1
1. Overview of Kapton Tape and Traditional Insulation Materials
1.1 Basic Characteristics of Kapton TapeKapton tape, primarily composed of polyimide, stands out with its exceptional properties. Renowned for its high-temperature resistance, it can withstand environments exceeding 280°C—ideal for applications in high-temperature equipment and aerospace. For instance, "PI material high temperature resistant 300 tape" ensures stability even at 280°C+, meeting stringent insulation requirements in demanding scenarios.
Chemical stability is another highlight. It resists corrosive substances like strong acids and alkalis, providing reliable protection for equipment in chemical production and laboratory environments. Its electrical insulation properties are equally superior, featuring high resistivity, low dielectric constant, and minimal dielectric loss, making it indispensable in electronic and electrical equipment to ensure safety and stability.
Mechanically, Kapton tape offers flexibility and toughness, effortlessly conforming to complex shapes without bubbling or wrinkling. Its dimensional stability remains consistent across temperature fluctuations, preventing cracks or detachment in insulation layers. These attributes collectively position Kapton tape as a versatile solution across diverse industries.
1.2 Types and Characteristics of Traditional Insulation MaterialsTraditional insulation materials, such as PVC, PET, and fiberglass tapes, each cater to specific applications. PVC tape, cost-effective and offering basic insulation and waterproofing, is prevalent in household wiring and simple cable wrapping. However, its poor heat resistance causes aging and hardening at elevated temperatures, limiting its use in harsh environments.
PET tape, based on polyester film, excels in mechanical strength and abrasion resistance, suitable for motor winding and cable protection. Yet, its flexibility is inferior, prone to cracking during bending or wrapping. Fiberglass tape, combining glass fiber and adhesive, performs well in high temperatures but has a rigid texture, posing challenges during application and generating fiber debris that may affect both work environments and equipment.
While these materials serve general purposes, their performance constraints highlight the need for alternatives in specialized contexts.
2. Comparative Analysis of Performance Dimensions
2.1 Thermal Performance DifferencesThermal resistance differentiates Kapton tape from traditional materials. While Kapton withstands >280°C (e.g., "PI high temp tape" maintaining functionality at 260°C+), PVC begins to degrade at ~70°C, PET softens above 150°C, and fiberglass tapes peak around 200°C. This disparity impacts long-term reliability: Kapton ensures insulation integrity in ovens, aerospace components, or industrial machinery subjected to extreme heat, whereas traditional tapes risk failure, compromising equipment safety.
2.2 Chemical Stability ComparisonKapton's polyimide core grants immunity to harsh chemicals. In acid baths, solvent exposure, or corrosive industrial settings, it maintains structural and electrical properties. Conversely, PET tape may swell or dissolve in solvents, PVC cracks under prolonged chemical stress, and fiberglass adhesive may degrade, necessitating frequent replacements. For chemical processing equipment or laboratory instruments, Kapton's durability slashes maintenance costs and downtime.
2.3 Mechanical Performance AdvantagesKapton's mechanical superiority lies in its balance of strength and flexibility. With high tensile strength preventing tears and exceptional flexibility enabling seamless wrapping around sharp edges or contours, it surpasses rigid fiberglass and brittle PET tapes. This adaptability streamlines installation in tight spaces, minimizing labor time and insulation layer defects.
Moreover, its tear resistance during handling reduces waste, and its smooth surface facilitates clean removal without residue—a critical advantage in electronics assembly.
2.4 Electrical Insulation Performance DistinctionsElectrical metrics favor Kapton tape. Its low dielectric constant (≈3.5) and dielectric loss (≈0.04) make it suitable for high-frequency environments, such as microwave circuits or high-voltage transformers. Traditional materials like PVC (dielectric constant ≈4.5) or PET (≈3.8) exhibit higher losses, potentially causing signal degradation or arcing risks in advanced applications.
Furthermore, Kapton's high breakdown voltage (≥20 kV/mm) enhances safety in scenarios where electrical stress is intense, solidifying its role in critical systems.
3. Practical Application Case Studies
3.1 Applications in LED ManufacturingIn LED chip soldering (temperatures up to 260°C), Kapton tape prevents short circuits. A manufacturer shifted from PET tape (melting at high temps) to Kapton, boosting yield from 82% to 98% by avoiding insulation failures. Additionally, Kapton's non-corrosive adhesive protects delicate LED structures during powder coating, ensuring long-term reliability.
3.2 Applications in Electronics and Electrical EngineeringMotor coil insulation demands materials enduring thermal cycling and mechanical stress. For H-class motors (operating at >200°C), Kapton tape replaces fiberglass tape: its flexibility simplifies winding processes, while its thermal endurance eliminates insulation breakdowns. Transformers benefit similarly—Kapton wraps mitigate electromagnetic stress-related failures.
3.3 Applications in Circuit Board ManufacturingIn flexible circuit boards (FPCs), Kapton tape shields components during drilling and cutting, reducing damage rates. Multilayer PCBs subjected to acid etching or high-temperature lamination rely on Kapton’s stability to preserve trace integrity. Its thin profile and high insulation performance prevent signal interference, vital for aerospace or medical devices.
