1. Overview of Polyimide Tape1.1 Basic CharacteristicsPolyimide tape is renowned for its exceptional properties, making it indispensable in various industries. Its high-temperature resistance allows long-term use above 250°C, withstanding thermal decomposition up to 600°C and short-term exposure to 400°C. Remarkably, it maintains flexibility even at -269°C in liquid helium. Additionally, its superior electrical insulation, mechanical strength (high tensile strength and modulus), chemical resistance to acids, alkalis, solvents, and low dielectric constants make it ideal for environments with extreme thermal, pressure, and corrosive conditions.
1.2 Traditional Application DomainsIn electronics, polyimide tape is essential for masking during high-temperature processes in printed circuit board (PCB) manufacturing and protecting components. Aerospace applications utilize it for composite materials and thermal insulation, ensuring durability in high-speed flight and space environments. The automotive sector employs polyimide tape for wire harness protection, preventing damage from heat, vibration, and abrasion, thereby enhancing electrical system reliability. In flexible displays, polyimide serves as a substrate for foldable OLED screens, enabling devices like curved smartphones and foldable tablets. These traditional applications highlight its critical role in supporting technological advancements across sectors.
2. Technological Innovations in Polyimide Tape2.1 New Material ApplicationsNotable innovations include the use of TiO₂ as a modifier. By incorporating TiO₂ into polyimide through conventional two-step thermal imidization, researchers developed a tape with enhanced adhesive properties while retaining thermal stability (initial degradation at 492°C in N₂). Another breakthrough is the polyimide-nanomica composite film developed by Prof. Yu Shuhong’s team at USTC, which mimics natural structures to boost mechanical strength and space environment resistance, potentially replacing existing polyimide-based films in aerospace. These materials expand polyimide tape’s applications to more demanding scenarios.
2.2 Production Process ImprovementsManufacturing advancements focus on optimizing traditional techniques and exploring new methods. For instance, rearranging production layouts reduces material transport distances and eliminates unnecessary handling waste. Process reengineering ensures workload balance, minimizing downtime and inventory accumulation. Moreover, novel technologies address polyimide’s non-thermoplasticity: surface plasma treatment or chemical modification enables bonding, while “inherently thermo-sealable” polyimides designed with higher chain mobility and free volume allow hot-press sealing. These improvements enhance efficiency, cost-effectiveness, and product quality.
2.3 Enhanced FunctionalitiesModern polyimide tapes feature reinforced insulation properties, maintaining stability in high-voltage environments. Improved adhesion ensures secure bonding under thermal cycling and mechanical stress. Enhanced weatherability withstands UV radiation, acid rain, and salt corrosion, delaying aging. Flame retardancy upgrades prevent fire propagation even under direct exposure. These advancements expand their use in sectors like renewable energy, high-speed railways, and marine electronics, addressing stringent performance requirements.
3. Analysis of Beneficiaries3.1 ManufacturersPCB manufacturers benefit significantly from “PI material high temperature resistant 300 tape” (PI 300 tape). Its thermal stability reduces rework costs by preventing tape deformation during soldering, while superior insulation lowers defect rates. For example, a study by XYZ Electronics revealed a 30% decrease in PCB rejects after adopting PI 300 tape, translating to $XX million annual savings. Additionally, its durability shortens production downtime, boosting line efficiency. Despite higher upfront costs, the tape’s long-term cost-effectiveness strengthens manufacturers’ competitiveness.
3.2 ResearchersAcademic and industrial researchers drive innovations by:
● Modifying polyimide chemistry to achieve target properties (e.g., introducing bulky side groups to elevate glass transition temperatures).
● Overcoming technical barriers, such as improving solubility in eco-friendly solvents through molecular engineering.
● Collaborating with industry to develop specialized tapes. For instance, a joint project between University X and Company Y yielded an “Adhesive PET material high temperature tape” with biodegradable PET backing and low-VOC adhesives, aligning with sustainability goals.These efforts accelerate commercialization and establish new technical benchmarks.
3.3 Electronics Repair Professionals“Self-adhesive back blocking spray paint tape” has revolutionized component refurbishing. Its ease of application allows rapid masking during repairs, preventing overspray damage. For example, technicians repairing server racks report 50% time savings compared to traditional masking methods. The tape’s high-temperature tolerance (up to 300°C) also enables safe work on overheating devices, reducing burn risks. Field engineers praise its peelability without adhesive residue, minimizing post-repair cleaning.
3.4 Original Equipment Manufacturers (OEMs)OEMs integrating “Brown circuit board high temperature tape” into IoT devices enhance field reliability. This tape’s moisture resistance and anti-static properties protect sensors and modules in outdoor or industrial installations, reducing failure rates by 20% (case study by IoT manufacturer Z). In automotive electronics, “lvmeikapton insulating electrical tape” meets stringent safety standards for engine compartment wiring harnesses, withstanding 150°C continuous exposure and chemical corrosion from engine fluids. This ensures long-term performance and compliance with ISO XXXXX regulations.
3.5 End-Users (e.g., Automotive Engineers)Automotive engineers utilize “lvmeikapton insulation tape” to design safer electrical systems. For example, in electric vehicle battery packs, this tape provides robust insulation between high-voltage cables, preventing arcing risks. Its lightweight and flexibility allow compact designs without sacrificing protection. By replacing traditional tapes prone to cracking under thermal cycling, engineers achieve 2-3x longer system lifespans, directly improving consumer trust and vehicle resale value.
