When Should You Replace Standard Masking Tapes with Polyimide Variants?
I. Importance and Overview of Masking Tapes
1.1 Role of Masking Tapes in Industrial Production
Masking tapes play a crucial role in various industrial processes. In spray painting, they protect surfaces from unintended coatings, ensuring precise paint boundaries and flawless finishes. During welding, they prevent spatters from damaging adjacent areas, reducing post-processing efforts and maintaining weld quality. In printed circuit board manufacturing, they shield non-printed regions, avoiding short circuits. Widely used in automotive, electronics, construction, and other sectors, masking tapes are essential for maintaining product quality and efficiency.
1.2 Common Types and Performance Characteristics of Standard Masking Tapes
Standard masking tapes include paper-based tapes (cost-effective but vulnerable to moisture and heat), PE tapes (waterproof but limited in heat resistance), PVC tapes (flexible but prone to deformation at high temperatures), and PET tapes (high strength but costly). While suitable for low-temperature applications (<180°C), they struggle in harsh environments, often suffering from adhesive degradation, tape deformation, or chemical corrosion, leading to unreliable protection.
II. Performance Advantages of Polyimide Tapes
2.1 Superior Heat Resistance
Polyimide tapes excel in high-temperature scenarios. Withstanding up to 400°C short-term and 260°C long-term, they maintain adhesive strength and structural integrity even in lead-free soldering (exceeding 180°C). Unlike standard tapes that may melt or lose adhesion, polyimide tapes ensure stable coverage, preventing solder splashes and contamination, crucial for electronics and automotive assemblies.
2.2 Chemical Stability
These tapes exhibit exceptional resistance to aggressive chemicals (e.g., strong acids, alkalis, fluxes). Their dense molecular structure shields surfaces from corrosive attacks, ensuring longevity in electroplating baths or chemical etching processes. Industries such as semiconductor manufacturing and chemical engineering rely on polyimide tapes to avoid tape dissolution and maintain process reliability.
2.3 Mechanical Strength
Polyimide tapes boast high tensile strength, tear resistance, and flexibility. They adhere firmly to curved or irregular surfaces without cracking, resisting mechanical stresses during handling. This durability reduces tape failures in demanding applications, enhancing productivity and minimizing replacement costs.
III. Scenarios Requiring Polyimide Tape Replacement
3.1 High-Temperature Processes
In lead-free soldering (peak temperatures >180°C), standard tapes often deform, allowing solder residue to penetrate and damage components. Polyimide tapes, with their thermal stability, prevent contamination, ensuring solder joint integrity and product longevity. Industries like aerospace and high-tech electronics mandate their use to meet stringent quality standards.
3.2 Corrosive Chemical Environments
Processes like electroplating and chemical milling involve prolonged exposure to corrosive agents. Polyimide tapes act as robust barriers, resisting degradation while maintaining adhesion. Their inertness to acids, alkalis, and solvents safeguards substrates, reducing product defects and equipment maintenance costs.
3.3 UL-Certified Insulation Requirements
Applications in electrical equipment (e.g., motors, transformers) demand UL-certified insulation to ensure safety. Polyimide tapes offer low dielectric constants, stable electrical properties, and resistance to thermal aging, meeting stringent UL standards. Their use in windings or cable terminations enhances reliability, preventing failures due to insulation breakdown.
IV. Cost Analysis
4.1 Market Price Comparison
Polyimide tapes cost significantly more than standard alternatives due to advanced materials and production processes. As of 2022, global polyimide tape sales reached CNY 3.905 billion, with China accounting for CNY 1.181 billion. In contrast, PET tapes retail at fractions of this price, while paper tapes are often priced under $10 per roll. The premium reflects performance advantages in critical applications.
4.2 Impact on Total Production Costs
Short-term adoption may increase expenses, but long-term benefits offset costs. Polyimide tapes reduce rework due to thermal or chemical failures, saving labor and material waste. Their extended lifespan in harsh environments lowers replacement frequency, balancing initial investments with operational efficiency.
4.3 Reducing Rework and Scrap Costs
By preventing tape-related defects (e.g., adhesive residue, tape tearing during high-temperature processes), polyimide tapes minimize scrap rates. For example, in electronics assembly, avoiding solder contamination can decrease rework by 20-30%, translating to substantial cost savings.
V. Usage Considerations for Polyimide Tapes
5.1 Application Time and Storage
At 260°C, tapes are suitable for short-term use; 180-200°C is ideal for prolonged exposure. Store in cool, dry environments (15-25°C, <50% RH) to prevent adhesive degradation. Avoid direct sunlight or high humidity, which can weaken performance. Regularly check for dust or contaminants to maintain adhesive effectiveness.
5.2 Preventing Deformation in High-Temperature Applications
Minimize thermal stress by pre-conditioning tapes at gradual升温 before application. Ensure substrate surfaces are flat and clean to avoid uneven stress distribution. For complex geometries, use mechanical fixtures (e.g., clips) to stabilize tapes during heating cycles. Periodic inspections can identify early signs of deformation, allowing timely adjustments.
