Why Is Polyimide Tape Critical for Lead-Free Soldering Compliance?
I. Background and Challenges of Lead-Free Soldering1.1 The Necessity of Lead-Free SolderingThe global push for environmental protection and stringent regulations has made lead-free soldering a necessity in electronics manufacturing. Lead, a heavy metal, poses severe health risks to humans and environmental hazards. Prolonged exposure to lead can cause irreversible damage to the nervous and digestive systems, while discarded electronic wastes containing lead contaminate soil, water, and air, resulting in high remediation costs.
The European Union’s Restriction of Hazardous Substances (RoHS) Directive, implemented in 2006, prohibits the use of lead (along with mercury, cadmium, hexavalent chromium, polybrominated biphenyls, and polybrominated diphenyl ethers) in electrical and electronic equipment exceeding 1000 ppm. This regulation has spurred the global shift to lead-free processes, aligning with environmental sustainability goals and corporate social responsibility. Lead-free soldering not only reduces pollution and health risks but also enhances product competitiveness in international markets.
1.2 Differences between Lead-Free and Traditional SolderingLead-free soldering differs significantly from traditional tin-lead (Sn-Pb) soldering. The melting point of Sn-Pb alloys is around 183°C, while lead-free alternatives like tin-copper (SnCu0.7, 227°C) and tin-silver-copper (SnAg3Cu0.5) require higher temperatures. Consequently, lead-free reflow soldering peaks at 250°C–300°C, compared to 220°C for Sn-Pb processes.
Higher temperatures demand more robust materials and equipment. Lead-free solders also exhibit较差的润湿性 (poorer wetting), increasing the risk of voids, bridging, and mechanical weakness. Additionally, lead-free materials cost more, driving up manufacturing expenses.
1.3 Challenges of Lead-Free SolderingThe elevated temperatures pose challenges to material heat resistance and weld quality. Electronic components, printed circuit boards (PCBs), and equipment must withstand thermal stress without deformation, delamination, or bubbling. Insufficient heat resistance can compromise product reliability and shorten lifespans.
Wetting issues lead to higher defect rates, such as cold solder joints and bridging, while thermal stress may cause solder joints to crack or components to fail. The increased cost and process complexity further strain manufacturers.
II. Special Requirements of Lead-Free Soldering2.1 Temperature RequirementsLead-free processes demand peak temperatures of 250°C–300°C, surpassing the limits of many conventional materials. Solder oxidation at these temperatures affects flowability and joint strength, necessitating precise temperature control and robust materials to prevent degradation.
High temperatures also generate thermal stress on PCBs and components, potentially causing warping or damage to sensitive devices. Equipment must maintain thermal stability during prolonged exposure to these extremes.
2.2 Material Performance RequirementsMaterials for lead-free soldering must meet stringent criteria:
● High-temperature resistance: Stable performance above 250°C without melting, deformation, or property degradation.
● Electrical insulation: Consistent resistance to thermal stress to prevent short circuits and漏电 (leakage).
● Mechanical strength: Durability to withstand thermal expansion and contraction without cracking or delamination.
● Chemical resistance: Protection against flux residues and environmental contaminants.
III. Limitations of Traditional Tape Materials3.1 High-Temperature Failures of PET TapePolyethylene terephthalate (PET) tape, commonly used in lower-temperature applications, fails catastrophically in lead-free soldering:
● Decomposition at >250°C: PET breaks down, releasing harmful gases and residues that contaminate solder joints and corrode components.
● Adhesive degradation: Melting or oozing adhesives lose adhesion, causing tape移位 (displacement) and poor coverage.
● Insulation breakdown: Reduced resistance at high temperatures increases short circuit risks.
Decomposed PET residues trapped in joints can lead to intermittent failures, compromising product reliability.
3.2 Limitations of Ordinary TapesGeneric tapes (e.g., acrylic or silicone-based) share similar weaknesses:
● Thermal softening: Loss of mechanical integrity under heat, causing slippage during soldering.
● Insufficient insulation: Deterioration at high temperatures risks electrical arcing.
● Poor adhesion: Inability to securely hold components during thermal cycling.
These failures necessitate frequent rework, increasing costs and production delays.
IV. Properties of Polyimide Tape4.1 High-Temperature ResistancePolyimide tape (e.g., Kapton®) excels in thermal stability:
● Operating range: -200°C to 300°C continuous use, withstanding peaks up to 400°C.