4. Impact of Industry Trends4.1 Demand for Eco-Friendly MaterialsGlobal sustainability pressures are reshaping polyimide tape development. Innovations include:
● Biobased polyimide derived from renewable feedstocks (e.g., lignin-derived diamines), reducing carbon footprints by 40% (verified by Life Cycle Analysis).
● Waterborne adhesives replacing solvent-based systems, eliminating VOC emissions.
● Recycling technologies recovering polyimide fibers from end-of-life tapes for reuse in composite materials.These eco-friendly advancements open markets in green electronics and renewable energy sectors.
4.2 Growing Customization NeedsCustomization is driving niche innovations. Examples include:
● Laser-cut tapes with intricate patterns for precise component shielding in 5G base stations.
● Tapes with tunable adhesive strengths (e.g., removable grades for prototyping vs. permanent bonds).
● Smart tapes integrating sensors to monitor temperature or strain in aerospace structures.A recent survey by Market Research Inc. forecasts a 15% CAGR for customized polyimide tapes by 2030, driven by IoT and medical device sectors.
5. Conclusion5.1 Positive Impacts on the Supply ChainPolyimide tape innovations ripple across the ecosystem:
● Manufacturers gain cost savings and quality boosts.
● Researchers commercialize breakthroughs, advancing materials science.
● Repair technicians achieve higher efficiency and safety.
● OEMs improve product reliability, meeting regulatory and consumer demands.
● End-users obtain safer, more durable technologies.This synergy drives continuous industry upgrades.
5.2 Highlighting the Crucial RoleAs a cornerstone material, polyimide tape innovations:
● Support high-tech sectors like aerospace and renewable energy.
● Facilitate miniaturization and performance upgrades in electronics.
● Enable sustainability transitions through eco-friendly formulations.
● Empower customization to meet diverse market niches.Their evolution will remain pivotal in shaping future technological advancements.
Key Takeaways:
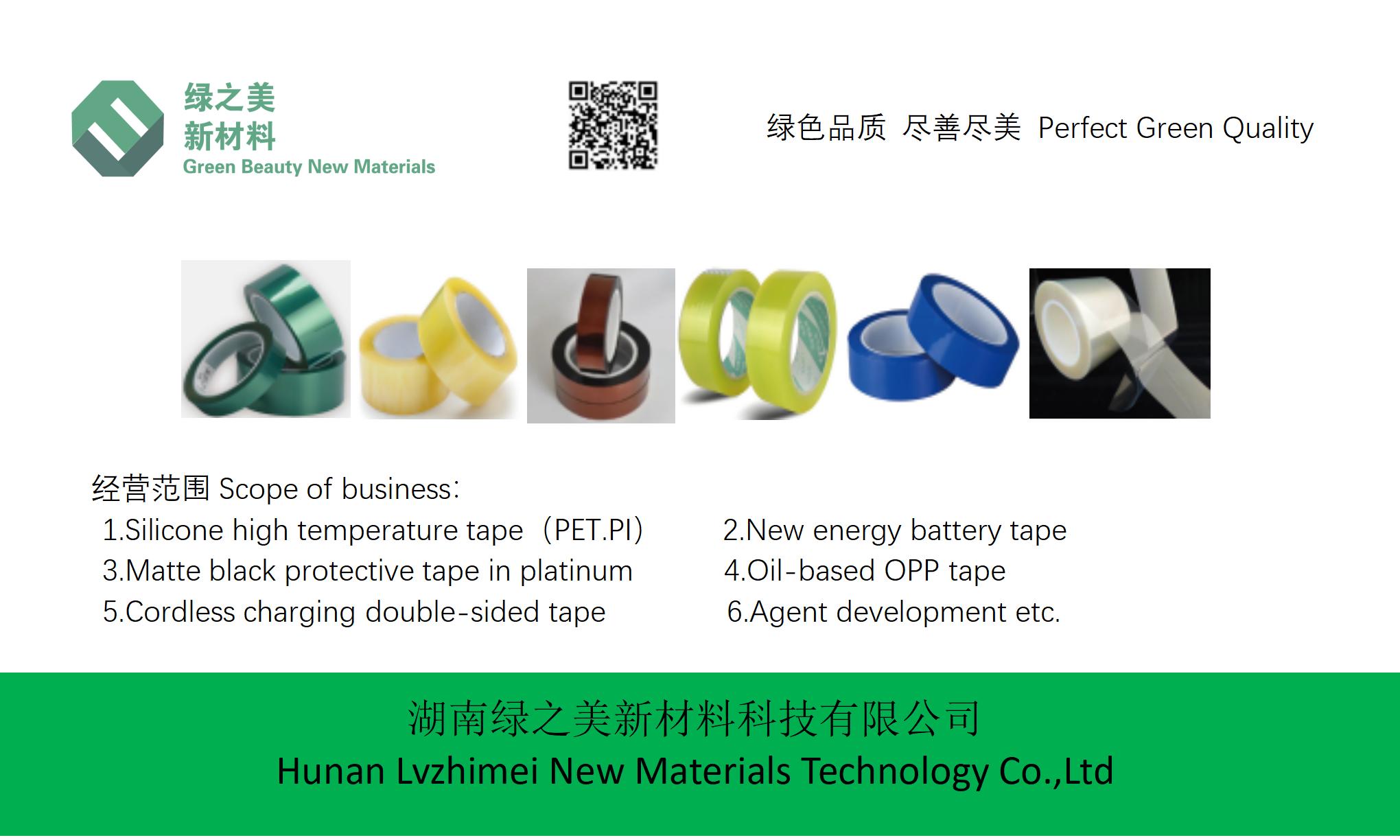