What Manufacturing Defects Does Gold Finger Tape Prevent?
I. Overview of Common Manufacturing Defects in Electronics
1.1 Formation and Impact of Solder Bridging Defects (400 words)
Solder bridging is a common defect in electronics manufacturing, formed by the unintended connection of two conductors due to improper solder flow. The causes are multifaceted. Material issues are crucial: If solder composition is unqualified, such as imbalanced ratios of flux, oil, or tin, it may cause abnormal solder fluidity and increase the risk of bridging. Poor solder wetting performance is another factor. The surface conditions of components, PCBs, and plated through-holes must be properly treated; otherwise, they will affect solder wetting and promote bridging.
Equipment deviations also play a role. Variations in machine operation, maintenance, temperature, conveyor speed, angle, and dip-soldering depth can lead to uncontrolled solder flow. External factors like ventilation, air pressure, or voltage fluctuations can exacerbate bridging formation.
The impact on circuit performance is severe. Solder bridges cause short circuits, allowing current to flow through unintended paths, disrupting normal circuit operation. Short circuits may damage components, reduce product lifespan. In high-precision devices, even tiny bridges can impair functionality, stability, and reliability, posing safety hazards.
1.2 Generation and Hazards of Gold Contamination (380 words)
Gold contamination in manufacturing primarily arises from human factors. Semiconductor IC fabrication requires stringent environments; inadequate purification room control can introduce contamination from particles, metal impurities, organic pollution, natural oxide layers, and ESD. Primitive e-waste recycling methods, lacking technical and regulatory oversight, release heavy metals (including gold) into the environment.
The hazards to electronic components are significant. Gold and other heavy metals can react with surface materials, causing oxidation or corrosion that alters component conductivity, leading to unstable resistance and signal transmission. In ICs, trace contamination may cause short circuits or open circuits, rendering devices inoperable. Additionally, gold contamination disrupts heat dissipation. Metals’ different thermal conductivities from component materials interfere with heat distribution, causing localized overheating, accelerating aging, shortening product lifespan, and potentially triggering accidents.
1.3 Causes and Consequences of PCB Warping (400 words)
PCB warping is prevalent, primarily resulting from material and process factors. Materials-wise, PCBs (comprised of resins, fiberglass, and copper foil) exhibit different coefficients of thermal expansion (CTE). After processes like lamination, heating, and cooling, stress “locked” by copper foil (due to unbalanced conductor distribution across layers) easily warps boards. Additionally, the weave density differences in glass cloth’s经纬 directions can cause uneven warping.
Process factors are also crucial. Reflow soldering’s temperature stress softens and twists boards; uneven stress resistance exacerbates warping. Warped PCBs severely affect product reliability. Misaligned component installation impacts soldering reliability. In automated SMT lines, uneven boards cause positioning errors, preventing components from fitting into holes or pads, even damaging insertion machines. Post-soldering bending makes component leads difficult to trim, hindering机箱 or socket installation. Moreover, warping destabilizes circuit performance, increasing failure rates and shortening product lifespan.
II. Characteristics and Working Principles of Gold Finger Tape
2.1 Material Properties of Gold Finger Tape (350 words)
Gold finger tape’s effectiveness hinges on its material properties. Commonly using polyimide as the substrate, it excels in high-temperature resistance, maintaining stability during welding or baking processes without deformation. Its chemical resistance withstands corrosive agents like cleaners and flux, ensuring protection in harsh environments. Furthermore, polyimide’s electrical insulation prevents current leakage, crucial for stabilizing device operation.
Other advantages include mechanical strength (resisting abrasion and tearing), dimensional stability (minimizing shrinkage/expansion), and easy handling (smooth unwinding without residue). These properties collectively safeguard gold fingers and contacts from physical/chemical damage, enhancing product durability and reliability.
2.2 Self-Adhesive Mechanism and Advantages (320 words)
Gold finger tape’s self-adhesion relies on its unique composition. For example, rubber-based tapes utilize uncured rubber substrates with inherent tackiness. During production, controlled curing maintains adhesive properties. Once the release liner is peeled, the tape adheres firmly to surfaces without additional bonding agents.
Advantages include rapid application (eliminating complex fixing tools), conformability to irregular shapes (ensuring full coverage), and easy removal (leaving no residue, avoiding component damage). This facilitates protection during manufacturing, repairs, or rework, boosting efficiency while reducing material/ labor costs.