VI. Conclusion and Recommendations
6.1 Key Takeaways
Switch to polyimide tapes when facing:
● Temperatures >180°C (e.g., lead-free soldering).
● Exposure to aggressive chemicals (fluxes, plating baths).
● UL insulation requirements.
While PET tapes suffice for <180°C masking, polyimide variants are mandatory for harsh operations to prevent process failures.
6.2 Importance of Tailored Tape Selection
Optimal tape selection hinges on process specifics. Blindly using standard tapes in critical environments risks product defects, safety hazards, and increased long-term costs. Assess temperature ranges, chemical exposures, and electrical requirements to match tape properties precisely. This proactive approach ensures process reliability, enhances product quality, and boosts operational sustainability.
Table: Comparison of Tape Types (Optional)
Tape Type | Temperature Range | Chemical Resistance | Mechanical Strength | Cost (vs. Polyimide) |
Paper-Based | <80°C | Poor | Low | 10-20% |
PE | <120°C | Moderate | Medium | 30-40% |
PVC | <150°C | Fair | Fair | 50-60% |
PET | <180°C | Good | High | 70-80% |
Polyimide | -200°C to 400°C | Excellent | Exceptional | 100% (Baseline) |
Note: Cost comparison reflects relative pricing; actual figures vary by supplier and region.
References (Optional)
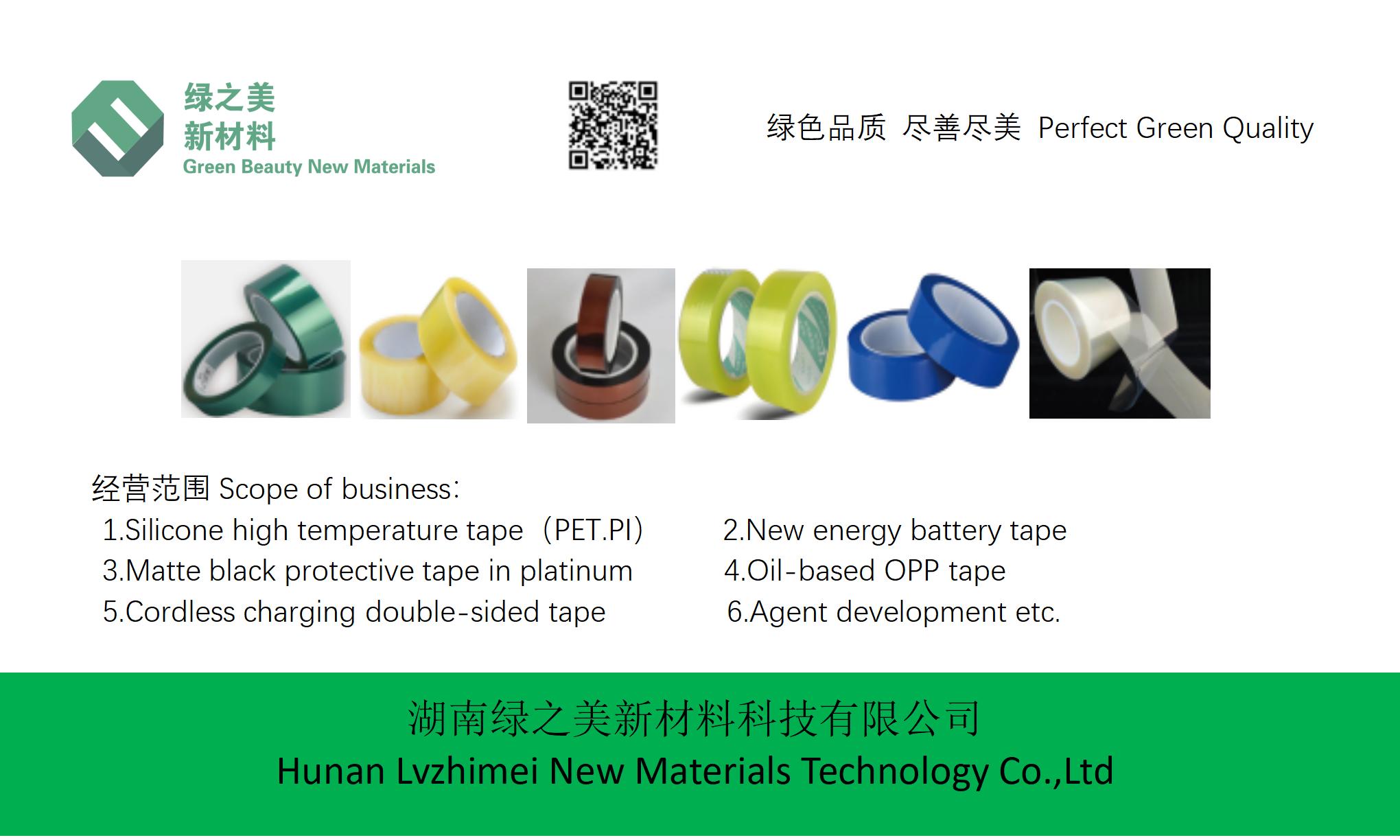