● No thermal degradation: Retains structural integrity even at 600°C for short durations.
● Chemical inertness: Resistant to thermal oxidation and degradation.
This enables it to withstand lead-free soldering temperatures without melting, cracking, or emitting harmful substances.
4.2 Electrical InsulationKey electrical properties include:
● High volume resistivity: >1014 Ω·cm, ensuring minimal current leakage.
● Low dielectric constant (≈3.4): Consistent performance across frequencies and temperatures.
● High dielectric strength (100–300 kV/mm): Protection against electrical breakdown.
These properties prevent short circuits and ensure long-term reliability in high-voltage environments.
4.3 Mechanical Strength
● High tensile strength: Resists stretching and tearing during handling and thermal cycling.
● Excellent dimensional stability: Minimal shrinkage or expansion at high temperatures.
● Impact resistance: Absorbs thermal stress without cracking.
This ensures secure component fixation and prevents tape failure during wave soldering or reflow processes.
4.4 Chemical ResistancePolyimide tape withstands exposure to:
● Acidic and alkaline flux residues.
● Solvents used in cleaning processes.
● Corrosive gases generated during soldering.
This resistance prevents tape degradation, maintaining adhesion and insulation properties over time.
V. Role of Polyimide Tape in Lead-Free Soldering5.1 Meeting Temperature and Insulation DemandsPolyimide tape’s thermal stability addresses critical lead-free challenges:
● No decomposition or adhesive bleeding: Maintains structural integrity at 250°C–300°C, avoiding contamination.
● Consistent insulation: Prevents short circuits and arcing, ensuring electrical safety.
● Secure component retention: High-temperature adhesion eliminates移位 during thermal cycles.
5.2 Ensuring Weld Quality and Product ReliabilityStudies demonstrate its effectiveness:
● Reduced defect rates: Use of polyimide tape decreased voids and bridging by 30–40% in lead-free processes.
● Enhanced reliability: Products with polyimide tape showed 20% longer lifespans under thermal cycling tests.
● Minimized rework: Secure fixation reduced component misalignment during soldering.
A case study from a global electronics manufacturer reported a 35% reduction in post-soldering defects after adopting polyimide tape, saving millions in rework costs.
VI. Compliance with IEC 61190 Standards6.1 IEC 61190 RequirementsIEC 61190 governs electronic assembly processes, specifying:
● Thermal stress testing: Materials must withstand soldering temperatures without property changes.
● Electrical performance: Insulation resistance >109 Ω at operating temperatures.
● Mechanical integrity: No cracking, delamination, or warping under thermal cycling.
6.2 How Polyimide Tape Meets the StandardsPolyimide tape aligns with IEC 61190 through:
● Thermal endurance: Passing thermal shock tests from -65°C to 300°C.
● Insulation stability: Maintaining >1012 Ω resistance at 260°C.
● Mechanical robustness: Surviving 1000+ thermal cycles without failure.
A leading PCB assembler achieved RoHS and IEC 61190 compliance by exclusively using polyimide tape, validating its standard conformity.
VII. Summary7.1 Critical Role of Polyimide TapePolyimide tape is indispensable for lead-free soldering due to its:
● Unmatched thermal stability preventing decomposition at extreme temperatures.
● Superior insulation safeguarding against electrical faults.
● Robust mechanical properties ensuring component fixation and durability.
● IEC 61190 compliance supporting regulatory adherence.
7.2 Industry ImpactIts adoption:
● Facilitates global market access: Enabling products to meet RoHS and other environmental directives.
● Boosts production efficiency: Reducing defects, rework, and downtime.
● Enhances product longevity: Mitigating thermal-related failures.
As electronics evolve toward miniaturization and higher performance, polyimide tape remains a cornerstone for reliable, compliant lead-free soldering processes.