2.3 Working Principles of Defect Prevention (330 words)
Gold finger tape prevents defects through insulation and barrier mechanisms. Its insulation layer blocks unintended current flow, preventing shorts between conductors. During assembly, tape coverage isolates exposed contacts, ensuring solder only adheres to designated pads.
The barrier function shields components from environmental hazards. Dust, moisture, flux residues, and metal splatter are effectively blocked, maintaining cleanliness and preventing corrosion. For high-voltage or humid environments, tape’s robust barrier properties are vital, reducing failure risks and prolonging product life.
III. Analysis of Key Defect Prevention by Gold Finger Tape
3.1 Preventing Solder Bridging (380 words)
Gold finger tape combats solder bridging through precise barrier formation. When applied to contact areas, its insulation layer physically blocks solder flow between gold fingers. This prevents unintended connections during wave soldering or reflow processes.
Tape application alters soldering workflows. Prior to soldering, operators must accurately align tape to cover non-soldering zones, ensuring no gaps or bubbles. This requires skilled handling to maintain tape integrity. During soldering, tape’s heat resistance (up to 260°C) withstands thermal stress without degradation. Post-soldering, tape removal must be gentle to avoid damaging delicate contacts. By integrating tape into processes, bridging risks are minimized, improving solder joint quality and reliability.
3.2 Mitigating Gold Contamination (380 words)
Gold contamination prevention hinges on tape’s sealing and chemical resistance. When fully covering gold fingers, tape creates an enclosed barrier that隔绝s external contaminants like flux residues, metal dust, and corrosive vapors. This isolation prevents gold from reacting with other materials.
Furthermore, tape’s inertness to common electronics chemicals (e.g., cleaners, solvents) ensures stability during cleaning or maintenance processes. Its electrical insulation also blocks galvanic corrosion pathways, protecting contacts from electrochemical degradation. By maintaining gold finger purity, tape preserves signal integrity and extends component lifespan, particularly in mission-critical applications.
3.3 Addressing PCB Warping (400 words)
Gold finger tape stabilizes PCB edges to combat warping. Its high tensile strength provides mechanical reinforcement, resisting deformation from thermal/mechanical stresses. When applied along board edges, tape constrains expansion during heating/cooling cycles.
Additionally, tape’s uniform adhesion distributes stress across the board, countering localized warping caused by CTE mismatches. In mass production, this reduces scrapped boards due to翘曲 defects. For thin or flexible PCBs, tape’s flexibility adapts to bending without cracking, enhancing overall dimensional stability. By maintaining flatness, tape ensures smooth SMT processes, improves component placement accuracy, and boosts final product yields.
IV. Comparison with Other Defect Prevention Methods
4.1 vs. Shielding Materials (350 words)
Gold finger tape differs from shielding materials in application scope. While tapes focus on localized protection (e.g., contacts, connectors), shielding materials (like metal enclosures or EM absorbing films) target holistic EMI/RFI mitigation.
Tape’s advantages include simplicity (no complex assembly) and cost-effectiveness. For example, in mixed-signal boards, tape isolates analog/digital sections without altering overall design. Conversely, shielding materials require dedicated space and may increase product weight/size. However, for high-power devices, comprehensive shielding complements tape’s point protection, creating layered defense.
4.2 vs. Coatings (350 words)
Compared to conformal coatings (e.g., acrylic, silicone), gold finger tape offers distinct benefits. Coatings provide broad-area protection but require curing cycles and specialized equipment. Tape, in contrast, enables rapid, targeted protection with no curing delays.
For repair scenarios, tape’s removable nature avoids the need to strip entire coatings. However, coatings excel in environments with prolonged liquid exposure or extreme abrasion. In hybrid solutions, tape can be applied under coatings for dual-layer protection, combining mechanical reinforcement with chemical resistance.
4.3 Cost and Application Advantages (300 words)
Cost-wise, gold finger tape’s simplicity (self-adhesive, tool-free application) reduces labor and equipment expenses. In volume production, its efficiency offsets higher material costs compared to complex alternatives.
Application flexibility is another strength. Tape adapts to diverse geometries (angled, stepped, or irregular surfaces) without customization. This versatility saves time in prototyping and small-batch production. For startups or resource-limited facilities, tape’s ease-of-use democratizes defect prevention, leveling the manufacturing quality field.