4. Cost Considerations
4.1 Cost Analysis of Kapton TapeKapton tape’s cost reflects its advanced material and production complexity. Polyimide synthesis involves costly precursors and stringent processes, driving raw material prices. Manufacturing entails precise steps like casting, coating, and curing, demanding specialized equipment and skilled labor. Market data (2022) show global sales of 390.5million,withChinaaccountingfor118.1 million, indicating stable demand in tech-intensive sectors. Though premium priced (ranging from XtoXX per roll), its performance offsets long-term replacement costs in critical applications. 4.2 Alternative Options for Cost-Sensitive ProjectsFor less demanding scenarios, cost-effective substitutes like PET tape (1/3–1/5 the price) or glass cloth tape can suffice. PET tape offers adequate insulation for room-temperature electronics, while glass cloth tape provides thermal resistance up to 180°C in large equipment. However, sacrifices in flexibility or chemical resistance must be weighed against budget constraints.
5. Summary of Key Decision Factors
5.1 Decision Flowchart or TableThe decision matrix guides selection based on application needs:
● High-Temp Environments (≥280°C): Kapton tape is mandatory.
● Chemical Exposure: Opt for Kapton over PET or PVC to avoid degradation.
● Complex Geometries: Choose Kapton for flexibility; fiberglass for rigid structures.
● High-Voltage Systems: Prioritize Kapton for superior electrical metrics.
● Cost-Constrained Projects: Assess if PET or alternatives meet reduced performance thresholds.A flowchart visualizes this prioritization, aiding rapid decision-making.
5.2 Conclusions and RecommendationsSelect Kapton tape when:
1. Thermal stability is critical (e.g., LED soldering, aerospace).
2. Chemical resistance is non-negotiable (lab equipment, industrial machinery).
3. Components require tight wrapping (FPCs, miniature electronics).
4. High electrical reliability is mandated (transformers, high-frequency circuits).For budget projects with moderate requirements, explore PET tape or glass cloth tape. Balance performance needs with cost-effectiveness using the decision tool. Integrating "lvmeikapton insulating electrical tape" into high-reliability designs ensures longevity and safety.
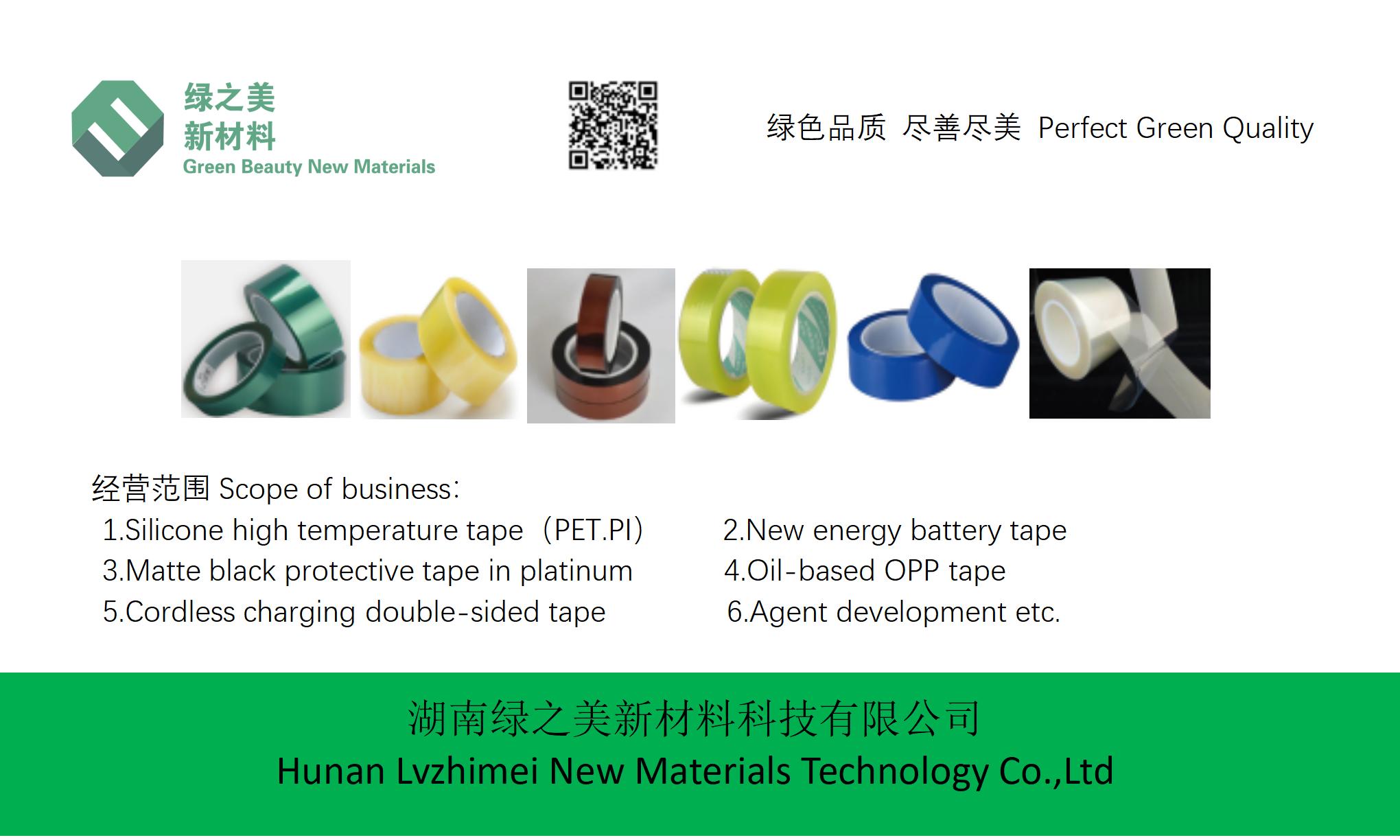