essential engineering solution. Understanding its mechanisms and applications empowers designers to optimize electronic systems for durability and performance.
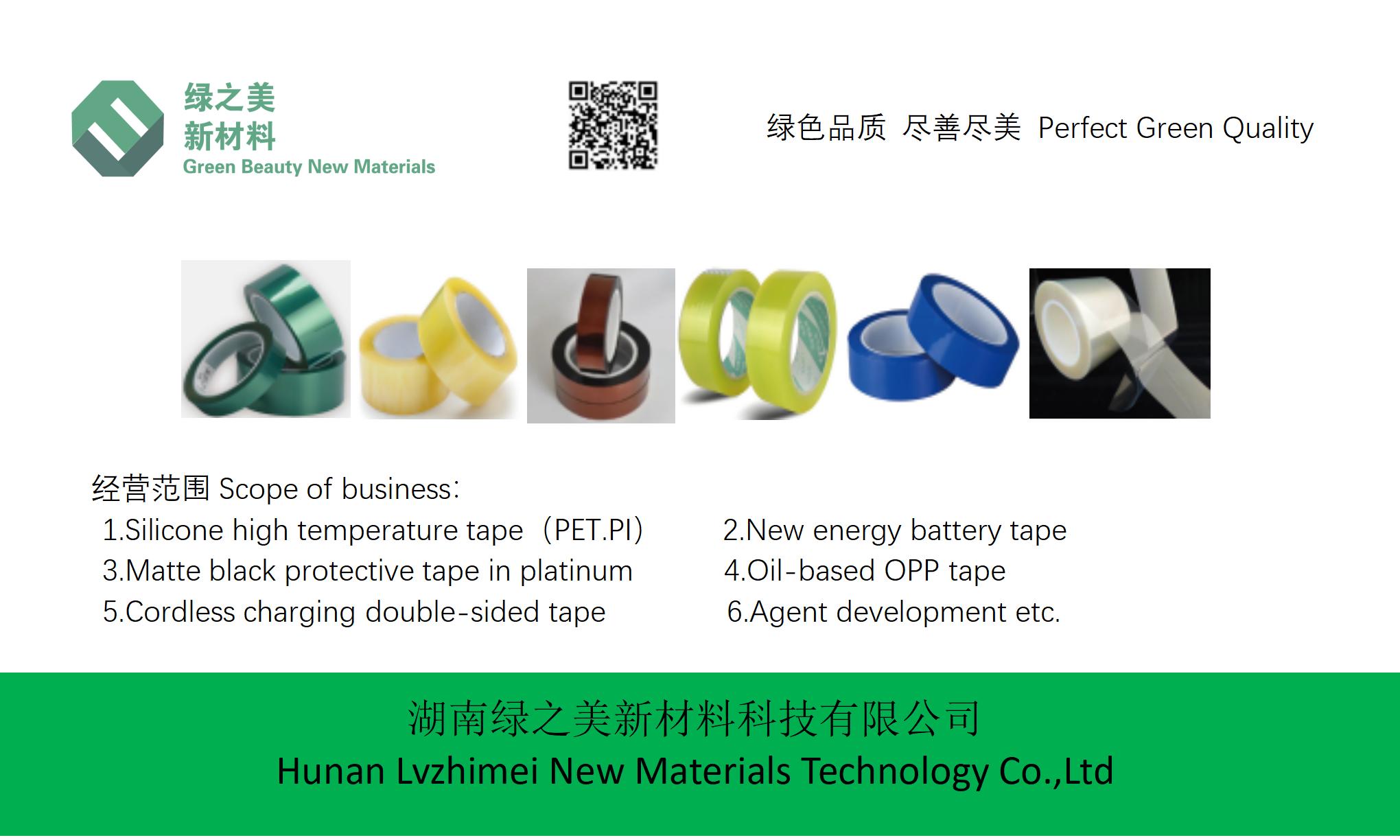