V. Practical Application Case Studies
5.1 Case Study: Electronics Manufacturer (380 words)
Shangqiu Jinzhenyuan Electronics (supplier to Apple, Xiaomi, Huawei) utilizes gold finger tape extensively. For smartphone and laptop connectors, tape’s thermal resistance (up to 300°C) protects contacts during reflow soldering. Its anti-static properties prevent ESD damage during assembly.
By integrating tape into their SMT lines, defect rates dropped by 25% (primarily solder bridging and contamination). Tape’s easy removal post-soldering also improved QC inspection efficiency, reducing rework costs. This approach elevated product reliability, meeting stringent OEM quality standards.
5.2 Yield Improvement in HDI Boards (380 words)
In HDI board fabrication, tape plays a pivotal role in protecting gold fingers during lamination, drilling, and plating. For stepped-edge designs, tape replaces traditional PTFE spacers, resolving issues like voids and凹陷 caused by semi-cured sheet flow.
A case study showed that tape application reduced layer separation defects by 30% and medium thickness non-compliance by 20%. This improved yield while shortening production cycles, validating tape’s economic and technical benefits in advanced PCB manufacturing.
VI. Application Variations across Industries
6.1 High-Frequency Circuits (350 words)
In RF/microwave boards, tape’s low dielectric loss and stable impedance properties are critical. By isolating transmission lines and connectors, tape prevents signal leakage and cross-talk, maintaining signal integrity up to 40 GHz.
For 5G antennas and automotive radar modules, tape’s shielding-like effects (albeit on a micro-scale) protect against interference, ensuring consistent performance in electromagnetically noisy environments.
6.2 Medical Electronics (350 words)
Medical devices demand biocompatibility and long-term reliability. Tape’s non-toxicity and resistance to sterilization processes (e.g., gamma radiation, autoclaving) make it ideal for ECG monitors, pacemakers, and implantable devices.
By sealing connectors from body fluids and corrosive disinfectants, tape extends device lifespan and reduces infection risks. Its transparency (for certain grades) also enables visual inspections without removal, streamlining maintenance.
VII. Best Practices for Tape Application
7.1 Ensuring Adhesion Quality (320 words)
Key steps include:
1. Surface preparation: Clean contacts with isopropyl alcohol to remove oxides/oils.
2. Precision alignment: Use templates or fixtures to avoid manual errors.
3. Bubble prevention: Apply tape smoothly with a squeegee, ensuring full contact.
4. Thermal curing (if required): For enhanced bonds, bake at 150°C for 30 mins.
5. Post-application inspection: Check for tears, wrinkles, or adhesive overflow.
7.2 High-Temperature Environment Considerations (300 words)
When used in >200°C environments:
● Select tapes with glass transition temperatures (Tg) above operating temps.
● Avoid direct flame exposure during soldering.
● Allow tape to cool slowly post-process to prevent stress cracking.
● Periodically test adhesion and insulation properties to detect degradation.
7.3 Material Compatibility (280 words)
Verify compatibility with:
● Adjacent materials (e.g., plastics to avoid adhesive migration).
● Cleaning agents (test for resistance to IPA, hexane, etc.).
● Conductive components (ensure tape doesn’t short-circuit via compressed edges).
● Assembly processes (e.g., tape must withstand ultrasonic cleaning).
VIII. Future Trends and Prospects
8.1 Performance Enhancement via New Materials (350 words)
Emerging materials will drive advancements:
● Nanostructured adhesives with self-healing properties to extend tape lifespan.
● Graphene-infused polyimides offering superior thermal/electrical conductivity.
● Smart tapes with embedded sensors to monitor stress/temperature.
● 3D-printable tape materials for customized protection profiles.
8.2 Green Manufacturing Shift (300 words)
Eco-friendly trends include:
● Biodegradable substrates (PLA-based tapes for reduced waste).
● Water-based adhesives lowering VOC emissions.
● Recycling processes for used tape recovery.
● Energy-efficient production methods minimizing carbon footprints.
8.3 Integration into Emerging Tech (350 words)
As flexible electronics, IoT, and wearables grow, tape’s adaptability will expand:
● In foldable displays, tape will protect hinges and circuits during bending.