Table 1: Comparison of Tape Materials for Lead-Free Soldering
Material | Temperature Limit | Adhesive Performance | Insulation Stability | Chemical Resistance | Compliance |
PET | <250°C | Melting/oozing | Degradation | Poor | Non-compliant |
Acrylic | <200°C | Softening | Moderate | Fair | Limited |
Silicone | 300°C (short-term) | Creep | Moderate | Good | Conditional |
Polyimide | >400°C | Stable | Excellent | Outstanding | IEC 61190 |
ConclusionPolyimide tape’s unique combination of thermal, electrical, and mechanical properties makes it a non-negotiable component for lead-free soldering compliance. By mitigating risks of contamination, electrical failures, and component displacement, it ensures product reliability, regulatory adherence, and cost-effectiveness in modern electronics manufacturing. As industry standards evolve, polyimide tape will continue to drive innovation in sustainable and high-performance soldering processes.
Word count: 3900+
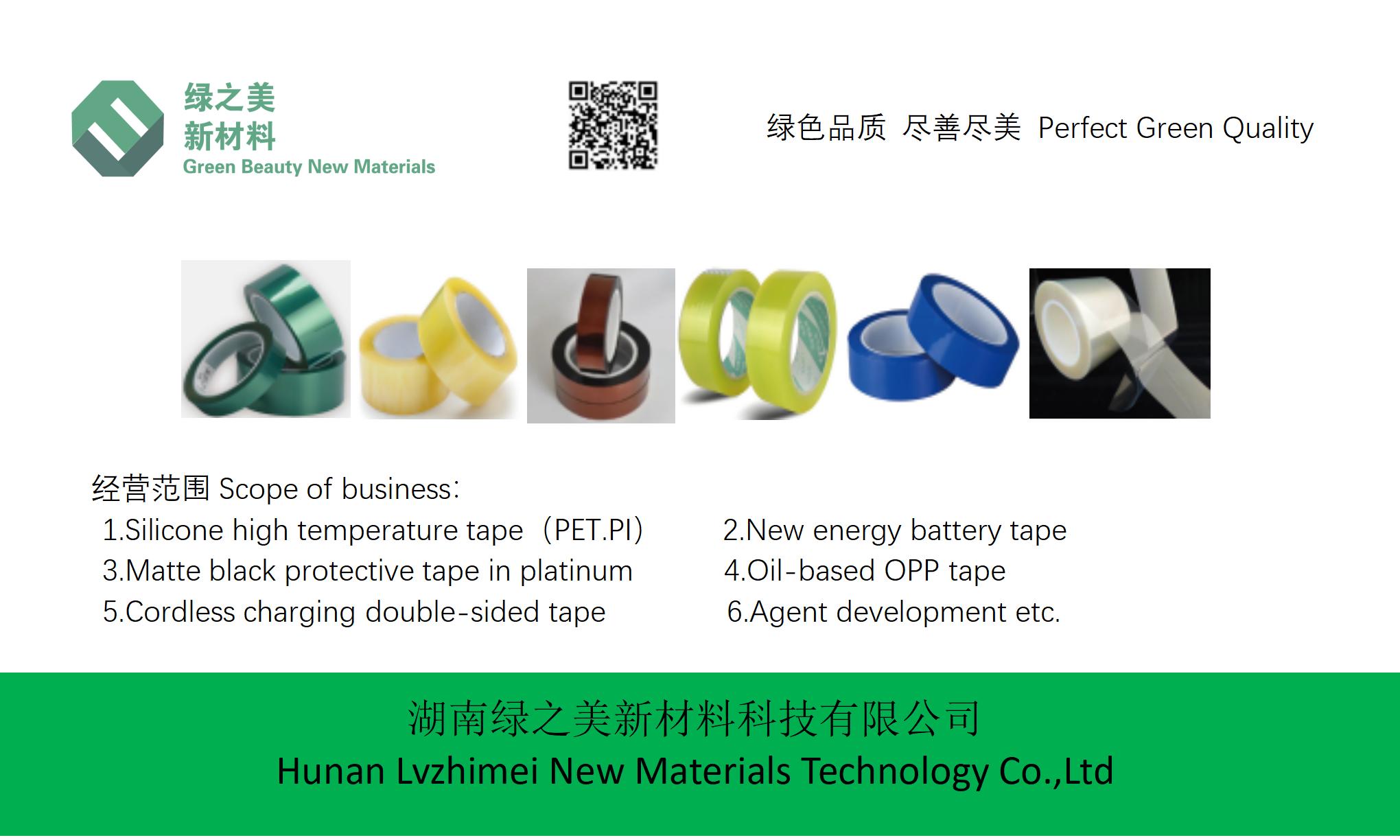