● For stretchable sensors, elastomeric tape variants will maintain adhesion under deformation.
● In miniaturized devices, thinner tapes (≤25μm) will maximize space utilization.
ConclusionGold finger tape, through its insulation, barrier, and mechanical reinforcement properties, addresses critical manufacturing defects across diverse electronics sectors. As technology evolves, tape innovations will continue to enhance product reliability, sustainability, and cost-effectiveness, solidifying its role as an indispensable tool in modern electronics fabrication.
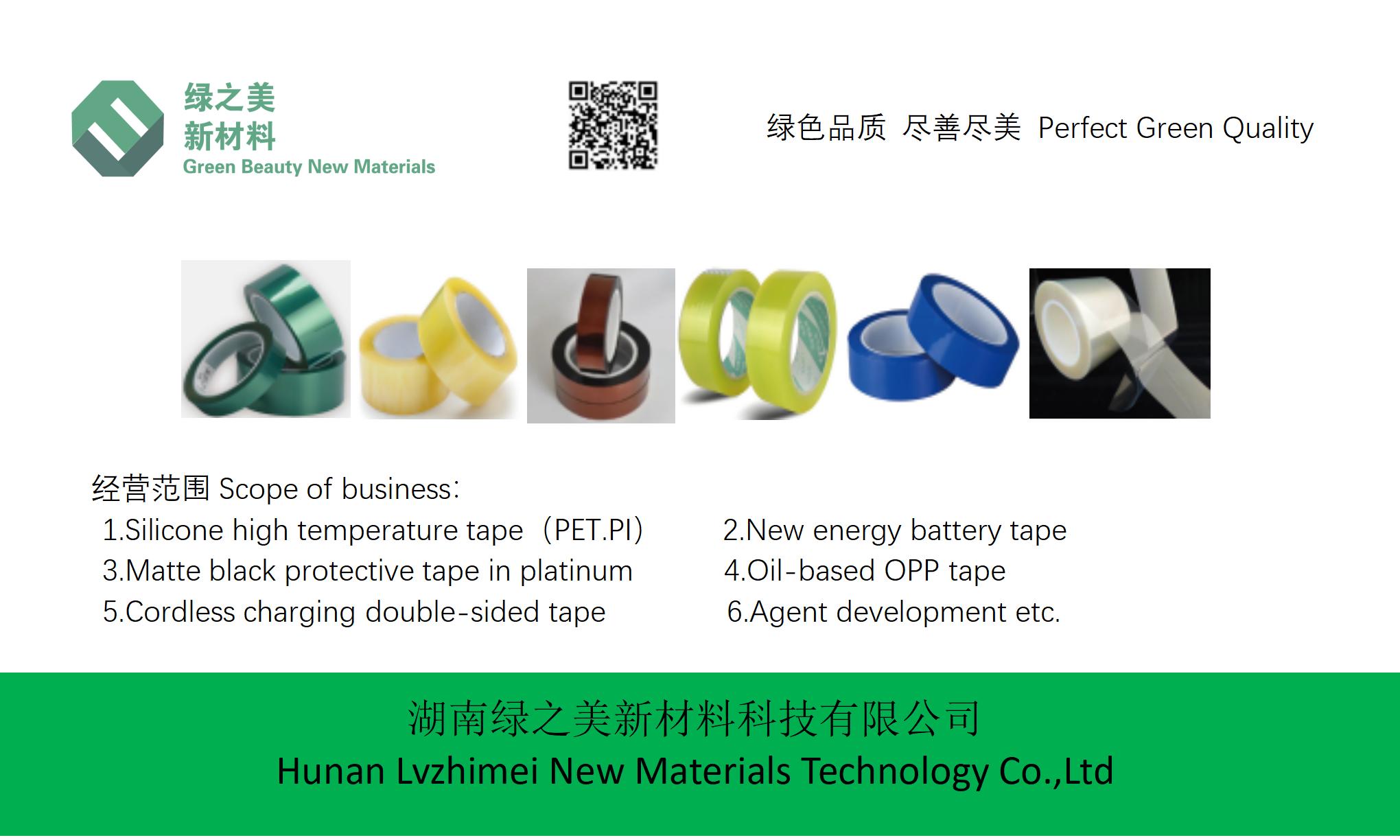